"Electricity is getting expensive," said Thomas Boerrnert, head of heat recovery for ABB Switzerland. "Especially for the cement industry, reducing energy and carbon dioxide footprint is very important. And waste heat is just blowing out the chimney."
This week at ABB Automation and Power in Orlando, Boerrnert showed how much lost waste heat can mean to a cement plant, and how much a typical cement plant can save in electricity cost by recovering energy from waste heat, and using it to generate electricity. "Waste heat recovery," Boerrnert said, "is the most important measure towards low heat losses, and has the highest priority. It is the most efficient way to increase energy efficiency because the efficiency of the heat recovery is high."
ABB has produced an innovative take on an existing methodology, the Organic Rankine Cycle (ORC), which uses an organic liquid that evaporates at a relatively low temperature. Based on a highly modular design, the system "allows maximum flexibility during the planning phase and operation of the plant," Boerrnert said. "The business case is to produce a small-footprint, relatively self-contained and automated power plant that is ‘plug and produce.'"
Phase 1 will produce 1.9 MW (10.5 GWh per year); phase 2 will push that to 2.6 MW (14 GWh per year). "This may not sound like that much, but it is equivalent to the power needed to run 2,000 Swiss homes," Boerrnert said. "We expect to reduce the plant's consumption of externally generated electricity by at least 20%."
Because of its modular design, the ABB ORC heat recovery system can be integrated into nearly all industrial processes, Boerrnert said. ORC technology permits the use of air streams and hot gases with temperatures from 150 °C (typically found in the chemical industry) to 300 °C (typically found in the steel industry).
At Untervaz, the ORC plant's modularity came in very handy. There was no ground space to install the plant, so, because the plant has a low load bearing weight requirement, it was installed on the roof. The system has a bypass design so it doesn't interfere with the process, and it is easy to shut down and restart quickly, just like the cement plant itself.
Water use and water waste are other significant issues in the cement industry, especially for cooling. The ABB ORC heat recovery system uses dry air condensers instead of water, so there is no additional water discharge. The fact that it is a closed system, with hot water and low-evaporation-point organic liquid, both of which are recovered and reused, means the plant will reduce energy use without additional carbon footprint.
When asked, "How is the payback?" Boerrnert replied, "A wise man would answer that question, ‘It depends.'" Typical expenditures are in the tens of millions of dollars, and the payback usually runs between three and six years without taking into account any government subsidies that might be available for energy-use reduction.
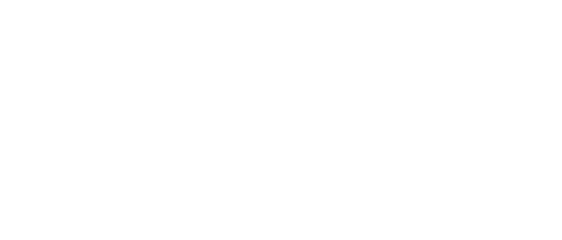
Leaders relevant to this article: