By Andrew Bond, Industrial Automation Insider
Europe’s Best-Kept Automation Software Secret Marks 20th Birthday with Windows Vista Certification
Wonderware, it seems, isn’t the only SCADA software vendor celebrating its 20th anniversary in 2007, and while its birthday celebrations were no doubt extensive and expensive, they almost certainly didn’t feature a 250-year-old former archbishop’s palace as the venue. However, Schloss Leopoldskron on the outskirts of Salzburg, Austria and the location for some of the key scenes in the film of “The Sound of Music,” was where Copa-Data last month held its own 20th birthday party. And before you say “Copa-Who?” be aware that the guest list included top brass from key customers such as BMW, Audi and Ford of Germany. Nor does Microsoft have to ask who Copa-Data is—the latest version of Copa-Data’s zenOn SCADA package is the first offering of its kind from any vendor to achieve the accolade of being “Certified for Windows Vista.”
All of which is heady stuff for a company that is not only entirely self-financed, but now once again entirely owned by its founders, brothers Thomas and Alexander Punzenberger, after they bought back all of the externally owned shares last year. With both brothers still well on the right side of 50, there’s no sign of that independence being surrendered. Indeed it’s a key plank of the company’s strategy, not least because it allows it to pursue its own—or perhaps more exactly Thomas Punzenberger’s own—ideas about what a SCADA system should look like. But it’s also increasingly seen as an advantage, even by its bluest of blue chip clients.
“Many of our prospective customers are looking for a hardware independent solution,” explains brand manager Markus Stangl. “Although the automation market is growing at between 5% and 10% a year, it’s also consolidating so that there are fewer players. As a result users seem to have less control over their core processes and are experiencing higher total cost of ownership.”
Meeting user expectations means focusing primarily on ease of use and ease of integration. zenOn, it is claimed, can be implemented entirely without coding and purely by parameter setting and boasts what the company believes is the widest range of its own drivers for third party devices.
Why Not Rely Simply on OPC?
Because another key plank of the approach is quality, says, Stangl, and “You can’t control the quality of the other vendor’s OPC implementation.”
The same, he argues, goes for proprietary drivers from third parties, so Copa-Data has a policy of always developing its own. Expensive maybe, but it’s seen as a key differentiator not just from hardware vendors’ SCADA offerings, but from those of the other independent vendors, and the payback comes in ease of integration and implementation and, hence, in customer satisfaction. The same goes for what he describes as its “one click networking” and “one-click FDA compliance” and its automated engineering documentation. Add the capabilities of its Straton soft PLC, developed by its French joint venture Copalp and currently being used by Audi for logic control in a plant in Hungary, and you have what Stangl calls a “true open DCS” or, more colorfully, “Esperanto for automation.”
Mits’ MES Module Does Away with MES
Mitsubishi has made something of a habit of announcing new products under old names, for example, maintaining the MX branding when it switched from Intellution to Citect for its SCADA offering back in 2003. So when the hacks were summoned to Mits’ UK headquarters at Hatfield, some 30 miles north of London, last month, it wasn’t entirely surprising that part of the justification for the trip—made somewhat more complicated by PR consultant Bob Dobson’s failure to identify in his instructions the correct junction at which to leave the motorway—was the launch of a new MES software product under the MX brand which comes neither from Intellution nor from Citect, but from Gemba Solutions, the Leicester, U.K.-based MES developer which was bought out by its management from the MCS Group.
More of that later. First, however, what looks a lot like a new variation on the Mits approach—a new name for an old product. In fairness, the iQ platform, which carries the tag line “Intelligent Automation,” does involve one new module, and Jeremy Shinton, product manager for modular PLCs and software, assured us that there are “a whole lot of additional things to come,” but for now the fact remains that we’re talking about one new module that fits into the backplane of the long-established Q-series of PLCs.
That said, however, the new MES module is certainly significant and could have some of the other vendors reassessing their own approaches. Already in use in Mits’ own plants in Japan and in the GEMA (Global Engine Manufacturing Alliance) facility which builds 800,000 engines a year for Chrysler, Mitsubishi Motors and Hyundai, it represents, claims commercial communications manager Jeff Whiting, a “new generation of integration.”
Eliminating PCs
What it actually does is to connect directly to industry standard databases, such as SQL Server and Oracle, flattening the architecture and eliminating the need for PCs to link the plant floor to the ERP and MES layers. A key objective in the development was to eliminate any requirement for programming or scripting so that setup would be entirely a matter of configuration, selecting which data is to be logged and at what intervals or on what trigger. The module doesn’t just have access to the Q-series backplane in which it is installed, but can get data from anywhere on the plant network and talk to up to 32 concurrent databases, automatically generating the relevant SQL code. In addition, it provides local backup in the event of a communication failure, buffering data locally on standard flash cards until communication can be restored. It thus has a significant role to play in regulated traceability applications.
Shinton argues that the module significantly reduces capital and engineering costs and will encourage a whole new range of manufacturers to invest in MES.
“It brings the data together throughout the business,” he explains. “Previously the actual cost of putting this layer in has prevented users from doing it.”
He argues that in its simplest form the PC and communications necessary to implement the equivalent functionality would cost between £6000 and £10,000 (approximately $12,000 to $20,000), whereas the new solution can be implemented in an existing system for under £2,000 ($4,000).
Cockrell Named ISA President-Elect
Meeting last month in the 116 °F heat of Phoenix, the ISA Nominating Committee named Professor Gerald Cockrell as president–elect. Professor Cockrell holds a chair in electronics and computer technology at Indiana State University and declares a special interest in microcomputer-based process control and system integration, data communications in the process industries, fieldbus and DeviceNet and industrial training. Word on the Phoenix street is that his nomination was an unexpected rebuff to the ISA establishment.
We also hear of a proposal to make another change in what those three letters stand for: not the Instrument Society of America; not the Instrumentation, Systems and Automation Society; but the International Society of Automation. Not necessarily a case of rearranging the deck chairs on the Titanic—membership is reportedly up in the last few months, boosted, one suspects, by the decision to make ISA standards available free to members. Amazing what effect giving members something for their subscriptions can have.
Safety Group Shares Expertise on DVD
The Safety User Group, the body established in 2000 to focus on instrumented safety for the process industries, has produced a two-disc DVD box set which discusses current best practice for safety and takes an in-depth look at some of the common mistakes and misconceptions surrounding the IEC 61508 and 61511 functional safety standards. Included are contributions from 11 leading experts, including Emerson’s Thomas Steiner, Invensys’ Pasquale Fanelli, IEC 61508/1-2 Working Group chairman Ron Bell and international lawyer Christian Huglo.
“Dealing with safety every day, I can see that an increase in awareness and understanding throughout the safety arena is essential,” commented Safety Users Group president Didier Turcinovic “This doesn’t just mean the safety specialists, but those having management responsibilities, project engineers, integrators, plant production and maintenance teams through to the legal department—safety matters to everyone.”
Top Down
Reflecting this top-down approach, the DVDs’ content extends from the technical detail of Safety Instrumented Systems (SIS) and their relevance to IEC 61508/61511 through to how demonstrating best practice in safety can support companies in a court of law.
“There is no excuse for ignorance concerning safety,” said Ron Bell. “As a consultant I help companies improve their procedures—but this means nothing if the company’s management and those staff having specific responsibilities for functional safety, are not competent to carry out their responsibilities. This DVD provides a practical resource for staff training, and for improving the understanding of functional safety within an organization.”
The box set costs Euro 90 or $115, but you can get a preview at www.safetyusersgroup.com.
Third parties join process industry wireless party
If the process automation vendors thought they were free to argue amongst themselves about how to implement wireless in the field, then they were rudely disillusioned by last month’s announcement from Cisco of its own solutions, aimed fairly and squarely at the upstream oil-and-gas sector.
Dubbed First Mile Wireless, it is specifically designed to operate in harsh physical environments where the problems of limited infrastructure and scarce IT resources are compounded by the presence of exposed, densely packed metal structures, networking control devices, maintenance sensors, mobile service workers, physical security assets, service vehicles and location service tags, as well as integrating mobility services such as wireless voice over IP, video and guest access.
Blast-Proof Cases
The standard solution comprises Cisco 1500 Series wireless mesh access points housed in specialized blast-proof cases with Cisco WCS for wireless network management supported by Cisco Secure Services for network security. Onward transmission is provided by a variety of backhaul technologies including Wi-Fi bridging, WiMAX and satellite connectivity and operation technologies and applications. Cisco plans to bring its solutions to market in conjunction with its Wireless LAN Specialized Partners, offering a broad portfolio of end-to-end services based on proven methodologies for planning, design, implementation, operation and optimization.
“Mobility is about empowering businesses to make better, faster and more informed business decisions,” said Cisco director of mobility solutions Ben Gibson. “The Cisco First Mile Solution helps to enable the next wave of business performance and breakthroughs for one of the most challenging business environments, the oil and gas industry.”
We’re grateful to Walt Boyes of Control for pointing out that Rockwell has recently announced a partnership agreement with Cisco which raises the intriguing possibility of Rockwell’s coming to market with a fully fledged wireless solution, giving real credibility to its recently voiced aspirations in the process market.
Meanwhile Apprion, the Californian wireless specialist with whom Invensys Process Systems has partnered in order to develop its Secure Wireless Architecture, has announced a new generation of its ION System, which it describes as “the first truly open, scalable and extensible foundation for managing multi-vendor wireless devices and applications.” The new release claims to deliver improved security, management and integration capabilities for the process manufacturing environment.
Fragmented
Apprion argues that, although the basic building blocks for a wireless plant already exist, the systems remain fragmented, proprietary and difficult to integrate, making it difficult to realize the technology’s full potential in an industrial setting. By contrast, with the ION System, it claims, it is possible cost-effectively to design, deploy and manage wireless-enabled applications within a unified system that is secure, reliable and extendable as technologies evolve and new applications become available.
The system comprises the IONosphere on-site controller which automatically brings devices, systems and applications under management and the IONizer which, the company claims is the process industry’s first industrial wireless networking appliance and integrates such disparate wireless-enabled applications as VoIP and condition monitoring. Specific enhancements in the new release address security issues, making it easy for administrators to bring legitimate devices and systems under unified management. In addition, ION delivers what is claimed to be the first interface to give users perspective from both a geospatial and relational framework, making photographs, maps or CAD drawings available via a web-based portal and allowing users to record and use information in the form that is most appropriate for their operational responsibilities.
“Apprion changes the way process industries look at wireless. Apprion is the only company that has devised a way to make implementing wireless industrial applications easier and more cost-effective,” claimed Apprion president and CEO Stephen Lambright.
Latest from Home
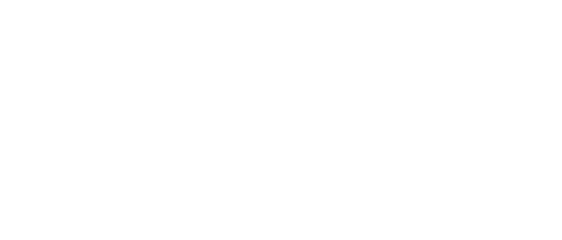
Leaders relevant to this article: