By Paul Miller
Today’s state-of-the-art SCADA is not your granddad’s supervisory control and data acquisition system. It’s not even the one you may have cut your teeth on as a new process engineer back in the day. The monolithic master station running proprietary supervisory applications is long gone. So is communication via inflexible, single-purpose, analog remote terminal units (RTUs) over often-tenuous, low-bandwidth radio or telephone system-based links.
Over time, commercial-grade personal computers (PCs) or servers running more open and interoperable, standards-based HMI and supervisory applications replaced that proprietary master station. Broadband wireless networks or Internet protocol (IP) technology lifted directly from the commercial world have replaced the telephone and old-fashioned radio links. Those dumb, analog RTUs have evolved into today’s much smarter and more functional digital RTUs. And, increasingly, industrial programmable logic controllers (PLCs) or programmable automation controllers (PACs) are taking the place of dedicated RTUs in many SCADA applications. We also now have a new class of intelligent electronic devices (IEDs) that communicate with either the RTUs or directly with the SCADA via standard protocols.
“SCADA used to be a proprietary station that reached out to RTUs with a limited number of points and some minor control algorithms going back and forth,” says Jack Peterson, senior project manager, energy supply and management, at Southern California Edison, Rosemead, Calif. “Today, SCADA is more closely aligned to a DCS or specialized hybrid control system that uses open architecture platforms and today’s high-speed networking technology. These are combined with secure protocols and secure stations following new guidelines, such as those issued by NERC (North American Electric Reliability Corporation) and FERC (Federal Energy Regulatory Commission) in the electric industry. Now SCADAs are sitting on top of PCs or laptops doing everything they used to do – only faster, smarter and more connected.”
This evolution offers many advantages to end users.
“Over the last 25 years, SCADA has evolved by orders of magnitude, pushing more intelligence from the central control room into the field and embracing standard protocols over proprietary protocols,” says Mike Chmilewski, vice president/general manager of the controls business at Invensys Process Systems. “This provides new degrees of freedom for field device selection and for integrating real-time operational data with advanced applications and business systems to enable real-time business control.”
“While SCADA was previously used as a monitoring and control system for RTUs, it now has a broader concept,” says Prasad Pai, Proficy HMI/SCADA iFIX Product Manager at GE Fanuc Intelligent Solutions. “PLCs have taken over much of the control, and SCADA’s scope has expanded into new applications. Because of the flexibility of SCADA, everything that happens in a facility can now be in a single application. What we used to think of as DCS has now become a PLC. It all used to be in one box – both hardware and software. Now a PLC is controlling the plant, and the software, the SCADA, is PC-based. What we used to think of as DCS has shrunk in size, but not in functionality.”
Eduardo Ballina, GEO-SCADA business manager at Wonderware says, “The software originally used for supervisory control has greatly increased in capability over the years. Functionality, such as optimization simulation, and asset management, can now more easily be incorporated into the same solution, bringing these systems from supervisory control into the management space.”
Phil Aponte, HMI/SCADA product marketing manager at Siemens Energy and Automation, says, “SCADA is evolving from a centralized architecture to a more distributed architecture, and the trend is to push production data up the chain to the business. In brownfield facilities, where DCSs, PLCs or other automation platforms from different vendors are already in place, SCADA is also often the path of least resistance for migration purposes.”
As SCADA moved closed, proprietary, application-specific industrial technology to more open and interoperable commercial information technology (IT), cybersecurity became a concern. Post-9-11 visions of terrorists or disgruntled employees hacking into a SCADA system to disrupt the nation’s electricity grid, shut down a critical pipeline, threaten a municipality’s water supply, blow up a tank farm or something spawned today’s thriving cybersecurity industry. With support from the U.S. Department of Defense, Department of Energy, Department of Homeland Security and other governmental agencies, new cybersecurity technology has been developed and is being implemented in industrial facilities. Important new cybersecurity standards are also emerging.
Cybersecurity has developed into a healthy specialty within the already healthy IT consulting industry.
As a result, SCADA technology is being implemented in some new and interesting applications. According to George Quesada, a product manager at ABB, “SCADA has grown by leaps and bounds in the oil and gas industry. This is particularly true in the upstream sector, where drilling activity has been exponential in the last four years, making it a necessity to be able to monitor and control wells, upstream compressor stations, water injection, and well tests.”
Increasingly, elements of SCADA technology are also being used for in-plant process control applications. Since today’s SCADA, HMI, MES and DCS systems all share many of the same open technologies (Microsoft-based HMI, data analysis, and historian applications; Ethernet IP; Web services; etc.) and can be used to address overlapping applications, it’s becoming increasingly difficult to differentiate between the different systems.
This all begs questions such as, “What does a modern SCADA system look like,” “What kind of technology does it use?” and even, “What is a SCADA application?” The answer to all three questions pretty much appears to be, “anything goes.”
For example, the way modern SCADA technology is being applied in today’s municipal and utility operations bears little resemblance to the traditional SCADA with which many old-school automation professionals grew up.
Funny, It Doesn’t Look Like an RTU!
The Evansville Water and Sewer Utility (EWSU) in Evansville, Ind., has been modernizing its automation and information infrastructure in stages over the last two years. The utility currently pumps an average of 32 million gallons of water per day of treated water from the Ohio River to the 150,000 people of Evansville and handles all wastewater treatment, sanitary and combined sewer systems for the city.
InGen Technologies, based in Evansville, is a systems engineering and process control company that has primary responsibility for designing and implementing the upgraded automation and IT infrastructure for EWSU. This includes new process control systems for the three treatment plants, a SCADA and public notification system for combined sewage overflow (CSO) events and monitoring the 84 lift stations and other remote points, a central data center and a Motorola Canopy wireless umbrella.
“The EWSU CSO project provides an excellent example of how SCADA technology is evolving and can be used in a creative manner to ease regulatory compliance,” says Michael Halbig, InGen’s president.
Environmental Protection Agency (EPA) regulations require utilities to monitor, generate reports and immediately notify the public about any CSOs. These can occur when the combined sewers can’t keep up with a heavy rainfall, and either storm runoff or combined wastewater is diverted to rivers or streams.
Fig. 3
RTU in enclosure at Long Beach Water Treatment Plant
According to Halbig, “The CSO project presented some interesting challenges. We decided to retain the existing Teledyne ISCO flowmeters, which were doing a great job under some pretty tough environmental conditions. To be able to provide remote, real-time access to the flowmeter data, we installed low-cost SCADA devices mounted in compact enclosures on nearby 40-foot poles, and ran a Modbus connection between the devices and the flowmeters. These low-power devices from Semaphore, called T-BOXes, combine RTU-like communications and control with onboard data collection, trending, alarming and long-term data storage, all in one box.
We equipped the individual T-BOXes with Motorola 900 MHz ‘subscriber module’ radios that communicate with Motorola Canopy wireless access points installed on top of three water towers throughout the city.”
This broadband wireless umbrella now provides an efficient communications backbone for the entire EWSU system.
“The ISCO flowmeters indicate how much, if any, combined wastewater is being diverted to the Ohio River, and the T-BOXes automatically upload this information in real time via the wireless umbrella to a secure server in the utility’s central data center. If for any reason, the wireless link is lost, the individual T-BOXes retain the data until it can be uploaded. A web server in each of the T-BOXes also provides a basic human interface and simplifies troubleshooting, if needed, via a technician’s laptop.”
InGen also developed a custom Web application for the CSO system that allows Evansville residents to subscribe for automatic overflow notification via email or to access current CSO status via the utility’s website. Real-time data from the flowmeters are automatically uploaded into this web application, thus meeting the EPA’s CSO notification mandate. Anyone can visit this website at http://cso.evansvillegov.org/.
You call that PC a master station?
The Long Beach (California) Water Department (LBWD) provides the city’s 487,000 residents with clean drinking water, collects more than 40 million gallons of wastewater per day, and operates and maintains nearly 765 miles of sewer lines. The complete network includes more than 90 remote sites equipped with RTUs plus 85 major equipment sites equipped with PLCs.
The SCADA configuration for the district’s water system gathers information from nearly 30,000 different widely dispersed data points via PLCs and RTUs. The Windows XP-based SCADA system uses Wonderware’s InTouch HMI software for real-time visualization for monitoring and control of the different sites. LBWD engineers programmed a PLC to poll the 40 remote sites throughout the water system an average of once a minute.
Operators can remotely operate pumps and valves via this HMI. This is important to the water department, since it enables the district to adjust water pressure in emergency situations. Data inputs from the remote PLCs and RTUs are centrally stored in a Wonderware IndustrialSQL Server historian, where the information is readily available to operators. Wonderware trending and analysis software helps the operators predict and avoid operational or maintenance issues and also to generate reports.
Fig. 4.
LBWD Sewer Pump Station SCADA display
LBWD, which, according to Gonzalez, was an early adopter of Wonderware HMI software, also uses the software for its groundwater treatment facility, the largest and one of the most modern of its kind in the United States. Here, a control system links nearly 1,500 data points from eight separate RTUs. The control system consists of two PC’s and one data-collection server that poll the department’s 50 remote sites an average of once every minute each day. Through continuous monitoring of the city’s sewer and storm drains, department operators can determine if pumping stations need to reroute water along different mains. Embedded system alarms were configured to warn operators about potential sewer overfills. Using information from the RTUs, water department operators can identify and locate sewer mainlines and assess lateral repair needs without undertaking what otherwise could be very expensive street excavation.
According to LBWD’s Gonzalez, “Now that real-time data is accessible from all the remote sites and our treatment plant, we no longer have to employ additional operators and maintenance staff to control various equipment and pumping stations throughout the city. The remote stations have local intelligence, which means they run as stand-alone stations. The operators have the ability to change remote station operations by downloading setpoints to increase or decrease flows.”
Is That a DCS or a SCADA?
At recently upgraded Formellino Wastewater Treatment Plant at Forenza, Italy, GE Fanuc Proficy HMI/SCADA software now runs in a PC runs over a programmable automation controller. In addition to performing traditional SCADA functions, such as data collection, trending, reporting and alarming, the new systems provides closed-loop process control functionality, similar to what you’d expect from a small DCS. The PAC is configured in a redundant, hot backup fashion, similar to the manner in which many DCS controllers are configured to provide high availability.
The old plant was run using fixed-time logic, where the sewage water was retained in the various vessels for a predetermined time period. To improve plant processing and energy efficiency, the new system controls the transit times of the sewage in the tanks and machine operation based on real-time sensor data, such as oxygen, ammonia, suspended solids and nitrates measurements.
The new control system also provides both a local operator interface in the plant as well as relaying data via a direct Modbus/TCP link to a central off-site control room that Hera Imola-Faenza, the company that operates the Formellino plant, mans around the clock to be able to monitor their different plants when they are unmanned.
Novanet, a system integration and engineering firm based in Imola, Italy, designed implemented the new SCADA and process control systems at the Formellino plant. The redundant GE Fanuc PACs provide the local intelligence and control and interface with the field instruments on a Profibus network using a combination of fiber optic and copper wire. There are approximately 600 controlled tags in all. A local computer running the GE Fanuc HMI/SCADA software collects, monitors and displays information and data for the local daytime operators. Data from the Formellino plant is stored in Hera’s SQL database and displayed so that a remote operator can be alerted to faults and respond if necessary.
In the short time since the new system has been in operation, process operations have improved and energy consumption has been reduced by 30%.
Is That a SCADA or a Decision-Support System?
Increasingly, new SCADA software applications provide critical real-time decision support information to help companies meet new, increasingly more complex business challenges. For example, generation management systems (GMS) extend SCADA technology to enable electric utility companies to operate successfully in the newly competitive, deregulated environment.
In one example, Invensys’ Foxboro SCADA group and a large, U.S. investor-owned electric utility designed a new GMS that enabled the utility to accurately determine its net energy position. This is critical for effective power supply scheduling and purchasing. The GMS provides:
- Improved ability to control generation schedules through implementation of automatic generation control;
- Advanced calculation engine to calculate net energy short and long conditions, losses applied to schedules and multiple ramp rates over a time base;
- Historical data collection, including short- and long-term data capture in a Microsoft SQL-compatible format;
- Forecasting tools, including real-time and historical trending, wind modeling and qualified facilities modeling.
Fig. 5
Formellino Wastewater Treatment Plant
The Invensys GMS enables the utility’s real-time operations group to determine accurately the company’s net energy position in real time. This capability is essential to allow the utility to compete effectively in the various electricity markets in which it participates, while optimizing the utilization of its power generation assets.
The Future of SCADA
So what does the future hold for SCADA users?
According to LBWD’s Gonzalez, “SCADA technology is getting to the point where the software can be programmed to take care of everything from controlling pumps and valves to bypassing problematic processors to automatically restarting a halted PLC or frozen PC. Already, my computers run around the clock and pretty much take care of themselves, though my technical staff check them weekly to verify communications.”
Wonderware’s Ballina adds, “Software distribution and management of very large systems will continue to improve. Easier access to larger bandwidth communications and the associate technology will continue to displace earlier modes and bring many SCADA systems from the scheduled poling schemes to continuous or near-continuous communications.”
SCE’s Peterson says, “The open architecture has allowed SCADA to morph from the old hard-wired days to what it is today, and I only see the SCADA architecture getting more open and non-proprietary. This includes both hardware and software platforms. I also think that we’ll see multiple applications running on one SCADA platform. For example, instead of just doing a little supervisory control and data acquisition, I think you’ll probably see some high-level batch applications doing things across blends, or detailed control applications working across different RTUs, while the high-level batch is running. In a large process plant, the DCS will still be your workhorse, but outside the plant, you’ll have SCADA applications that can keep running even if the communications are lost.”
Clearly, the distinctions between SCADA, DCS, PLC, PAC, HMI, MES and other technology categories and application spaces will become even less defined and less important as these technologies and applications continue to merge via the adoption of common industry standards and commercial IT technologies and approaches.
SCADA vs. DCS
While the line between SCADA and DCS appears to be blurring a bit, some important distinctions remain.
“Distributed Control Systems are very deterministic in nature. SCADA operates in a less deterministic, ‘select before operate,’ environment, where the control will periodically time out or deactivate for safety or security reasons. You’d almost never see that happen in a deterministic DCS,” says Invensys’ Chmilewski. “Another distinction is that, with SCADA, the hardware and software can be separate platforms. With a DCS, the hardware and software are bound together into one platform. Most SCADA today still deals with out-of-plant activities, often across widely distributed assets. However, it’s not uncommon for a SCADA system to sit over and provide supervisory functions for multiple different in-plant systems, such as process control, HVAC and laboratory systems,” says Chmilewski.
Wonderare’s Ballina adds, “Distributed control systems are very process-centric and focus on controlling the process. SCADA systems are more data-centric and focus on gathering data while performing supervisory control only. DCSs are permanently connected to their associated hardware, which is typically in one location. SCADA systems connect to widely distributed equipment and are better designed to deal with low bandwidth intermittent communications.”
ABB’s Quesada explains the differences between DCS and SCADA as follows:
While a DCS will typically have a relatively small number of I/O concentrated at a single site, a SCADA system will typically have a large number of I/O spread over multiple sites. A DCS is controller-centric, and those controllers will typically be made by the DCS vendor; SCADA is system-centric and can communicate with many different brands of RTUs and PLCs. A DCS is designed to communicate with controllers over a high-speed network; SCADA is designed to communicate over many different communications media and often at low speeds. DCSs are designed for very fast data acquisition (measured in milliseconds); SCADA data acquisition operates at moderate speeds (measured in seconds). The respective approaches to fault-tolerance and recovery also differ. DCSs have redundant hot servers, preventing disruption in the event of switchover. With SCADA systems, the redundant server will be in standby mode, requiring seconds to switchover. Unlike most DCSs, SCADA systems also have the ability to buffer data locally when communications are interrupted, enabling the upper level SCADA station catch up with no data loss once communications are restored. This is known as “store and forth of data.”
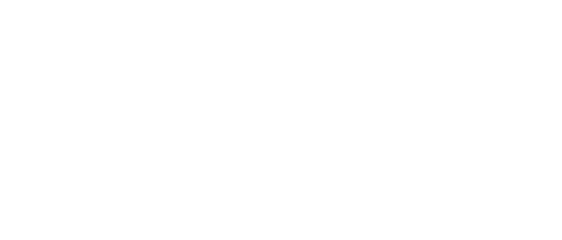
Leaders relevant to this article: