By Dave Harrold, co-founder of the AFAB Group
If the purpose of regulatory control is to maintain the mass and heat balances of a process, then the purpose of advanced process control (APC) is to manipulate the mass and heat balances to achieve optimum performance. As far back as 1970, APC experts and analysts have repeatedly claimed that the benefits of implementing APC were a 2% to 6% increase in production. A recent APC provider company’s press release claimed that the use of APC could enable capacity-restrained plants to increase production by 2% to 3%.
In a typical hydrocarbon processing plant, such an improvement would increase bottom line hundreds of thousands of dollars per year or more. The folks at AspenTech say, depending on the processing unit, the benefit numbers might be much greater. (See Table 1)
TABLE 1: Estimated Benefits using Dynamic Matrix Control in Hydrocarbon Processing
Estimated Refinery Unit Benefits | Benefit in $s Per Year |
Crude Unit 150,000 BPSD | $2,250,000 to $4,500,00 |
FCCU 70,000 BPSD | $4,200,000 to $10,500,000 |
Cat Reformer 50,000 BPSD | $1,500,000 to $4,500,000 |
With so much upside potential for improving a business’ bottom line, one would think the phones of APC provider companies would be ringing off the hook, but they aren’t—although a recently released market study from Frost & Sullivan predicts that by 2012, APC sales will be nearly double 2005 sales of $600 million. While that prediction is encouraging, when adjusted for inflation, the forecasted growth hardly reflects the much-touted APC upside potential. Something seems to be missing. What is it about APC technology that is taking businesses so long to embrace it?
A Bit about APC
The need for APC likely began shortly after John Ziegler and Nathaniel Nichols published their breakthrough paper on loop tuning in 1942. Once the PID (proportional–integral–derivative) control loop could predictably be brought under control or tuned, process control technicians and engineers rapidly accelerated the use of closed-loop control. However, what immediately became apparent to early adopters was that single-variable, closed-loop PID wasn’t always capable of getting the control job done. Users found that minimizing the interactions of other controlled and uncontrolled variables required the addition of controller modifiers (e.g., lead, lag, bias, gain, feed-forward, cascade, etc.).
By the 1950s, the development and availability of control modifiers had advanced so that entire unit control strategies for boilers, ammonia processes and distillation columns were being successfully developed and implemented.
While working for Shell, Charlie Cutler and his colleagues developed the forerunner of today’s model-predictive control (MPC) techniques. In 1979, he presented his landmark paper, “Dynamic Matrix Control—a Computer Control Algorithm,” which remains one of the most important advances in modern APC.
Cutler’s success kicked off a flurry of additional APC initiatives, including Edgar Bristol’s work on multivariable adaptive feed-forward and Bob Otto’s and Kelvin Erickson’s work on multivariate control.
People tend to think of APC as a complex control algorithm, when sometimes it’s simply soving old problems by looking at them through new glasses. In a 1986 article, “Analysis of Valve-Position Control for Dual-Input Processes,” authors Chen Ching Yu and William Luyben introduced a completely new approach to tuning the integral-only function of a controller in order to achieve a valve response fast enough to reject large process upsets.
Terry Blevins of Emerson Process Management says, “People tend to confuse valve position control with valve positioners or digital valve controllers. The tuning of the integral-only control function for valve position control is much more critical than most people realize. The technique described by Yu and Luyben helps eliminate the limit cycle at the split range point caused by the increase in nonlinearities and the decrease in resolution imposed by backlash, backfilled pipes and dip tubes, rangeability limits and friction, particularly associated with beginning a flow from zero. This technique also eliminates the conceptual and tuning problems with valve position control.
The cost-effectiveness of computing power and memory kicked off another round of R&D spending by major control companies intent on developing commercially feasible APC applications, including controller-based fuzzy logic and neural networks, self-tuning, and multivariate adaptive feed-forward.
By the late 1990s, users had a wide variety of sophisticated APC applications available from which to choose. However, despite an increasing number of conference presentations and seminars heralding all sorts of benefits to be derived from using APC, the market remained relatively stagnant.
All About the Benjamins
Many APC implementations have been very successful, at least in the eyes of the engineers that installed them and the operations folk who work with them.
One anonymous poster to the APC-Network.com web site says a multivariable controller has been operating with a 98% uptime since Dec. 1999, had a seven-month ROI, and produced $730,000 of annual benefit to the company—$5.1 million of savings in the past seven years.
Unfortunately sharing that much detailed information about an APC installation is rare. Most of the time, APC benefits are stated in non-quantified terms, such as fewer operator interventions, reduced flaring, optimized production, better control, etc.
Most companies say they don’t share their APC successes because they are fearful their competitors will gain valuable insight into their business. A more likely reason is that the ROI and benefit claims of the APC application haven’t been “blessed” by the companies’ finance departments.
Finance determines how the company accounts for everything, prepares the quarterly and annual reports, and talks to investors and Wall Street analysts. Finance is involved intimately in budget item approval. When it comes time to close, modernize or expand production facilities, Finance owns one of the major decision-making chairs, and APC seems to be invisible to Finance.
Peter Martin, vice president of performance management at Invensys, and Tom Fiske, senior automation analyst at ARC Advisory Group independently concur that a major factor keeping APC from reaching its full potential is that process engineers haven’t made friends with the folks in finance.
Martin and Fiske agree that the process instrumentation and control (I&C) industry has committed a near-fatal error. Instead of working with finance to develop ways and means of developing real-time accounting, it has knowingly, and with some regularity, bypassed company finance groups and created its own benefit accounting methods. The result is all sorts of unsubstantiated ROI numbers.
Correcting Past Mistakes
Some APC supplier companies claim that unit APC justification studies are no longer necessary because APC is accepted as a best practice. A 2002 worldwide study of APC applications, “A Survey of Industrial Model-Predictive Control Technology,” by S. Joe Qin and Thomas A Badgewell verified that to be true for the refining industry. The study reports that of the roughly 2,200 APC installations surveyed, 82% were implemented in the refining and petrochemical industry.
Does that suggest that other process industries do not have similar optimization opportunities? Hardly. SABIC-Europe, a major polyolefin producer, has a great track record using the Aspen Apollo APC application and isn’t afraid to say so.
In 2006, its German site reported an ROI of €12 million per year from a €4-million investment. One-third of that was directly related to the APC system, while the other two-thirds came from introducing better work practices.
Joep Bazelmans, plant automation engineer at SABIC-Europe’s Competence Center says, “Looking back, you can see that an ethylene plant was always focused on maximizing production of ethylene and not at the same time maximizing output of propylene. With APC we found we could maximize both at the same time.”
SABIC-Europe’s APC implementation yielded:
- a 10% total throughput increase
- a 3% ethylene production increase
- a 15% propylene production increase.
High-Maintenance?
One persistent and outdated APC perception is that APC is costly to purchase, implement and keep running. Though that may have been true in the past, today’s APC implementations are much easier and far more robust than their predecessors, and usually offer at least 98% uptime. SABIC-Europe reports nearly 100% APC uptime.
The way to change business executives’ perception from “APC is an engineer’s toy” to “APC represents a worthwhile business-improvement tool” is to become friends with finance.
A Matter of Timing
Despite efforts that began in the mid-1990 to banish batch accounting principles, a great many companies continue to develop annual reports based on quarterly reports based on weekly reports based on daily reports based on shift reports.
Traditionally businesses production reporting frequency has followed this model:
- Regulatory control and operations = seconds;
- APC and supervisor = minutes;
- Real-time optimization = hours;
- Scheduling = weeks;
- Planning = months.
Plug this timing into the buy vs. make vs. trade decisions executives face, and it is clear that traditional reporting systems don’t provide the information business leaders need in the time frame in which they need it.
For example, not too many years ago companies signed six- and twelve-month contracts for their energy and raw material needs. Electrical cogeneration wasn’t even a thought, and the commodity “spot market” was limited to things like fruits, vegetables and hog bellies. Today energy and raw material contracts are bought and sold multiple times daily. Some plants have invested heavily in cogeneration, so they not only can meet their own electricity needs, but also have the option of selling excess electricity back to the grid. Crude-oil refineries are also brokers of their product, and similar business arrangements are possible in other processing industries.
If you were a CEO or vice president in one of these companies, how comfortable would you be making 21st century business decisions using 20th century reporting methods? Probably not comfortable at all.
Why? Because as an instrumentation and control (I&C) professional, you know that getting real-time production information in a meaningful format isn’t that difficult.
Guess what? Key executives don’t know what you know. They are getting their business decision information through finance, and finance doesn’t have real-time production data. Even if finance does have the data, the staff may not understand how to turn it into useful real-time production information. There’s never been a better time for I&C professionals to reveal their significance to the company.
Helping Your Friends
And what does all this talk of energy and raw materials have to do with APC? If the purpose the purpose of advanced process control is to manipulate the mass and heat balances of a process to achieve optimum performance, then the connection becomes clear. When production processes perform at optimum levels more than 98% of the time, they tend to produce far less waste while efficiently converting energy into finished product.
The way you help your friends in finance is to assist them to banish batch in favor of near-real-time reporting by working together to identify what near-real-time data they have and/or need and how that data relates to production costs.
If the data isn’t readily available, work with your friends in Finance to find ways to get it. The solution might be as simple as configuring an OPC server to share the data point. Remember, if the finance folks see tangible benefits for the business, they will find funding for the project.
Once all the data is in place, and finance agrees it’s providing valuable near real-time measures that senior executives readily can use, begin educating your friends about ways to reduce those messy and unexpected production variables using an APC application.
Sneaky? Not at all. It’s really what we I&C types should have been doing all along—working with the finance folks to establish quantified, reportable baseline measurements upon which future production improvements will be based.
Earlier the question was, what is it about embracing APC technology that is taking so long? The truth is it has nothing to do with the APC technology and everything to do with understanding and accepting that if Finance isn’t onboard with how results are measured and reported, you can forget trying to convince anyone else.
About the Author |
Dave Harrold is co-founder of the AFAB Group. He can be reached by e-mail at [email protected].
Latest from Home
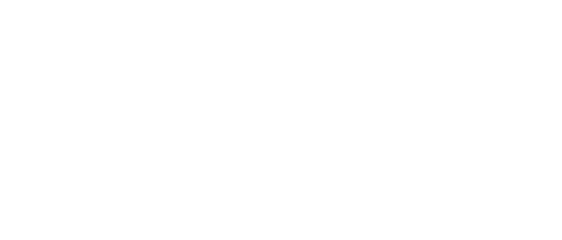
Leaders relevant to this article: