By Luther Kemp
Burning biomass with other fuels such as coal requires a multi-fuel boiler. Operating a multi-fuel boiler can be difficult, particularly in cogeneration (cogen) applications with varying steam demands. Biomass fuel availability is variable and subject to frequent interruption, and Btu content of the fuel varies significantly and quickly. Process steam loads fluctuate, sometimes suddenly. Controlling a multi-fuel boiler in a cogen application is several orders of magnitude more difficult than running a unit with a single fossil fuel.
A highly skilled operator can operate such a facility by watching video cameras focused on the bed and flame and by observing the on-screen outputs of steam flow, pressure, temperature and excess oxygen sensors, along with other process variables.
He or she continuously tweaks the boiler control setpoints in response to changes in the combustion process and other process variables. At times, it's as challenging as driving a car through a snowstorm, and it always requires constant attention. While Minnesota Power has highly skilled operators, this semi-manual mode of operation isn't the optimal way to run a major power and steam-generating unit.
Updating Controls in Duluth
Our M.L. Hibbard Renewable Energy Center power plant in Duluth, Minn., (Figure 1) has a multi-fuel traveling grate boiler that burns both wood waste and coal. The boiler generates steam that feeds two condensing turbines that provide power to the grid and supply steam to the New Page Paper Mill. The plant is working to be able to burn 665,000 tons of biomass per year and 13,000 tons of coal to produce 3,600,000 klb of steam to generate 220,000 mWh of power and supply process steam to the New Page Paper Mill.
Figure 1: The M.L. Hibbard Renewable Energy Center power plant in Duluth, Minnesota has a multi-fuel, traveling-grate boiler that burns both wood waste and coal. The problem was that it operated almost all the time on manual controls.
The boilers, when owned by the City of Duluth, were primarily used for steam generation for the paper mill and generated electricity only when excess steam was available. Over time, ownership of the boilers was transferred to Minnesota Power, and legislation was enacted that mandated power facilities generate a substantial amount of their power from renewable sources.
We wanted the facility to maximize generation while maintaining the load to the paper mill and to do so in an optimal fashion under automatic control. Although it was a multi-fuel plant, the control system as it was implemented wouldn't support substantially increasing the amount of biofuel without excessive intervention and attention from our operators. It also wouldn't permit us to prioritize the amount of power generated from the plant.
Although the overall plant was controlled by a modern Emerson Process Management DeltaV control system (www.emersonprocess.com/), much of the plant had older control equipment with limited capability. The two boilers were converted to burn wood residue and coal in 1986 and 1987 and have been running virtually unchanged ever since.
Manual intervention by our operators was often required as steam demand varied, as fuel quality varied, and as other conditions changed. The excess oxygen control was inoperative, and at times we had to manage process swings using natural gas as a supplemental fuel because the control system couldn't react fast enough with coal or wood fuel. Boiler warm-up was a cumbersome process that required multiple operators, and the variability between operating shifts was excessive.
In 2010, we decided to upgrade the boiler and its controls. We were planning to burn more wood waste to meet increasing regulatory requirements, and we had to supply steam to the New Page paper mill. The New Page mill would consume about 40% of the steam produced,
As is typical when supplying utilities to an industrial process, we have no control over demand. The mill can increase or decrease its steam demand nearly instantaneously by wide margins, thereby upsetting boiler and steam turbine operations.
Another concern was related to biomass regulations. At the time we began the upgrade project, we did not know what the U.S. Environmental Protection Agency (EPA) or the State of Minnesota would eventually pass in terms of legislation regulating the use of alternate fuels. Therefore, the control system would have to accommodate virtually any mix of wood and coal fuel.
These new developments meant we could no longer count on controlling the boiler with frequent manual intervention. We wanted to achieve maximum steam production from wood, savings in emissions and faster response to upsets. We also wanted to reduce operational problems such excessive ash carryover that was causing a need for frequent boiler cleaning.
The solution was twofold. First, we addressed boiler process issues by installing a new overfire air (OFA) system from Jansen Combustion and Boiler Technologies (www.jansenboiler.com). Jansen's retrofit included new OFA ports, a new duct design with improved measurement locations and new damper actuators with position feedback. The OFA system (Figure 2) improves air delivery to the boiler by getting air to where it is needed for biomass burning and creating a turbulent mixing zone to allow complete burnout.
Second, we improved the controls by upgrading the software configuration in the Emerson DeltaV control system. Essentially, we used mathematical and model predictive tools to do what our best operators were doing, but with added speed, precision and repeatability.
Analyzing the Control Problem
Before embarking on a major change to the boiler control strategy, it was important to first understand the dynamics of the new OFA system and the other mechanical modifications we made to the boiler. We wanted a holistic control system that included an integrated solution of hardware and software.
Jansen's engineers had already done an extensive study of the air/fuel requirements when designing the OFA system and the ductwork, so we had an excellent foundation from which to start.
We retained Emerson Process Management to do a survey of our boiler and new air system. Emerson has engineers that specialize in industrial powerhouse controls and multi-fuel boilers. The Emerson consultants worked with Jansen and Minnesota Power engineers to analyze the process performance and make recommendations.
From the survey, Emerson identified the need for a combustion control strategy specifically designed to address the challenges of biomass burning. Control functionality was needed to automatically handle variable Btu in real time, chase load swings with wood fuel primarily and prioritize wood use in general while operating within all constraints.
The decision was made to implement Emerson's SmartProcess Boiler solution for multi-fuel boilers. This control strategy would leverage the model predictive control (MPC) tools called Predict-Pro within the DeltaV control system, and provide full-automatic wood-burning optimization. No changes would be needed in the DeltaV hardware for boiler control.
Simulating the System
After the engineering survey was completed, Emerson was engaged to configure a SmartProcess Boiler implementation for our boiler. This provides a Btu-based combustion control strategy that eliminates the traditional air-to-fuel curves and allows use of variable fuels such as wood to be improved.
The Btu from wood that is available for combustion is mathematically derived in real time by the control strategy. With this, adjustments to operation of the boiler can be made automatically by the controls to compensate for wood-fuel quality variations and wood supply changes or interruptions. The control strategy will automatically make air adjustments or pick up coal when needed to maintain stable operation.
In accomplishing Btu-based control, the SmartProcess Boiler configuration also makes use of PredictPro. Having advanced control functionality in the DeltaV allowed the boiler optimization to be implemented right at the controller level to simplify training and maintenance.
DeltaV also has a simulation environment, which allowed us to test our new advanced control strategies 100 times faster than real time. We set up our control model on a DeltaV system at the local Emerson representative, Novaspect Inc. (www.novaspect.com) in Grand Rapids, Minn..
SmartProcess Boiler allowed us to set up various control scenarios, including firing mostly biomass, firing all coal, firing mixtures of biomass and coal, and changing economic scenarios based on the price of coal or biomass. Although the cost of biomass and coal is usually similar, prices can vary, and sometimes coal becomes an economically attractive fuel, but using too much coal carries high emissions costs. All of these factors enter into the advanced control calculations.
We could also simulate changing process conditions, such as swings in steam demand from the paper mills and varying ambient temperatures. For example, when the temperature drops to -40 ºF in the winter, the paper mills obviously use much more steam than in the summer.
Operators were naturally quite wary of transferring control to a fully automated system. But running test simulations prior to start-up convinced them that the system was indeed capable of automatic control through all manner of changes in steam demand, fuel quality and other factors.
The simulations showed that the new control system—theoretically, of course—was capable of handling process upsets, reducing emissions, reducing ash carryover, starting up the boiler automatically and adjusting for the varying Btu content of wood. The acid test would occur when we installed the system and ran it on the actual boiler.
Installation and Start-Up
Installation of the Predict-Pro and SmartProcess Boiler optimization solution into the boiler's existing DeltaV control system was simple—we just unlocked the advanced control license and downloaded the control configuration program that had been developed and tested.
The system came on line, we discovered a few glitches, did some tuning of the control algorithms, and everything was up and running within a few days.
The control system now operates the air systems in cascade mode; that is, air flow adjusts automatically according to demand and fuel conditions, and under-grate air is now used to improve the unit's speed of response to load swings. Fuel control remains in cascade mode, and fuel is controlled according to cost priorities.
The Jansen OFA system is leveraged by the DeltaV SmartProcess Boiler controls to deliver proper air placement for optimized combustion throughout the entire load range, and boiler start-up is also automated.
The upgrades have yielded a boiler process that operates more efficiently and with less required operator intervention, all while remaining in strict compliance with all regulations and process constraints. As with any process, more efficient and automatic operation will result in less required maintenance and lower overall lifecycle costs.
Because of the success of the project, a similar system is being developed to control the second boiler in Duluth.
More Projects
The Duluth project began in the summer of 2010, and progress was so encouraging that Minnesota Power decided to begin a similar project in May 2010 at the Rapids Energy Center (REC) in Grand Rapids, Minn., to improve controls of the steam header (Figure 3).
Figure 3: A similar control system update was performed at the Rapids Energy Center (REC) in Grand Rapids, Minnesota
REC provides steam, air and electrical power to the nearby Blandin paper mill—and the mill supplies 300 tons of wood waste daily to the power plant. At REC, steam is the main product and power to the grid is a byproduct.
Like Duluth, the Grand Rapids plant had older technology, some of which was piecemealed together, and its operation required frequent manual intervention by our operators. The mill's steam demand varied widely, making control of the steam header very difficult.
Another issue with the plant operating routine was that a sudden drop in steam demand from the paper mill was often met by diverting steam to the atmosphere. A main goal of any upgrades would be to divert this excess steam to the condensing turbines in order to generate the maximum amount of power at all times.
Reliable and efficient operation of the steam header was dependent upon the skill of the operator, and efficiency varied from operator to operator. Our goal was to automate control of the steam header, to deliver as much steam as possible to the turbines in order to generate as much power as possible, and allow for the operators to focus on the cause of the header upset versus reacting to the problem.
In the fall of 2010, the project team began testing to ensure that the steam system transmitters and valves were working properly. We worked with Novaspect, the local Emerson representative, to inspect and test the field devices and to address issues that were found. We then implemented Emerson's Predict-Pro and SmartProcess Header solution on the DeltaV process automation system.
We set up the software solution on a DeltaV system at Novaspect's offices in Grand Rapids, configured Predict-Pro and SmartProcess Header to represent our boiler and steam header situation, and ran simulations. We trained four operators on the simulator, and they accepted the new system quickly.
We installed the header optimization solution on the REC DeltaV system in April 2011, started it up, did some tuning, and it's been running near perfectly ever since.
Prior to the SmartProcess Header, two of our pressure relief valves (PRVs) were regularly open more than 50%. Now the PRVs open only during turbine outages. This increased flow through the turbines allows an increase in electrical power generation, which will contribute to an estimated one year payback. The biggest gain is an easy-to-use header control package that will help our new work force tremendously as our experienced operators retire in the next five years.
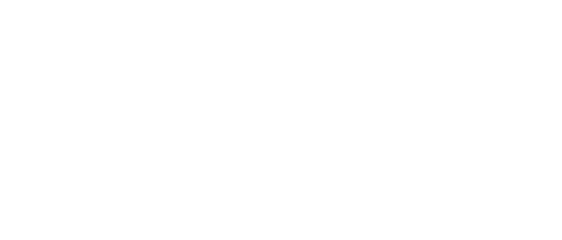
Leaders relevant to this article: