This article was printed in CONTROL's October 2009 edition.
Greg McMillan and Stan Weiner bring their wits and more than 66 years of process control experience to bear on your questions, comments, and problems. Write to them at [email protected].
Stan: A lot of retired engineers may be available for consulting. Some, like me, have found other things more important, such as making sure there is water for southeast Florida, and that the everglades don’t become a parking lot.
Greg: I flunked retirement, so I moved to Austin and started working as consultant in the areas of process modeling and control.
Stan: The lesson here is that if industry wants access to its consultants, it should insure their prospective retirees have no outside interests.
Greg: I don't think companies can make plants as attractive as golf courses or the backwoods, but maybe they can appeal to the strategy to score and the thrill of the chase by adding online performance metrics, so engineers will want to go after the worst loops—or they could let engineers wear golf and hunting garb.
However, this may all be wishful thinking, so let's get back to our discussion with Nick Sands and Bob Cox to see what can be done to make sure expertise is not lost forever. They are two process control engineers in a large, diversified chemical company. Nick works in one of that company's SBUs, and his associate, Bob, is a principal consultant in what may be the best corporate process control group in the chemical industry.
Stan: What role do you see for process design (e.g. steady-state) simulations and dynamic simulations in capturing expertise and educating new people?
Nick: I have not thought of simulations as a method for capturing expertise, though I can see how they could be used that way. There is certainly a lot of knowledge encoded in a simulation. Depending on how it is done, it might be easy or very difficult for someone to extract that knowledge.
Bob: Process dynamic simulation, when set up as a virtual reality process environment, is a great way to teach process operability. If done correctly, students can immerse themselves in the virtual environment, making operational changes or design changes on the fly, and immediately seeing the impact. Our internally developed simulation software is definitely set up to run in this virtual reality mode.
Our simulator developers purposely blur the line between model configuration and model running. For example, you can re-wire a regulatory control system, add process equipment and make other changes, all while the simulation is running. This approach provides rapid feedback to casual modelers of the impact of any changes they make.
Greg: Do you use a dynamic simulator for internal teaching?
Nick: We do have dynamic simulations for our company's process control courses, and frequently use them for operator training. There are also occasions when the simulations have been used for troubleshooting or for running "experiments." I have tested different control strategies using the simulation. It doesn't upset the operators like testing in the plant does.
Bob: Building dynamic models is ingrained into our corporate group. Almost any consulting job we do usually begins by building a dynamic model. This model becomes part of the shared understanding between the consultant and the plant engineers. As part of that model building process, both the plant engineer and the consultant usually learn the key aspects of process operability that will help them complete the task at hand. Any new project, any major process expansion and any major DCS conversion project almost always include an operator training simulator (OTS) based on the model. This OTS allows checkout of the control system configuration before start-up. It also helps the operator learn to navigate the DCS, as well as take the process through unusual process events. The best plants will keep their OTS evergreen, using it to refresh the training of experienced operators, as well as teach new operators.
Stan: Do simulation specialists primarily build and use dynamic models?
Nick: Primarily, the specialists build the simulations, though there are quite a few engineers that build their own. The simulations become more valuable when the technical team can run the simulations, and update them when changes are made to the process.
Bob: Most of our models are built by members of our corporate group (who are process control consultants first and foremost). But, as Nick said, we do have some plant engineers, who build their own models, and many more that can modify existing models. Even more can run existing models, including taking the virtual process through a start-up or some other major event. We aim to make the simulation software usable by the "casual modeler," and give regular courses on model building to plant E&I and process engineers. I feel that the experience of building a model provides the best opportunity to really learn the process. Model validation is always a big concern. But, when plant engineers build a model of a process they know well, they can validate model results quite easily. I would add that for new processes, where a dynamic process model is critical, model validation is more difficult. Here, the skills of an experienced modeler are usually required.
Greg: What books, if any, do young engineers use, or do they rely on the web for all their information?
Nick: We handed out A Guide to the Automation Body of Knowledge in the boot camp. Harold Wade's Regulatory and Advance Regulatory Control has been helpful to new control engineers, as has Advanced Control Unleashed. They are interested in different topics, but we have a lot of book reviews posted to help them find what they are looking for.
Bob: In addition to the control-focused books Nick mentioned, I would note that we are a very "process" centric process control group. So you would also see Page Buckley's Techniques of Process Control, Greg Shinskey's Process Control Systems, and Bill Luyben's Process Modeling Simulation and Control. A few people also use Karl Astrom's, Tom Marlin's, Harmon Ray's and Dale Seborg's process control books.
Stan: People are so busy these days they may not take the time to read reports or books. A more interactive and action-based environment like the virtual plant may be more captivating and ultimately more useful.
Greg: To get more people to learn about process control, I suggest the following:
Top 10 Ways to Make Process Control More Enticing
10. Travel programs focusing on the process control systems of cruise ships.
9. Sci-fi flicks devoted to the process control systems in star ships.
8. Reality shows where teams compete to improve process control performance.
7. Entourage shows where groupies use process control to keep their star from a meltdown.
6. Sport analysis programs, where commentators and listeners talk about dynamics and feed-forward control opportunities in football.
5. Robot movies, where advanced parallel processing robots optimize plants.
4. etective shows where a special investigator with cute obsessive compulsive habits and an incredibly keen mind for details solves mysterious process control problems.
3. "Who done it" novels where the culprit is a bad-acting control valve.
2. Web video with cute animal antics in the foreground and engineers talking about process control opportunities in the background.
1. "Cash for clunkers" programs to replace inefficient old distributed control systems, transmitters and valves.
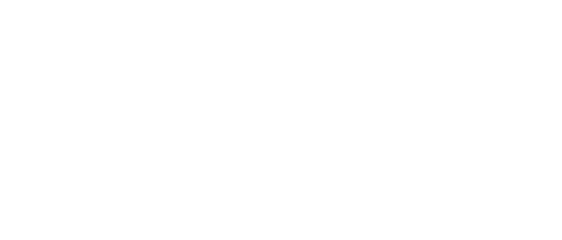
Leaders relevant to this article: