Over the past three years, wireless field networking technology has taken the process industries by storm. Answering the need for fast and easy implementation relative to wired alternatives, hundreds of wireless mesh networks and thousands of wireless sensors have been successfully deployed and continue to reliably, efficiently and economically broaden the measurement landscape.
“The principal advantage we see around wireless is the ability to accumulate and analyze a much greater array of data than would otherwise be possible,” says Michael Ingraham, technical manager at BP’s Cherry Point refinery in the U.S. “Wireless enables us to get more data more efficiently, more economically than we ever have been able to in the past.” (For more ideas on how leading process manufacturers are innovating globally with wireless field networks, see the article, “Far From Quiet on the Wireless Front.”)
In addition to the new frontier of sensor data afforded by the wireless field is a large and rapidly growing class of wireless success stories: “plant-level” applications that are boosting the productivity, safety and security of plant personnel as well as easing the connection of physically disparate digital systems into an integrated whole.
To accommodate the disparate needs of wireless field- and plant-level applications, Emerson Process Management’s Smart Wireless architecture consists of two layers that are seamlessly integrated with the company’s control and plant network offerings (Figure 1). The plant-level wireless layer is based on Cisco’s Unified Wireless Network architecture, and is managed through the Cisco Wireless Control System (WCS) platform.
Ways to benefit from plant wireless
Having successfully implemented hundreds of wireless field network applications, Emerson has more recently seen a dramatic up-tick of interest in plant-level wireless network applications. Topping the list of customer requested wireless applications are: empowering mobile workers, location tracking, safety mustering, integration of non-traditional signals such as video, and bridging remote or isolated control systems.
Mobile worker productivity. Perhaps most appealing of all wireless plant network applications are those designed to enhance the productivity of mobile workers. Indeed, it’s here where perhaps the biggest wireless plant network returns are to be made—incremental productivity improvements that pay off repeatedly. “The dollars really add up when you can save 10 minutes to an hour, over and over again,” explains Neil Peterson, wireless services marketing manager for Emerson Process Management.
The variety of wireless-enabled mobile devices now available ranges from hardened, 13-in. tablet PCs to ½-VGA palm-sized devices to hand-held communicators. For example, the Panasonic U1 is a handheld PC that includes built-in Wi-Fi and cellular communication capabilities and is able to run a full-featured Emerson DeltaV operator interface client.
“The operator is no longer chained to his desk,” Peterson says. “We finally have the devices and the networks that make this possible.” And instead of installing a wireless plant infrastructure, users can even leverage commercial mobile data networks where it makes sense. “All you need is a connection back through the firewall, a data plan, and away you go.”
Smart handheld devices, of course, have been around for some time—streamlining data-gathering tasks during operations and maintenance rounds. But with wireless connectivity comes the ability to continuously synchronize data as workers move from point to point. There’s no need to dock the device at the end of the shift; information moves and updates immediately.
A growing class of worker mobility applications is allowing plant personnel to readily access the information they need, wherever they are in the plant.
Another and often critical class of wireless plant network applications involves real-time location awareness. That is, the ability to know where your people and your mobile plant assets are located at any given time. In the case of a safety incident, the ability to know immediately where all your employees are facilitates safer and more efficient mustering. The wireless application replaces clipboard tracking, allowing for quick, automated roll-call during an emergency.Location tracking and safety mustering.
Tracking the location of high-value equipment can be a boon to maintenance productivity. Further, when paired with a growing range of mobile worker applications, location awareness could even be used to manage a particular operator’s permission levels relative to their specific location in the plant.
Video. Because broadband plant wireless networks are based on commercial IT networking technology, they can readily handle a range of signals more common to the telecom world, namely wireless video and voice. Video applications include both process monitoring and security applications – for the video monitoring of flares, for example, or for complying with perimeter security monitoring requirements.
Bridging. The higher bandwidth of plant wireless networks is required in the bridging of two control system areas into one network.
“A wireless segment is an effective means of integrating two remotely located control systems,” says Peterson. The wireless bridging of two areas of control systems may be essential when the systems are located across bodies of water or are separated by terrain that is too difficult or expensive to trench for cable.
Field data back-haul. Similarly, wireless back-hauls are used to integrate remote wireless field networks into the existing plant-level control network: Wi-Fi is used to overcome obstacles to physical network wiring such as roads, rivers, railroads or just plain distance.
Wireless-enabled operations management
The promise of a wireless-enabled mobile worker is even more potent when considered in the context of the latest generation of real-time production management applications such as Emerson’s new Syncade smart operations management suite offering. Itself a modular, scalable suite of software applications, Syncade is designed to integrate real-time plant-floor data with off-line and transactional plant business processes. Add wireless mobility to the mix and you have a powerful combination for improving productivity while avoiding procedural and documentation errors.
Consider, for example, the following scenario: A wireless pressure transducer alarms because of excessive pressure drop across a filter. The alarm is seamlessly transmitted to the control room operator who, suspecting a plugged filter, locks out the associated pump and kicks off a maintenance request.
A maintenance tech receives the request on her wireless-enabled mobile device and, because she can directly access the pump and filter specifications from her handheld, arrives in the field with requisite spare parts in hand. She then accesses the control system to verify that the pump is indeed locked out, accesses the work processes library for the proper filter replacement procedure, scans the barcodes on the filter and pump to track and ensure the proper filter is being used, and replaces the filter. Then, she updates the equipment maintenance log electronically to sign off and places the pump back in available status. All from the convenience of her wireless handheld device.
Regulatory compliance can also be enhanced by a combination of a plant wireless network with real-time production management tools. Imagine that a technician is sent to confirm that Unit 1’s safety system is working. Syncade suite, communicating with the worker’s mobile device, verifies that the tech’s safety training is current, verifies that the test procedure being utilized is current, collects data as the tech executes the procedure, and then documents that the test was properly completed with all associated data and records.
Wireless plant networks have requirements that are unique and different from wireless field networks. Wireless field networks, including those described by the WirelessHART standard, are single-purpose and low in bandwidth and power consumption. Wireless plant networks, on the other hand, are based on IEEE wireless network standards common to the broader IT world, including the 802.11-2007 Wi-Fi series of wireless protocols. These higher bandwidth plant networks are designed to accommodate multiple simultaneous applications. “The plant network completes the union of a seamless wireless plant architecture, bringing the higher capacity that spurs full integration of the likes of cameras and bar code gear with the process infrastructure of intelligent information-bearing field devices,” explains Jane Lansing, Emerson Process Management vice president. “It’s a marriage of networks for a sustainable future of advantages.”
“The wireless plant network is a shared resource,” adds Emerson’s Neil Peterson. “You can have multiple virtual networks within one physical plant network.” These virtual local area networks are configured with quality of service guarantees; to ensure that control signals, for example, have the proper transmission priority relative to other, less critical signals such as video monitoring. “You can use one physical installation of wireless mesh network hardware for multiple and different applications such as video and personnel tracking,” Peterson explains.
Start anywhere. start today
It’s important to note that a key differentiator of the Emerson Smart Wireless network offering is its scalability. Users don’t have to install both field- and plant-level wireless networks at the same time. Users can start small, with either a field- or plant-level network and evolve from there.
At the field level, users can start with a gateway and a handful of measurement points and, as long as a few simple rules of thumb are followed, have confidence that the mesh network will come to life with little fuss. No exhaustive site survey is necessary, and an initial field network can be readily expanded—in fact becoming more reliable as more measurement points are added.
At the plant level too, users need not start with an extensive wireless infrastructure. Indeed, two of the most common wireless plant network applications – the bridging of two control system networks and the back-haul of field network data – are relatively straightforward to get up and running, requiring no extensive infrastructure plan (and no site survey if it is less than five miles and there is a clear line-of-sight).
Of course, deploying an asset tracking application over a wide area would require a bit more planning, engineering and a site survey—but fortunately there’s help available for that, too.
So you’re ready to scale…
You may have started with a wireless field network in a tank farm. Then added a localized mobile worker application. But at some point you may be ready for a full-blown wireless infrastructure project—and you’ll be glad you started with Emerson.
One key aspect of Emerson Process Management’s approach to wireless plant-level networks is its relationship with networking leader Cisco Systems. Cisco’s industry-leading Wireless Control System (WCS) for wireless network planning, configuration and management provides a cohesive communications platform across the physical as well as the functional areas of plant operations so that a shared wireless plant network can readily grow into and support a variety of applications.
Emerson itself offers a comprehensive services portfolio to help customers design and deploy wireless plant networks. With three global service centers located in North America, Europe and Asia, users can be assured of consistent support on a global basis. Included in the project services portfolio are capabilities for site surveys, network planning and design, network installation and commissioning, application implementation, network support and management, as well as project management. And even after your wireless network is up and running, Emerson’s after-project support is available to help you continue to get the most from your wireless plant network investment.
Latest from Safety Instrumented Systems
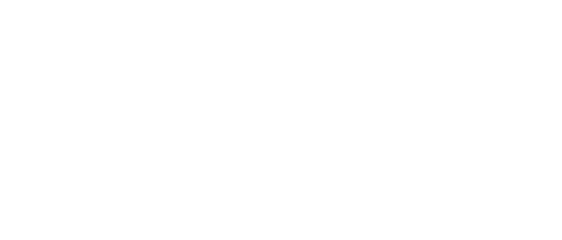
Leaders relevant to this article: