By Dave Harrold
A dozen years from now—2020—Brazil, China, India, Indonesia, Mexico, Russia and Turkey could account for as much as one-fifth of global pharmaceutical sales, according to a recent PricewaterhouseCoopers report, “Pharma 2020: The Vision—Which Path Will You Take?” PricewaterhouseCoopers also reports that 58% of multinational pharmaceutical executives said the center of gravity is shifting to Asia Pacific.
Richard Spoor, senior vice-president of global procurement at Merck & Co., Whitehouse Station, N.J., says, “We’re seeking to outsource non-core functions—those where external manufacturers may have greater expertise, and also have the ability to deliver a particular active ingredient, excipient or even a final product more efficiently than we could.”
Janet Woodcock, deputy commissioner of the U.S. Food and Drug Administration (FDA), has alluded to one of the reasons: Pharmaceutical manufacturing is not “state-of-the-art.” She went on to describe what is causing many drug manufacturers to incur manufacturing costs that are as high as its R&D investments.
According to Woodcock, manufacturing utilization rates are as low as 15% at some companies due mainly to inefficient batch production processes. Woodstock added that some companies are wasting as much as 50% of what they produce; product scale-up activities remain unpredictable; some companies’ global operations are fragmented; and too many companies don’t know the causes of production failures.
The handwriting is on the wall. Like it or not, where and how we manage batch processes will differ dramatically by 2020.
More Innovation Required
Many batch management innovations were initiated by people working in the highly regulated biopharma sector. Ironically, at the same time, the sector lags behind others in implementing these improvements. (See “Is PAT a Silver Bullet,” June ’08, p.55.)
From a controls, automation and integration perspective, among the most significant of these efforts is the ANSI/ISA-88 and -95 series of standards and references.
Bob Lenich, data management services director with Emerson Process Management, observes, “Certainly the adoption and use of past innovations and solutions will continue to represent good engineering practices in the future. However, where and how the biopharma sector manages batch processes in the future requires that it embrace the industry’s Operational Excellence and FDA’s Process Analytical Technology (PAT) initiatives to seek out and adopt even more innovative batch management solutions that reduce batch review and release cycle times; increase use of integrated recipes and automation to reduce unintentional SOP errors and batch processing problems; reduce recipe-to-recipe and batch-to-batch variability; and increase standardiz ation to support technology transfer and help ensure regulatory compliance.”
When you add these goals to the likelihood of increased contract manufacturing from the burgeoning drug manufacturing business overseas, and factor in recently introduced prescription drug “pedigree” laws, it may appear that the pharma industry is facing insurmountable odds—until you learn that some pharmaceutical companies are close to achieving these goals.
Each year, the International Society for Pharmaceutical Engineering announces the winners of its Facility of the Year Awards. In 2007, Cook Pharmacia in Bloomington, Ind., won for Facility Integration, and Genentech’s Oceanside, Calif., facility won for Project Execution. Both used advanced approaches. Cook’s project transformed an abandoned television factory into a scalable, tightly integrated contract manufacturing facility, while Genentech’s “design-build hybrid” project used ISA88 to develop an automated recipe-level process control system. Genentech applied the FDA’s 21 CFR Part 11 regulation to develop a paperless, dock-to-dock system that includes assembly of electronic batch-end records and electronic signatures. What Cook and Genentech’s accomplishments reveal is that, when it comes to batch management, innovation is quite doable.
MES Misapprehensions
At a recent control and automation user conference, David Kircher, manager of global manufacturing execution systems (MESs) for Abbott Laboratories, Abbott Park, Ill., described how Abbott implemented a highly automated, tightly integrated batch management solution at its facility in Barceloneta, Puerto Rico. He reported there was considerable discussion at Abbott about the need for an MES at the Barceloneta plant, but there also were some common misapprehensions about MESs, such as:
- MES is best suited for single-product plants. False. Because MES facilitates product changeovers and enables other efficiencies, it’s actually better suited for plants producing campaigned products.
- Avoid implementing MES during plant start-up. False. Despite some disruption during implementation, a significant amount of good results come from implementing MES from the beginning. With MES present, there is no need to write instructions and author procedures more than once, and personnel training can be streamlined and standardized.
- Delay the cultural trauma of switching to a paperless system until after plant start-up. False. The need to undergo this culture change has to happen sometime; why not sooner rather than later?
- Enterprise resource planning (ERP) and process control systems (PCS) can be made to do what an MES does. False. Each of these tools—ERP, MES and PCS—has a sweet spot. For MES, it’s the ability to manage manual operator instructions and procedures, close orders, execute weigh-and-dispense activities and perform other functions. ERP and PCS also have advantages and limits. For example, Abbott’s ERP system doesn’t handle material expiration dating.
- MES represents a huge integration challenge. False. MES implementation doesn’t necessarily require customization. Abbott’s customizations were limited to integrations and custom reports. Everything else was implemented “out of the box.”
Honeywell Process Solutions’ Chris Morse adds that MES can help close the cost of the production/sale price loop by automatically collecting costs, such as raw materials, utilities, equipment occupancy, etc., and presenting business managers with near- real-time production costs.
Despite these successes, not every batch manufacturer has figured out how to address these issues. Kam Yuen, Proficy product manager at GE Fanuc, says GE Fanuc is seeing more flexible batch management projects that include quality initiatives. However, sometimes they’re designed incorrectly, so the installed solution doesn’t deliver the expected or potential benefits.
Yuen’s observations are shared and expanded on by Paul Wlodarczyk, vice president at JustSystems. Wlodarczyk believes that for the biopharma industry—product-owner companies and contract manufacturers—to work together, they must use a standardized batch control and recipe development solution.
“Product development information is often recorded by scientists using flowcharts and spreadsheets. When it comes time to transfer product and process information from R&D to a pilot plant and, later, to production, extracting and interpreting this information requires a series of conversations and manual development of new documents. This is difficult and time-consuming when all parties work for the same company, but transferring this information between the product owner and a contract manufacturer to produce an executable recipe can be downright maddening. By leveraging the World Batch Forum’s BatchML implementation of the ANSI/ISA 88 family of standards, it’s possible, using the XML schema language, to develop upstream recipe development tools that can output BatchML-conformant recipes,” claims Wlodarczyk.
Changing the Picture
Since about 1990, the biopharma industry has invested heavily in information technologies (IT), and those investments have paid dividends. However, according to a number of surveys, these IT investments could be doing much more.
One such poll occurred during a recent batch management webinar about moving from paper to paperless manufacturing. During the presentation participants were asked, “How are you managing recipes and process definitions today?”
Participants selected from one of four pre-defined answers, and the tabulated results were as follows:
- 42.3% selected “Manual, ad hoc, spreadsheets, flow charts and other static documents;”
- 11.5% selected “Manufacturing operation adopted ISA88 standards, but in isolation (no coordination with R&D or enterprise ERP systems);”
- 30.7% selected “Process development hands off process specifications to contract manufacturer responsible for recipe development;”
- 23.0% selected “Standardized, authoritative, reusable process definitions and manufacturing actions.”
When you compare these poll results to how to address Lenich’s four goals, one solution keeps showing up—create a robust MES environment based on quality-by-design principles the FDA has been evangelizing for nearly a decade.
Kircher says MES solutions come in many flavors, but users should still expect out-of-the-box capabilities that address:
- Document control and archiving that provides controlled access and version control per FDA 21 CFR Part 11 requirements;
- Electronic batch records that conform to cGMP best practices, support multiple entry methods, manage execution of standard operating procedures and production batch protocols, while providing complete traceability, batch history, audit trails and consistent reporting;
- Equipment tracking that includes equipment properties, status states and events such as usage, cleaning and maintenance;
- Material management that supports material lifecycle workflow, including management of material purchasing, receiving, warehousing and shipping;
- Recipe authoring that uses object-oriented techniques, supports multiple languages and produces XML-based work instructions;
- Scheduling and tracking that meets requirements dictated by master recipes, manages conflicts and keeps ERP systems updated;
- Security and audit capabilities that rigorously conform to the FDA’s 21 CFR Part 11 regulation for electronic records and signatures;
- Statistical analysis of analog values and discrete events, with charting and trending tools that help with continuous improvement efforts;
- Training and development records management and tracking of cGMP courses, administration and personnel scheduling;
- Weighing and dispensing that guides operators through pre-defined and approved workflows, uses bar-code scanning, electronic weigh-scales, etc., and produces a complete record to facilitate product release and regulatory review.
We’ve taken a peek at a few biopharma companies that have successfully made the business-to-production connection. Abbott shared some impressive, quantified improvements resulting from their MES implementation. We know that volumes of stories exist that describe successful S88, S95, BatchXL, MES and production-to-ERP implementations. With so many tools and publicized successes, why would the FDA’s Woodcock say that pharmaceutical manufacturing is not “state-of-the-art?”
I’m going out on a limb, and say the problem Woodcock refers to isn’t so much about availability of advanced batch management technologies, but rather about the slow adoption rate of commercial off-the-shelf technologies caused by our reluctance to embrace change.
Logically, those who recognize, embrace and pioneer batch management improvements will be here in 2020 and beyond. Those who don’t, won’t.
Dave Harrold is co-founder of the AFAB Group.
ISA88 in BriefISA88 is designed to address four areas of batch control and automation:
Note: ANSI/ISA88 is known internationally as IEC 61512. |
Abbott’s Quantified MES SuccessAfter one year of operation, Abbott validated the benefits of its Baceloneta, Puerto Rico, facility’s MES implementation. According to Kircher, Abbott’s use of MES eliminated 40% of documented exceptions, with contributions coming from:
|
ISA95 in BriefISA95 addresses three areas of control-system-to-business-system integration:
|
BatchML in BriefBatchML is a set of XML schemas written using the World Wide Web Consortium’s XML Schema language (XSD) for implementing batch, master recipe and equipment data in part or in whole per the ANSI/ISA88 family of standards. BatchML is available royalty-free provided credit is given to the World Batch Forum. Visit www.wbf.org for more information. |
Latest from Asset Management
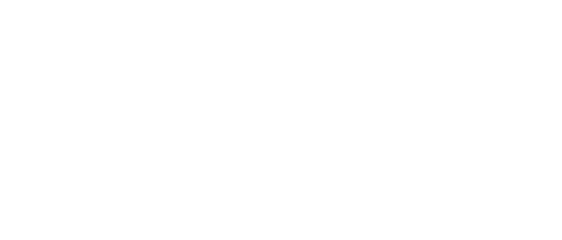
Leaders relevant to this article: