Sometimes a network does more than just communicate. Sometimes a network is so far-reaching and profound that it improves entire applications and their organization’s performance. Such is the case with Invensys Process Systems (IPS) and Foxboro Automation’s Mesh Network and its many related components. In their “Move and Groove to the Mesh—Upgrade Planning and Best Practices” presentation July 16 at the 2007 User Group Conference in Boston, Foxboro’s experts and several end users showed how the Mesh Network functions, how to plan for it, and how it was added to two major applications.
The users included Jack Easley, primary I/A administrator and control system cyber security team member at TXU Power’s Martin Lake Steam Electric Station, Stan Hobbs, Foxboro’s technical support specialist, Orren Siders, I&C team leader at Southern Co. and Georgia Power’s Plant Branch facility. Foxboro’s presenters included Stan Hobbs, technical support specialist, Gayle Hicks, advantage and lifecycle management director for all product lines and brands, and Jack Golding, regional customer service manager.
Hicks first traced Invensys implementation of its “lifecycle discipline” across its brands, and described how its traditional “continuously current” process strategy and services helps users define deliverables for their own management, and achieve consistency during a typical lifecycle. To further help users plan, Foxboro defines five lifecycle phases, including preferred/latest products, available products, mature products (within three-, five- and 10-year categories), a lifetime phase that requires a one-year notice when parts will no longer be available, and an obsolete phase when the device can no longer be fixed. Hicks reports that Foxboro now has dedicated lifecycle policies for its Foxboro A-Squared and I/A Series, InFusion, Spec 200, Spectrum and Tricon lines, and that policies are under construction for its Foxboro M&I, Foxboro SCADA, and other Triconex products.
“Lifecycle planning enables users to go to their finance people, and say this is what we’re going to need in the next three years,” says Hicks. “This helps them make sure there won’t be any surprises, lets them plan their processes, and reduce maintenance by keeping current.”
Easley says TXU put many of Foxboro’s methods into practice when it upgraded Martin Lake’s Unit 2 from a 36-station, legacy Nodebus system to a new Mesh Network solution with DCP270s and P92s. He adds the old system was slow, had alarm problems, was prone to data loss, and, at 75-90% load capacity, was soon going to have parts problems. The upgrade took four of the plant’s I&C technicians and one Foxboro representative about two weeks to install and three weeks to check out.
“Ninety percent of our migration to Mesh is done. We tied everything together with Mesh switches, and ended up with 15 stations that are faster, have lots of room for growth, and operate at only 15% load capacity,” says Easley. “And our Mesh-based data now goes through a multi-zone firewall, which works with an isolation station, so we have two layers of security.”
Likewise, when Southern Co. and Georgia Power decided to upgrade their Plant Branch facility, they also chose to use Mesh Network, I/A Series controls, and two ATS stations. The plant’s four coal-fired units needed to go from a dual-redundant, 10 Mbps or slower system to a 100-Mbps/1-Gbps system with sub-second fault response and a self-healing network. “The requirements for plant-wide information here required a bigger data pipe and bigger backbone,” says Hobbs. “It also needed redundancy at every level.”
Siders added that Foxboro helped him and his I&C colleagues convince management to invest in a phased upgrade plan, and that now he’s adding LAN modules to link Plant Branch’s Units 1 and 2, and will soon replace its CP40s units with ZCP270 devices. “This plan helped me go to management, and show why we needed the money to replace CP units to people that didn’t know what a CP unit is,” added Siders. “It was very useful to have Foxboro help us develop this phased approach.”
Latest from Safety Instrumented Systems
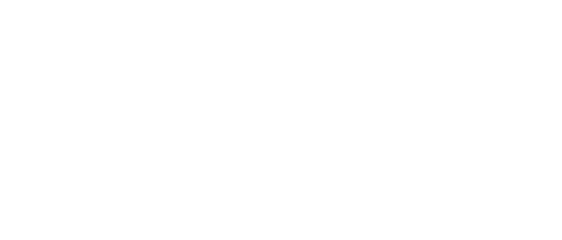
Leaders relevant to this article: