Ruchika Kalyani is a control system engineer at Fluor Daniel India Pvt Ltd.
A diverse range of flowmeters, along with the turndown factors, is available for various flow applications, such as regular flow control (steam, gas, utilities, etc), process flow rates, fiscal or custody-transfer metering, and others. Most of these applications will be unidirectional, but some will be bidirectional.
The measurement of unidirectional flow rate is possible with all types of flow technologies, but the bidirectional flow measurement capability is required to measure the flow rates within the same flow loop in opposite directions. This sometimes creates difficult situations, challenges, process interruptions and/or measurement inaccuracies that can significantly affect the production and profitability of the plant.
We will further discuss the selection of the appropriate metering for bidirectional situations and applications, limitations, advantages and disadvantages, maintenance and installation costs.
Bidirectional Flow Measurement
Bidirectional flow lines are not very common in refineries and petrochemical plants, but if they are needed, they are always difficult. For bidirectional flow, the piping scheme uses the same line to accomplish delivery and/or control functions for flows moving in opposite directions (forward or reverse flow), depending upon the process conditions and objectives.
Examples of bidirectional flow are
- Raw water feed to two or more water treatment plants,
- Bidirectional steam lines supplying steam from one unit to another unit in the plant,
- Utility and circulating pumping of dielectric fluid into underground electrical cables in order to dissipate heat generated by high-voltage power lines,
- Gas injected or withdrawn from the gas storage field or reservoir,
- Purging and blanketing of nitrogen in plants, and
- Chilled water plant decoupling headers.
Bidirectional Flow Measurement Using Volumetric Flowmeter Options
The selection process of bidirectional flow metering depends on application requirements, process demand, end-user accuracy requirements and physical design constraints of the flowmeter itself. Various flowmeters are available with bidirectional flow capabilities, such as DP transmitters with an orifice, the Venturi or wedge element, Coriolis, ultrasonic, vortex, pitot, turbine and magnetic flowmeters.
Instances where a bidirectional flow measurement is required include
- Possibility of having two different flow rates in either direction, due to the process and design conditions, and both flows need to be measured,
- Reverse-flow accuracy is required by end user or by the process,
- The need to measure reverse flow in the process,
- Bidirectional flow measurement using dual DP transmitter options.
For bidirectional flow measurement between two process units in a process plant, for example, when two steam units are linked to each other, at the time of deficiency of steam in one unit, the other unit will supply the required steam to the deficient unit and vice versa. If reverse and forward flow rates are identical in both directions, and precise accuracy is not required, then dual transmitters, one for each flow direction, are the best solution for measuring the steam flows in/out of the plant. Two DP transmitters with an orifice plate, along with temperature compensation, can be used for the bidirectional flow. In this case, a non-beveled, square-edge type orifice plate should be used, and the two edges of the orifice should comply with specifications for the upstream edge mentioned in the ISO 5167 standard. It's also necessary to make sure of the full "upstream" straight lengths on both sides of the flow instrument. This must be clearly communicated to the piping design team during design reviews and before construction begins.
With this combination, do not expect high accuracy and turndown. This combination will provide the lowest installed cost with acceptable accuracy, as it is easy to maintain and replace. Also, this dual transmitter combination option will be ideal in cases where the transmitter will experience reverse flow once every four or five years for a four- or five-day period.
Bidirectional Flow Measurement with a Single DP Transmitter
A single DP flow transmitter coupled to a primary element option, such as the special orifice plate mentioned above, can also be adopted for cheap reverse-flow measurement. This arrangement will cut down the expense of installing another (second) DP transmitter, orifice plate, additional hardware, meter installation requirements and the complexity of signal switching.
The square root function is complicated by the one-transmitter option because reconfiguration of the transmitter signal (4-12 mA and 12-20 mA) requires added function blocks and, subsequently, corresponding function blocks or logic at the distributed control system (DCS) side.
In cases where it's only a matter of knowing the reverse flow direction, and accuracy is not important, then the existing DP set without configuration can be used. At zero flow, 4mA is shown, and an output less than 4 mA can be used to alarm for reverse flow even when the square root function is on.
With newer, smarter flowmeter techniques, transmitters are equipped with a feature that allows reconfiguration of the DP transmitter range, such as split-range output signal (4-20 mA) to the system side (DCS, PLC). The bidirectional function, such as square root functions, can be directly applied to the transmitter by either installing special bidirectionality software at the control system side, or by using the built-in capability of the flowmeter to be used in both forward and reverse flow directions.
With equal or unequal flow rates, flow direction will be indicated as the output value (4-12mA = Reverse and 12-20 mA = Forward). With equal flows, zero flow point is established based on the DP range of forward and reverse flow, and for unequal flow rates, zero flow point will be a calculated value.
Bidirectional Flow Measurement with Vortex Flowmeters
The other option of two vortex flowmeters can also be used for steam bidirectional flow if higher accuracy is required than can be achieved using the orifice solution. However, this application is limited to smaller line sizes because vortex meters are more economical up to 4-in. (100-mm) pipe size. Beyond this size, orifice plates are more economical. In addition, the selection of a vortex-shedding flowmeter may increase the maintenance and installation cost.
Wherever higher accuracy is required, vortex flowmeters are not a good option, as vortices shed by both bluff bodies propagate really far beyond the pipe and may affect the other meters' readings. Another drawback is that the straight pipe run distance required between two vortex meters is unpredictable. For example, in the case of no obstructions, the meter required the run of 10 D (diameters) to 15 D, and if there is a control valve in either direction, the meter may require a higher run of 25 D to 30 D or even more. In comparison to the options of dual transmitters for bidirectional flow measurement between the two process units, DP flow measurement may be the most cost-effective solution.
Bidirectional Flow Measurement with Turbine and Magnetic Flowmeters
Bidirectional flow measurement is always a challenge when there are changes in process parameters, such as viscosity, conductivity, etc. It is always worth keeping these specific situations in mind while selecting any flowmeter technology, but with bidirectional flowmeter applications, it is especially important. DP type meters are usually not really well-suited to handle these process parameter variations.
Again, an example is utility pumping and circulating plants pumping dielectric fluid into underground electrical cables in order to dissipate heat generated by high-voltage power lines. This application requires flow rate monitoring upstream and downstream because it involves dielectric fluid; therefore, it requires viscosity compensation as the temperature of the dielectric fluid changes. In this application, turbine flowmeters can provide the solution for bidirectional flow measurement with moderate accuracy. However, drawbacks associated with this technology include a poor response of the flowmeter at low flows due to bearing friction; lack of suitability for high-viscosity fluids because the high friction of the fluid causes excessive losses; as well as the requirement for regular maintenance and calibration to maintain its accuracy.
The magnetic flowmeter can also be used for bidirectional flow measurement. It has the advantages of no pressure drop, linear output, short inlet/outlet pipe runs (five diameters upstream of the electrode plane and two diameters downstream), and good turndown. Magnetic flowmeters are relatively expensive and are mainly limited to conductive fluid applications, such as acids, bases and slurries, as well as water. A pre-requisite for this type of flowmeter is that the fluid is electrically conductive with an absolute minimum conductivity of 2-5 µSiemens.
Bidirectional Gas Flow Measurement with Ultrasonic Flowmeters
At gas storage fields or natural gas reservoirs, accurate gas flow measurements are required for tasks such as injection and withdrawal of gas from these reservoirs. Reservoirs are used as buffers between suppliers and consumers. In order to maintain the balance for the entire reservoir, it's necessary to monitor bidirectional flow at the wellhead.
For this purpose, conventional DP flowmeters with an orifice are far from a suitable solution, as they lack accuracy and reliability. Orifice plates are subject to wear and tear. Secondly, regular inspections and maintenance are required. While measuring the dirty gas, the pressure taps of the orifice plates are particularly exposed to clogging due to the solid particles which may be present in the dirty gas. These will definitely distort the accuracy of measurement.
In these cases, an ultrasonic flowmeter may be a far better solution because this type of flowmeter has no pressure drop, no flow blockage, no moving parts, and is suitable for high-volume bidirectional flow and also for low-flow measurements where other types of flowmeters do not provide the required results.
The advantage of using the clamp-on gas flowmeter transducer on the outside of the pipe is that it doesn't require any pipe work or any kind of process interruption. With this type of flowmeter even a little moisture content present in the gas can't significantly affect the measurement.
The reliability, negligible maintenance with highest accuracy and long-term cost of ownership are the major benefits of this technology.
Bidirectional Flow Measurement with Coriolis Mass Flowmeters
In the process industries, Coriolis technology has set the standard for flow and density measurements. This technology is used for various applications, such as mass balance, monitoring of fluid density and custody transfer, but also to reduce maintenance, and for bidirectional flow measurements.
In refineries, there are bidirectional applications, such as import and export of product, product transfer to storage and to petrochemical plants, and where the accurate measurement is more important than cost.
Coriolis mass flowmeters can be used for accurate and reliable measurements of all streams in and out of the plant. This is critical for accounting and profitability. End users should take into account that inaccurate measurements sometimes may cause them to give away more product than they are being paid for. This can result in a significant loss of profit.
Conpared to the traditional use of volumetric flow technology for bidirectional measurements, the use of Coriolis mass flowmeters eliminates various well-known drawbacks of volumetric technologies, such as the requirement for significant upstream and downstream straight piping length and the reduction of potential errors that occur in compensation for temperature, pressure, viscosity or specific gravity. The Coriolis mass flowmeter technology does not require that compensation.
Coriolis meters measure mass flow. They do have their own inaccuracies, but these tend to be low relative to other types of flowmeters. The turndown of Coriolis meters is high compared to other types of flowmeters. Another advantage is that no recalibration is required when switching fluids or for changing process conditions.
Purchase Price vs. Cost of Ownership
It's important for control system engineers to evaluate accuracy required for applications before selecting any bidirectional flowmeter technology, as more accurate and precise flow measurement often results in higher cost of the flowmeter.
The control system engineer must understand that price is always the consideration. However, there are some important distinctions to be made in terms of price. A flowmeter can have a low purchase price, but can be very expensive to maintain. Alternatively, a flowmeter can have a high purchase price, but will require very little maintenance. In these cases, the lower purchase price may not be the best bargain. Other components of price include the cost of installation, the cost of associated software, the cost of training people to use the flowmeter, the cost of maintaining the meter, and the cost of maintaining an inventory of any needed replacement parts. All these costs should be taken into account when deciding what flowmeter to buy. This should be the one reason for many users to look beyond purchase price when considering flowmeter costs.
Latest from Flow
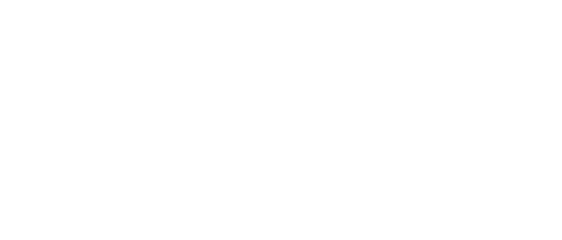
Leaders relevant to this article: