IN OLDEN days, single-loop controllers cost hundreds or even thousands of dollars each, came in pneumatic and electronic versions, and each controller was about the size of a modern “tower” PC. Process plants installed them in 19-in. racks that stretched for 20 or 30 feet. Each had analog, bar-chart readouts, and most engineers tuned them so that, when the loop was at setpoint, the big red arrow indicator was smack-dab in the middle of the vertical bar. The indicators were so large, an operator could glance down a rack of controllers, and a quick look would tell if all the pointers were centered, meaning the plant was “lined out.”
Even today, modern HMI screens often have “faceplate” displays of 8, 16 or 32 loops with vertical bar chart indicators centered at the setpoint. Control engineers in the 1940s and ’50s performed spectacular feats with those old “large case,” single-loop controllers, setting up feed-forward and cascade control schemes that still boggle the mind.
Then along came microprocessors, and the old pneumatic and electronic analog controllers died off, replaced by micro-based, ¼ DIN, single-loop devices, multi-loop controllers, distributed control systems and PLCs. Today, a single-loop controller is basically a commodity control, available from catalogs, distributors, local stores, and on the Internet for about $150-$200. For that money, you get auto-tuning, dual setpoints, ramping, fuzzy logic, Ethernet connections, and other features undreamed of by engineers 50 years ago.
The capabilities of these modern loop controllers helps keep them alive. With such a device, it’s possible to control small processes, systems, machines and equipment at relatively low cost, and without needing a PLC or control system. Temperature controllers, for example, continue to sell in large quantities, hitting nearly $1 billion in sales in 2004, according to Venture Development Corp.
Many major process control system vendors gave up years ago on loop controllers, probably because Asian suppliers made them unprofitable, and loop controllers detracted from their DCS sales. Some loop-controller vendors died off, or got acquired and reacquired. MicroMod Automation was formed in 2004 to acquire the loop-controller lines of Fischer & Porter, Bailey, Kent-Taylor and Taylor Instruments from ABB, and Moore Industries-International added the loop controller line from Powell Process Industries.
As you will see in the following roundup, only a few new, general-purpose loop controllers were announced in the past few years. Nearly every new controller fits a niche of some kind, such as boiler control, chlorination, temperature, mass flow and so on. Some new or existing devices now have web connections.
If ISA ever gets the SP100 wireless standard off the ground, it could inject new life into the loop controller industry. Imagine what you could do with a $150 single-loop auto-tuning controller that has a wireless fieldbus interface. So stay tuned.
Product Roundup:
Loop Controllers
Boiler Controls Step Right Up
SteamPAK series of boiler control packages come ready to use with pre-loaded, pre-configured control strategies. Each package comes with dedicated installation and startup instructions that describe how to connect the field instruments, and use the boiler-specific displays to start up a boiler. In many cases, the payback period reportedly is less than 12 months. MicroMod Automation; 585/321-9202; www.micromodautomation.com
Chlorination Controller
Model 555 1/4 DIN controller handles flow proportional control, residual control, compound loop control with lag times, and dechlorination with sulfur dioxide, making it suitable for use in the water and wastewater industry for chlorination and dechlorination processes. The front panel is NEMA 4X rated for protection from water and corrosion. When performing compound loop flow pacing control, the unit clearly displays flow rate and residual chlorine simultaneously. Moore Industries-International; 818/894-7111; www.miinet.com
Internet Controller
I-Series meters/controller with embedded Internet connection lets users monitor and control processes from anywhere via a web browser. Using the controller with a heater, for example, a technician can monitor temperature, change alarm points, turn the heater off, and make other modifications without special software. Ethernet and Internet functionality is embedded, so it can connect directly to a network, instead of plugging into a computer's serial port. Omega Engineering; 203/359-7815; www.omega.com
PID Control via the Internet
Master Controller module lets users create a “virtual HMI,” allowing single-loop and multi-loop PID controllers to be controlled and monitored via any networked PC with a standard web browser. The controller also can log system data directly to CompactFlash in Microsoft Excel-compatible CSV files, which can be retrieved via USB or the web-server. Red Lion Controls; 717/767-6511; www.redlion-controls.com
1/8 DIN Controller Spells it Out
Model 32H8 1/8 DIN temperature/process controller has a text display, high accuracy input, and five on-board process recipes. The text display reportedly makes it easy to use or configure the controller. When accessing the controller user interface, every parameter is accompanied by a scrolling text message to describe its function. Scrolling alarm and event messages can alert an operator of plant condition changes. Messages can be customized with a PC tool. Eurotherm; 703/669-1330; www.eurotherm.com
Embedded Digital Signal Conditioners
CellMite Model 4326A Intelligent Digital Signal Conditioner uses its digital and analog outputs to tune and control local actuators. It includes signal conditioning, excitation and sense voltages, digitization, and processing power, along with analog and digital serial outputs suitable for direct connection to a PC. A sensor network can be established by bussing together multiple units. Electro Standards Laboratories; 401-943-1164; www.electrostandards.com
Tough Mass Flow Controller
Max-Trak Model 180 industrial mass flow controller for gases is NEMA 6 (IP67) compliant for use in applications needing frequent wash-downs or hose-downs. It has a fully enclosed valve to minimize leak-in paths. The unit measures and controls gas mass flow rates from 0 to 400 slpm in a flow body a little over 5 in. long. Accuracy is 1% FS with repeatability of 0.2% FS. Sierra Instruments; 800/866-0200; www.sierrainstruments.com
Temperature Controllers
Series RMB and RMC mainframe-style, single-zone temperature controllers are suitable for runnerless molding applications. The controls allow operators to adjust the current trip from 1-15 amps. Using Modbus communications, users can set or change all zones from a desktop computer, a handheld device, or any other module in the mainframe. It has an operator keypad, two LED displays, and three indicators for heat-current, alarm and manual mode. Athena Controls: 800/782-6776; www.athenacontrols.com
Multi-loop Controller Software
pCon multiloop controller software provides auto-tuning temperature or process PID control of up to 128 loops for approximately $22 per loop. A free trial version can be downloaded from the company’s web site. It uses Excel files as its database, can be integrated with HMI programs, and can be remotely controlled by a PLC. I/O sensors, outputs, relays and PLCs can be connected locally or remotely using OPC. PC-PID: 717/671-1566; www.pc-pid.com
Controller/Positioner
Type 1067 PID controller/positioner is compatible with virtually any rising-stem or quarter-turn valve/actuator used for process control. The unit consists of two components: the valve stem position pickup and a microprocessor-driven pneumatic controller. The control or position setpoint can be adjusted via the integral display panel, or sent remotely via common current (0–20mA, 4–20mA) or voltage (0–10 VDC) signals. Burkert: 800/949-2091; www.burkert-usa.com
DIN Temperature Controllers
Plus series DIN temperature controllers have plug-in modules for outputs, inputs, alarms and communications, so users only need to keep one type of controller in stock, and adapt it for each application as required. Models include 1/16, 1/8 and 1/4 DIN size units sold under West and Partlow brands. Controllers have dual setpoints that can be selected from a remote location, as well as PID control with pre-tuning and self-tuning. Danaher Industrial Controls; 800/873-8731; www.dancon.com
Flow Computer
MVI56-AFC flow computer for the ControlLogix platform allows integrated process control and flow computer capabilities in a single-slot, in-rack solution. It supports 16-meter runs, and has three built-in Modbus ports, allowing user access to a defined meter data table. One Modbus port can be configured as a Master, providing an interface to gas chromatographs for gas analysis or any other Modbus slave devices. ProSoft Technology; 661/716-5100; www.prosoft-technology.com
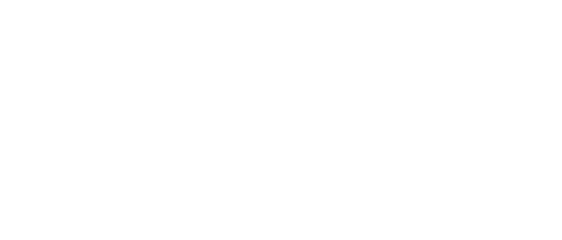
Leaders relevant to this article: