For more on distillation control, go to www.controlglobal.com/distill7.html.
Globally, more than 80 million barrels of crude oil are refined daily. American refineries spend 50 percent to 60 percent of their operating costs on energy, while the chemical industry spends only 30 percent to 40 percent. If the optimization strategies described in this series are implemented, refineries can cut their energy costs by a third, while improving product quality. Ethanol and other bio-fuels are also products of distillation, and the efficiency of these processes can similarly benefit from the described strategies. In the United States six billion gallons of ethanol were produced in 2006 and 35 billion is projected by 2017.
In this last part of this seven-part series, I will integrate the “sub-optimization” strategies described earlier and show how plant-wide optimization is implemented in a refinery. The first step toward plant-wide optimization is to define the operating equations which describe the material, heat and momentum balances of each column.
Sub-Optimization
The theoretical operating equations are normally developed by tray-to-tray runs of calculations on off-line computers. After this is done, a statistically designed set of runs is made, and the information thus obtained is curve-fitted into the form of equations. Once these steady-state theoretical equations are developed, they are refined by online tests. Variables that can not be directly measured, such as the internal reflux flow rate, can be determined on the basis of the heat balance around the top tray. These tests involve operating the column at different loads to determine the actual influence of the Li/F ratio (internal reflux to feed ratio) on separation. By this process, the overall separation efficiency (E ) is adjusted to make (Li/F) equal to the actual Li/F ratio.
The purpose of dynamic compensation is to correct for changes in such a way that the column’s terminal flows respond to the feed flow changes at the proper time, in the correct direction and proportion without under or overshoot. (Figure 1 at www.controlglobal.com/distillfig1.html describes sub-optimized columns). The simplest dynamic element that can be used is a sum of a dead time and a second-order exponential lag. The dynamic constants (t, T1, and T2) in the operating equations for calculating B and L (See Figure 2 at www.controlglobal.com/distillfig2.html) for the bottom and reflux flows have different values. The column’s five degrees of freedom can be utilized to determine the feed tray location (FT), feed enthalpy (∆HF), column pressure (P), heavy key component concentration in the top product (%HKD), and light key component concentration in the bottom product (%LKB). The tray efficiency is also included in the operating equations as a fixed value.
Total Optimization
Total optimization is defined as the strategy to maximize profits. This maximum is obtained by selecting an objective function and manipulating its variables to maximize or minimize the value of that function. Local optimization can mean the optimization of a single column, where the goal is to meet product specifications at minimum energy consumption or at maximum throughput. A unit consisting of several columns is optimized by the effective allocation of both feed stocks and energy among the columns. Plant-wide optimization involves coordinating the control of distillation, furnaces, compressors, etc. to maximize the profitability of the entire operation. In such a hierarchical optimization system, the setpoints of the lower-level control systems are received from the higher-level optimizers.
If product prices are unknown, the optimum column pressure (P) can be found by lowering the operating pressure until the condenser capacity is reached, or until liquid entrainment occurs in the vapor on the trays. When terminal product prices are known, the column is optimized to obtain the specified separation at the least operating cost. For a particular column, optimum separation can 1) be determined independently of feed cost, 2) be obtained by generating the product with the highest unit price at minimum specified purity, 3) be a function of the price difference between products and 4) be a function of the price difference between the heavy key component in the top and bottom and of the price difference between the light key component in the top and in the bottom products.
When product prices are known, economic optimization almost always requires that the column be either operated against a constraint or be operated at a separation [(LKB), (HKD)] at which the gain from an incremental increase in production will equal a corresponding rise in operating cost. Column loading is increased when either the separation is improved or, if the separation is constant, when the feed rate is increased. The operating constraints are a function of the capacities of 1) the condenser, 2) the reboiler and 3) the column.
As feed rate or separation is increased, the capacity limits of one of these three pieces of equipment will be approached. Ambient conditions, steam pressure, feed composition, etc. can influence these capacity limits and therefore the limiting constraint can change as a function of these variables.
Conclusions
While the optimization techniques described in this series of articles can improve refinery productivity and profitability by 25 percent to 33 percent. (The Chinese could benefit even more. Their refineries require 40% more energy and their industry is 3 times as carbon-intensive as those in industrailized nations.) This goal will only be achieved if instead of individual PID loops, integrated unit operation controls are implemented. In multi-variable unit operation control, flows, levels, pressures and temperatures, etc. become only limit constraints, while the controlled and optimized variable is productivity and profitability.
As was explained in this series of articles, each distillation column has its own “personality,” and one can fully optimize it only if that personality is fully understood. Therefore, as we have left behind the age of the single PID loop and entered the age of model based multi-variable controls, the importance of the role of process control engineers did not diminish, but actually increased, because one CANNOT control a process, if one does not understand it. Therefore, suppliers can only furnish “empty boxes” which cannot contain the unique nature of the process because that “personality” is understood only by the process control engineer who operates it.
For more on distillation control, go to www.controlglobal.com/distill7.html.
Béla Lipták is a control consultant, editor of the Instrument Engineer’s Handbook, a former Chief Instrument Engineer of C&R (later John Brown) and former adjunct professor at Yale University. He can be reached at [email protected].
Latest from Safety Instrumented Systems
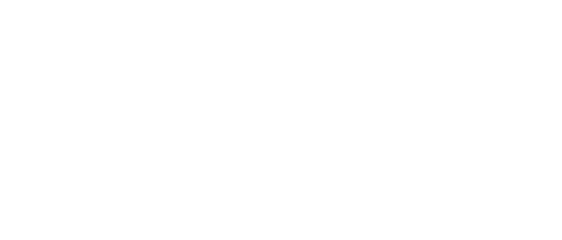
Leaders relevant to this article: