Tim Matheny is president of ECS Solutions, Inc.
Randy Otto is vice president of ECS.
Southwest Baking Co. in Tolleson, Ariz., had a problem. The batch system designed for its dough mixers was no longer supported by the OEM that developed and installed it. The bakery had a PC-based batch system connected to Rockwell Automation's control hardware. The PC could fail at any time. With the possibility of a system failure, Southwest Baking needed to do something.
Flexible Dough Mixing
The OEM offered to supply Southwest Baking with a new batch system, which would also be specifically for dough mixing. As an alternative, Southwest Baking turned to Rockwell Automation, supplier of their controller equipment, and ECS Solutions in Evansville, Ind., an RA Authorized Process Integrator and Control System Integrators Association (CSIA)-certified control system integrator. Rockwell Automation's team proposed replacing the OEM batch system with FactoryTalk Batch, which adheres closely to the ISA-88 standard.
FactoryTalk Batch is flexible enough to be applied to any process. However, implementing FactoryTalk Batch carried a higher initial cost than purchasing an upgrade from the OEM. It also raised fear, uncertainty and doubt about modifying the OEM controller code to properly interface with FactoryTalk Batch. This is a smaller systemājust the size system which many might say does not need a fully capable batch management system. However, Southwest was able to see the power in flexibility.
"Southwest Baking's upper management fully supports the use of leading edge technology" says Robert Wroblewski, engineering manager at Southwest Baking. "Applying a proven, flexible, off-the-shelf solution that can adapt to our process opens the doors for continuous improvements, even if we don't realize all of the benefits immediately."
FactoryTalk Batch can be applied to any new or existing process in three general steps:
The first and possibly most critical determination to make is which of the major pieces of process equipment need to be units and which do not. The determining question is, "Does a major processing activity occur inside this equipment?" A pump is not a unit because a pump just transfers material, while the material is unchanged. A raw or finished goods storage vessel is generally not a unit because it's for storage, not processing. ECS determined that four hoppers and the mix bowl filler needed to be defined as units in FactoryTalk Batch (Figure 2).
Programming to make the equipment do whatever it does goes into the basic process control system (BPCS). In this instance, the BPCS was a RA Logix controller system. How the equipment was to be used was "programmed" as FactoryTalk Batch recipes.
The second step ECS took was to make modifications to the BPCS code. ECS kept as much of the OEM programming as possible. The OEM BPCS code was broken up into tasks, each using specific pieces of process equipment. ECS then added logic to interface each task to FactoryTalk Batch.
Jeff Harpenau, the ECS project manager notes, "In hindsight, it would have been more efficient to scrap the OEM code entirely and start over. The code was inflexible and not modular. The wrappers we created to separate the code into phases had to be woven into the existing code, making the changes more challenging." Even Southwest Baking recognized this and asked ECS to evaluate replacing the OEM code entirely with S88 Builder. ECS recommended, and Southwest plans to use, S88 Builder on a potential second line, line one being retrofitted later.
Also Read: Managing the Digital Oilfield of the Future
The third step involved programming how the equipment will be used. In a BMS, such as FactoryTalk Batch, recipes are built up from phases. A particular recipe phase in FactoryTalk Batch runs a particular equipment phase in the BPCS. FactoryTalk Batch starts the phase, monitors its state, collects any data required and then terminates it on completion. ECS configured a phase in FactoryTalk Batch for every task or phase created in the BPCS.
The flexible flowchart-like recipes described in ISA-88 and implemented in FactoryTalk Batch encourage focus on efficient utilization of the process equipment. At this higher level, it is very easy to see how certain process steps might execute in parallel and to arrange those process steps (phases) as efficiently as possible (Figure 3).
At runtime, FactoryTalk Batch allocates equipment, keeping another batch recipe from using the equipment when needed and releases it, so that another batch can start when it is no longer needed. In the dough mixing system, a "minors" unit is released as soon as it empties into the primary mix unit. While the primary mix unit is mixing batch "A," the appropriate minor ingredients for batch "B" can be loaded into an available "minors" unit. FactoryTalk Batch does this whether batch "B" is part of the same production run, sometimes called a campaign, or not.
A combination of factors all related to flexibility in the control system improved process equipment utilization significantly. A five-minute cycle time per batch was reduced by 30 seconds, or 10%. Who would not like to see a 10% capacity improvement?
Wroblewski says, "The new batching system and ongoing support from ECS allow me to sleep at night. From an operational viewpoint, it's proving to be a reliable and very stable platform. The new system makes it possible to recover batches we would have lost in the past. We're now able to quickly and effectively resolve any issues we might have in the batching system. The system is complex and powerful, and with ECS's help it's usable by most of our team."
He adds, "We easily converted existing equipment to alternate uses with changes in the system programming without the cost of added equipment. Southwest Baking has done many startups before, both system upgrades and new installations. With ECS, projects have gone off without any major issues and on time. We at Southwest Baking couldn't be happier with the results we're seeing. We owe a lot of this to ECS. They listen to our goals, and continue to respond to those needs."
And Data Collection
ECS implemented data collection as part of the new FactoryTalk Batch recipes. FactoryTalk Batch has the flexibility to collect data at the start, during and/or after any phase. ECS configured a time-series historian to collect data periodically, independent of a particular batch or batches. All data is collected into Microsoft SQL Server where Southwest can readily access it via reporting services, built in FactoryTalk Batch reports and even Microsoft Excel.
"We've become adept at reviewing the collected data to learn why we observed a variation in our end product," says Wroblewski.
Also Read: FactoryTalk Editions Reach Out and Coordinate Data Treasure
This knowledge allows Southwest Baking to take appropriate corrective actions.Ā He continues, "As a company, we've always been believers in repeatability through data collection, accurate and timely reporting that allows us to respond in a proactive way. FactoryTalk Batch provides a lot of good reporting, and ECS has supplied other, more company-specific reports that we needed to accomplish our goals. Through these reports we can see areas that might need attention to keep the speed and high accuracy of our ingredient flowing into the process."
Sweet Taste of Success
The taste of success is sweet, but Southwest Baking is not satisfied to stay where it is. "We want to get to where the data tells us we are having a problem while it is occurring, rather than after the fact," says Christian Belzunce, Southwest Baking's general manager.
Belzunce has a vision of paperless operation, starting on the factory floor and moving throughout Southwest Baking. Follow-up projects will include reporting, dashboards and interface to Southwest's ERP system.
ECS will finalize implementation of FactoryTalk Batch Material Manager. Material Manager brings just-in-time material management to batch execution systems, allowing more effective management of materials and recipes. It complements ERP-level resource management by providing plant-level material management and tracking. Raw material receipt transactions will be sent from the ERP system to an ECS interface, which will record the raw material quantities in Material Manager.
When a FactoryTalk Batch recipe consumes raw materials, the Material Manager database is automatically updated by FactoryTalk Batch. Later, another ECS interface will pass the consumption and production transactions to the ERP system. This project will eliminate paper, with the accompanying errors, replacing it with accurate electronic transactions.
ECS and Southwest Baking are discussing dashboards to help operations identify real or impending problems and take corrective action more quickly. One approach being discussed is to start with monitoring overall equipment effectiveness (OEE).
Southwest Baking achieved the results it has and will be able to achieve the results it desires because its management spent a little more money to purchase a flexible system. Southwest Baking chose to work with a competent, CSIA-certified, independent system integrator even though that seemed counterintuitive to working with the original equipment manufacturer. Once again, the power of flexibility trumps a more rigid, but initially less expensive system.
Latest from Asset Management
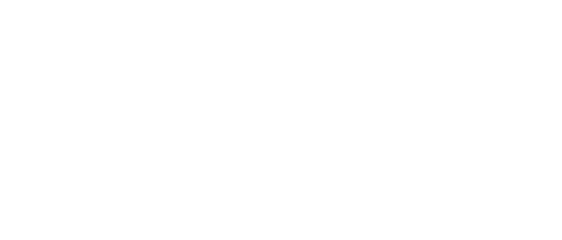
Leaders relevant to this article: