By Dave Harrold
To outsiders, the New Sampling/Sensor Initiative (NeSSI) may look like one of those ideas whose time is never going to come—a good idea that, for whatever reason, never quite catches on. Those closer to its development and its early adopters see things differently. The road to wide NeSSI adoption has been a little rougher than may had hoped, but over time, improvements and new developments have kept alive the hope that it will finally fulfill its potential.
First, a bit of history. Near the end of the 20th Century, analytical measurement engineers recognized that, while advances in computer hardware and software allowed analytical devices to become more capable, more reliable and easier to use, the basic design of sample-handling and delivery systems hadn’t kept pace. Convinced that improvements in sample-handling systems would allow placement of analyzers “at process,” and with sponsorship from the Center for Process Analytical Chemistry (CPAC) at the University of Washington in Seattle, a dedicated group of end users, equipment manufacturers and academies launched NeSSI in 1999.
From its inception, NeSSI’s objective has been to create an open architecture platform on which manufacturers and end users could assemble miniature, modular, intelligent sampling systems that: improve analyzer system performance; reduce design, build and installation costs; and reduce operating and maintenance costs.
Overcoming Surprises
Achieving these goals has proven to be a bit more complicated than first thought. Rick Ales, NeSSI’s secretary and a marketing manager at Swagelok, says, “NeSSI can be thought of as a ‘two-rail concept.’ One rail provides the fluid interface, and the other rail provides the electrical interface. Sample systems that implement the fluid interface (mechanical rail) as defined in ANSI/ISA 76.00.02 are considered NeSSI Generation I systems. Adding the NeSSI bus interface (electrical rail) to a Generation I system creates a Generation II system.”
While progress and success were achieved on the fluid interface (mechanical) portion, NeSSI’s steering committee was surprised when it turned its attention to the bus interface (electrical) portion of its initiative. “When we released Generation II’s specification in 2002,” says Dave Veltkamp, senior research scientist at CPAC, “we thought the steering committee could simply tell people what communications network to use, and that all NeSSI developers would use it. However, once we looked at what was available, we found that nothing met all of NeSSI’s requirements.”
That revelation required the steering committee to take a more pragmatic approach to establishing NeSSI’s bus technology—one that allowed the users and vendors to decide cooperatively what bus communication protocol was best, with the component vendors agreeing to support whatever protocol was eventually chosen.
From the beginning, the Controller Area Network (CAN) bus protocol had been the preferred technology, but CAN bus did not meet the NeSSI Generation II requirement for intrinsic safety. Then, in 2004, two significant milestones were achieved. First, the technical committee for sensor technology of the Instrumentation and Measurement Society sponsored draft standard IEEE P1451.6, producing an intrinsically safe CAN bus solution, which met NeSSI’s intrinsically safe requirements. Second, the NeSSI Generation II spec was modified to include Foundation fieldbus as an acceptable NeSSI bus technology—a definite benefit for new installations, but not so much for existing facilities with cable trays full of 4-20mA wire.
Wiser from this experience, NeSSI’s steering committee turned its attention to how best to achieve interoperability, maintain its open architecture goal, and accommodate existing hardwired facilities.
Interoperability
A key technology used by both 4-20 mA and fieldbus-based instrumentation is Electronic Device Description Language (EDDL). EDDL has been adopted by ANSI/ISA, and is part of the international consensus standards IEC 61804-3 and -4. Therefore, EDDL has a high acceptance rating in the instrumentation and controls industry.
Terry Blevins, of Emerson Process Management and the ISA SP104 committee’s chairperson, says, “The main reason for NeSSI’s interest in EDDL is that it enables manufacturers to describe the features of their sampling systems. Because EDDL is supported by all major control system manufacturers, sampling system manufacturers only need to develop one EDD file, which makes it easy for them and end users. Also, because the EDD file is a text file and is independent of any operating system, the original EDD file can coexist in a control system, even if the sample system manufacturer later updates its product and EDD file with new features. Finally, EDDL enhancements that were added a few years ago and that are reflected in the latest IEC 61804 standards are fully capable of supporting highly complex sample system and ‘at process’ analyzer applications with effective graphic interfaces.”
Another piece of the interoperability puzzle is HART, which is the most recognized and successful deployment of EDDL, with more than 20 million installed HART-based devices worldwide. Developed in the late 1980s, HART is based on the Bell 202 Frequency Shift Keying (FSK) standard that defines how to superimpose low-level digital communication signals on the same wire as 4-20mA analog signals, which satisfies the needs of most hardwired plants to use at-process instrumentation.
In 2007, the HART Communication Foundation released its WirelessHART standard and stated that wired and wireless HART devices can coexist on the same network. Though at press time NeSSI’s steering committee had made no announcement about including EDDL and HART in its Gen II specification, it seems reasonable to think that both of these technologies will play a major role in helping NeSSI achieve its goal of producing cost-effective, open architecture sampling systems.
Cost-Effective
Almost from its beginning, NeSSI’s goal has been to reduce the cost to design and build process analyzer sampling systems by 40% and reduce the cost to own them by 35%. So far, only a handful of end users with NeSSI projects underway have openly shared their results, but those that have done it report some pretty impressive findings. For example, UOP LLC is in petroleum refining, gas processing and petrochemical production, and believes NeSSI’ could produce significant benefits in nuclear magnetic resonance (NMR) solids and liquids, high-temperature calorimetry, specialty micro reactors, and gas absorption.
To validate its beliefs, UOP carefully documented a gas-handling system project using NeSSI technologies and reported significant savings (Table 1).
At the spring 2008 CPAC meeting, Carl Rechsteiner, of Chevron Energy Technology Co. presented a number of eye-opening examples of the benefits provided by at-process analytical measurements.
Rechsteiner’s presentation was based on the premise that current sampling practices tend to minimize the collection frequency and, thus, the number of samples available for analysis—mostly because of limited on-site lab capacity.
Rechsteiner discussed several examples of how using at-process analytical instrumentation could produce significantly larger numbers of data points. However, as we all know, more data seldom equates to more knowledge. The significant point of Rechsteiner’s presentation was that at-process analytical instrumentation can provide the time-stamped data necessary for sophisticated analysis software to produce meaningful knowledge about the quality of the product being produced.
Even though NeSSI specifications remain a work in progress, there is a growing number of end users that see enough benefit in what already exists to move forward.
What’s Next?
From its earliest days, the NeSSI steering committee envisioned that the final version of its work would actually be three specifications:
- Generation I, focused on the mechanical aspects of fluid handling;
- Generation II, focused on connectivity and activities to eliminate manual adjustments and “trips to the field”; and
- Generation III, focused on microanalytics and development of tighter integration between sampling systems and analyzers.
We witnessed the dawning of microanalytics when NASA’s Mars rovers began sending all sorts of data about the planet’s climate, minerals and other elements back to scientists on earth. Essentially, the Mars rovers use microanalytics or “lab-on-a-chip” (LOC) technology designed to integrate several laboratory functions.
LOC technology has several advantages, including:
- Small fluid samples, resulting in less waste, lower reagent costs and easier, less costly sample disposal;
- Faster analysis and response times, resulting from short diffusion distances, faster heating, high surface-to-volume ratios and smaller heat capacities;
- Improved process control and possibly closed-loop control, resulting from faster and more frequent sample updates;
- Low-powered, intrinsically safe electronics, resulting in safer “at-process” solutions.
Technologies generating near-term interest in using microanalytics include process mass spectrometry, including Fourier-transform (FT) mass spectrometry (sometimes called FT-ion-cyclotron-resonance) and nuclear-magnetic-resonance online processing (industrial magnetic resonance).
Even though a growing number of at-process projects are reportedly underway, it’s hardly news that as a group, process industry engineers are ultra-conservative. They remain aware of emerging and new technologies, but when it comes to adopting new technologies they prefer to allow someone else to work out the bugs. Their attitude toward NeSSI adoption has been no exception.
It’s unclear how long it will be until NeSSI achieves all of its goals, but one thing is certain, NeSSI activists are committed to providing end users with miniaturized, modular sample-handling systems that allow safe, cost-effective, efficient, at-process analytical measurements—eventually.
Dave Harrold is co-founder of the AFAB Group and a regular Control contributor.
Control Does NeSSIControl has been covering NeSSI since its inception. The following NeSSI-related articles are available on the www.ControlGlobal.com web site. 2003
2005
2006
2007
2008
|
Other NeSSI-, CAN bus-and EDDL-Related Links
|
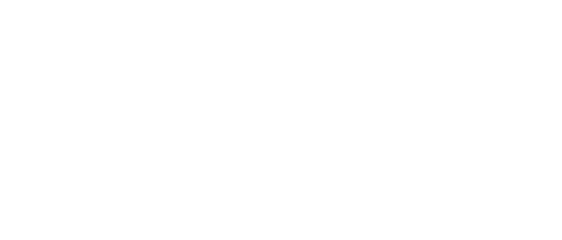
Leaders relevant to this article: