By Monte Smith
United Canadian Malt Ltd. (UCML) is Canada's largest manufacturer of a wide variety of liquid and dry, diastatic and non-diastatic extracts of malted barley, wheat, oats and rice. Our company was founded in Peterborough, Ontario in 1929, and since then has been a major international supplier of premier malt extracts and sweeteners for the food, pharmaceutical and brewing industries. Our customer base is extremely diverse, as customers use our ingredients in everything from cereal, bread, biscuits and pastries to chocolate, pet food, vinegar, chewing gum, ice cream, and, of course, beer.
Malt extract is a vacuum-concentrated sweetener made from high-quality malted barley. United Canadian Malt manufactures approximately 300 different liquid extracts using a variety of grains and process parameters to produce these natural, viscous sweeteners. In the food industry, extracts are used in a variety of baked goods, as the fermentation process assistance improves structure, color and crust appearance. The additional advantage is malt extract's ability to enhance these foods naturally with a unique, subtle and desirable flavor.
UCML is a certified organic production facility offering liquid extracts and syrups made from a range of organically certified grains. In the pharmaceutical industry, the distinct flavor of both liquid and dried malt extracts is an effective vehicle for active substance administration. With its broad nourishment characteristics, malt offers an improvement over plain sugar syrups.
At our facility, the main ingredient, malted barley, is stored in two outdoor silos. From them, it is drawn, crushed and then blended with water to yield a slurry called "mash." Precise quality control on temperature, time and specific water quantity allows the release of nutritional components from the grain. During this process, the natural enzymes inherent in the malted barley convert the grain starches and proteins to soluble and digestible sweeteners and protein components. The resultant fluid, called "sweet wort," is separated by filtration from the spent grains. The wort is then concentrated by evaporation to produce a viscous malt extract consisting of 80% solids material.
Challenge
Brewing production scheduling requires an accurate assessment of our primary ingredient—the malted barley, which is stored in UCML's two 15-m (49.2-ft) steel silos. To do so, we need a very reliable, accurate and robust system to provide constant grain level information from our silos.
Figure 2. Sitrans LR460 (in background) and Sitrans LR560 (in foreground) are measuring the level of malted barley at UCML. The compact size of Sitrans LR560 makes it easy to carry to the top of the silo.
Our previous weight and cable level measurement system and rotary paddle switches resulted in ongoing maintenance and reliability issues. Imagine removing caked-on grain dust from an inoperative spindle wheel atop a 15-m (49.2-ft) silo during a June rainstorm. Or better yet, reseating the control rope and winding motor in January's frigid and icy weather.
[javascriptSnippet]
When the electronics of the weight and cable system failed, we temporarily used a manual level control system. Time and safety issues were substantial cost and efficiency factors, however, as workers had to climb the silo, open the hatch and check levels with a flashlight. And, really, just how accurate is that flashlight level check? Truthfully, the only benefit from all of this climbing to the top of the silos was the positive effect on the manager's heart rate and his fresh air exposure!All of this took place at UCML with malted barley grain arriving by rail car or truck every few days. Grain delivery was always a control headache, as the silo's capacity is much less than the more than 70 metric tons (MT) on a rail car. With the variable delivery schedules and the expense of rail car unloading demurrage time, it is crucial to have constantly accurate inventory level measurement. Precise inventory monitoring ensures that unloading from rail cars or trucks takes place within the allotted days, and without exceeding the silos' capacity, since cleanup of spilled grain on surrounding streets is not easy. We also wanted the ability to coordinate the brewing usage of the grain discharged from the silos without shutting down production, as this would save both time and money.
UCML investigated several options for reporting silo grain levels. Load cells, a very accurate method, were too expensive to retrofit onto our existing silos. Repairing our weight and cable system's electronics was also quite costly, considering its mechanical problems. An ideal system would have mechanically and electronically reliable construction, and would be accurate over the full length of the silo—especially the bottom cone discharge section. Such a solution would also have a remote readout capability at some distance from the silo and capability for a high- and low-level alarm shut-off option. Finally, it must be able to handle the grain silo's intense dust level during the filling cycle.
Solution
United Canadian Malt was already familiar with Siemens Industry's level measurement transmitters in its manufacturing process. UCML had previously installed a Sitrans LG200 guided wave radar transmitter on a wort tank. Wort is a challenging substance to measure because of high temperatures and excessive steam and foam that are generated during the wort transfer process. The tank also requires a weekly chemical sanitation bath and a high-pressure water washdown, and there is little headroom, complicating the installation of any instrumentation.
The installed Sitrans LG200 operates with a flexible, single cable probe with a sanitary tri-clamp fitting. The transmitter is connected to a remote display at the operator's station to enable convenient remote monitoring. The LG200 performs consistently and accurately, despite at times working through a meter of foam and its accompanying sticky residue. This unit has done so for several years, which imparts a great deal of confidence in the reliability of Siemens' instruments, both from our production and maintenance operators' standpoints.
UCML's first silo level control monitoring device was a Sitrans LR460 installed on the first of our two outdoor silos. It is connected to a remote display inside the building. Sitrans LR460 is a non-contacting, 25-GHz frequency-modulated continuous wave (FMCW) radar level transmitter, and it uses a four-wire connection (two for 115 VAC power supply and two for the mA output). After some fine-tuning of the signal, Sitrans LR460 provided reliable operation.
The Sitrans LR460 uses a 4-in. horn antenna with an 8° beam angle. Due to the center location of the Sitrans LR460, the transmitter was detecting the seams of the silo, which were tuned out via the process intelligence feature called "Auto-False-Echo-Suppression." This process required the silo to be near empty. Once configured, Sitrans LR460 provided acceptable readings, except for the lower cone area.
Figure 3. Sitrans LR560 has plug-and-play performance because of the 4° narrow beam and 78 GHz. Alternatively, the 8° wider beam of the Sitrans LR460, requires fine-tuning to find the correct echo profile.
With the success of the both the Sitrans LG200 and the Sitrans LR460 in mind, United Canadian Malt selected the new Sitrans LR560 for a solution for level measurement of the second silo. The stainless-steel housing was readily adaptable to UCML's preferred way of installation on our silo inspection hatch, and its compact size made it easy to carry the transmitter to the top of the silo for the installation. From our electrician's point of view, the unit's two-wire configuration was also instrumental in saving installation work and wiring costs.
Sitrans LR560 uses a high frequency of 78 GHz and a unique lens antenna to provide a narrow 4° beam. The local display interface has an easy-to-use, graphical Quick Start Wizard that allowed operators to set up the Sitrans LR560 in a couple of minutes using the display pushbuttons. The extreme narrow beam of Sitrans LR560 provides plug-and-play performance, and no additional fine-tuning was required. The seams of the inside of the silo did not interfere with the level readings, and reliable readings are provided all the way to the bottom of the cone area.
Sitrans LR560 is available with HART, Profibus PA or Foundation fieldbus protocols. Programming can be performed remotely with Simatic PDM (process device manager), AMS or PACTware with Siemens' DTM. The local display interface features a backlit display, and can be rotated in four positions. An integrated purge connection is readily available for self-cleaning of the antenna lens if the solids material is exceptionally sticky.The 78-GHz frequency creates a very short wavelength that provides exceptional reflection from sloped surfaces and aiming is rarely necessary. An optional aiming flange is available to aim the antenna away from obstructions or towards the center of the discharge cone for reliable readings in the cone area.
Benefits
Since the Sitrans LR560 was installed, UCML's operators have noticed very stable readings from the transmitter, from completely empty to full. During filling, our operators simply keep an eye on the remote display, monitor the filling cycle and then shut the transfer system off if the level approaches the top of the silo. There has been zero maintenance on the Sitrans LR560 since its installation, and no maintenance is expected.
UCML's silo cleaning schedules have also benefitted from the Sitrans LR560's compact design. Its low profile and lack of extended horn have meant a significantly easier—and safer—cleaning process for the two workers who are on top of the silo performing the required operation. The yearly maintenance cost associated with the previous mechanical level system has been eliminated. In fact, the cost of the new equipment was paid back well within the first year of its operation.
Overall, as the general manager at United Canadian Malt, I am very happy with all of the instruments we're using from Siemens Industry. We have acceptable performance from the Sitrans LR460, and we were very surprised with the small size of the Sitrans LR560 and how much easier it was to install, set up and operate. Our operators know what is going on throughout our process, and we no longer have any overfilled silos or inaccurate readings from old technology.
Monte Smith is general manager at United Canadian Malt Ltd.
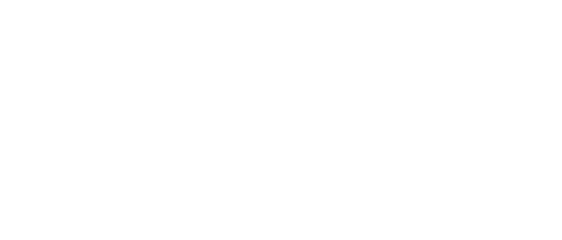
Leaders relevant to this article: