Check out ControlGlobal.com on Google+
In a successful industrial manufacturing environment, data is king. During two sessions at the Rockwell Automation TechED conference this week in Orlando, Fla., attendees learned both how displaying and representing operating data to process operators should be done to maximize operator awareness and performance, and how proper data collection, organization, and record keeping make life easier for companies with regulatory compliance responsibilities.During the session "How to Improve Plant Operations Through Better HMI Graphics," Dave Board, Rockwell Automation commercial manager, provided key insights into how to design effective human-machine interface screens for plant operators, noting "Who wants to be responsible for designing an HMI graphic that can lead to confusion, cause eye fatigue, and cause operators to make mistakes?"
So, Board said, good situational awareness for operators means "being aware of what is happening around you, understanding what the information means to you now, and understanding what that information means to you in the future. It also relates to the goals and objectives of a specific job or function."
Board said designers and engineers form in their heads a different mental model of the process than do the operators. "So by understanding how operators select and use goals, designers can better understand how information is perceived," he stated. "Without understanding the user's goals on situational awareness, the information presented has no meaning."
Board explained how to apply situational awareness (SA) terminology to HMI graphics. "Level 1 SA is a process and instrumentation diagram (P&ID) representation with raw numbers on a screen," he said. "Level 2 SA provides the operator with the relevant information they need to understand how the plant is operating. Level 3 SA provides trending data so that the operator can see how it has /performed and how it will perform." Level 2 and Level 3 SA, Board said, reinforce the operator's mental model of the plant or process.
"We had to shut the cooker down until it was resolved." Jonathon Riechert of Hillshire Brands shared how the company's data historian and visualization tools have helped to quickly diagnose process issues.
Board made it clear that despite the wonderful and imaginative, 3D color graphics available to designers today, they have no place in a best practices list for industrial operator displays. "Use gray background, vessels and pipes in low contrasting grey," he said. "High contrasting color objects strain the eyes and cause fatigue. Warm colors—the reds, orange, and yellow—especially when flashing, draw the operators attention to them. Color should be used for abnormal plant conditions only." In like fashion, there should be little or no movement of objects that cause unnecessary distractions.Board is a big fan of analog status indicators to help interpret data. "The brain interprets analog more quickly than a number," he said. "We should provide a pointer to a scale, provide a clear indication of the normal working range, and clearly show upper and lower limits." With an analog display, the operator can easily see where the value is as well as what it is. And he can easily see rates of change. "The key operating parameters should be trending on screen, not requiring the operator to click to show them.' Board stated.. "And radar plot are good for easy monitoring of multiple, but related variables."
Good Data = Safer Food
In a second TechED session entitled "Hillshire Brands: Manufacturing Intelligence Key Ingredient in Food Safety Modernization Act Compliance," attendees learned that the completeness, integrity and historical availability of production data in the food processing industry for product traceability is of critical importance, given a heightened consumer awareness of inspection failures and product recalls in recent years.
Most of the activity is driven by the Food Safety Modernization Act (FSMA), explained Ian Tooke, director of consulting at Grantek Systems, which works with Hillshire on these issues. "In 2011, the CDC estimated that in the U.S, more than 48 million people got sick as a result of food-borne illness," Tooke explained. "Not all of that is attributable the manufacturing process, but annually 3,000 die from it." Tooke further estimated the hit to the U.S. economy at $7 billion per year, not including the potential impact on a particular company's brand equity.
"Food manufacturers are watching as the Food Safety Modernization Act (FSMA) evolves to the next levels," Tooke said. "The focus of the FSMA is to shift food contamination responsibility from response to prevention."
As a result of the FSMA, Tooke said, manufacturers need to be proactive and start thinking about how the FSMA will impact: manufacturing plants, manufacturing business systems, production methods and supply chains.
"There's always been regulation, but this is the most significant effect on the entire supply chain of food manufacturers, from farm to consumer, since 1938," Tooke said.
Product traceability, which is at the heart of the new law, occurs at multiple levels. "This means traceability through the whole production line," Tooke said. "There's post-production traceability to minimize food safety risk in case of recalls. There's matching and verifying packaging, as well as presence and quality responsibilities to check that codes on packages are readable."
Jon Riechert, senior engineer–Innovation at Hillshire Brands, outlined a current data collection project at its corn dog facility near Ft. Worth, Texas, that aims to deal with the issues resulting from FSMA. "This is the fourth facility at which we've installed FactoryTalk Historian and FactoryTalk VantagePoint from Rockwell Automation, but what's unique about this project is that we're attempting to cover every area of the plant. That means 1,500 data points across utilities, processing and packaging." In the end, Riechert said, management will be equipped to respond to changes more quickly.
The project's goals, Riechert said, were to use data to improve line transitions from sanitation to production; provide end-of-day production reports; determine yields and pounds produced by SKU, by area and for the entire facility; provide food safety traceability. "It's all aimed at having full capability to ensure product traceability during the journey through the entire plant process, if ever a problem arose, as well as collect valuable process data to aid in the investigation of production hiccups."
"The food safety focus areas involve process data from two cook lines, 12 freezers for each of the frying lines and 15 different packaging lines," Riechert reported. We have product distribution flow throughout the plant that varies, so we have to track and record what product goes to what packaging line from what fryer. In addition, we have a packaging verification step to make sure that it's correct for the product."
A good example of the data collection effort for food safety integrity comes from a sister plant, said Riechert. A sausage cooker in Alabama was often overcooking and undercooking for reasons unknown. "We had to shut the cooker down until it was resolved," Riechert explained. "We sent executives and engineers in on the company plane because this was a serious problem."
"Using FactoryTalk Historian we located the deviations and the dip in cook temperature zones. We created another graph, drilled down further and found that a steam valve controlling humidity was not in control; it was always open or always closed. That was traced to the operators reacting to deviations by raising the cook temperatures, driving the humidity down and causing the valve to stay open, which drove the whole system out of control. We lowered the temperature 50 degrees, to where the recipes originally called for, and the system went back in control. We never would have found that if we hadn't been able to back to the collected data in the Historian."
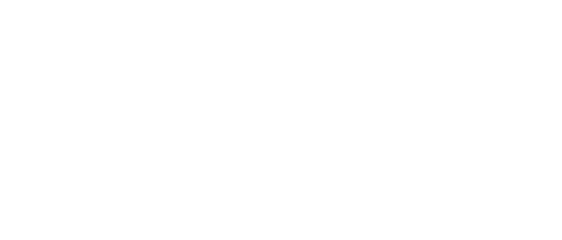
Leaders relevant to this article: