Two types of process analyzers that can be applied in cooling towers and flares are gas chromatographs (GCs) and flame ionization analyzers. Gas chromatographs can measure the chemical composition of just about any form of liquid or gas, and can be used to monitor areas, waste gas streams, waste and cooling water. Flame ionization systems are particularly good at measuring total hydrocarbon content (THC) in a gas stream at high temperatures and with up to 100% water vapor (See Figure 1).
Pharma Puts Analyzers Online
More regulation is coming to the pharmaceutical industry. Process Analytical Technology (PAT) is an FDA program that promises better quality control of pharmaceuticals and will require the use of online process analyzers. Begun in part by Ajaz S. Hussain, Ph.D., deputy director, Office of Pharmaceutical Science, CDER, FDA, PAT is a system for designing, analyzing, and controlling manufacturing through timely measurements of critical quality and performance attributes of raw and in-process materials and processes with the goal of ensuring final product quality. Thus, PAT allows for continuous process manufacturing improvement.
The PAT program will do for the pharmaceutical industry what similar process improvement programs have done for other industries. According to Honeywell Process Solutions Life Sciences marketing manager Mark Albano, the approach defined in the PAT initiative is consistent with approaches that have been used by other industries to improve control of their processes. The program goes beyond just process measurements, and includes all aspects of effective process automation and information management.
While off-line testing refers to lab-based checks, at-line, in-line, and on-line are three terms used in describing the degree of connection of the analyzer to the process stream. In a Web-based paper, Peter Scott, quality assurance analytical services, AstraZeneca, Westborough, Mass., points out the differences. “The first step away from off-line testing (laboratory separated from the production plant), is at-line testing. This is the movement of process-dedicated testing equipment to the production line to provide rapid results. One advantage is elimination of the transfer of samples involving time delays.
Along with traditional tests such as dissolution, assay, friability, hardness, and thickness, at-line testing could also include accelerated dissolution rate analysis and NIR tablet analyzers. One approach of process analytical chemistry is on-line testing, which either draws samples or monitors periodically. Another mode is in-line testing, which places probes in constant contact with drug product. The advantage of on/in line testing is better control of the process.”
One pharmaceutical that has already explored NIR at-line testing is Nycomed Pharma in Denmark. Kent T. Møller said, in an Analytical and Research Technology article (Sept., 2004), “NIR is very useful in the pharmaceutical industry. The validation (of our test) shows that the NIR method was specific, accurate, and precise. Because the NIR apparatus is robust and the measurement requires no laboratory facilities, the analysis can easily be integrated into the production plant for at-line determination. Thereby the pharmaceutical industry could move a step closer towards parametric release determinations.”
Track Process Chemicals
Other industries can also benefit from on-line process analyzers. The quality of the chemicals used for manufacturing semiconductors requires continued monitoring and precise control of wet processes to produce quality product. The SEZ Group in Zurich, Switzerland is a supplier of wet-wafer surface preparation equipment to the global semiconductor manufacturing industry. According to Michael Roth, director global marketing communications and operations, the SEZ Group is using ABB’s Wet Process Analyzer (WPA) in equipment it sells for continuous on-line monitoring of the chemical concentrations of a wide range of etching, cleaning, and stripping solutions. WPA is a Fourier Transform Near Infrared (FT-NIR) spectrometer connected through optical fibers to a Teflon sensing cell called the Clippr. Being able to extend the lifetime of baths such as SC1 and SC2 by 25–30% can result in a ROI for the analyzer in typically less than a year.
“Fringe” Technologies
New technologies, especially those that are spectrometric-based, are extending the capabilities of process measurements. For example, Fiber Brag Gratings (FBGs) are imprinted onto optical fibers by means of a one-time treatment with UV radiation. The resulting sensor can measure strain, temperature, pressure, vibration, and acceleration. Bayer Technology Services (BTS) has applied this technology from Advanced Optics Solutions GmbH to temperature, producing multiple imprints (sensors) on a single fiber, each of which can be distinguished spectroscopically on the basis of unique period lengths.
According to Dr. Wolfgang Borchers, this sensor array is capable of producing 3D temperature measurements in process fluids. BTS’ SpectroBAY spectrometer platform can combine temperature measurements with NIR substance concentration measurement in a single device. He adds that temperature profile measurements in packed beds of catalyst enable efficiency gains of up to 10%.
Clevett says GCs still enjoy a lot of use in the petroleum and petrochemical industries. However, because of a GC’s relatively long cycle times, users are looking toward spectrometric techniques, which can provide much faster response times, use in-situ probes, and take advantage of fiber optic transmission. These techniques include near infrared (NIR), mass spectrometry, and Raman Spectrometry.
The use of diode array technology allows Ametek’s Model IPS-4 integrated process spectrometer to measure up to eight wavelengths and quantify five measurement components simultaneously—with no moving parts. It comes with chemometric capability to solve complex measurement problems and covers a spectral range of 220–110 nm. The instrument’s xenon lamp has a life expectancy of two or more years. The unit has serial ports plus a Fast Ethernet port, and includes a built-in Web server to offer Internet connectivity.
MRI For The Process
Invensys has added crude oil distillation and fluid catalytic cracking to its growing list of magnetic resonance analysis (MRA) applications for hydrocarbon and petrochemical processes. MRA uses the same MRI technology found in hospitals. Refiners apply the Process MRA measurement technology to analyze material feed and product streams from an atmospheric crude distillation column for forwarding to a control algorithm. MRA provides non-invasive sampling, precise analysis, and high availability; and requires little maintenance. Crude oil blending measures crude oil quantity to blend crude and compares the ratio to standard specification. Fluid catalytic cracking measures both raw material feed and product streams off the FCCU, and sends the data to the control algorithm.
Communications and software key to the future
Clevett suggests that since most on-line analytical techniques including GC systems are computer-based, industrial networking and software play a very important part in the overall system design. Industrial networking in the form of fieldbus has much to offer, says Michael Fersky, process analyzers marketing manager at Emerson Process. “Not only does fieldbus enable the customer to monitor process conditions from the control room, but it also decreases installation costs and enables customers to monitor the health of their analyzer and detect problems before they happen, thereby increasing process availability and reducing maintenance costs.” Other trends, according to Fersky, include micro-analyzers using “lab on a chip” sensors, wireless communication, and smart modular plug-and-play elements that can readily be combined into sampling/sensor systems as championed by NeSSI.
Today, we pretty much take software for granted because it’s built into or comes with much of the hardware we buy. But apply it to process analytics, and it plays several important roles. Says Pete Anson, Emerson Process’ instrument product manager, “Software is being leveraged to provide advanced diagnostics, reduced lag time from sensor readings to analyzer, easy-to-use menu screens on the analyzer’s display, on-board troubleshooting in the analyzer, and multiple languages native to the analyzer.”
Take software a step further and combine it with wireless communications, and you get more versatility. According to Honeywell’s product manager, Thomas Griffiths, software can help make the analyzer “smart,” enabling configuration via a wireless device (See Figure 2).
Honeywell’s UDA2182 dual analyzer measures pH, ORP, conductivity/resistivity or concentration, and dissolved oxygen concentrations. An IR port allows configuration from a Pocket PC or laptop using Process Instrument Explorer software.
Software can also help provide an easy and logical way to configure the analyzer, for example, by using function blocks. He adds that Ethernet can also help staffs that are short on help save a lot of steps when they need to get a handle on process measurements at fair distances from the control room.
Definitely, according to Emerson’s Anson, web-enabled connectivity, wireless, Ethernet TCP/IP networks, automatic sensor ID and enabling upon connection to a digital analyzer will be key features you’ll see on new instruments.
Wireless communications at the sensor/analyzer end can save a few dollars. Says John P. Connelly, sensor product manager at Foxboro Measurements and Instruments Div., Invensys, “E’chem sensors and especially pH sensors when connected wirelessly provide low cost and fast installation, resulting in multipoint and redundant measurements at lower cost per point.”
The portability of wireless also suggests a worthwhile application—the temporary location of an analyzer where and when it’s needed. For example, if an engineer decides that after a trial period the analyzer is really needed in a particular spot, he can opt to leave it, or replace it with a wired device—provided the wiring is in place. Later on, he can move the wireless analyzer to other locations.
Basic Concerns Remain
While some of these advances are, admittedly, esoteric, users are still concerned with the simple issues: reliability, fast implementations, cost per loop, and sample handling. Fersky says that customers’ needs haven’t changed. They still want accurate measurements that are repeatable over time with minimal calibration and maintenance. While many vendors offer serial connections and fieldbus-connected instrumentation, Fersky says that many of his customers still prefer analyzers connected via 4–20 mA to PLCs or DCSs. Customers also want transmitter style analyzers that they can move closer to the process and eliminate long sample lines, thus enabling more efficient process monitoring and faster installation at a lower cost.
However, process site implementations often require analyzers that can work in hazardous areas and in changing ambient conditions and withstand vibration. Other needs include multi-component analysis of solid and liquids, smaller sized analyzers, on-board diagnostics and processing capabilities.
Griffiths’ customers want to have the flexibility with an analyzer that allows them to get it up and running quickly. Once the instrument is on-line, they want to be able to access it quickly and use the information it provides to make process decisions.
Anson sees the industrial process world as staid and unwilling to accept change or trendy innovation. Most plants are looking for the basic criteria of value, reliability, durability, longevity, and vendor support—sometimes translated as collaboration.
For example, Archer Daniels Midland’s (ADM’s) ethanol facility in Cedar Rapids, Iowa has to maintain pH levels that keep sulfur dioxide levels low in its product. The trick is that pH has to be monitored in a fermented mash at 235° F during the distillation process. “We tried taking pH readings directly from the process, but the 235 F temperature ate sensors,” says Lloyd Feickert, instrumentation supervisor. To reduce excessive sensor costs, Feickert set up a slipstream arrangement, where a sample of ethanol is run offline to cool down to 140° F before the measurement is taken.
While this arrangement extended pH sensor service life, process conditions caused temperature fluctuations within the slipstreams. The solution to this problem was to have Foxboro Measurements & Instruments Div. collaborate with Feickert to develop a field-rebuildable measuring electrode that could withstand severe temperature cycling to 250° F. The rebuildable electrode incorporates technology from the Foxboro DolpHin pH sensor line and has improved sensor service life from 10 days to four months while located directly in the process.
While much of this discussion has considered analyzer trends and applications, it’s easy to forget that the analyzer can provide a measurement that’s only as good as what’s delivered to it—just like the ADM story where Feickert tried moving the sensor out of the immediate process. Ronald A. Downie, systems engineering manager at Teledyne, points out that the results of poorly designed sample conditioning vary from the analyzer not operating at all to an analyzer operating only with extremely high maintenance requirements and/or giving erroneous or poor data. Downie provides some practical tips in sample handling systems in a five-page white paper.
Getting What You Need
Whatever the process variable or constituent to be monitored, there’s a process analyzer to do the job. But achieving analyzer reliability is no accident, and Clevett suggests that engineers and maintenance technicians receive adequate training to ensure that their skills are appropriate for the job at hand. This will usually require that companies set up organizational structures to make sure this happens. And, watch for the weakest link—the sample handling system. Process analyzers can help manufacturers keep their processes running at maximum efficiency and keep the government regulators away.
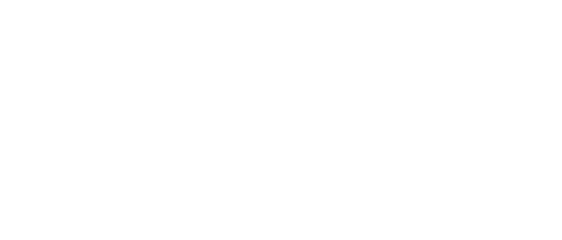
Leaders relevant to this article: