Virtually Simulating the Next Generation of Clean Energy Technologies
Stephen E. Zitney is Director of the AVESTAR Center at the National Energy Technology Laboratory in Morgantown, W.Va.
Imagine using a real-time virtual simulator to learn to fly a space shuttle or rebuild your car's transmission without touching a piece of equipment or getting your hands dirty. Now, apply this concept to learning how to operate and control a state-of-the-art, electricity-producing power plant capable of carbon dioxide (CO2) capture. That's what the National Energy Technology Laboratory's (NETL) Advanced Virtual Energy Simulation Training and Research (AVESTAR) Center (www.netl.doe.gov/avestar) is designed to do. Established as part of the Department of Energy's (DOE) initiative to advance new clean energy technology for power generation, the AVESTAR Center focuses primarily on providing simulation-based training for process engineers and energy plant operators, starting with the deployment of a first-of-a-kind operator training simulator for an integrated gasification combined cycle (IGCC) power plant with CO2 capture.
The IGCC dynamic simulator builds on, and reaches beyond, conventional power plant simulators to merge, for the first time, a "gasification with CO2 capture" process simulator with a "combined-cycle" power simulator. Based on Invensys Operations Management's SimSci-Esscor DYNSIM software (http://iom.invensys.com/EN/Pages/SimSci-Esscor_DynSimSuite_DYNSIM.aspx), the high-fidelity dynamic simulator provides realistic training on IGCC plant operations, including normal and faulted operations, as well as plant start-up, shutdown and power demand load changes. The highly flexible simulator also allows for testing of different types of fuel sources, such as petcoke and biomass, as well as co-firing fuel mixtures.
The IGCC dynamic simulator is available at AVESTAR's two locations, NETL (Figure 1) and West Virginia University's National Research Center for Coal and Energy (www.nrcce.wvu.edu), both in Morgantown, W.Va. By offering a comprehensive IGCC training program, AVESTAR aims to develop a workforce well prepared to operate, control and manage commercial-scale gasification-based power plants with CO2 capture. The facility and simulator at West Virginia University promotes NETL's outreach mission by offering hands-on simulator training and education to researchers and university students.
Balancing America's Energy Supply and Demand with Environmental Responsibility
Today most of the energy consumed in the United States comes from coal, petroleum and natural gas. Fossil fuel sources account for approximately 80% of national and international energy production, and coal-fired power plants account for greater than half of the electricity generated in the United States. With increasing global energy demands, coal is expected to play a dominant role in meeting future energy needs.
Why do we use coal? The answer is fairly simple, considering that the United States is home to the largest accessible reserves of coal in the world, accounting for approximately one quarter of the world's coal deposits. Coal is the largest domestically produced source of energy. While estimates vary, it has been projected that the United States has enough coal reserves to last another 200 years. Availability and accessibility, coupled with relatively low cost—particularly in light of other energy sources—are the primary reasons why consumers in the United States benefit from some of the lowest electricity rates in the world.
However, there are trade-offs for inexpensive energy. The use of coal produces emissions that can impact our environment. For example, coal combustion is associated with increased sulfur dioxide, nitrogen oxide and mercury. Coal use also emits CO2, a greenhouse gas that has been prominent in the news due to its association with global warming. Significant advances have been made to reduce environmental contaminates resulting from coal usage, and ambitious efforts are underway to advance new technologies to burn coal more efficiently while minimizing environmental impact. NETL and its partners have undertaken a variety of strategic initiatives to explore ways of capturing and permanently storing CO2 as a way to reduce CO2 release into the atmosphere.
The Role of AVESTAR in Accelerating Clean Coal Technology
Relative to power efficiency and environmental conservation, gasification technology represents the future for coal-derived electricity. Simply defined, gasification is a process that uses heat, pressure and steam to convert coal into a synthesis gas (also known as syngas), which is mainly hydrogen and carbon monoxide. The syngas is cleaned to remove impurities and sent to a gas turbine where it will undergo combustion to produce electricity. The hot exhaust gas from the gas turbine is used to generate steam, which is then fed to a steam turbine to produce additional electricity. This process is known as IGCC because a coal-fired gasification process is integrated with a combined cycle system that produces electricity from both a gas turbine and a steam turbine driven by the gas turbine's exhaust.
Compared to traditional power plants, IGCC offers many advantages, including increased power plant efficiency, resulting in lower-cost electricity. Because gasification occurs at higher temperature and pressure, with limited oxygen, environmental contaminants are easier to remove from the flue gas stream. The system also makes it possible to concentrate CO2, providing for more efficient removal. Aside from coal, a wide range of carbon-containing materials, such as petroleum coke and biomass, can be used to produce syngas. In addition to being used for electricity, syngas can be converted to other end products, such as specialty chemicals, clean hydrogen and transportation fuels. Coal gasification electric power plants are now commercially operational in the United States and other nations, and energy experts predict that this process represents the future of clean coal technology.
However, IGCC is also a complex process requiring highly trained operators and process engineers. Many plants are now in various stages of design or construction in the United States, and there is a pressing need for a well-trained work force. The AVESTAR Center is therefore providing high-fidelity dynamic simulation environments that will enable trainees to learn to interact with controls that are almost indistinguishable from those they would encounter in a real plant.
What Makes AVESTAR Work?
Flight simulators that train pilots create realistic environments using full cockpit mock-ups and computer-based software. These two pieces work together to replicate what really happens when the pilot flies the plane. When the pilot adjusts the thrust, the simulation software changes the instrument readings and cockpit screen to create realistic views of flight scenarios, including take off, landing and the occasional mishap, all in a safe training environment.
Today, the energy industry is also using training simulators to teach plant operators how to safely start up, control and shut down their processes in a risk-free environment. For AVESTAR, Invensys Operations Management (www.iom.invensys.com) has worked with NETL to develop a virtual "cockpit" (the plant control room) and "flight simulator" (the plant real-time dynamic model) to create an environment where trainees can be taught how to operate clean-coal IGCC power plants with carbon capture.
Invensys's DYNSIM software combines heat and material balances, thermodynamics and reaction chemistry to create high-fidelity dynamic process models that accurately predict what will happen when operators perform certain actions from inside the plant's control room. The company's InTouch software, a human-machine interface, recreates the look and feel of the control room to complete the training environment (Figure 2). For example, the integrated DYNSIM and InTouch system allows an operator to open a plant valve, initiating the flow of coal slurry into the gasifier vessel. The DYNSIM software predicts the rate at which the coal will react with oxygen from the air separation unit and provides readings on gasifier conditions to the plant operator, who is working in a simulated control room using InTouch. Viewing the information provided via DYNSIM, the operator knows when the gasifier is at full load so he or she can maintain safe operation and avoid gasifier trip conditions.
DYNSIM and InTouch can model every operating condition, including emergency and hazard scenarios, to provide complete training in a risk-free environment. The training platform can also provide simulations that assist in the design, construction and performance improvement of IGCC plants. Designers can run and validate an entire control strategy before the plant is even built. And once the plant is up and running, the training solution can be integrated with the control system for continuous operation and refinement based on real-world data.
Leveraging AVESTAR's Simulators in Training, Education and Research
The AVESTAR Center offers a combination of classroom and dynamic simulator instruction to provide hands-on experience operating a commercial-scale IGCC plant with CO2 capture. A portfolio of courses are being offered, ranging from an orientation for engineers and managers to an advanced operators' course, all developed for NETL by Fossil Consulting Services (www.fossilconsulting.com). Information about training is available online at www.netl.doe.gov/avestar/training.html. The AVESTAR team can also work directly with clients to analyze their needs and goals to design customized training programs.
Based on early interest, AVESTAR is getting off to a good start and generating significant attention. In several inaugural demonstrations, more than 50 engineers and researchers from industry, government and academia received hands-on experience with the gasification section of the IGCC simulator. The Center also recently offered its first IGCC training course for participants from the power industry. The overall feedback was extremely positive with the trainees clearly impressed with the simulator, course content, and their "learn-by-operating" experience. More recently, the AVESTAR team provided training on the pre-combustion carbon capture and compression section of the IGCC dynamic simulator to the industry advisory board for the DOE's Carbon Capture Simulation Initiative (CCSI) aimed at accelerating the widespread deployment of CO2 capture technology to hundreds of power plants (www.acceleratecarboncapture.org).
With support from NETL's Regional University Alliance (http://www.netl.doe.gov/rua/index.html), the AVESTAR Center is also enhancing graduate and undergraduate engineering education in process dynamics, control, and safety. Students and researchers at West Virginia University are using the IGCC simulator to learn how large-scale energy plants respond dynamically to changes in manipulated inputs, as well as how control systems impact plant performance, stability and robustness.
To further leverage the AVESTAR facilities and simulators, NETL and its university partners are also pursuing an innovative and collaborative R&D program. In the area of IGCC process control, AVESTAR researchers are developing enhanced strategies for regulatory PID control and coordinated plant-wide control, including gasifier and gas turbine lead, as well as advanced process control using model predictive control (MPC) techniques. Other AVESTAR R&D focus areas include high-fidelity equipment modeling using partial differential equations, dynamic reduced order modeling, optimal sensor placement and 3D virtual plant simulation.
What's in the Future for AVESTAR?
In the next phase of the training program, AVESTAR will incorporate Invensys Operations Management's EYESIM software to add 3D immersive virtual reality to the training experience (www.netl.doe.gov/avestar/3d_virtual.html). The EYESIM solution extends training beyond the control room, allowing the field operator to perform manual functions, such as opening or closing a valve or starting or stopping a pump, from anywhere within the IGCC plant.
Wearing a stereoscopic headset or eyewear, trainees enter a virtual environment that allows them to move freely throughout the simulated 3D facility to study and learn various aspects of IGCC plant operation, control and safety. Using gamepads for navigation, trainees can interact with plant equipment items (e.g., gasifier in Figure 3), activate transparent views (e.g., liquid level in a tank), display pop-up trends (e.g., gas turbine combustor temperature over time), and experience equipment sound effects (e.g., pump engines), malfunctions (e.g., leak in Figure 4), and visual training scenarios (e.g., distillation column operation in Figure 5).
Figure 4: Gas leak in sulfur recovery section of IGCC immersive training system
Combined control room and field operator instruction allows for realistic training without compromising worker, equipment and environmental safety. It also better prepares operators and engineers to manage the plant closer to constraints while minimizing or avoiding the impact of any potentially harmful, wasteful or inefficient events. Additional benefits include improved communication and collaboration among work crews, off-line evaluations of procedures and training for safety-critical tasks.
Figure 5: Transparent view of distillation column operation with animation of vapor flow and liquid holdup on trays
NETL and its partners plan to continue building the AVESTAR portfolio of dynamic simulators, immersive training systems and advanced research capabilities to satisfy industry's growing need for training and experience with the operation and control of high-efficiency, near-zero emission energy plants. To learn more about the center and training capabilities, visit the AVESTAR website at www.netl.doe.gov/avestar.
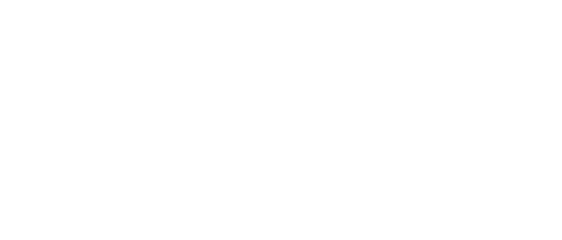
Leaders relevant to this article: