By Rich Merritt
For several years now, ISA88 has been accepted worldwide as a way to define recipes and control batch processes, and ISA95 is gaining more acceptance as a way to connect batch control systems to higher- level software, such as data historians and ERP. But users and vendors are beginning to discover that both ISA88 and ISA95 can be used for more than just batch.
Take Steve Rubin, president of Longwatch in Norwood, Mass., for example. Longwatch makes video surveillance equipment that connects to HMI/SCADA systems via plant industrial networks, such as Modbus or Ethernet. Longwatch lets operators actually see the process equipment they are monitoring on HMI workstations (Figure 1).
Figure 1: Longwatch allows operators to monitor a process and see it at the same time. Video snapshots can be scheduled in ISA88 and stored away in batch records for visual confirmation that process steps were carried out properly.
Rubin has been demonstrating Longwatch systems to pharmaceutical companies as a way to verify that operators actually add the ingredients or perform other scheduled operations when theyre supposed to. He suddenly realized that commands to take video snapshots could be integrated into ISA88 recipes, and the video images, time stamps and event logs could be sent to historians and FDA documents via ISA88 and ISA95.
This opens up a whole new venue for us, says Rubin. Thanks to ISA88 and ISA95, we can provide any company thats controlling a regulated process with video proof that operations, steps and procedures are actually being carried out when required, and embed the information into an historical record that can be called up when needed.
Hes not the only one who was surprised by the capabilities of ISA88 and ISA95. These two standards are being used for everything from continuous process control to packaging equipment and robots. The toughest sell is to continuous control, whose advocates remain unconvinced. But the times they are achangin, and a marriage of batch and continuous loomsespecially since many ISA88 and ISA95 applications are already living in sin, some without the knowledge of their continuous control parents.
Continuous Control Isnt Continuous
Most people identify ISA88 with pure batch control and recipe formulations. But ISA88 allows procedures, steps, logic and other functions to be defined, which means it can be used to define continuous processes too. Thats because continuous processes arent really continuous.
As my old boss, Dr. Ray Copeland at CRISP Systems in Columbus, Ohio, used to say, Most continuous processes are actually piece-wise continuous. That means even continuous processes have non-continuous elements, such as start-up, ramp-up, shutdown, emergency shutdown, clean-in-place, and so on. Tanks have to be filled and emptied, requiring on/off control of valves and pumps. One way to look at a continuous process is that it is really a batch process with a very long steady state in the middle.
Steam generation might be considered a continuous process, but Jean Vielle, president of Control Chain Group, a consulting engineering company in Paris, France, says it can be defined in ISA88 as a procedure with operations, phases and control modules (Figure 2). Setting up the ISA88 definition for Boiler 1 can easily be replicated for Boilers 2 and 3, says Vielle. This simplifies configuring a steam generation process.
Figure 2: Some people may think steam generation is a continuous process, but it can be defined in ISA88 for steam generation.
Steve Zarichniak, of Honeywell Process Solutions, says Honeywell used ISA88 in a customers continuous process. At a specialty polymers plant, the customer was faced with the problem of making a grade change every three days, says Zarichniak. Each grade change took up to half a day with the old system, and at least one complete shutdown happened every year because of poor operator transition technique.
By using ISA88, the plant was able to define transitions and grade changes for many different products and dozens of possible transitions from one product to another. After converting to ISA88 and automating best practice transitions, the company cut off-prime product by 20% and saved over $2 million per year, says Zarichniak.
Companies all over the world are using ISA88 in similar non-batch applications. But the toughest sell appears to be to the continuous control people.
Selling ISA88 to Continuous Control Advocates
Lynn Craig, past chairman of the SP88 committee that wrote the ISA88 standard, says that ISA88 is a good way to handle all the non-continuous aspects of a process. The biggest sources of potential problems in a continuous process are start-up and shutdown procedures, plus any other procedures that operators dont do often, says Craig. This is because these are mostly manual processes and depend on operator skill and training. Continuous processes sometimes run for weeks and months between start-up and shutdown, so the operators dont do a procedure often enough to stay sharp on the details. Computers dont forget anything, so if the procedures are defined in ISA88, then theyll be done exactly the same way every time and are no longer dependent upon the skill of the operator.
Doing manual processes incorrectly can shut a unit down. Honeywells Dr. Wayne Gaafar says, In petrochemical and refining processes, start-up and shutdown often are the most dangerous times because if things get in the wrong state at the wrong time, then it creates a dangerous abnormal state that could result in an incident. If start-up or shutdown go awry during a simple grade change, the process unit may have to go into an emergency shutdown, which might take it off line for days, instead of for a few hours. This can cost millions of dollars, just because of poor operator transition technique.
Dave Emerson, director of the U.S. Development Center for Yokogawa Corp. of America in Carrolton, Texas, says loss of operator knowledge applies to all processes in general. Many companies are losing employees or watching their workforce get older, and process knowledge is leaving the company, he says. In some cases, processes have been running without problems for years, mainly because of the skilled people involved. When they leave, this information may not be passed on. Unless the company defines the process in ISA88, that is.
Marc Leroux, marketing manager for ABBs Collaborative Production Management, agrees. The issue of skill loss is huge and much more complex than can be addressed by one standard. The continued implementation of standards like ISA88 and ISA95 greatly reduce the impact of the skill loss, but there is no one standard that does it by itself. That said, implementing ISA88-based solutions go a long way to reducing some of these issues.
Dave Chappell, president of Complete Manufacturing Automation Associates in West Chester, Ohio, has married several continuous processes at Procter & Gamble to ISA88. At Procter & Gamble, we have successfully created hybrid process control applications, says Chappell. The results of these adventures exceeded expectations. Using the recipe management and sequencing capabilities of ISA88 improved the operational management and execution of continuous manufacturing, though gaining acceptance was quite difficult.
ABBs Leroux says one of the major issues in gaining acceptance is that engineering contractors and end users are focused on capital costs rather than operational excellence. In many cases, the requirements are quite straightforward and easily implemented at the controller level, he says. Moving it up to the unit level improves OpEx, but it comes at a higher cost.
Chappell says that getting ISA88 accepted by continuous advocates is a challenge. There are groups that believe strongly in the superiority of continuous manufacturing, and they will go to great lengths to prove it, including rejecting any automation techniques that are shared with batch systems, he says.
Emerson says one way around this problem is to not call it a batch solution, which can kill the idea from the get-go. If you can address their process problems from a business standpointsuch as how do you handle product changes, or how do you document the process?then you can introduce ISA88 concepts of modular automation, procedural control and tracking production without calling it batch.
He also sees more acceptance of ISA88 in continuous processes because engineers with ISA88 experience are changing jobs. As the pool of engineers familiar with ISA88 has grown and individuals have moved between companies and projects, he says, it has been natural for them to use their successful practices in batch in other areas. We are just starting to hear more of this in application papers and case studies.
Honeywells Gaafar agrees and adds wryly, We never mention the B word to continuous control people. Instead, we tell them we have a standard framework for defining process operations, transition management and report generation. If they ask, we tell them its based on ISA88, but we never mention the word batch.
Leroux also agrees. Removing batch from the descriptions is a start, he says. Another way, which ABB supports, is to use the standards internally for our own solutions. For example, ABB uses ISA88 as the mechanism for dynamically configuring analyzers in our Industrial IT for PAT solution.
Figure 3: ABBs factory in Dalmine, Italy, produces medium-voltage switchgear products. The automated factory relies on ISA95 for communication to the business system layer, and uses the models for scheduling, processing, tracking and reporting of materials.
Others are turning to ISA88 because they cant find similar solutions on the continuous side. Zarichniak of Honeywell explains, Tracking production runs in a continuous process is a nightmare with standard historian or data acquisition software, he says, because it isnt set up to handle all the various procedures. Programmers can write spaghetti code to tie it all together, but it is much easier to generate production reports using ISA88.
ISA88 Engaged to ISA95
Many people view ISA95 as sitting atop ISA88 in the missionary position. Essentially, an ERP or other enterprise function tells ISA95 what to make; ISA95 relays this information to ISA88; and ISA88 tells the control system how to make it. Like many marriages, the problem has been that ISA88 and ISA95 dont talk to each other very well because they dont use the same definitions. Tools such as B2MML (Business to Manufacturing Markup Language) and BatchML (Batch Markup Language), developed by WBF, can be used to make the connection.
Work is underway to correct this deficiency. A recent draft report, Harmonization of Industrial Automation Standards, also known as ISA TR 88-95.01: Alignment of ISA-88 and ISA95, is a major step in resolving the issues. The marriage proposal was submitted to the ISA Standards and Practices Board on July 15, 2008, for approval and publication. TR-88-95 recognizes that automation involves more than just batch control. (Table 1 illustrates that all types of manufacturing are involved).
In a classic case of practice what you preach, ABB uses ISA88 and ISA95 in its own manufacturing operations. Leroux explains: Several years ago, ABB was looking to modernize the workflow and information exchange in our factories, which produce electrical components, such as circuit breakers, switchgears, motors and drives. The initial reaction was to use the technology and solutions that ABB provides to other manufacturers in the process industries. ABB already provides solutions based on ISA95 for hybrid manufacturersthose that have a mixture of batch, continuous and discrete in their facilitiesso using the same solutions for our discrete manufacturing sites made sense. The ISA95 solutions for ABB factories are being rolled out worldwide and use ISA95 for communication to the business system layer, scheduling, processing, tracking and reporting of materials throughout the facilities.
The TR88 report identifies key areas of overlap and gaps between ISA88 and ISA95, and shows how to make the interactions work. Its just the first step in the marriage between ISA88 and ISA95, but it shows that progress is afoot. As ABB and others have demonstrated here, ISA88 and ISA95 arent just for batch any more.
Getting into Discrete
ISA88 is moving into discrete automation, too. John Parraga of Rockwell Automation used ISA88 to automate an anodizing application that involved robots, robot controllers, cranes, processing tanks and part ID tags. The control portion involves regulatory control, monitoring, interlocking, exception handling and repetitive discrete managed as sequences.
We used Rockwell Automations FactoryTalk Batch to define the system, says Parraga. First, we used the equipment editor to define what the plant equipment is capable of doing. Then, we used the recipe editor to define the procedures that coordinate the equipment. If the equipment isnt capable of performing the function, the recipe editor wont permit it.
FactoryTalk Batch provides sequencing instructions as well as the equipment arbitration needed to carry out tasks, and then downloads commands to the controller or to an operator to perform a task manually.
Parraga says Rockwell Automation is using the ISA88-based FactoryTalk in several other non-batch applications. In one application involving manual assembly of high-reliability military batteries, we use ISA88 to define every step in the process, he says. The system tells the operator exactly what to do, checks quality measurements and logs everything.
Hes also involved in a brewery routing application, which has many storage tanks and many filling stations. Connecting these is usually a job for PLCs written in relay ladder logic. Parraga is using ISA standard concepts to determine routing instructions involving tanks, valves, pumps and filling stations. ISA88 organizational concepts help determine what has to be done to get beer from any tank to any filling station.
Applying ISA88 design principles is beneficial to a wide range of industries, says Parraga.
Rich Merritt is a contributing editor to Control.
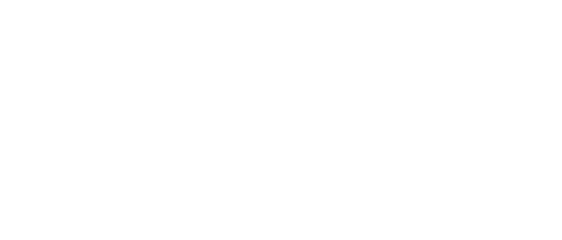
Leaders relevant to this article: