U |
OP LLC develops and commercializes technology for the refining, petrochemical and gas processing industries. In the 90 years since the company was founded and introduced its first thermal cracking process, it has created breakthrough technologies that make possible the formulation of a broad array of oil-derived products, such as motor fuels, plastics, detergents, synthetic fibers and food preservatives.
UOP’s expertise extends from research and development to engineering, process technology, technical services and the manufacture of adsorbents, catalysts and specialty chemicals that are used by customers to make end products of all types. Nearly every oil refinery uses one or more UOP processes and UOP sells more than 70 different catalysts used in various refining and petrochemical processes. It also offers separation and purification process technologies for the natural gas industry.
UOP applies the same rigorous methodology used to develop process technologies and related products to its own production processes. By taking this approach, UOP ensures that its products always meet customer needs.
Managing in Real Time
UOP has made extensive use of the Real-time Performance Management (RtPM) platform from OSIsoft. UOP uses the application’s multiple modules to create “skunk works” pilot facilities to prove process concepts during the R&D stage. UOP then scales these processes up from lab size to production volumes. UIP also uses the RtPM Platform for managing internal production processes for making intermediate chemical products for sale to end users.
“This flood of data provided our researchers with detailed information that they previously lacked, and also exposed numerous data quality problems that had been hidden by our hourly summaries.”
In 1996, UOP implemented the PI system—the “engine” that feeds the RtPM platform. With 65,000 tags and more than 20 control device interfaces, the PI system is used by more than 100 R&D users to monitor pilot plants. Two years later, having found that the new platform helped improve productivity, UOP implemented 65,000 additional tags and installed PI servers in five major manufacturing plants including Mobile, Ala.; Riverside, Ill.; Shreveport and Baton Rouge, La.; and Brimsdown, England. UOP pursued the system’s expansion as part of a Six Sigma quality program.In its RtPM implenetation UOP deployed a number of application modules with functions that include:⢠Archiving for all application data,⢠An interface to provide a hierarchical view of all alarms anywhere in the system,⢠A database that sorts real-time data, aliases, parameters or process specs into useful groups for use in programs and displays,⢠A graphics package for creating dynamic, interactive displays of data,⢠A batch monitor that helps attain an ideal batch for improved consistency,⢠Process templates, that facilitates process variable evaluation over repeatable time segments,⢠An interactive configurable environment for deploying RtPM information and applications over the Internet or corporate intranets,⢠An IT monitor for monitoring network status,⢠A computing engine for building equations and managing calculations on data from the PI system, and⢠A manual logger coupled with handheld terminals.Effective Research Tools
UOP’s research organization at UOP’s Riverside site and Des Plaines, Ill. headquarters uses the RtPM platform to streamline its research efforts in both refinery cracking processes and production of catalyst materials. One of the first research applications UOP developed, employed the PI system to view real-time data, replacing hourly data summaries. Using OSIsoft’s application programming interface and itsExcel-based reporting applications, the research staff also created their own program named PlantBook.PlantBook works in conjunction with OSIsoft’s ProcessBook application to combine real-time plant data with analytical data from the research staff’s Oracle database and from their Laboratory Information Management System (LIMS). PlantBook brings this information together and allows researchers and plant operations personnel to manipulate and interpret the data.This flood of data provided the company’s researchers with detailed information that they previously lacked, and also exposed numerous data quality problems that had been hidden by our hourly summaries. This resulted in a systematic correction of data quality problems originating with instrumentation, automation systems, and operational procedures. There is considerable expense in running pilot plant experiments, so this early improvement in data quality probably paid for much of the initial investment in the RtPM Platform in less than a year. Data is the product generated by UOP research, so it is vitally important that we maintain a robust infrastructure for systems generating, acquiring, storing, transferring, and manipulating data.UOP’s research staff continues to seek ways to provide a comprehensive look at plant data in a graphical manner. The company was looking for a way to combine process, analytical and calculated result data so it will be more meaningful for researchers. To meet this goal UOP developed a custom dataset add-in that’s capable of displaying gas chromatography data alongside regular data in a trend. “One of the nicest benefits of these new extensions of our RtPM implementation is that we’re getting new metrics that everyone can use to document and increase their productivity, efficiency and quality.”
Users can now see how plant operations are affecting their analytical data in real-time and can respond more quickly with efficiency and quality improvements in pilot plant operations. Analytical data can be easily trended along with the plant process data stored in the PI system, which has revolutionized the way pilot plants are monitored and operated. The system and its applications have been a success and it is now in use by well over 250 research users.Adding to Plant Functionality
The latest wrinkle in UOP’s implementation is the deployment of the RtPM toolsets for uses other than research and production. For example, at the McCook/Riverside plant, the RtPM platform is now used to enhance the efficiency of many routine, non-production activities such as machine maintenance, facilities inspections, fire extinguisher maintenance, safety ladder, and safety shower facilities inspections. The data gathered by the PI system is used extensively to fulfill UOP’s Health, Safety & Environmental (HS&E) Tier 1 and Tier 2 audits.Enhancing data collectionThe system’s web portal environment has been invaluable for integrating weather information into the various production processes at the five main plants. The company often heats recipe ingredients with hot air or infused steam during the production of complex products such as catalysts. The company’s process and control engineers have been trying to correlate ambient air humidity with product quality, to try and arrive at some method of accommodating local weather conditions at these plants. This is difficult when you’re attempting to make duplicate high quality products in Louisiana, where it’s hot and humid, and Illinois, where it can be cold and dry.UOP invested in weather stations for all its manufacturing sites, both for aiding in production as well as in monitoring any plant emissions. Once people found out about the weather stations they wanted to see what was happening locally at the plant weather-wise. Unfortunately only about 25% of the people onsite have the necessary application module installed on their machines. Our solution was to put the software system’s portal environment on the PI server to broadcast the weather data on UOP’s intranet. Now everyone can view weather data and relate it to plant processing activity.Process dashboardsOne of the major things UOP’s engineers have done to facilitate user creativity is the development of process dashboards that use the systems process monitoring application to give a quick snapshot of what’s happening within the manufacturing plant. Process dashboards rely on the alarm interface module to gather views of real-time production alarms coming from the plant control systems, the statistical quality control (SQC) alarms for process, and the analytical and vendor certificates of analysis (COA), which are calculated alarms. Decision trees were implemented so that if users get an alarm that something has gone out of spec or a physical quality control alarm that this process isn’t operating correctly, that person can simply click a button and go either directly or via the web to the decision tree display that will walk them through an appropriate response to the alarm.
Mike Jackson is the global system applications specialist for UOP LLC based in Des Plaines, Ill. His e-mail address is [email protected]. Joseph Schaaf is a software engineer with UOP LLCbased in Des Plaines, IL. His e-mail address is [email protected].
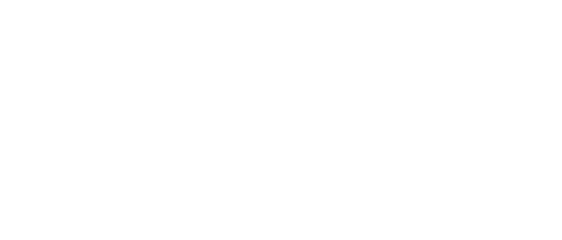
Leaders relevant to this article: