Nonetheless, additional flow measurement improvement can be achieved by transmitting signals to the control system or data acquisition system using digital signal transmission in place of analog signal transmission techniques.
Analog Signal Transmission
Flowmeter measurements can be transmitted to the control system in a variety of ways. In process control systems, it is common for the flow transmitter to generate an analog signal (usually 420 mA) that is wired to the control system. The analog input module in the control system then converts the analog signal to a digital measurement that is used by the control system.
Many flowmeters are inherently digital devices (to improve stability and performance), there can be as many as three signal conversions taking place when using analog signal transmission:
-
An analog-to-digital conversation that digitizes the raw sensor signal
-
A digital-to-analog conversion that converts the transmitter measurement to an analog signal that represents the flow measurement
-
An analog-to-digital conversion that converts the analog signal that represents the flow measurement to a digital measurement in the control system
The digitization of the raw sensor signal is included within the accuracy specification of the flowmeter. The other two conversions can introduce significant measurement error, especially when the analog signal is low in its range and when environmental factors are considered.
For example, a typical analog output circuit of a magnetic flowmeter will add up to 0.06% of full scale error to the flowmeter accuracy statement. The accuracy of an analog input to a distributed control system (DCS) adds about 0.03% of full scale. In contrast, the accuracy specification of an analog input module for programmable logic controllers (PLC) has been noted to be as high as 0.40% of full scale. The table calculates the percent rate error associated with these signal conversions for a linear flowmeter.
Examination of the table indicates that these conversion errors can be significant, especially at low flow rates. In some applications, the errors caused by conversions at some flow rates can exceed the accuracy of the flowmeter.
Performance can be improved somewhat when the frequency (pulse) output of the flowmeter transmitter is used because the digital-to-analog conversion used to generate the analog signal is not needed. However, the frequency signal must be converted to a digital value in the control system.
Environmental factors, such as ambient temperature variations, can further degrade the performance of each of the conversions. However, suppliers may not publish these specifications even though temperature effects can be significant. For example, consider a converter with a temperature coefficient of 0.005 % of full scale per degree Celsius. This may seem small, but when such a device is located outdoors where the ambient temperature can vary by 25° C, the error introduced could be 25*0.005, or 0.125% of full scale. For a linear flowmeter operating at 10% of full scale flow, the error introduced could be as high as 1.25% of rate.
Noise and Other Interference
Electrical noise, radio frequency interference, electromagnetic interference and other installation-related issues related to the analog signal can also degrade measurement accuracy. Cabling problems, including those stemming from wet signal cables, can partially ground the signal wires and adversely affect accuracy. Loose or poor connections can alter the signal in some installations. Connecting too many receiving instruments in series and/or paralleling additional instruments to voltage signals can introduce error as well.
Fieldbus Signal Transmission
Fieldbus communication allows the control system to communicate digitally with the flowmeter. As such, the need for the transmitter to generate an analog signal is eliminated. Further, the need for the control system to measure and interpret the analog signal is also eliminated. Eliminating these conversions can improve the quality of flow measurements. In addition, other information, such as secondary measurements and flowmeter status information will also be available using digital communications. Flow measurements that are inherently digital, such as vortex shedders, may not require any analog-to-digital conversion. There are a number of fieldbuses however. The most commonly applied fieldbuses to process control are HART, Profibus-PA, and Foundation fieldbus (FF). Fieldbus segments (wires) can be used to communicate with multiple transmitters and supply their power (See Figure 1). A flowmeter with a HART output can generate an analog signal that allows the use of existing wiring and analog signal transmission. Digital communication is implemented by superimposing digital signals on the analog signal, allowing simultaneous analog and digital communication.HART Digital Signal RequiredReplacing a flowmeter with an equivalent HART transmitter will not necessarily improve flowmeter performance because an analog signal is still generated by the transmitter and converted by the control system (See Figure 2).
FIGURE 2
To eliminate the need for the transmitter and control system conversions and the errors associated with them, the control system and HART flowmeter must communicate digitally. Dick Caro, a consultant with CMC Associates in Acton, Mass., and author of the book The Consumer Guide to Fieldbus Network Equipment for Process Control, adds, Existing wiring can still be used to power the HART transmitters, but the existing control system interface will have to be upgraded to include the capability of HART digital communication with the transmitter.
HART digital transmission was generally considered too slow to be effective for flow control loops. However, Wally Pratt, the chief engineer with HART Communication Foundation, says, The new HART C8PSK specification allows C8PSK-compatible transmitters and control systems to operate at higher data rates that are sufficiently fast for most flow control loops. Caro explains that once this is done, HART C8PSK-enabled systems can have HART and HART C8PSK-enabled transmitters communicating digitally on the same HART segment wiring.
FIGURE 3
The capabilities of Profibus-PA and FF transmitters are similar with regard to flow measurement. However FF transmitters can contain standard field control blocks that can be configured to control and perform calculations. This means that FF transmitters such as linearization and pressure/temperature compensation that would otherwise be located in the control system or in a flow computer. Profibus-PA transmitters cannot perform these functions, but they can be performed by the control system. With field control, flow transmitters can contain proprietary algorithms that may be superior to conventional algorithms. Locating flow totalization in the transmitter can sometimes improve performance because the totalizer block is usually more accurate if since it usually runs more often in the transmitter than it would in the control system. Flow Computers InsideFlow measurement systems often use flow computers to incorporate information from various measurement devices, such as from a flowmeter, pressure transmitter, and temperature transmitter to compensate the flowmeter measurement for the operating pressure and temperature. Hans Kwee, an instrumentation/process control engineer with Gaz de France in the Netherlands, notes, The performance of flow computer systems would be improved if the measurement devices could communicate with the flow computer using fieldbus. He laments the lost opportunity because flow computers are not compatible with fieldbus.Rick Heuer, sales manager for the Flow Technology Division of Emerson Process Management in Houston, replies, Flow computers that communicate with instruments via fieldbus are available for process applications. However, the use of fieldbus in flow computers is dependent upon the availability of a flowmeter that can communicate via fieldbus. For example, Coriolis mass flowmeters and differential-pressure flow transmitters that communicate via fieldbus are readily available, whereas turbine flowmeters are generally not available. In these applications, flowmeter selection may be limited by the fieldbus communication requirement. Ed Morrison, a consultant with Automated Services, Houston adds, Flow computers using fieldbus instruments have the capability of being used for custody transfer in North America. However, these flow computers must be certified by a third party to ensure compliance with applicable standards. Morrison continues, No such flow computer has yet been certified for custody transfer.The First to ComplyThe Merluza off-shore oil platform is located approximately 200 km off the coast of Brazil. Carlos Moura and Nerivaldo Marangão, technical consultants with Petrobras in Rio de Janeiro, Brazil, say, Using fieldbus transmitters to retrofit this platform reduced the down time and its associated lost revenue. The window for equipment being out of service averages only about 4 hours per day and could be less. They continue, Using fieldbus transmitters helped Merluza to be the first Brazilian offshore platform to comply with ANP (Brazilian National Petroleum Agency) standards for custody transfer.Heuer adds, A multivariable flow transmitter with an integral flow computer that can communicate via fieldbus avoids the communication issues by performing all functions within the same device. Communication to the control or data logging system can be performed using fieldbus and provide access to the measurements.In contrast, Wes Meger, an instrument/electrical supervisor in the Operations Reliability Group at Suncor Energy, Fort McMurray, Alberta, Canada, has non-custody applications where non-fieldbus instruments can provide the required performance as transmitters improve and become more stable. The additional accuracy afforded using fieldbus communications might be nice, Meger reports, but the availability of flowmeter diagnostics is a larger driver.Diagnostics Communicated Here
A part of improving flowmeter performance is increasing the amount of time that the flowmeter produces good measurements. The ability to communicate flowmeter diagnostics to the control system can allow faster detection of failed or failing flowmeters. In addition, diagnostics signals can alert users of impending failures and give them enough time to prevent them before they actually happen.Joe Incontri, director of sales and marketing for Krohne in Peabody, Mass. says, Fixing the flowmeter prior to complete failure keeps the flowmeter producing good measurements for a larger percent of the time and can reduce the number of process upsets. For example, consider a magnetic flowmeter that has diagnostics that can detect electrode fouling.
Continue Reading
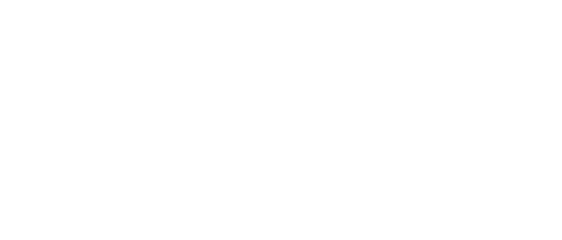
Leaders relevant to this article: