This article was printed in CONTROL's August 2009 edition.
By Jim Montague
Wireless is getting easier. No kidding. Just a few years ago, when wireless technologies began to migrate from old-time radios to digital nodes and fieldbus-like networks, much of the initial advocacy focused on it as a logical replacement for hardwiring. Consequently, discussions about how to implement it focused on the physics of wireless transmitters, antennas, coverage areas, signal strength, frequencies, bandwidth, data rates, packet sizes, switching and other interference-limiting issues that could make it as reliable and familiar as hardwiring.
Since then, some increasingly brave souls have adopted a variety of wireless methods. And many wireless devices and their underlying software are steadily improving, removing early technical barriers, and making many wireless tools far easier for even novice users to understand, set up, program, configure and deploy. Now, those early adopters are extending their leads because they have the wireless experience, foundation and conceptual know-how to fulfill the original potential of wireless and take it in directions it was probably supposed to go in the first place.
However, StatoilHydro reports flow loss at the three platforms was very hard to detect because there were no flowmeters in the well pipes. Also, manual readings were taken only at the beginning and end of a shift, so a flow loss could easily go undetected for a long time. Unfortunately, installing flowmeters in the wells wasn't practical because it would have required a complete and prohibitively costly production shutdown. As a result, the company's engineers decided a non-intrusive solution was required, but also knew that new sensors would need a link back to the control room. However, the wellheads were very crowded and had to be kept clear for safety, so introducing added cabling, trays and junction boxes wasn't possible.
To automate its flow loss monitoring unobtrusively, secure real-time data and reduce personnel presence in hazardous areas, StatoilHydro's engineers implemented a pilot wireless project on its Gullfaks A, B and C platforms by installing Emerson Process Management's (www.emersonprocess.com) 648 wireless temperature transmitters to indirectly indicate flow on lines at each of 40 wells. Equipped with the HART Communication Foundation's (www.hartcomm.org) WirelessHART protocol and Emerson's SmartWireless capabilities, the three platforms' new wireless devices transmit readings every 30 seconds from clamp-on temperature sensors mounted on the surface of the flow pipes and send them back via a Smart Wireless gateway. Tormod Jenssen, staff engineer for plant integrity at the Gullfaks field, adds that, "Emerson's wireless transmitters enabled quick and reliable detection of lost flow and allowed immediate action to re-establish flow and increase production."
Anders Røyrøy, StatoilHydro Norway's project manager for R&D projects, adds, "Installing added wired measurement points at the wellhead would have meant lots of wiring and long cable trays. However, we were able to install the new wireless devices very quickly. Typically, it only took a few hours to install each wireless device, compared to up to two days for each hardwired device. Wireless offers an inherent reduction in cabling infrastructure, complexity and weight, resulting in lower installation costs. Because there's daily radio communication in the well area, it's essential that the wireless field network coexist without reduced performance. Smart Wireless mitigates the impact of interference, and the data reliability is 100%. Rich process information and plant diagnostics are essential for unmanned operation, and by introducing Smart Wireless transmitters to our platforms, we're making broad strides towards our goals."
More recently, StatoilHydro added more Smart Wireless devices at Gullfaks, for a total of 90 wireless transmitters covering all production flow lines on the three platforms.
The Basics
To secure both the obvious and less-apparent advantages of wireless, veteran users and system integrators have several primary recommendations—even though every process application has its own unique characteristics and needs.
Steve DeHaan, P.E., engineering vice president at Technical Systems Inc. (www.tsicontrols.com) in Lynnwood, Wash., says potential wireless users should first learn the basics of radio frequency propagation for the various frequency ranges, and then understand the various radio frequency (RF) network architectures and communication methods, including point-to-point, point-to-multipoint, mesh, store-and-forward, repeaters and others. TSI is a large system integrator that's worked in the water and wastewater market for nearly 40 years. It has experience in radio telemetry systems, and most of the systems it has installed use FCC-licensed frequencies in the 170 MHz to 460 MHz range due to the site-to-site distances, terrain and tall trees common on the U.S. West Coast. TSI also has experience with 900MHz and 2.4GHz systems for higher bandwidth applications, such as wireless Ethernet.
"Users should identify and define the requirements of their planned wireless system and then determine when wireless makes sense. They need to look at the cost, reliability throughout and response of wireless, and compare it to hard wiring," says DeHaan. "An onsite RF path survey using the proposed equipment is very important and must be done before finalizing the wireless system design and purchasing equipment. Most wireless manufacturers will loan demo equipment for a few days of onsite testing. The onsite survey will help identify radio path problems due to obstructions, terrain, distance, etc., and will help to identify repeater locations if necessary.
"When a manufacturer claims a certain ‘range' for its products, this claim must be taken with caution because it's usually a maximum range in an optimal environment—in flat terrain between transmitter and receiver, with no obstructions or interference. The user must also recognize that higher frequencies offering higher bandwidth come with much lower range limitations and increased susceptibility to noise. When comparing products, users should look at the tangible performance values for each device, namely transmitted power and sensitivity, instead of the maximum range claimed."
Starting Small
Another way that users begin to approach wireless is by trying it out in the smallest, non-critical application in their facility—often just a couple of signals via one or two transmitters, antennas and receivers. Several suppliers offer very basic packages that rookies can use to experiment with wireless, and then scale up as they gain experience and knowledge about how wireless works in their facility and local environment.
In fact, Emerson's Smart Wireless field starter kit establishes an out-of-the-box, secure, self-organizing WirelessHART network that delivers greater than 99% communications reliability in the steel-and-concrete setting typical in most industrial plants. The kit also contains discrete switches and vibration and pH transmitters.
Though they can be adapted to specific needs and environments, there remain several basic steps for getting wireless up and running in any application or facility, according to Penny Chen, Ph.D., principal systems architect for Yokogawa Corp. of America's (www.yokogawa.com/us) IA Global Marketing division. Dr. Chen says this list should include:
- Understand your process application's needs and use them to direct you toward the appropriate wireless solution for it.D
- Develop your wireless and update your wired integration strategies together and employ your overall networking needs to help pick the right standardized wireless technology for your application.
- Perform a site survey to gain a thorough understanding of your facility's environmental conditions, limitations or likely interference sources, such as buildings, walls, steel structures, water, deep forest, long distances, short distances with emissions, dead angles, etc. Changing antenna technologies can help transmit or receive optimal signals.
- Start your wireless sensor network with a small trial at the beginning.
- Implement wireless to fulfill your application's needs for today, but design your network so it can be expanded, scaled up or made to accommodate more sophisticated types of data in the future.
- Educate and train field personnel in the skills they'll need to gain the most benefit from your new wireless system, and encourage them to come up with new places where future wireless signals and nodes may be useful.
Mostly Monitoring
To more reliably monitor, diagnose and maintain water equipment and processes at its plant in Calvert, Ky., industrial gas and specialty chemical manufacturer Air Products (www.airproducts.com) recently installed wireless remote monitoring equipment and services from GE Enterprise Solutions (www.ge.com/enterprisesolutions), including sensor and wireless technology, software hosting, alarm notification, application expertise, and installation services. These connect to Air Products' water treatment data and help perform liquid level monitoring of the company's large tank operations, eliminating manual tracking and improving productivity by providing timely information on chemical inventories.
Basically, a submersible level probe sensor from GE Sensing and Inspection Technologies is dropped into each tank to collect measurements. Using GE Digital Energy's wireless MDS technology, the raw data is sent to a Trinity gateway, which serves as the field data collection point for each application. This gateway sends collected data to secure hosting servers managed by GE Fanuc Intelligent Platforms, where it's translated into online diagrams showing liquid levels and consumption rates. In addition, experts from GE Water are on call in the support center to help analyze information, resolve issues and drive continuous optimization for the business.
"This wireless system helps us to be proactive as we monitor chemical tank levels that support our water operations, and we can access it at any time from anywhere," says Bruce Marshall, Air Products' site manager. "Wireless monitoring allows us to check the water treatment systems that support our chemical operations remotely, and the system can automatically alert us when specified process conditions are reached," explains Marshall. "It ensures that we're getting the right information at the right time to aid in our decision-making for our operation."
Familiarity Breeds Creativity
The primary advantage of wireless that's beginning to emerge is that it isn't just a replacement for hardwiring, but is instead a way to gather signals and communication in ways and places that hard wiring could never do.
For instance, to increase production at its steel-recycling mills in Tuscaloosa, Ala., Nucor Corp.'s (www.nucor.com) engineers knew they would need to upgrade its operations and more reliably monitor temperatures around the furnace in areas not previously monitored. The application is a hot-rolled coil and cut-to-length plate mill, which makes carbon and high-strength, low-alloy steels for structural and pressure vessel applications.
In addition, a key requirement for the upgrade was to know instantly what temperatures were in the furnace, which can reach more than 1000 °F, to protect against a production upset if temperatures were to get too high. Another concern was the huge magnetic field that exists around the furnace, a result of running over 120,000 amps to it, and the field's impact on transmitter functionality.
To obtain accurate and reliable temperature readings more quickly in this extreme environment, Nucor's engineers determined they could install Honeywell Process Solutions' (hpsweb.honeywell.com) XYR6000 temperature and pressure transmitters just a few feet from the base of the furnace's flames. The transmitters were installed on the cooling circuits for the furnace, and encased in specially built protective boxes to withstand the extreme heat.
As a result, Nucor reports that its steel-recycling mill was able to increase production by 15%, prepare for future efficiency gains, improve safety with better process status measuring, reduce maintenance requirements compared to using wired transmitters, and provide a foundation to expand wireless across the mill to improve overall process reliability.
New Wireless Paths
Because initial exploration and use of wireless seems to spark unexpected ways to deploy it, this new appreciation of wireless' potential also is inspiring many suppliers to develop and launch novel products to help users make the most of wireless' capabilities in their applications.
Tom Skwara, director of technology at Electrochem Solutions (www.electrochemsolutions.com), a subsidiary of Greatbatch, reports his firm began by specializing in lithium thionyl chloride batteries, more recently got involved in producing wireless sensing, and now helps individual users implement customized wireless solutions.
Electrochem recently helped Rooney Petroleum Services (RPS, www.rpservices.biz) in Riverton, Wyo., to better monitor its gas wellheads by installing its PressureSensorOne (PS1) wireless pressure sensors on RPS' gas wellheads. The PS1s transmit wirelessly to Electrochem's BaseStationOne-U gateway, which is located in the RPS mobile command center.
"PS1 is ideally designed for hazardous oil and gas environments, and each sensor provides multiple readings of various elements. Reporting is configured for up to 20 sensors in the field simultaneously at speeds up to 10 readings per second," says Skwara. He adds that Electrochem's solution helped reduce RPS' operating costs by reducing manual labor by $80,000 to $250,000 each year, and that quality of service has improved by enabling more frequent measurements for users.
Similarly, Opto 22 (www.Opto22.com) has added wireless Ethernet capabilities to its Snap PAC programmable automation controllers and I/O components. "By adding an internal radio and antenna for a wireless local area network (WLAN) to our Snap PAC, we're basically offering wired and wireless at the same time and in the same way that they're available in any laptop PC," says Benson Hougland, Opto 22's marketing VP. "This makes it easy for a user to, for example, set up a quick pilot project in one day to monitor an electrical room for the energy their facility is using, and send that data wherever they want without having to drop in lines."
However, to make sure these and other wireless applications can run securely, Opto 22's "Overcoming Concerns about Wireless PACs and I/O in Industrial Automation" white paper cautions, "Wi-Fi Protected Access (WPA), including the Temporal Key Integrity Protocol (TKIP), replaced the older WEP algorithm in 2003. The more recent WPA2, introduced in 2004, uses the even more secure Advanced Encryption Standard (AES) 802.11i algorithm. WPA2's AES algorithm is compliant with the National Institute of Standards and Technology's (NIST) FIPS 140-2, required by some government agencies and corporations. These standards can protect a robust communication system. For secure communications, WPA2-compliant products should be used for industrial wireless implementations today."
Besides security, wireless devices need power, so Advanced Cerametrics Inc. (ACI, www.advancedcerametrics.com) recently introduced its Harvestor-III power modules that can capture mechanical vibration energy to provide perpetual electric power for microcircuit applications.
Finally, though vibration monitoring is more data intensive than other measurements traveling via wireless, KCF Technologies Inc. (www.kcftech.com) reports that its online vibration monitoring system uses a web-enabled wireless receiver and wireless sensors, which also can be powered by a power-harvesting unit. In fact, three of KCF's wireless vibration sensors were recently installed on each of two 1,200-ton chillers, and they transmit data on an assigned 5-minute to 12-hour schedule. This real-time data allowed KCF's software to perform continuous monitoring, and detect energy transients such as stall and surge. KCF estimates its wireless installation is about 48% less expensive than hardwiring. So what are you waiting for? Start walking the wire...less.
Jim Montague is Control's Executive Editor.
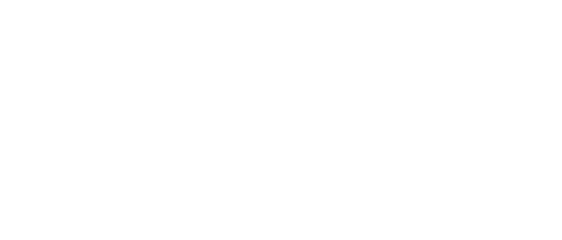
Leaders relevant to this article: