"This is something I've been preaching for 25 years," says Dan Miklovic, principal analyst at Lean Manufacturing Research, St. Louis, Mo. "If equipment starts to wear out, it's much harder to maintain the quality of the product. You use more energy and raw materials as you try to maintain the equipment. The best way to reduce energy, optimize production and minimize waste is good maintenance practice."
It's Complicated
One of the problems is that "asset management" is a nebulous term itself, and, as George Buckbee, vice president at ExperTune (www.expertune.com) says, "Customers don't want to hear about 'optimization.' It's overused. And 'sustainability' is like mom and apple pie—everybody says they want it, but what does that mean?" But, once the numbers reflected in ROI start showing up, investment in good asset management that can be leveraged into energy savings and sustainability efforts, their connection becomes clearer.
"Everybody thinks sustainability is a new fad," says John Benders, vice president, asset intensive industry solutions at Mincom (www.mincom.com), which was acquired by ABB in June of this year. "The real reason organizations are doing this [upgrading asset management systems] is that it saves them money. The push to sustainability drives them to look at asset management more closely. It's more cost-effective to do stuff when it's not broken."
Where do you start on such a journey? Dan Miklovic says many companies do it on a project-by-project basis. They start with a single project and look at the gains achieved. "Start with CMMS, then a low-cost EAM system, and, ultimately, push to the limit. You get there over time," he says. "If you have a good CMMS and a good data historian and some kind of analytics tools, such as MyDials or PI, you can do this without spending hundreds of millions of dollars. If you're a small company, you can increase your profit 10% by doing this kind of thing. If you invest $50,000 to get back $250,000, that's a good investment."
He also says that making the connection between asset management and sustainability is "a philosophical issue as much as a technical issue. The technology exits. The tools are there. The vast majority [of companies] haven't done it, not because there's no technology or it costs too much, but because of the cultural shift required."
Many Ways to Skin a Cat
There are many paths to upgrading maintenance practices and driving energy savings and other sustainability initiatives. There is no one "right" way, but rather multiple strategies that will get you where you want to be.
At the Siemens Drive Technologies (www.sea.siemens.com) manufacturing plant in Alpharetta, Ga., a total productive management (TPM) strategy is in place. It uses Siemens' own Siemens Production System (SPS), a methodology devoted to the guiding principle of "avoiding waste." Leveraging lean practices, SPS is a holistic approach involving equipment maintenance, scheduling and a drive to minimize downtime, says Shujath Ali, operations manager at the plant.
One of the SPS metrics is overall equipment efficiency (OEE). "A big part of this is equipment utilization," says Ali. "We measure how much equipment is being used, how often, and its efficiency. The product of utilization and efficiency gives us a scale of how effectively we're using the equipment. We want between 95% and 105% efficiency."
The plant manufactures machines for light and heavy rail and mobile mining equipment, and its chief competencies are assembly and testing. In the testing facility, says Ali, they look at the carbon footprint of the testing machines. "How hot are the machines getting? Do we need to change the equipment? Do we need to get better at using it? All these things feed into maintenance. [We ask] are we overloading the test? Defining the parameters incorrectly? Is there something wrong with the machine?"
In Siemens' case, the drivers for this initiative are cost, productivity and energy consumption. "We have very specific targets for energy consumption, waste management, electricity and water consumption," says Ali. "The entire plant has targets for these things."
Ramping up Maintenance; Cutting Energy Use
Mohawk Fine Papers, Cohoes, N.Y. (www.mohawkpaper.com), is the largest manufacturer of premium writing, printing and digital paper in North America. It operates five manufacturing facilities that use energy-intensive paper machines and 30 converting centers, with a total capacity of 175,000 tons of paper annually.
Paul Stamas, vice president of IT at Mohawk, outlines the challenge for the company. "Our energy costs rose 30% over the past five years, and the U.S. Dept. of Energy told us to expect another 10% increase in one year. Energy is Mohawk's largest operating and maintenance expense—60% of the total—and our motor and pump assets consume 75% of that energy." No wonder cutting energy costs is high on Mohawk's corporate must-do list.
Mohawk sought a solution by means of ramping up its EAM system. "Management needed visibility into data on the factory floor for better decision making," says Stamas. "We needed an EAM system integrating energy into our asset management strategy."
Figure 1. The Des Moines, Iowa, Water Reclamation Authority linked EAM and SCADA to beef up maintenance and save energy.
The system Mohawk chose was Infor10 EAM from Infor (www.infor.com). It was linked to Mohawk's Microsoft SQL Server database to manage the large amount of data the system was collecting.Stamas got the expected benefits of improved preventive maintenance programs through more proactive inspections, calibrations and repairs, but he also got a surprise. "As machines performed better through improved maintenance, our total energy consumption was decreasing. We realized that a more sustainable approach would be to drive down energy consumption in the first place through better energy management at the asset level, which also makes financial sense."
So Mohawk added Infor 10 EAM Enterprise Asset Sustainability solution, which allows the maintenance staff to compare the designed energy use of assets versus actual energy consumption. "We can now incorporate energy efficiency into our asset management program," says Stamas.
Mohawk's system is also integrated with thousands of sensors on the factory floor collecting real-time energy data. The system thus can identify machines whose performance is degrading and sends alerts, so cases of energy waste can be addressed and resolved. "We can even create a condition-based preventive maintenance program, says Stamas.
The sensors collect real-time energy use data, which is then compared to the utility bills, and that information is reported in the EAM to help users identify real, energy-saving opportunities. It also supports repair-or-replace decision-making. "We can find out whether the cost of buying a more efficient motor is less than the energy we're spending to run an old, inefficient motor," Samas explains.
The results are everything Mohawk could have hoped for. Stamas says, "We expect an additional 15% to 20% drop in energy consumption on top of the nearly 15% we've already realized."
Infor's latest iteration, Infor10 Asset Sustainablity Edition (ASE) is a pretty advanced system, says John Murphy, Infor's director of solution management for EAM. He admits that when the company released the solution in 2008, "We were ahead of the market. Customers were not asking for it."
However, visionaries at Infor pushed for it, and, Murphy says, in spite of it being a "tough sell" for customers who aren't so far along with their asset management programs, those who are ready want it to take them to the next level.
"It really is all about the cost data," he says. "As we get more stories about ROI achieved, it will be easier."
The SCADA Connection
One of those advanced customers is the City of DesMoines, Iowa. It's the contracting operator for the region's wastewater reclamation authority (WRA), and it operates a treatment facility that processes the wastewater from an area of 16 entities that encompasses several counties, municipalities and sewer districts.
The facility handles treatment from preliminary stages through secondary treatment and disinfection, including biosolids production and disposal. It has a maintenance department of 26 with an annual maintenance budget of approximately $3.5 million.
Built in 1987, the facility began its trip to advanced EAM starting with MP2 from Datastream. It upgraded to MP7, now Enterprise EAM from Infor (www.infor.com), several years ago. In 2010, driven by the desire to improve its energy efficiency, it embarked on a project funded by the IowaGrants program to integrate its supervisory control and data acquisition (SCADA) and enterprise asset management (EAM) applications to enable that objective. The project was initiated in July 2010 and went online this past January.
This Continuous Commissioning and Energy Efficiency project had several key goals: integrate data between the EAM and SCADA applications/systems; establish and configure energy and condition monitoring capabilities within the EAM; analyze energy usage trends for high-energy-use assets; and identify energy savings opportunities.
To achieve these goals, the WRA upgraded its system to Infor Enterprise EAM Asset Sustainability Edition (ASE). It also had to identify "pilot" equipment items and available data points; establish, design and implement a data structure for integration; and establish trend and analysis reporting.
Other key applications relevant to the project included Rockwell Software's FactoryTalk SCADA/HMI system (www.rockwellautomation.com) and the Hach Water Information System (WIMS) application (www.hach.com/im).
The project set up its test environment by September 2010 and was able to go live with its first operational phase in January 2011. Initial project objectives were to reduce energy usage by roughly 200,000 KW, which makes for savings of more than $40,000 annually.
Actual results achieved in less than six months are on track to save almost four times the original projections. Energy consumption has been reduced by 100,000 KW in the first half year, leading to $20,000 in savings already.
"What amazed us is that we had it in a test environment for five months, so when we fired it up it instantly showed us which were our most energy efficient assets," says Bill Miller, CMM, MMC, MRO, ASE-EAM system administrator, facilities management, City of Des Moines WRA (www.dmmwra.org). "We had about a $15- to $16-dollar-an-hour spread between our most and least efficient blower fans. Once we identified our energy hogs, we quickly switched over to 'data diggers' to find out what was going on."
Data Diggers
Making the system a success required a big pile of data to dig through and some serious back-end analysis tools. "We needed a reliability-centered maintenance program, so we reconfigured our EAM system to support this. We added 'causes for failure' fields to be completed by the craftsman. These were based on root-cause failure analysis. We checked oil analysis, vibration analysis, preventative maintenance (PM) programs and the event history for years back in the EAM system. We started to find out why there was such a wide range of efficiency. In some cases, it was simple. PM frequency might need to be adjusted. A component, say a bearing or a belt, might have needed replacing. Some had more run-time than others because of more use. Buy switching to more efficient assets, we started getting immediate returns—$200,000 in energy savings"
The second practice Miller initiated was facility condition assessments (FCA). "You go out and inspect and rate your assets, your buildings, your critical assets in terms of how much life they have in them. We have an annual report that shows what we need for replacement this year, next year, etc. We configured our EAM system to handle these assessments. We identified all the critical assets that we wanted included. We go into the field and we dig out histories on assets, run lifecycle reports, put all the data together, and compare and come up with an index rating. We have a drop-down menu with four or five fields. We fill them in, and the system calculates that index rating."
They also mined that rich source of data, the SCADA system. "We took our SCADA programmers and brought in a consultant and Rockwell, who helped us connect the SCADA system to the EAM and the historian," he says. "Most companies are keeping some kind of data logs. The Infor asset management system identifies the most efficient assets. If nothing else, send somebody out to look at your own maintenance. [Ask] 'what am I doing with more efficient assets that I'm not doing on the others?' Once you find those and make the correction, it doesn't take that long to see results."
Miller adds, "We're one of the first in the nation to do this in an industrial environment. This strategy has been more used in facilities management."
The strategy earned the Des Moines WRA the 2010
Governor's Iowa Environmental Excellence Award with special recognition in energy efficiency.
This story is one of an overnight success years in the making. Miller says that first there had to be a change in the culture. "Management began to realize how important this data was and the changes that could result. That was when I got permission to do all this stuff," he says.
Once Miller demonstrated the nexus between asset management and sustainability, he also needed to change the focus in IT. "Our program had been set up by IT. What do they know about maintenance, processes and practices? Nothing. I talked them into letting me reconfigure the program. That's when I started using maintenance best practices. Then we went to a web-based service provider that could do monthly vibration and oil analysis inspections. Then we decided to [aim for] asset sustainability."
Lessons Learned
Miller has suggestions for anyone wanting to implement the same kind of asset management system.
First, go about it incrementally, he says. "Pursue a strategy similar to the Des Moines WRA and integrate SCADA and EAM applications while implementing dashboards to identify asset performance related to energy usage. Identify key integration points and upgrade software to the most recent versions. Also, focus on the largest opportunities first, and then on progressively smaller opportunities. Success breeds support. Set objectives at clearly achievable levels that adequately justify the investment and over-deliver."
Being able to detect process deterioration is also of very high value. Establishing a dashboard of key performance indicators (KPIs) was essential to understanding which assets to focus on next.
Don't obsess over the optimum, says Miller. "Just getting all assets to perform at the level of the currently best-performing asset is often enough to produce results sufficient to gain buy-in," he says. "Once parity is achieved, start working on continuous improvement. Finally, invest in internal skills development. Des Moines was able to complete its project in less than a year after grant approval due to its strong internal skills base. Where skills do not exist, be prepared to invest in appropriate skills augmentation by external service providers, but make it a learning opportunity."
Latest from Asset Management
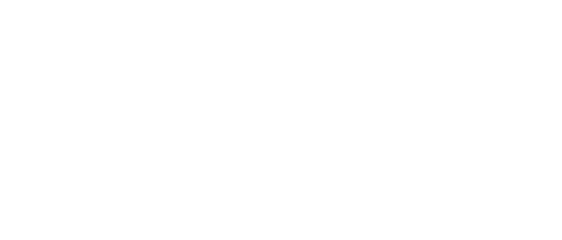
Leaders relevant to this article: