Today's work environment has been revolutionized by PC's and PC workstations. The most dramatic changes have taken place in industrial control centers and control rooms. Control rooms, traditionally used for sharing instrumentation information, have evolved from large panels with support instrumentation in adjacent rooms, to modern control buildings that support people interfacing with computers. This change has impacted the way these buildings are designed and has introduced a new discipline called Human Factor Engineering (HFE).
Listen to: Podcast: The Control Room of the Future
In the past, the only human factor influencing control room design was the grouping of instruments to support pattern recognition. This scheme allowed operators and engineers to maintain the "big picture" of the process under control. Sometimes the designers followed another simple human factors guideline that dictated a minimum and maximum height for instrument mounting, somewhere between 40—70 in. from the floor, so the typical operator could read all the instruments without having to stoop or stretch.
Unfortunately for processors, the vast majority of the control panels were not designed by human factors engineers, but by instrumentation engineers, unfamiliar with the finer points of ergonomics.
Instrument engineer-designed panels do have some redeeming features—many of which readers should be familiar with, including the ability to recognize patterns and quickly identify process changes. Similarly well-known to veteran processors was the ability to identify trends by pen marks in the folds of plotter paper, and the enforcement of a low number of alarms due to cost and space limitations.
Unfortunately, most did not recognize these positive aspects of traditional control interfaces during the transition from analog instrument-based control to digital (computer) control. Much of this was lost during the transition to first and second-generation Distributed Control System (DCS) control room designs. During that period, some processors also lost the ability to effectively share control and process information among operators (both field and control room), supervisors, engineers and managers.
The House Instruments Built
The building that housed the control room was designed with the instrumentation in mind, and then, later, DCS equipment. The primary and secondary users of the building were often an afterthought and had to live within the constraints of the design. Often kitchens, and even restrooms, were not originally planned, so space for operator comfort was adapted where available.
Second-generation control rooms were often characterized by their independence from field instrumentation; as witnessed by the appearance of the first consolidated control rooms. The advent of electronics permitted greater distances between the field instruments and the previous-generation control rooms, but the instrument engineer still dominated their design.
Operating consoles were usually off-the-shelf designs supplied by the same instrumentation vendors who produced DCS equipment. This technology was big, bulky, noisy, and did not adhere to modern ergonomic design considerations. Hence, support equipment such as hardwired alarms, phones, public address systems, and PC's were difficult to incorporate into the layout of the room. All of these things were just bad add-on accessories.
It was during this stage of control room design evolution that industry trade associations and regulators began to realize that the layout of the room, the control interfaces it encompasses and the building it's housed in, can have a great impact on an operator's performance.
Read Also: Control Center Design Can Boost Operator Performance
When we look at human reliability we discover that even on a good day, seemingly innocuous elements of the work environment can stress the operator. Common maladies such as headaches, eye strain and sleep-related problems often have root causes traceable to such factors as glare from poorly designed lighting systems; poor temperature and humidity control; bad air quality; and poorly maintained buildings.
Adding to the woes of the operator are poor workspace design, an environment aggravated by uncomfortable consoles, keyboards, chairs and noise. Often excessive, noise generated by console fans, panel alarms, radio/PA speaker interference and constant radio communications all contribute to poor ambient conditions.
These environmental factors are exacerbated by a poorly implemented DCSs. Many systems are plagued with issues that make it very difficult for an operator to detect, diagnose and respond to in an abnormal situation. These issues commonly include excessive and undisciplined use of alarms that obscure more critical alarms; poor user interfaces that make it difficult to recognize changes and perceive important deviations; and poor navigation, forcing operators to spend precious time flipping through displays to find critical data.
One-Trick Pony
The workstation is often designed for one specific task—interfacing with the DCS—and thus has no capacity for other duties such as report writing or training. Similarly, there are often few, or inadequate facilities for using and storing manuals and communication equipment. Other ergonomic problems include broken or patched chairs, furniture never designed for 24-hour operations and no rest/recovery strategies incorporated into control room design. Resourceful operators often find ways of taking a break or getting some exercise, but few control room environments take into account operator downtime or well being into the design.
Read Also: The Control Room of the Future - Smarter Reality
Distractions are myriad and create one of the most common environmental problems for operators. Distractions can come from anywhere: poor traffic flow through the building, non-essential personnel congregating in the control room; undisciplined telephone traffic; auxiliary equipment noise; doors opening; alarms sounding; other operators talking on the radio, etc. The list is endless but the point is distractions in the control room are not conducive to trouble-free operations.
To Err is Human
"The combination of human and machines, in its organizational and environmental context, is considered as an overall system to be optimized. The optimization is achieved by developing solutions that emphasize and maximize the strengths, features and capabilities of both humans and machines in a complimentary fashion. The human component, the machine (hardware and software), the work environment, and the control (operation and management) shall be harmonized integrated during all phases of the design process, conceptual and detailed design, assembly and construction, commissioning, user training and operations."
Worldwide industrial practice has evolved to build new control buildings that will withstand a worst-case-scenario incident and still protect the inhabitants of the building. However, with the growth in centralization and the flexibility to move the building anywhere, industry has responded by moving non-critical people outside the battery limits and into a safe area. The API "Guidelines Management of HAZARDS Associated with Location of Process Plant Buildings, Recommended Practice 752" provides advice on building structures and locating personnel, but this is not a legal requirement, and is often not implemented in a new building project due to economic constraints.
Steps to Good Design
To generate a Functional Design Specification, ISO 11064 identifies a front-end loading methodology, but the organization also acknowledges that many of the other work design systems required to ensure human safety, such as health and well-being, are not fully identified or addressed by the standard.
The standards do, however, help the designer understand the use of space, considerations for workstation layout and design, and the use of other systems such as off-workstations. The methodology is a participatory process and uses an iterative design approach.
Regardless, important questions must be addressed before the design process is started. During the process the designer often has to deal with additional complexity, such as changes to the number of console operators; changes in DCS system and technology; a change in software and user interface design capability; or correcting previous design deficiencies or incorporating recent advances in control, process technology, operations and improved management systems.
Step 1-Identify Primary Users
Accurately defining the number of operators depends on new approaches to determining staffing levels. Most previous control room schemes have had more operators than required, or created an unevenly distributed work load. Operator roles and responsibilities must also be defined, and that dictates the console operator's span of control (how many operating units). The number of console operators is also influenced by organizational and management system constraints such as training.
Step 2–Identify HCI Design
Once the number of console operators has been determined, the next step in design a truly ergonomic system is to specify the Human Computer Interface (HCI) System.
Although it is difficult at this stage of a typical project to design the HCI, it is possible to generate a vendor independent specification which includes a graphics navigation strategy, a keyboard design and the number of screens per console. This HCI system guidance is specified in the EEMUA 201 Human Computer Interface Guidance document.
At this point a graphics style guide can also be developed , but will require good human factors engineering involvement to specify foundation requirements that are needed to guide important decisions. These decisions are based on questions such as: "Will the background color for screens be a lighter gray, or will a more traditional color such as black be used?" This is important for lighting design to ensure glare is not an issue. The last decision to make at this stage is to determine if the design will incorporate large off-workstations, safety systems, communication systems, hardwired panels, etc.
Step 3–Specify Console Requirements
With personnel and equipment requirements known, designers can determine console requirements. This is one of the main systems requiring ergonomic design considerations. Companies commissioning new control building and control room facilities must decide on how much investment they want to put into the console. The choices are to continue to use one of the instrument vendors' off-the-shelf consoles, use off-the-shelf office furniture or use off-the-shelf console furniture that is designed for the control room.
Only one of these solutions will meet the international ergonomic requirements and encompass the physical, anatomical, anthropometric, physiological, behavioral and biomechanical capabilities ins such a way as to provide good workplace layout and design, e.g., working postures, materials handling, line of sight and repetitive movement. Currently the U.S. regulators do not insist on human factor compliance, however, they have tried to pass, and will continue to promote legislation in this area as the current annual cost for shift worker fatigue exceeds $77 billion.
Step 4–Specify Console Layout
Once the numbers of consoles are known, and the size and equipment requirements are specified, the layout of the consoles in the control room needs to be specified based on communication and collaboration requirements. This is determined by studying the process interactions and identifying common utilities that will cause domino effects. Locating the console operators in close proximity will promote, but not guarantee, improved communication and collaboration.
The ISO 11064 standard Part 3, Control Room Layout, provides guidance on workstation groupings, spacing requirements and location of visual displays for best line of sight.
This is an undeveloped topic for industrial control rooms. Recent research has suggested that trying to provide a traditional chair and table solution is doomed to failure due to the wide variation in operating styles, and how people handle stress and fatigue. It is becoming apparent that flexibility is the main requirement. Being able to vary posture by perching, lounging or standing are good options to supplement the more traditional right-angle seating. With the introduction of "power" napping who knows were console design may go?
The most important factor in console design is not only to meet the ergonomic standards, but to provide a practical work environment that looks good, reduces stress and fatigue, and helps operators perform their tasks efficiently.
The simple, low-cost solution for control room users is to specify an instrumentation vendor's off-the-shelf solution. But a few years down the road, legislation might check this common-sense tactic, forcing users to upgrade to a more ergonomic solution, somethnig that could be expensive, difficult and disruptive to implement. Any savings realized by going for the low-cost solution will be lost in the upgrade. The user company should also consider the yearly costs related to shift-worker fatigue and the impact of human error on profitability. What looks initially like a cost effective solution is really a poor investment.
Step 5–Secondary Requirements
Step 6, as required by the ISO 11064 standards, is to work with users to determine the control room's parameters, such as space required, its intended use, and its adjacency requirements identified as either preferred, neutral or negative adjacency. During this phase designers should determine the ergonomic requirements of each of the individual rooms in the building. Lighting, noise and traffic flow should be specified as well, and include addressing reverberation issues and specifying windows, walls and ceilings.
Step 7–Functional Requirements
This is where a knowledgeable control room architect needs to be involved in understanding and extracting details for heating and ventilation, air circulation, specific lighting levels, and electrical/piping and communications equipment requirements.
The International Ergonomics Association says "ergonomics (or human factors) is the scientific discipline concerned with the understanding of interactions among humans and other elements of a system, and the profession that applies theory, principles, data and methods to design in order to optimize human well-being and overall system performance." This is exactly what the standards are calling for; hence, industry has to respond by re-training instrument engineers or employing trained professionals with HFE experience to design a control room. It's not just an instrument panel anymore.
Read Also: Human Factors: Planning & Design of a Control Room
The IEA continues, "Ergonomists contribute to the design and evaluation of tasks, jobs, products, environments and systems in order to make them compatible with the needs, abilities and limitations of people."
This is the motivation. Control rooms are about the people in them, not the equipment. "Domains of specialization within the discipline of ergonomics are broadly the following;" says the IEA website (www.iea.cc/ergonomics). "Physical ergonomics is concerned with human anatomical, anthropometric, physiological and biomechanical characteristics as they relate to physical activity. (Relevant topics include working postures, materials handling, repetitive movements, work related musculoskeletal disorders, workplace layout, safety and health)."
These are the required skills needed to design a console. It is not a task to be left to an instrument engineer or an architect.
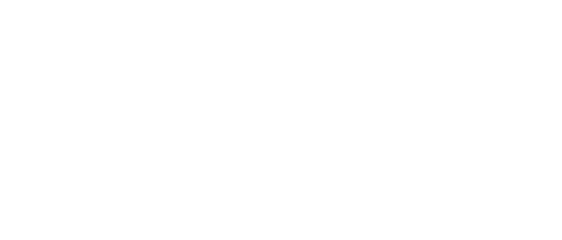
Leaders relevant to this article: