By Nancy Bartels, Managing Editor
If you still think outsourcing is about sending large chunks of your operations to low-cost-labor countries, it’s time to get your head out of the 1990s. That still happens, of course, but companies have learned that cheap labor isn’t the complete solution to their problems. They also need to optimize operations, and they need skilled engineers and technicians to do that, engineers and technicians that are retiring in droves over the next ten years.
“It’s a perfect storm,” says Larry O’Brien, research director for process automation at ARC Advisory Group. “Labor is part of it, but the focus, particularly in North America and Europe, is on getting maximum return on assets. Manufacturers need to get the most from what they have. They need to improve plant performance and productivity, and they don’t have the resources in-house to do that.”
Ironically, this second wave of outsourcing demand is in part a result of the first wave. In the last two decades, companies have downsized, right-sized and reengineered their work forces, all with an eye to cutting labor costs, but apparently ignoring the looming retirement avalanche. In its May 2007 report, “Services Market Boom for Automation Suppliers,” ARC tells of a “major refining company” losing 2,500 years of experience last year when 100 operators, with an average of 25 years’ experience each, retired at one of its sites and of an unnamed “major chemical company” that did a demographic analysis and found that one of its largest plants would lose 75% of its operating staff to retirement by the end of the decade.
At the same time, it’s getting harder and harder to find qualified replacement engineers. “It’s not a very sexy profession any more,” says O’Brien.
In another irony, many of the engineers shed by manufacturers over the past decades have found homes with the automation vendors. They have “ended up hiring the engineers who don’t see the opportunities in the industry anymore,” says O’Brien. “Some of the best people in oil and gas, refining and pharma are being hired by suppliers. We also see a large pool of older people getting hired. The vendors are hiring the gray-haired gurus. These guys are popping up again on the other side of the fence.”
The result is more and more process manufacturers are looking to others to provide expertise they one time had in-house, and the first place many of them are looking is to their automation providers, who are more than happy to help. Vendors are building some of the scarce skill sets into their products, providing a kind of “stealth” outsourcing that lets manufacturers replace lost process knowledge with software. Then they are packaging this new capability along with integration and training services. (See sidebar, “An Alarming Situation.”)
For example, Siemens’ Si-BASIC set of engineering tools and services gives customers the choice of picking all or some of five key process control project engineering tasks—I/O hardware configuration, development of the control module, interlocks, process graphics and simulation—to offload on to Siemens or one of its partners, who then use a packaged methodology and toolset to install them. Other major automation players may have entire engineering teams (some of which are located offshore) to handle such jobs. Some are specializing in certain functions ripe for outsourcing. ABB offers a comprehensive maintenance package, and Invensys Process Systems has just announced a whole package of services around equipping plants with wireless technology.
“What we’re trying to do—because our customers are asking for it—is leverage our industry and automation expertise to complement the plant,” says Tim Olsen, a process consultant with Emerson Process Management. “We’re not taking over their jobs so much as providing tools and services to complement their plants to run them better. The biggest driver is the retirement of the baby boomers. What’s a plant supposed to do? The experience isn’t necessarily on the street.”
Kevin McDevitt, program management officer in the Process Automation Systems group at Siemens, says, “’Outsourcing’ is a bad term here. We see it as value-add. The reality is that the marketplace is putting pressure on everyone, and we’re trying to respond.”
It’s not just the labor shortage that’s driving the push to outsourcing. The variable nature of the demand for many engineering tasks makes them attractive targets. “The biggest reason manufacturers are outsourcing parts of their operations is that they like to have variable costs,” says Bill Pollock, president of systems integrator, Optimation. “Capital projects come in cycles and waves. Even with things like maintenance, you may only need your maintenance people some of the time, and you don’t want to keep them on staff all the time. Companies are looking at costing a different way. They want to hire and buy just what they need at the moment.”
This was the rationale behind Kodak’s turning over its entire engineering operation, including the staff, to Optimation. “When we took things over from Kodak, it was just seasonal. There were blocks of the year when they needed everybody and had to hire more, and then there were times when it was slow, and they would have to pay to keep good people. Now we can charge Kodak fewer dollars per hour for each hour the engineers work, and Kodak has to pay only for the hours worked. It increases resources utilization and decreases costs. If you have outsourcing, you’re better off.”
Siemens marketing manager Todd Stauffer sees the same pattern. “What you see is customers outsourcing on-going life cycle maintenance because they can’t afford the people. Sometimes this is a part-time task. It’s 10 to 15 years between upgrades. What do you do with these people the rest of the time, especially if you’re a smaller plant?”
Outsourcing 2.0
This second-generation outsourcing isn’t as straightforward—if it ever was as straightforward as it sounded—as moving a factory or call center overseas. For one thing, some functions being outsourced have always been outsourced. Hiring a systems integrator to help install a new process control system or working with an engineering and construction firm to bring a new plant online is nothing new.
What’s different now is that as the supply of qualified engineers and operators gets tighter and the push to optimize production and keep costs down grows evermore relentless, companies are tempted to outsource functions that used to be considered “core competencies.”
Here’s where things can get dicey.
Autmation vendors services market grows
The total services market for served by automation suppliers will grow at over 12% annually through 2011.
Courtesy ARC Advisory Group.
On the one hand, there’s the vision of the “virtual company,” where the famous name owns nothing but the brand and outsources everything. “Some industries lend themselves well to this, electronics, for example. Others not so much,” says Paul Galeski, CEO and founder of systems integrator, Maverick Technologies. “This is a big and risky decision for a manufacturer.”
More likely, a manufacturer will keep core competencies in house. “If you’re talking about a key competency, you shouldn’t outsource it. If it isn’t a core competency, you should,” is Galeski’s rule of thumb.
Here’s where you need a tough self-analysis and an “honest assessment” of your business, says Galeski. “What are your profit drivers, the real keys to your business? What are the areas where you can’t or don’t need to be the best?”
He recommends the “income tax test”: “The analogy I use is the reason people don’t do their own income tax. You don’t have the time to focus on it, and you only do it once a year, so you hire a specialist. A systems integrator does some of these things every day all day. They’ll have the expertise and the core competency to do them well consistently.”
But how does the analogy translate into process manufacturing? Is maintenance a key competency? Maybe, but lots of companies are looking at outsourcing large chunks of that function. (See sidebar, “Remote Maintenance.”) What about alarm management and optimization? Instrumentation or loop optimization? How close to a “core competency” are those functions?
Some would say, “too close.”
“What should your core competency be if not engineering and maintenance?” asks Julie Fraser, principal at Industry Directions, a consultancy based in Newburyport, Mass. “Just because you’re not good at it today doesn’t mean you shouldn’t develop it into a core competency. Look at the Texas City Refinery. There are severe consequences to not having maintenance and engineering competency.”
Fraser also warns of the possibility of losing good skills. “You need to ask, what is the value our company adds. Why do people pay us for anything? You need to answer this as well as what you can outsource in the short term.”
Emerson’s Olsen says, “Plant management is working through what is core for its business. “It needs to be able to say, ‘This is why we’re running this plant this way. It’s not just arbitrary.’”
The problem is, the lines between core and non-core competencies aren’t as clear as anyone would like. “Areas where manufacturers want to do outsourcing, such as automation, have become a lot more complex,” says Olsen. “It’s different now. It’s digital. There’s data management. More people are running ERP systems on top of the control system. In some ways it’s almost an IT role. But you still need the core to run the plant.”
A vice president at a global oil company explains it this way: “Outsourcing doesn’t relieve you of the responsibility of managing your business properly. You have to have people there to make sure the outsourcers are doing the work you need cost-effectively and adequately. If you try to get by with just managers and accountants, but no technical people, you’re going to get into trouble with outsourcing.”
Letting all your engineering and operations talent go also leaves manufacturers vulnerable to shifts in the market. Since part of the goal of outsourcing is to provide flexibility for economic cycles, what happens when the next upturn takes place, and that talent is needed in-house again?
“Building up a new skill pool at that point is very difficult,” says our oil company exec. “You’re going to be out in the marketplace shopping for skills, and it’s hard to know what you’re buying if you don’t understand it.”
Not a Quick Fix
Outsourcing has other challenges besides deciding what to outsource. “One of the biggest things is that while on the one hand, you’re reducing your risk, you’re increasing it at the same time,” says Fraser. “As things change, your executives have very little leverage over these people. If you find a process that would work better and you want to change it, you need to build that capability into the contract. You need to be flexible enough to allow continued improvement, but specific enough to have grounds for severing the relationship if you have to. Unless you’re careful about the way the contract is structured, it’s not as easy to fire a company as an employee.”
Users look to automation vendors
for services
More end users are buying services from their automation suppliers now, and the trend is expected to grow.
Courtesy ARC Advisory Group.
Outsourcing also changes a company’s business processes, and it has to be ready to manage that, she adds. “All of a sudden, you’ve got a separate company involved in the process. Even if you’ve got good policies and procedures, it’s a different thing to enforce those on a contractor. And sometimes your processes will make them less efficient. They have their own best practices, and you may want to leverage them rather than impose your own. That changes the way you manage.”
Sorting out knotty issues of change management and the natural concerns of your own work force about having outside contractors on-site—Are these guys doing to take my job? How come they have different work rules for doing the same job?—there’s still the tricky question of intellectual property (IP).
Reputable services providers won’t steal your proprietary information, but there may be some subtle leakage. “We’re careful not to take any proprietary material,” says Optimation’s Pollock. “We don’t hold any patents. But there’s expertise that’s separated from IP. We can apply that in some areas.”
Maverick’s Galeski says, “There is a risk of commoditizing IP. This is why you have strong legal language to protect companies.”
Fraser adds, “There’s a real danger there. This is where the contracts come in. It will be hard for people working inside your plant not to take some ideas away. You’re opening your kimono entirely. It requires a lot of trust.”
The Long View
Most manufacturers still take the view that outsourcing is a better short- than long-term solution. Our oil company exec says that’s one of the criteria for choosing what to outsource. “I haven’t seen a lot of it in day-to-day stuff. We have some specialized help, such as with control valves, but in general, if it’s something we need long-term, we can do it better internally.”
His company limits outsourcing for the most part to the immediate projects. “New construction has always been heavily outsourced and always will be. We use contract maintenance for turnarounds and special events. We’ll shut down for maintenance and bring in two or three times the staff—for anything that’s not day-to-day run-and-maintain. You need a lot of outside help for that.”
However, many companies can’t afford that long view.
“You do need to ask what the long-term implications of outsourcing are,” says Pollock. “It can get to the alarming stage. You may have all these drawings and stuff that your employees can’t read. The problem is that most companies can only afford to look at the next six months, not ten years down the road. Ultimately that can come back to bite them.”
An Alarming Situation
The Foxboro unit of Invensys Business Systems provided the controls system for the upgrade, but the electric company has depended on Invensys, not to just install the new controls, but to help configure its alarm system and train its operators to maintain it.
“When we bought the package, it had 72,000 alarms,” explains Rees Scott, an operations specialist and control room operator at Salt River. “Only 38,000 of them were configured, and all were configured as Priority 1 alarms. You were just numb. All you wanted to do was shut up the alarms. That’s when we brought in Invensys to help us rationalize the alarm system.”Invensys provided a combination of support and training to help Scott and his coworkers get their alarm system in workable shape. “Invensys has the people and programs to help us get going on the project. It was a big undertaking, and we had to do it in stages. It took us from March to about June,” says Scott. “I refer to it as counting toothpicks. We had to physically look at every alarm, what it meant to the system, how to deal with it and decide what priority it should have. Invensys came in to help us do it and show us how to do it ourselves.”
Whether Invensys remains part of the mix for alarm management over the long haul remains to be seen. “I think it will be a mix of inside and outside,” says Scott. “If we can do things in-house, we’ll do them. But we have a great relationship with Invensys. We’ve quieted the alarm storm. Now we’re going through a relearning curve. We’re learning to pay attention to the alarms. It was crucial that Invensys was involved. I would not have known how to go about doing it. The stuff Invensys taught me has enhanced my ability to be a better operator.”
Remote Maintenance
Maintenance at the Voisey's Bau Nicel Co. is a challenge for a number of reasons. For a start, it's located in a remote region of Labrador, about 300 km north of Goose Bay and 200 km from the nearest infrastructure. Employees are flown in for 14-day, 12-hours shifts. There's no running down to the local supplier for parts.
Voisey’s Bay is a greenfield site opened in September of 2005. “It was important from a business perspective to have a fast ramp-up of the installation, thus we wanted to have a well-established approach to performing maintenance,” explains Joe Holmes, manager of the concentrator facility at the mine. “Beyond the ramp-up, we felt that the steady-state performance would be improved with a good contract arrangement, versus developing an in-house program. We didn’t want to reinvent the wheel with respect to maintenance.”
Therefore, Voisey’s Bay turned its maintenance operations over to ABB, who handles all the maintenance of fixed equipment at the mine and concentrator, including management, planning and execution at the concentrator, diesel power plant, port and ship-loading facilities and various infrastructure installations. Voisey’s Bay handles its materials management internally, but ABB determines what spares need to be in inventory. The job is handled by IABB (Iskueteu ABB), an Innu-Inuit partner of ABB, in keeping with Voisey’s Bay’s agreement with the local indigenous people to foster business development in the area.
Holmes says the outsourcing model is not common in the mining business, but that it is working well for Voisey’s Bay. “We’re pleased with how the team has developed, given that many of the maintenance employees are from a construction background or from other industries. Most of our early difficulties were related to design or installation issues, not maintenance.”
Cutting costs was not the chief motivation behind the project. “The driver was not about cost saving as much as maximizing the business,” says Holmes. “In our business, you can be penny-wise and pound-foolish. Anybody can save you money on maintenance, but sometimes you end up falling off a cliff in six months. Our objective is to maximize production and optimize maintenance. Over time, I’m sure we’re going to optimize the cost as well.”
There were some difficulties, particularly in terms of combining the Voisey’s Bay and ABB labor forces, but they too have worked out over the long haul, says Holmes. “With people working under the same roof, but with different employers, there’s the potential to create some issues. You can do it successfully, but you have to do a lot of preplanning. People think because they’re all working at the same place, they should be treated the same, but they’re covered by different collective bargaining agreements, so it’s not always possible—or even desirable—to treat everyone the same way. That’s one thing we didn’t get quite right. It’s not a disaster, but there are challenges around that issue.”
To find a checklist of outsoursing tips, click here.
Latest from Home
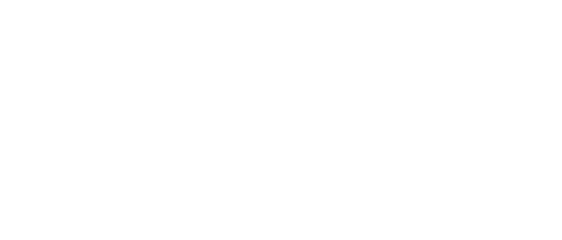
Leaders relevant to this article: