Two previous articles in this series pointed out the need to approach a process analyzer project with sufficient information and justification to minimize the lifetime cost of the project from conception through retirement. The first article, "How to Launch a Lifecycle Reliability Program," asserted that most lifetime project costs are determined, though not necessarily expended, by the end of the design and development phase—that is, after detailed engineering and before construction. The second article, "Accurately Scoping Process Analyzer Projects," addressed scoping an analyzer system project sufficiently before construction on the premise that changes are less costly to make on paper and in computer files than during construction and ongoing maintenance.
This article takes an additional step by illustrating how correct project engineering documentation deliverables help focus on gathering enough information about the project during concept development and detailed design to minimize or eliminate scope changes and rework during construction and ongoing maintenance.
Indeed, as Bruce Barkley and James Saylor explain in Customer-Driven Project Management—Building Quality into Project Processes, “Documentation is an essential project quality management tool because it disciplines the process and ensures that quality methods have been built into the design and production process. The project manager should see documentation in terms of a front-end process driving work rather than as a back-end process that records what work has been done and how.”
Table I below shows typical documentation that might be submitted to justify project approval at the end of the concept development stage of an analyzer system project.
TABLE 1: TYPICAL DOCUMENTATION SUBMITTED FOR SCOPE DEVELOPMENT
Document Name or Information | Information Needed |
Justification Scope Text | Understand the goal of the project and the analyzer system |
P&ID | Understand the manufacturing process and determine the physical conditions for the analyzer system |
Preliminary Safety Review | Determin how to address safety concerns with project execution and ongoing operation and maintenance |
Environmental Impact Review | Establish the project completion will not adversely impact site waste processing |
Utility Impact Review | Establish that sufficient utilities are available to operate and maintain the capital installation |
Custsheets, Sketches, Drawings and Meeting Notes | Go-bys to allow likely team members to prepare for kick-off meeting |
Alternatives for Solving the Problem | Increase safety, increase quality, lower cost, shorten schedule |
Project Schedule/Time Line | Human resource planning |
List of Project Team Members | Establish working realtionship and give early idea for human resource planning |
Instrument Loop Sheet | Understand how the signal is to be used and identify the signal type and power source |
Spec Item Cutsheets | Provides physical idea of required technology and hardware deliverables |
PFD | Estimate chemical concentration to determine and justify the measurement principle |
SHS Sketch or Drawing | Provide a physical idea of project hardware deliverables |
Photos | Provide a physical idea of project hardware deliverables |
Instrument Location Drawing | Provide a physical idea of project hardware deliverables |
Most control systems engineers and designers would agree that the P&ID, instrument loop and PFD/energy and materials balance (process flow diagram) might aptly be called the “road maps” for analyzer systems and most other instrumentation projects. (Some might argue that the PFD is not necessary unless corrosion needs to be addressed; that may be true for conventional instrumentation, but the PFD is absolutely essential for analyzer systems engineering because analyzers exist to measure chemical composition. Therefore, a successful analyzer application depends upon knowledge of the chemical composition during the concept development stage.)
Table II below is a small sample of the myriad and often esoteric documents and information generated during and required for successful detailed engineering and procurement, along with many details that need to be included in those documents.
TABLE II: TYPICAL DOCUMENTATION FOR DETAILED ENGINEERING & PROCUREMENT
Engineering
- Instrument index
- Tagged equipment data sheets
- Engineering scope and specification narrative
- Sample probe type and design
- Sample return/disposal type and design
- Alarms generated in analyzer system, DCS, or SIS
- Digital signal protocols
- Use of analyzer on-board I/O capability for external devices
- SIS Interlock logic
- Identify piping and tubing metallurgy and pressures
- Identify "closely coupled" analyzer options (eg. spargers)
- Estimate of direct labor identified by craft and contruction indirects/overhead
- Identify requirement for associated personnel safety monitors
- Analyzer house close to roadway to ergonomically supply cylinder gases
- Analyzer house sufficiently away from vehicular traffic, piperacks, and electrical right-of-way
Procurement
- Procurement/purchasing specification
- Documentation approval deliverables during system construction
- Documentation deliverables with system delivery
- Documentation as-built deliverables after system startup and commissioning
- Determine suitability of supplier safety record and credit rating
- FAT schedule, plan and personnel
- FAT punch list and agreed method, personnel, schedule and documentation for resolution
- SAT schedule, plan and personnel
- SAT punch list and agreed method, personnel, schedule and documentation for resolution
- Startup and commissioning assistance
- Order tagged items and accessories in order of expected delivery schedules
Many of the documents and their contents are, or should be, routine for capital projects, including control systems in general. But they are included in this list with the analyzer-specific documents so that we do not lose sight that, though analyzer system are highly specialized measuring instruments, they are nonetheless part of control systems technology.
Table III below with the construction documentation is actually a continuation of the detailed engineering documentation and includes nearly all of the latter. The additions are to address construction safety and to prevent us from overlooking or assuming too much about bulk materials/non-spec items while being so heavily involved with the spec items and their procurement.
TABLE III: TYPICAL DOCUMENTATION FOR CONSTRUCTION
Document Name or Information | Information Needed |
Construction scope and specification | Ensure that general contractor/builder has complete information to perform work |
Pre-construction safety review and plan | Agree on safety expectations, safety training, safety permitting, safeety issue resolution |
Self-contained breathing apparatus required | Personnel safety |
Division of work | Identify work appropriate for general contractor, owner-client specialists and supplier technicians |
Dismantling, decontamination, demotion, disposal required | Construction pre-work to compress construction schedule |
Repair, relocation, remediation required | Reuse existing equipment |
Pre-work construction (eg. conduit, wiring, piping) | Compress construction schedule and anticipate potential problems otherwise overlooked |
Temporary shutdowns required for construction completion | Minimize client operations costs and inconvenience |
Analyzer house and/or analyzer system weight and size | Develop safe and technically feasible lift plan |
Lift required near lethal-service piping | Develop safe lift plan |
Other activities in construction area | Benefit from construction project synergies or avoid construction schedule conflicts |
Identify construction crafts required | Efficient personel planning and determine how many craftsmen can safely work simultaneously |
Determine hardware deliverables storage location and time of deliverables | Material tracking and control from supplier to field installation |
Bill of material of bulk commodities | Facilitattes pre-work and minimize delays during final construction and startup |
Bulk commodities are instrument tubing, mounting hardware, conduit, wiring, fiber-optic cable, junction boxes, terminal strips, and so on. Piping and valves may or may not be spec items or bulk commodities, depending on their chemical service. When construction presents a safety issue, it must simultaneously be addressed as a cost issue. For example, a “simple” lift over lethal service piping or a hot tap to create an analyzer sample point create challenges that are more safely and economically addressed in earlier project stages. The lift is generally forbidden by operations safety procedures and could add significantly to the cost of construction logistics; hot taps are generally straightforward, but nonetheless require following a detailed procedure that costs money and time.
At this point, we must note that the terms “scope” and “narrative” were used frequently in the previous discussion and in the corresponding tables. The analyzer systems project engineering team must be clear that each of these scopes and narratives include much of the same information, but in different forms and levels of detail for different audiences. The initial scope for concept development will often take on an “executive summary” tone to let decision-makers know what needs to be done, why and how it will affect operations and budgets.
The scope that is developed during detailed engineering is much more detailed to give the engineering team highly specific technical details of what to purchase and what documents need to be developed, and to work out potential technical conflicts. The construction-stage scope is written for project execution. I like to write construction scopes as if the field construction supervisor plans to unstaple the pages and give each section to the respective construction crafts to install their respective spec items and bulk commodities. Naturally, this is not what happens, but this idea helps focus on construction’s mission to safely and efficiently put together materials that benefit the production owner/client.
Table IV below is deceptively terse because I want to restrict this discussion to documentation rather than to go too deeply into maintenance operations, an apt subject for another article. Therefore, project documentation can best address ongoing analyzer systems operations and maintenance by ensuring that at the end of capital construction, the project has an obligation to supply the analyzer system maintenance group with the most complete documentation possible for its 10-20 year experience with the analyzer system.
TABLE IV: TYPICAL DOCUMENTATION FOR OPERATIONS AND MAINTENANCE
Document Name or Information | Information Needed |
Pre-startup safety preview and punchlist | Ensure the analyzer system is complete and safe |
Analyzer system job book | Technical and financial audit trait for replication and replacement |
Project-sustan stage job book | Documentation for ongoing lifetime operation and service |
As-built documentation | Accurate drawings to support operation, service and replication |
Service personnel loading requirements and logistics | Ensure adequate sustain-stage manpower, parts and supplies |
Also note that the project closure documentation, often known as the “job book” for engineering and capital accounting archives may not be in the most useful format, nor include everything important to maintenance. For example, the pre-FAT analyzer system runout data, including stability testing and chromatograms, may not be important to engineering and capital accounting personnel. Therefore, it behooves engineering teams who need the continued cooperation and support of the analyzer maintenance group to put together documentation that is partially customized for that purpose.
Furthermore, the operations and maintenance documentation will include the current revision of nearly all of documentation from the preceding project stages. Earlier revisions are archived should the need arise to trace the history of a part of the project. There are two reasons for retaining documentation—to avoid “reinventing the wheel” the next time a similar project arises, and to provide a documentation trail to justify legally and financially why and how something was done.
Legal and accounting professionals may take a different view, but generally a mutually agreeable solution can be worked out once the parties understand each other’s needs.
No list of documentation is offered for the disposal and demolition life-cycle stage. Generally, an analyzer system at the end of its useful life is either part of an analyzer system replacement project or is part of a much larger demolition project and, therefore, will be explicitly included in narratives and drawing markups. Either way, the principle concerns associated with such an analyzer are safety and salvage. On the safety side, the project team must assure that the loss of measurement and signal do not create safety and process control problems and that hazardous process stream contents in the sample and sample return lines, sample handling system and analyzer do not create personnel and environmental hazards.
Both these safety concerns must be raised in the scope development project phase and directly addressed in the preliminary safety review, kept in mind during the detailed design phase, and again addressed directly in the construction and commission phases in both the construction kickoff safety review and the pre-startup safety review. Generally, the production owner/client will have a specific way to address removing the old analyzer and can offer constructive suggestions for executing the removal. On the salvage side, the analyzer maintenance group will know early in the project what parts of an old analyzer system are salvageable and which are not. The analyzer project manager has the responsibility to include the safety and salvage requirements in the narratives and drawings to ensure the corresponding safety and economy.
Nothing has been said about the documentation medium. The presumption is that all documents are held in electronic databases in appropriate formats such as word processing, spreadsheet, CAD or PDF files, with paper copy issued as necessary for meetings, signatures and stamps, field use during construction and maintenance, and so on. Maintenance generally wants paper copies for files, but even this is changing as analyzer technicians increasingly have access to PCs and other wireless tools.
Theoretically, each of these documents could be kept electronically and used in a paperless work environment throughout the life of the asset, provided each user has electronic access, and document security is such that permanent revisions to the respective documents is tightly controlled, but with classes of individual users having change privileges so far as needed to perform their jobs. For example, analyzer technicians could have their own markup copy with one or more “electronic layers” to graphically record and illustrate maintenance activities without affecting the current engineering revision.
Additionally, maintenance documentation can be layered starting with photos of the analyzer system installation and increasing in detail with close-ups of specific devices, (e.g., analyzer PC boards, photometric analyzer sources and detectors, check valves, pressure gauges, and chromatograph columns) with mouse-click links to the manufacturer’s cut sheets and service instructions.
About the Author |
Gary D. Nichols, PE, is principal control systems engineer with Jacobs Engineering Group and can be reached at [email protected].
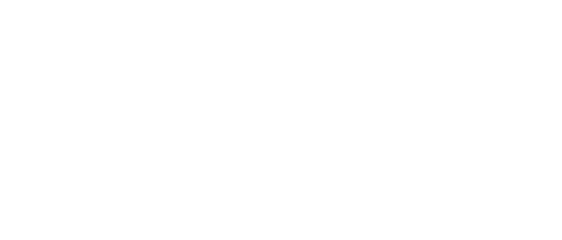
Leaders relevant to this article: