By David R. Llewellyn, Senior Engineer in Process Controls Group, TJ Cross Engineers
Berry Petroleum (www.bry.com) is an independent energy company engaged in the production, development, acquisition, exploitation and exploration of crude oil and natural gas. Berry needed a system to produce steam for injection into an existing oil field reservoir. The steam was to be used to heat otherwise inaccessible heavy crude oil, reducing its viscosity and making extraction viable. This process is known as steam-based enhanced oil recovery or thermal EOR, and it's used in conventional and shale oil fields.
Berry wanted a system that would be inexpensive to purchase and install, simple to maintain and cheap to operate. They evaluated existing solar thermal systems and found them wanting, so they turned to our company, TJ Cross Engineers (www.tjcross.com), and to GlassPoint Solar (www.glasspoint.com) for a better solution.
The beauty of the GlassPoint solar water heating system lies in how its simplicity translates into greater efficiency, less maintenance, and lower installed and operating costs (Table 1). But creating a simple system can often be quite challenging, particularly when it comes to automation. Systems from AutomationDirect (www.automationdirect.com), enabled us to provide the required automation at low cost using a straightforward design.
Steam by Solar
Most thermal EOR systems worldwide burn fuel, primarily natural gas, to heat water and produce steam for injection into the oil reservoir. By contrast, GlassPoint's solar steam generators use the sun's radiant heat to preheat water to about 190 degrees F. This preheated water is then introduced to the natural gas-fired steam generator, greatly reducing fuel use and operating costs.
Solar energy systems of all types often employ very complex designs and expensive components. Solar energy systems that convert sunlight to thermal energy often require a host of complex subsystems to perform tasks such as precise alignment of mirrors, maintenance and cleaning of the mirrors, and actual conversion of sunlight to thermal energy.
For example, a typical solar thermal system uses parabolic mirrors to concentrate sunlight to one or more thermal conversion components located at focal points. These components vaporize water into steam, and this steam is used to drive a turbine connected to a generator. The entire system is extremely complex as it combines a steam-cycle power plant with a large scale solar mirror system and associated thermal conversion components.
By contrast, GlassPoint's solar water heating design employs commercial-grade greenhouses to house the entire solar concentrator mirror and water heating system. For this project, the single greenhouse structure is of galvanized steel and aluminum construction, with tempered 4mm glass roof and walls covering approximately 7,000 square feet of land.
The mirrors are made of an anodized aluminum reflective material used widely in commercial lighting fixtures and are durable for decades indoors, but not usable outdoors. The mirrors are light enough to be easily supported by the glasshouse structure.
All solar thermal systems require precise mirror positioning systems to optimize the efficiency of sunlight reflected from the mirrors to the thermal conversion components. Without a greenhouse, the mirrors must be quite rugged and heavy. Automated mirror cleaning systems are often needed, adding weight and complexity.
Because exposed mirrors and associated cleaning systems are quite heavy, the positioning systems must produce lots of torque. This adds up front costs, and also increases operating costs as relatively large motors are frequently started and stopped to reposition the mirrors.
By contrast, the mirrors in the GlassPoint system are very lightweight. This makes them less expensive to purchase, install and position. For this particular project, the mirrors are positioned using only the torque generated by eight 40-watt stepper motors and drives.
Perhaps the greatest advantage of enclosing the mirrors and the thermal conversion system in greenhouses is the increase in solar efficiency due to two factors: greater heat inside the greenhouse, and a more direct path from the sun to the mirrors.
It's Hot Inside
It's hotter inside a greenhouse than outside, and the temperature differential can be as much as 30 degrees F on very sunny day. This higher temperature differential increases thermal conversion efficiency and boosts hot water output—ultimately lowering operating costs by cutting the use of natural gas in the steam generator. In a fortunate confluence of factors, many of the oil reservoirs that can benefit from steam injection are located in very sunny climes, further increasing benefits.
The thermal conversion device in the GlassPoint system is simplicity itself—just a carbon steel pipe. This pipe, or receiver tube, is located at the mirror focal point. The reflected sunlight illuminates the receiver pipe with 85 times more intensity than direct sunlight. The glasshouse structure provides a zero-wind environment inside, shielding the receiver pipe from wind-driven convective and conductive losses, and eliminating the need for an expensive glass envelope around the pipe.
This pipe runs from one end of the greenhouse to the other (Figure 2). Treated water at ambient temperature enters the pipe, is heated by the concentrated rays of the sun, and exits at a temperature of 190 degrees F for delivery to the steam generators.
Image 2. The receiver tube or pipe absorbs solar energy from the reflector mirrors. Ambient temperature water enters the pipe, absorbs concentrated solar energy, and exits at 190 degrees F.
Benefits of the greenhouse are summarized in Table 2, and include the ability to produce hot water with relatively weak sunlight. But no hot water is produced at night or under heavy cloud cover, which turns out to not be a problem in this application.
The big drawback of all solar energy systems is their inability to produce energy when the sun isn't shining with sufficient intensity. This is a huge issue in most solar energy applications, but not in solar EOR systems.
Studies have shown that the injection rate of steam into an oil reservoir for the purpose of increasing the flow of heavy crude oil can be intermittent with little or no adverse effects on oil production. This is because the reservoir acts as a thermal storage unit, storing heat when the sun isn't shining.
Although the greenhouse allows for a simple and highly efficient thermal solar system, there was quite a bit of complexity in the design of the automation system. But once designed and installed—the automation system enabled unattended operation of the system, along with remote monitoring of all relevant system parameters.
Simple System, Complex Automation
Tracking the sun, positioning the mirrors to deliver the maximum amount of solar energy to the receiver pipe, and regulating water flow rate were particular challenges—but solutions were found, primarily through the use of a Model Productivity3000 programmable automation controller (PAC) and associated automation components provided by AutomationDirect.
To track the sun, a proprietary control system from GlassPoint was integrated into the overall automation system. This proprietary tracking system concentrates solar energy to the water-filled receiver pipe. For maximum overall efficiency and effectiveness of the entire solar thermal EOR system, a constant output water temperature of 190 degrees F is needed.
The flow of water to the receiver pipe varies depending on how much solar energy is available. This factor changes constantly based on time of day, time of year, cloud cover and other factors. The more solar energy, the faster water flows through the receiver pipes, and vice versa.
The system maintains the desired flow rate and corresponding 190 degree F output temperature via a flow control loop. In the loop, a control valve is installed downstream of a constant speed pump. The PAC receives a 4-20mA signal proportional to temperature from a temperature transmitter installed at the receiver tube discharge from the greenhouse.
This measured process variable is compared to the 190 degree F setpoint in a PID loop control executed within the PAC. The PID loop output is a 4-20mA signal that modulates the control valve to regulate water flow to the receiver pipes. PID loop control functionality in the PAC is very powerful, and was easy to implement due to a very well written manual that included precisely defined data types and ranges.
Operator interface to the PAC is provided by an AutomationDirect 12" C-more color touch screen (Figure 3). The touch screen allows local operators and service technicians to monitor the system, and to make adjustments to certain variables. The data logging function uses AutomationDirect DataWorx software to transfer and translate data from the PAC to a Microsoft Access database.
The database software runs on a PC that's connected to the PAC via a hardwired Ethernet link. Temperatures, flow rates and some discrete values—about 10 parameters in all—are logged to the database every 30 seconds.
In operation since February 2011, the system is running smoothly with no particular issues, and our company is now working on another project with GlassPoint. Berry Petroleum has greatly reduced natural gas consumption for steam production, allowing continued enhanced oil recovery. Solar energy is sometimes seen as a competitor to fossil fuels, but in this case the two energy sources work hand-in-hand to increase efficiency in a sustainable manner.
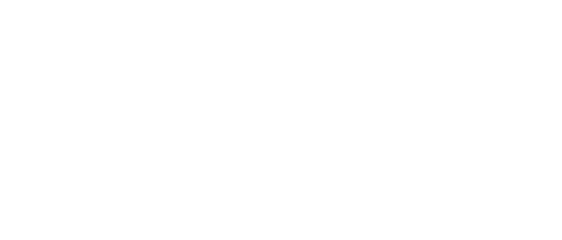
Leaders relevant to this article: