Greg McMillan and Stan Weiner bring their wits and more than 66 years of process control experience to bear on your questions, comments, and problems. Write to them at [email protected].
Stan: We continue our venture in the world of analyzers with an interview of Michael Chaney, a consulting technologist providing analyzer support of olefin and polymer plants.
Greg: What comes first—the analyzer or the analyzer application? The tendency in some plants to use analyzers for just process monitoring may have led to a status quo and, in some cases, a decline in applications. If an analyzer is used for closed-loop control, the demand and benefits are greater. I agree with Shinskey in that, if you can create the control systems that take advantage of the analyzers, you will create the demand for analyzers. What drives the demands for analyzers in your plants?
Michael: Our regulatory and advanced process control applications are a major user of analyzers. The plants demand high performance for accuracy and on stream time. The model predictive control (MPC) dynamic and the real-time optimization (RTO) steady-state models depend upon on-line or at-line analyzers. If an RTO system is turned off, it can be a flag that an analyzer needs maintenance.
Stan: How can analyzer maintenance be improved?
Michael: Gas chromatographs (GCs) are consistently reliable, but as with any device, parts need to be replaced. GCs have a 25-year life expectancy. For the first year after a new product release, experience is gained before the analyzer is used for control. For the next 10 to 12 years, we have support from the manufacturer followed by 12 to 24 years of just an offering of service and spare parts. At the end of the lifecycle (about 25 years) we resort to maintaining equipment with used spare parts.
Greg: The total time delay in an analyzer measurement is the sample transportation time delay, plus an equivalent dead time from analysis cycle time and multiplex time. The equivalent dead time is 1.5 times the cycle time and 0.5 times the multiplex time, since the results are communicated at the end and beginning of the interval, respectively. What are the control requirements in terms of allowable analyzer time delay?
Michael: We work to design the system so that the data is fast enough for an update of the model. The advanced process control (APC) group can give a specific time target. The regulatory control group tends to want the data even faster, and that is often a consideration. We keep the analyzer shelter within reasonable distance of the analyzer sample point, and choose a slip stream and sample flow rate and volume to provide an acceptable transportation delay. We recycle these streams as much as possible. We do not multiplex normally. When model update times are exceptionally slow, as might be the case with RTO systems that have relatively long execution time intervals, we may multiplex sample readings. For example, we have a single GC servicing up to five furnaces sequentially.
Stan: One of the problems we have seen is the reaction of control systems to extraneous changes in analyzer reading. How do you help ensure updates are representative of actual process changes?
Michael: I make sure the new analyzer meets the application requirements before I turn over the analyzer for use in control systems. It is attention to every detail in the entire system from the process tap to the DCS communications.
To avoid contaminants running along the pipe wall, a sample probe is extended into the pipe, paying attention to engineering fundamentals developed for thermowell wake frequencies. Sometimes I use an elbow with the sample tube facing downstream. The end of the sample tube is beveled (cut at a 30º angle) with the high edge on the side of flow impingement to minimize solids taken in the sample.
Small amounts of two-phase flow or solids are disastrous to analysis and can cause contamination and detector damage. We normally use a ¼-in. to 3/8-in. sample probe. The more process you take out, the more you have to clean, filter and return.
Membrane hydroscopic filters have helped some difficult sample systems. Good pressure and temperature control does a lot to eliminate the liquids from vapor components dropping below the dew point. A vaporizing heated regulator is often installed at the sample point. Steam tracing is not used because of the cost of ownership. A slight leak, a blocked condensate return, or overheating can cause thousands of dollars of damage. We use electrical tracing and smart temperature control with a resistance temperature detector (RTD), PID and soft start protection to prevent the lines from going from super cold to hot.
Greg: What are some of the latest developments in sample systems?
Michael: Miniaturization, standardization and smarter automation with the use of pressure transmitters instead of pressure gages and flow transmitters instead of rotameters. The cost is coming down, and the reliability is now being proven for chemical industry use.
Stan: Where do you use viscometers?
Michael: We use viscosity measurement as an inference of melt index in polymerization products. A sample is taken at the die plate of the extruder where a screen catches particles. A precision pump, a melt-pressure transducer, precision temperature control and orifice are used. The melt index changes by two orders of magnitude (0.5 for hard to 50 for soft). The speed of the pump manipulated within a 0 rpm to 75 rpm range for pressure control provides a measurement of melt viscosity. One unique issue is that the time delay of this analyzer depends on using the proper orifice. The volume is fixed from the extruder to the orifice. At 10% speed you are pumping 12 cc/min and at 90% speed you are pumping 108 cc/min. This variable process delay time gives us a 55-minute down to a 9-minute delay, depending on the process viscosity measured.
Greg: Where do you use density meters?
Michael: We use vibrating tube type density meters in our olefins plant where harmonics change with gas density. They are extremely reliable, and I haven’t touched them in many years. We have installed Coriolis meters for distillation advanced process control (APC) models.
Stan: What is your experience with mass spectrometers?
Michael: Our success level has not been good. A drop of liquid is disastrous. It is difficult to get them working reliably. The total cost of ownership is much higher than the cost of a GC. The skill level needed for proper application, installation and maintenance is much higher. The precision achieved may be lower than the stated catalog precision due to lack of chemistry stability where background gases cause interference.
Greg: How about other analyzers?
Michael: If we are looking at absorption at a particular frequency, IR is our first choice. New multiwave techniques can measure more than one component. The cost of ownership is low, since there are no or very few moving parts. We view NIR as a last resort. NIR is too complex and expensive, and the chemometric models are impossible to decode for some of our complex streams. We need extensive sets of lab samples to calibrate and validate and at least one PhD on the project team.
Top 10 Reasons to Use NIR
(10) IR is too far.
(9) Black boxes are special.
(8) Your son has a PhD in math.
(7) The supplier says you don’t need a sample system.
(6) The supplier says you can analyze anything.
(5) The supplier says you can have results in seconds.
(4) The supplier says just leave everything to him.
(3) The supplier says billions of calculations are a piece of cake.
(2) You think gathering samples for calibration and validation is fun.
(1) You will be retired by the time the analyzer is validated.
Latest from Flow
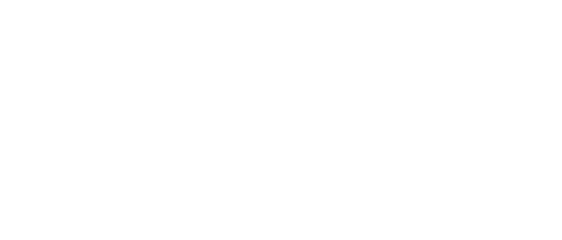
Leaders relevant to this article: