By Neal Hood and Kristi Simmons
The trick to passing a torch is having someone reliable to receive it. That's why users of proven and trusted technologies are often reluctant to try new solutions.
For instance, engineers at Alabama Power (www.alabamapower.com) recently needed to upgrade damper drives on two old, coal-fired, 720-megawatt-capacity units at the James H. Miller Jr. electric generating plant. Located on the Black Warrior River near West Jefferson, Ala., the two units have 25 years or more of service each. However, the original Bailey drives require high maintenance, and parts are becoming increasingly scarce, so this provided the economic justification for replacing 45 damper drives for each boiler.
Coal-Fired Boiler Basics
These sub-critical Babcock & Wilcox balanced-draft drum boilers for the generators burn sub-bituminous western coal to produce steam to the turbines. Seven pulverizers for each unit feed ground coal to the wall-fired furnaces.
Two damper drives control heated and tempering primary air to a common duct. A third damper from the common duct feeds hot air to each pulverizer. A DCS positions these 21 dampers to maintain a target temperature in the pulverizers, and develops the desired level of air flow to transport ground coal to the furnace burners.
Next, secondary air from the two forced-draft (FD) fans runs to the seven windboxes that surround a row of burners. A pulverizer feeds ground coal to each of the seven rows. The DCS positions two dampers on each windbox to provide air for maximum combustion efficiency and clean emissions. It controls induced-draft (ID) fan inlet dampers while fan speeds range between 17% and 24% of maximum. At higher fan speeds, the dampers are full open and the draft is strictly controlled by fan speed. These windbox dampers, plus dampers on the outlets of the FD fans and inlets/outlets of the four ID fans, bring the total of new drives to 45 for each generating unit. The plant plans to add new drives to the two primary air (PA) fans at a later time.
Consequently, torque requirements vary, depending on drive function. All can do continuous modulating with positioning accuracy of 0.1% for optimum process performance.
Smarter Drives Arrive
After a thorough study, the plant's engineers chose Intelligent Contrac electric rotary actuators from ABB Instrumentation (www.abb.com/instrumentation) to replace the Bailey drives. (Elsag Bailey was acquired by ABB in 1999.) The replacement drives have smaller footprints and are relatively simple to retrofit (Figure 1). Replacements went smoothly during planned month-long outages of the two units.
Figure 1: Alabama Power maintenance specialist Neal Hood checks a Contrac rotary electric drive with field-mounted, smart electronics located on the panel.
Plant engineers expect the new drives, which offer more precise and responsive damper positioning, to greatly improve boiler performance and combustion efficiency. In fact, according to Electric Power Research Institute (EPRI) calculations, improving excess O2 control by 0.5% with tighter FD/ID fan damper positioning can result in 0.15% heat rate improvement. For a 500-MW, coal-fired boiler, this can mean fuel savings of $120,000 per year! The replacements also drastically reduced maintenance costs for drives due to their 10-year service interval.Each new drive comes with field-mounted Contrac electronic units and HART protocol communications capability. The processor-controlled electronics unit receives 4-20 mA setpoint signals from the DCS, and feeds back 4-20 mA signals representing actual actuator positions.
Retrofitting the new drives involved changeover at the DCS of the original signal range (-10 to +10 Volts) to the Contrac signal range of 4-20 mA. ABB also provided new linkage between the drives and the dampers. Alabama Power fabricated new mounting plates where necessary.
The electronics unit drives the actuator's highly reliable asynchronous three-phase motor with cage rotor. Using advanced frequency converter technology, the unit can independently vary the torque or travel speed of the intelligent actuators.
The actuator continuously follows the damper drive setpoint signal from the DCS. The stepless motor increases or decreases the torque smoothly and proportionally as the damper drives seeks the desired position. The actuator force and the process counter force maintain a continuously balanced condition.
The electronics unit eliminates the need for torque or limit switches. If the voltage is cut off, the motor is deenergized, and a brake at the motor's rear shaft end holds the damper drive in its latest position. The electronics unit also logs operating, maintenance and service information. It provides predictive diagnostics with advance warning of required maintenance service.
Neal R. Hood is a maintenance specialist and Kristi Simmons is an air and gas engineer at Alabama Power Company.
Evolution of Digital Positioning
In both their electric and pneumatic formats, the recent performance gains of digital positioners is just the latest phase in how they have evolved since microprocessors were added in the early 1990s, later incorporating HART-based 4-20 mA and fieldbus communications. Of course, because earlier analog valves were mostly mechanical and used forced-balance principles, they couldn't get much better than 1% accuracy.
However, not only have digital positioners learned to perform formerly manual calibration and analog-to-digital (A/D) conversion tasks, but they've grown more accurate too. "We've been able to ramp up the A/D converting principle in our latest TZIDC Version 3 pneumatic digital valve positioner to 16000 steps of resolution, which gives it 0.25% accuracy," says Naas DeJager, ABB Measurement's actuator and positioner product manager.
Likewise, better microprocessors and speedier calculations allow TZIDC's users to control valves with auto-tuning and save on installation and commissioning time. For instance, while it takes about 30 minutes to set up an analog drive, it takes 10 minutes to install and commission a digital one.
"Also, once a TZIDC digital positioner is installed, we can use online adaptive tuning to do real-time performance optimization. This means we can readjust and optimize parameters of the positioner itself, which adds up to automatic calibration. No one else does this."
On the electric side, though earlier electrical actuators weren't fast or accurate enough to handle high-demand boiler dampers, DeJager reports that ABB added microprocessors and torque-balance capabilities to its Contrac electronic digital positioners in 1999. "This eliminated the need for torque switches and temperature switches in the actuator, as well as the requirement for over-temperature protection, and any need for end-of-travel motor cut-off," explains DeJager. "All this is possible by using variable-torque technology, which modulates power to the motor to maintain damper position, so the motor is only subjected to the power needed to maintain a steady position. This was a big milestone, and it's still the only technology that works this way."
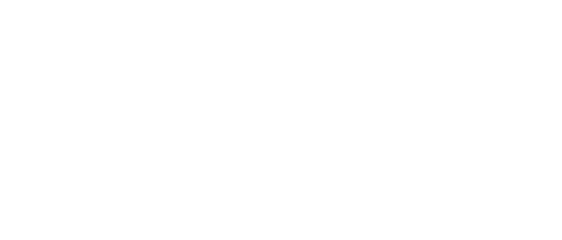
Leaders relevant to this article: