Greg McMillan and Stan Weiner bring their wits and more than 66 years of process control experience to bear on your questions, comments and problems. Write to them at [email protected].
Stan: Things have changed quite a bit from the 1970s and 80s when I did check-out and operator training. For check-out, we often used custom-made boxes for setting analog and discrete inputs. With the advent of the DCS, we got real sophisticated, and used spare controllers to write small models of particularly important and troublesome unit operations. The big breakthrough came in terms of a serial communication from a PC with automatically generated tieback models and some custom models with a serial interface to the DCS or PLC I/O. At Monsanto, it became a practice that all projects would use models and the serial I/O interface for configuration development and check-out, system acceptance testing and operator training systems. Then came the virtual plant, and the window to the future opened.
Greg: I've been writing about the use and application of the virtual plant—a dynamic process simulator integrated with a control system simulator—for years. Mynah Technologies is a staunch promoter of the virtual plant, delivering these solutions for customers all over the world. I recently caught up to Mynah's president, Mart Berutti, to get an update on trends in the use and application of the virtual plant.
Stan: What level of interest is there in the virtual plant in the process industries?
Mart: It's very high, mostly due to the incredible pressure the industry is under due to the upcoming shortages of plant operators. The U.S. Department of Labor says the average age of energy industry workers is over 50, and half the current work force (more than 500,000) is expected to retire over the next five to 10 years. As these workers leave industry, they will take with them an irreplaceable amount of knowledge and experience.
While older operators operated based upon mechanical skills and experience, younger employees, in general, have fewer mechanical and more computer skills. The old days of operators who knew if a compressor was performing well from the sound it made are coming to an end.
The need to have a method to train operators in a safe and effective manner is greater than ever before. In addition, a study published in Oil and Gas Journal in December 2001 said that it takes, on average, seven years for new workers to achieve a level of competence that permits them to make or recommend appropriate risk decisions. This seven-year figure is in direct conflict with the average worker's typical tenure expectation, which is five years in one position. This means that in many process plants, the operations staff are looking for their next positions before they really achieve competency in their current roles.
Greg: Can't they just address the operator shortage issue with more and better automation?
Mart: Modern automation technology provides excellent return on investment, and can be used to operate process plants with fewer qualified operators. In general, highly automated plants have less operations-related errors. Modern control systems are very advanced, and can handle many tasks quicker, more safely and at a lower cost than a human operator. Advances in automation system and process technology allow process plants to operate longer without downtime.
However, in a highly automated plant, the role of the operator is different and more difficult. Operators in these plants have to monitor a sophisticated system and make decisions about the health of the process and the performance of the system based upon trends and meta-information (information about information). In many cases instead of actively doing something, they have to review the information presented and make a decision about whether to do something or nothing at all. Also, because the system and process are more reliable, operators may seldom or never see upset conditions, and can quickly lose critical skills necessary to deal with those situations. This often results in compromised operating conditions. Studies show that the greatest cause of operational loss in the process industries is due to operator error. The need for a virtual plant is even greater in a highly automated process plant.
Stan: So, is the virtual plant only an operator training tool?
Mart: Not necessarily. The virtual plant is also an effective tool to reduce the risks in automation projects. While modern, field-based automation systems have great reliability and performance, the risk introduced by human engineering still remains. The risks may include hidden errors and issues in the automation system application software undetected until they cause process or operational issues.
Advanced control strategies that are not fully vetted can have affect plant operations adversely. In many plants, the operating procedures are in error or incomplete, so they are not used or trusted. At the same time, government bodies are putting pressure on process plants to document their efforts in administering a safe and effective operations environment. The OSHA National Emphasis Program, for example, often requires in-depth review of operating procedures, tag-naming conventions, management of change and/or automation system documentation. Process plants that do not test the control system implementation and operating procedures using the virtual plant have to address these issues during start-up or system commissioning. potentially endangering the process or operations staff by not addressing these risks in a safe environment. If they don't have a properly documented approach to dealing with these areas of risk, they expose themselves to OSHA violations or increased oversight.
Greg: Is there a right approach for implementing the virtual plant?
Mart: Properly using dynamic simulation for control system testing and operator training gives excellent business results. We use the term virtual plant to describe a replica of the control system with a dynamic simulation of the process and field automation system.
The right approach would start with the selection of a virtual control system that provides an exact replica of the real control system. This allows testing of the identical control strategies running in the actual process controllers with a virtual I/O system. It allows operator training on graphics, alarms and controls that are identical to the actual plant HMI.
In addition, a virtual process and I/O dynamic simulation system should be used. The system should be complementary to the virtual control system, providing real-time I/O and model updates so that the virtual control system appears to be controlling the real process. The dynamic simulation should allow the user to develop process models to the level of complexity or fidelity required by the task at hand. The system needs to be easy to use and change so that modeling changes can be made quickly and efficiently.
The simulation system must be built to support both control system testing and operator training, so that it can be used through the entire project schedule, providing the greatest benefit to the system user. Ideally, the virtual plant will be available for plant operations as a strategic asset to improve the quality of control system enhancements and increase the effectiveness of plant operators.
Greg: Next month we'll continue our discussion of the virtual plant and its uses, including the answer to Stan's question about using virtual plants for knowledge capture and transfer. Meanwhile, here are my top 10 reasons for using a virtual plant.
Top 10 Reasons I Use a Virtual Plant
10. You can't freeze, restore and replay an actual plant batch
9. No separate programs to learn, install, interface and support
8. No waiting on lab analysis
7. No raw materials
6. No environmental waste
5. You get to deal with virtual instead of actual problems
4. Bioreactor batches are done in 14 minutes instead of 14 days
3. The plant can be operated on a tropical beach
2. Last time I checked my wallet, I didn't have $100,000
1. The actual plant doesn't fit in my suitcase.
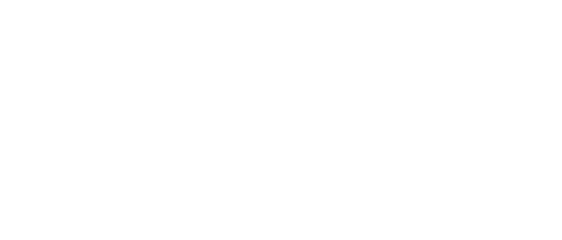
Leaders relevant to this article: