By Dick Caro
In the article, "Eliminating the Control Valve," I reminded control systems engineers that the electronic variable frequency drive (VFD) was an alternative to the control valve as the final control element in liquid flow control applications (Figure 1). Not only is this application less complicated than the more conventional use of a control valve, but it is also widely known to save energy.
Some control engineers have known this for many years, but have been reluctant to specify use of the VFD chiefly because they're unfamiliar with it. The primary incentive to use a VFD for flow control has been energy savings by elimination of the need to pump liquid to a high pressure, only to waste that pressure as energy loss through the control valve. Using a VFD to drive the pump motor allows the use of the pump speed rather than control valve plug position as the controlled variable.
Not only is there a significant potential operating cost saving by elimination of the pressure drop across the control valve, but also there is a strong potential to gain operating efficiency by virtue of improved process control. Improved control would result from elimination of the hysteresis of control valves that we call "stickiness," which often requires control loops to be de-tuned from optimal tuning settings. Another factor is the speed of response of modern VFDs in changing flow in response to the controller's output signal; control valves move slowly at mechanical speeds, while the VFD changes speed almost instantly. Faster response and elimination of hysteresis/dead time typically lead to reduced process variability that allows setpoints to be set closer to optimal conditions, thereby improving control loop performance. Optimal setpoints are necessary to improve process performance to gain such benefits as improved yield, reduced waste and more consistent product purity.
Support and Skepticism
As expected, response to Part 1 varied from complete support to outright skepticism. In that article, I asked for people who have tried closed-loop process control using a VFD driving the electric motor powering a centrifugal pump for liquid flow control to share their experience. The energy savings are so well-documented that there was no doubt. However, a few respondents did wonder whether the magnitude of the energy savings might not be enough to justify conversion of a working flow loop to actually remove the control valve. In one case, I suggested that the control valve may not need to be removed if a bypass was already present, which is normal for most petroleum refining and petrochemical processes. This was mentioned as a temporary means to test the quality of control, but elimination of all piping pressure drops is necessary to maximize the potential energy savings.
The Pump Affinity Laws
I continue to be amazed that control engineers are still confused by the pump affinity laws that show flow rate through a centrifugal pump is directly proportional to pump speed. In other words, changing pump speed causes a proportional change in flow rate. A few correspondents argued that since the head changes at different flow rates due to pipe friction, a real installation could not be exactly linear. However, the controlled variable—flow rate—is linear. The uncontrolled variable that changes in a non-linear way is power consumption. The pump affinity laws say that the power consumption will vary by the ratio of the speeds cubed. In fact, this is the very reason that substituting a VFD for the control valve saves so much energy.
Several respondents have told me that they routinely design their processes with VFDs for very large flows, such as for cooling water circulation or in wastewater aeration. However, it has not been documented that these applications are ever used to control the liquid flow rate. They have the capability to manually change the flow rates in response to plant needs, but generally there is no flow controller.
At one petroleum refinery, my contact reported that his group tried installation of VFD and actually used it to control pump speed manually, but the operations department would not let the control valve be removed "just in case the VFD failed." In several years of operation, the VFD has not failed, but the bypassed control valve remains in place.
More than one respondent suggested that the VFD may not be reliable enough for use as a process final control element. As we spoke, it became apparent that their previous attempts used a VFD produced in the early 1990s. These VFDs were probably based on use of GTO (Gate Turn Off) thyristor technology, or were among the first VFDs using IGBTs (Insulated Gate Bipolar Transistors) that replaced GTO thyristors. GTO thyristors and early IGBTs were not very reliable. Improvements in IGBT technology have been remarkable, but these are high-power devices. Modern drive design uses several IGBTs in parallel to achieve both peak power capacity and reliability through resiliency, thereby keeping the mean time between failures (MTBF) low. Maintenance improvements on modern drives alarm on IGBT failure and allow rapid on-line replacement to keep the mean time to repair (MTTR) low. This compares well with the operation of sticky control valves that require extensive repair time, but allow the process to continue operation with suboptimal tuning.
The water and waste treatment industry is the only one that routinely uses the VFD as a final control element for new installations. The very large sizes of pumps used in water and waste often means using very large control valves. New installations have saved considerable capital cost by installing VFD-driven centrifugal pumps with the motor speed tied to the flow controller output. Not only do these save capital by avoiding expensive very large control valves, but the pumps are also smaller, since they no longer need to generate the head loss that would have been necessary to provide the pressure drop across the control valve. On the other hand, control accuracy and process optimization is not often an issue in water and waste applications.
In each case where the VFD was actually connected to the loop controller, the interface used was the 4-20 mA speed input option offered on most VFDs. The VFDs are also available with Ethernet network interfaces that often support one of the high-level protocols, such as Modbus/TCP, EtherNet/IP or Profinet, in which the speed setpoint attribute can be changed. However, no drives are currently available with either an OPC server or Foundation fieldbus interface. Additionally, while most VFDs offer a PID algorithm and ramping function blocks, none of the companies using VFD as final control elements have taken advantage of these capabilities.
Similar to the way that control valves can be eliminated, large dampers installed in fossil-fuel-powered boilers also can be eliminated by using a VFD to drive the fan motors on forced draft power boilers. The primary control of power boilers for the generation of steam is the fuel flow rate. The fuel/air ratio controller, which usually positions the dampers to control the ratio is slaved to that fuel flow. Elimination of the dampers would save capital expense on new installations, reduce the cost of power by elimination of the pressure drop across the dampers, and possibly increase the capacity of the boiler by using the increased forced air fan capacity to operate at higher fuel flows.
Continued Research
In the time since Part 1 was published, new information has become available on the VFD topic. A manufacturer of industrial wiring says that it is necessary to shield electrical cables and to use electrical cables that have been designed for use with VFDs. (Shuman, "Choosing the Right Cable for your Variable Frequency Drive (VFD) System," www.belden.com/pdfs/techpprs/VFD_Choosing_WP.pdf, Belden, Inc.) Failure to install the right cables can lead to many of the problems that have been attributed to the use of VFDs in the past. The problems of electric motor failure due to harmonics and excessive electrical noise are often the result of replacing a motor starter or motor control center (MCC) with a VFD and reusing the existing power wiring. When installing a VFD to replace a motor starter or MCC, new wiring must also be installed.
The readers of Control and Motors and Drives magazines have responded to a survey related to the use of VFDs as final control elements replacing control valves. The results have been remarkably consistent with the informal interviews I have previously conducted with process control end users. In general, process control engineers are unaware that they can use a VFD driving the process pump to replace a control valve.
One strategy that might encourage end users to adopt the VFD more readily is if drive suppliers were imitate control valve/positioner suppliers, and offer fieldbus instrumentation users function blocks configured in the same way as control valve/positioner suppliers do. The trend in most new large petrochemical plants and petroleum refineries is the use of Foundation fieldbus instrumentation that is usually configured with the final control function block (PID) physically located in the control valve positioner.
At this time, none of the drive suppliers offers a Foundation fieldbus interface, either H1 or HSE, or conforming function blocks.
If drive suppliers were to offer Foundation fieldbus function blocks in their drives, as well as a suitable Foundation fieldbus interface, the use of VFDs could be more comparable to control valves.
Summary
In these articles, I have demonstrated that there is a distinct economic advantage to using a VFD on the electric motor turning a centrifugal pump in place of a constant-speed electric motor turning the centrifugal pump with the control valve/positioner combination for liquid flow loops. The resulting energy savings is quite large, but the potential savings in improved process control from improved yield, lower waste and more consistent product purity realized by operation closer to the optimal setpoint may actually be even larger. Failure to take advantage of the benefits of using the VFD and eliminating control valves when feasible is usually traceable to the lack of information and support from the suppliers of VFDs and to a lack of education on the place of the VFD in process control technology.
Dick Caro is a principal at CMC Associates, Acton, Mass.
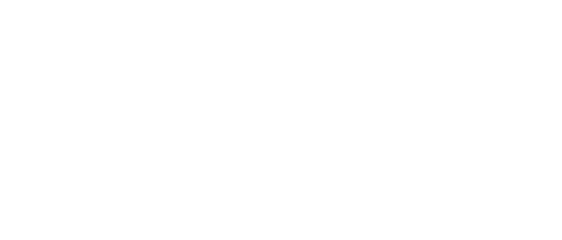
Leaders relevant to this article: