This article was originally printed in the February 2008 issue of our sister magazine Chemical Processing
By Todd Stauffer, Siemens Energy & Automation
Frank Berry of Air Products and Chemicals, Inc. was given a challenging assignment.
The Allentown, Pa.-based firm, which operates in more than 30 countries and is a leading global supplier of industrial gases, asked him to develop a company-wide replacement strategy for the multitude of Human Machine Interfaces (HMI) at its hundreds of plants. Air Products wanted a migration path that would minimize the number of different operating platforms, reduce re-engineering costs, provide a robust HMI system that would enhance operator confidence and maximize HMI commonality plant to plant.
Berry, control systems group leader of the firm’s Global Support Services Group for the Americas and Asia, and his team had much to consider in developing a strategy and putting it into practice. “Air Products has several hundred plants operating on different legacy platforms and HMI systems,” Berry noted. His team had to weigh the costs to migrate to a new HMI system, the lifecycle costs to sustain it, and the expenses to replicate it, all the while keeping in mind that the plants encompassed many different cultures and business demands. Berry didn’t want to change for change’s sake but to gain new capabilities through upgrading that would pay back the investment.
“As a group, the Air Products Global Support Services Group is sustaining a couple of hundred plants,” Berry noted. “We have a fixed number of resources in the group. Everybody has an HMI for sale. To choose one to standardize on is a difficult task.
Each one has benefits and a role in the marketplace. We had a lot of choices. The PCS 7/90 OS appears to be the best cost value and gives us the connectivity, commonality and robustness we were looking for in a HMI migration solution.”
A key test
Air Products’ cryogenic air-separation plant in Orlando, Fla., was chosen as the beta test for the migration. It was an ideal beta site, noted Berry, because it isn’t pipeline based and has liquid backup, like most of the company’s facilities worldwide. The plant could be taken down one day and started up the next and still achieve inventory projections, he added.
The project involved replacing three legacy operator consoles dating back to the early 1980s with Siemens PCS 7/90 OS HMI terminals. The plant kept the existing legacy distributed control system intact, including controller hardware, input/output (I/O) modules and field wiring. This strategy allowed swapping out only the most-difficult-to-sustain components, while maximizing the value of Air Products existing investment in hardware and application software. The PCS 7/90 OS servers connect to the legacy controllers via OPC using standard legacy interface cards.
The migration, which was completed in late 2004, took place in phases without interrupting the operation of the plant. For the first six months of the installation, the three existing legacy consoles and the PCS 7/90 OS system ran in parallel to help the operators become familiar with the new system.
Configured with Simatic PCS 7 OS software, the new HMI consoles have predefined faceplates and graphic symbols for interaction with the function-block-based controller code. Operators retain the consistent look and feel of the legacy system, thus minimizing the impact of change on them.
In addition, the new operator stations provide diagnostic capabilities, display controller alarms and messages, and provide the engineering tools required to update/maintain the configuration in the legacy controllers.
The importance of connectivity
The Orlando air separation plant runs 24 hours a day, seven days a week. Secure remote operator connectivity to the HMI system is critical, noted Berry, because the plant is unmanned during certain periods.
“The connectivity is much better than we had before,” Berry said. “We used to have to dial into the system because the platform was not Windows based. We also had to have the same graphical interface as the antiquated machine on the other end. Now operators and engineers can access the PCS 7 system from their own personal computers and enjoy faster speeds and a higher level of security than before.” The higher security is essential because the system now is accessible via the World Wide Web.
The PCS 7/90 OS HMI system is configured to notify operators of critical events by dialing directly to their ordinary cell phones. When alerted, operators can view the exact same screens remotely on laptop PCs as those that are displayed on the HMI consoles at the plant.
“One of the biggest benefits of moving from the legacy consoles to Windows-based PCs is not having to work with older-generation machines,” Berry explained. “Our previous vendor’s control system software is not compatible with today’s standard desktop computers. Now we benefit from the higher speeds, Windows-based security and report generation. In a pinch we could go to the local store to acquire a replacement PC, rather than searching to find old compatible machines.”
“The software that we had would only run on out-of-date PCs. I can only run them on machines that were slower than 133 MHz. I couldn’t buy those machines anymore.” Air Products had to stockpile obsolete computers to use as spares. Migrating to the new HMI system will ease the maintenance burden by minimizing the number of obsolete systems to be managed.
Because Orlando was a test site and the Siemens PCS 7/90 OS HMI was in the prototype stage, both companies took the time to work together to develop a solution that easily could be replicated with low risk at any of the 100 Air Products plants with this particular legacy control system, added Berry.
“Siemens invested a lot of time to develop the product in collaboration with us,” Berry said. “They did a lot of the engineering. The development exercises produced libraries, faceplates and templates. Now there is an existing library of elements from which we can pull information. Future upgrades will take advantage of this work and enjoy minimal re-engineering.”
A different driver
Halfway through the Orlando HMI upgrade, a similar large air-separation unit in Ghent, Belgium, was beginning a comparable transition from the same legacy HMI operating system to Siemens PCS 7/90 OS HMI. While one of the main drivers for the Orlando plant was remote connectivity, the Ghent plant had another priority — adding production capacity. At the time, a second large air-separation unit that would utilize a full PCS 7 architecture including control and I/O was being built at an adjacent site at Ghent. The goal was to introduce a platform that would run both the old and new units from one control room using a common HMI system. Berry said much of the information gathered at the Orlando beta site was shared with engineers working on the Ghent installation.
“Ghent learned from Orlando and Orlando learned from Ghent,” Berry noted. “We kept the controller hardware, input/output modules and field wiring from the legacy system.
A common terminal bus for HMI connectivity allowed us to share everything else between the legacy system and the new PCS 7 system — including clients and remote access.”
Now that both the Orlando and Ghent installations are operating, Berry said the robustness of the systems has improved. They have been running for months with no HMI related outage. He said diagnostics are clean. Parameters are good.
Broad applicability
“Our beta site at the Orlando plant proved we have established a solid HMI migration path for multiple platforms by standardizing on Siemens PCS 7 HMI technology,” noted Berry.
“One of the unique things about the Siemens architecture for migration is that the core engineering tools and everything above it (the HMI layer) are the same for each different control platform,” he added. “DCS-specific software plug-ins enable this and should make our work force more productive as we won’t have to rely on as many specialists.” Once the database is converted from any platform, the HMI work is the same across platforms from any vendor.
Berry said he now has the commonality in the HMI hardware, software and tool sets he was looking for to perform plant upgrades in the Americas and Asia. The Air Products controls team can work with a variety of HMI tools that they can carry over from one site to another, boosting their productivity and enabling them to more effectively handle the large number of plants.
Today, Air Products’ HMI replacement strategy is well underway. Plants in North America and worldwide are taking advantage of the clear migration path that is minimizing operating platforms and reducing costs, according to Berry. The end result will be increased operator confidence and maximized global HMI commonality, he said.
Todd Stauffer is PCS 7 Product Manager for Siemens Energy & Automation, Spring House, PA. E-mail him at [email protected].
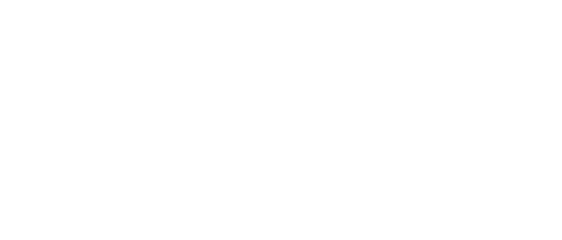
Leaders relevant to this article: