William M. Hawkins is a member of Control's Process Automation Hall of Fame (2008) and author of the recently published book, Automating Manufacturing Operations: The Penultimate Approach, Momentum Press, 2013.
Machines Need Operators
Machines require operators because, despite marketing claims, there are no intelligent devices. The only intelligence exists in human brains. Humans can program equipment to do interesting things, but the equipment is completely unable to deal with anything the programmers didn't think of or couldn't afford.
Operators use different skills for different processes. What they have in common is a desire to control equipment and a sense of satisfaction from doing that well. The job has long periods when all goes well punctuated by great activity to keep an accident from happening.
The people who tended steam engines were the first operators. They had to know how to take care of the engine, particularly lubrication, and know the engine's limits, as well as how to start and stop it. They also had to know how to operate the associated boiler. See How to Boot a Steam Locomotive by Phil Jern, available at several places on the web.
Read Also "How Industry Professionals Pull Together in Process Automation Projects"
Operators Need Training
The first controllers were closely tied to their sensors, which meant that indicators and controllers were mounted on a panel close to the controlled equipment. Operators had to walk through the process, checking on the equipment. Standard signals allowed instruments and controllers to be mounted on large panel boards in a central control room. Operators were then divided into board and field classes.
New operators started in the field with experienced operators. Humans are very good at retaining practices that they have been shown and given a chance to repeat. With sufficient practice, an operator could make the transition from the actual equipment to the abstraction at the central control panel. Further job advancement could put an operator back in the field looking for trouble before it got out of hand.
Operators Follow Procedures
Training must be followed by practice, or the training will be lost over time spent doing other things. Simulations are useful to maintain practice if the process is being operated by advanced automation. Process control simulations are much easier than aircraft flight simulations because the operator gets all the process knowledge from computer displays, and the control room is firmly attached to the ground.
An operator learns the details of the machinery and what the controls do, and then learns what to do with the equipment. There are procedures to follow for all sorts of potential events, including unwanted events. Operators also develop detailed mental maps of the locations of process equipment and the tag names that identify them.
Operators Make Mistakes
Equipment may break or fail in many ways, but humans make mistakes or errors. Operators make mistakes when they lose track of what the process has done, is doing and will do next. An alarm flood can confuse an operator about these things.
Procedural control can confuse an operator with no alarms at all if operators can't tell where they are in the procedure. An operator who performs procedures manually has little doubt about the present and future states of the process. A backup operator has to watch every step the active operator takes in order to stay up to speed. When automation performs procedures, the operator becomes a backup operator.
Accidents happen. The worst accidents seldom have a single cause. Trevor Kletz analyzed many accidents before writing Learning from Accidents. He found that when human error is suspected, the operator involved had not had adequate training or hadn't been trained recently. Another excellent book is Inviting Disaster by James R. Chiles.
Automation Replaces Operators
Automation introduces a machine or system to do some portion of the work of an operator. In discrete processes such as weaving and packing, machines were designed and built to make the motions that a human operator would make to produce a product. Fluid processes require devices that could hold a measurement to a target setpoint. This led to the development of PID control.
Digital computers make it possible for equipment to follow programmed procedures. Batch processes can have computers that provide procedural instructions to simpler computers in equipment that performs those functions that do not change with the product being made.
Read Also "The Changing Face of Automation Engineering"
Perhaps the most advanced automation is found in aircraft, both military and commercial. People in that field talk about situational awareness and opaque automation when discussing controlled flight into terrain. Bad things happen when pilots either are unaware of what the automation is doing or are aware and can't understand what is going on, distracting them from the real situation.
Developing Machine Intelligence
The faults of human operators could be overcome by computers that can learn from teachers and create novel solutions from known or deduced properties of the process and its equipment. While anyone who has operated a computer would find this highly unlikely, there are some amazing developments in neuromorphic processors that could make that level of computing a reality in a decade or so.
The prospects for truly intelligent computers that can learn from each other raise the possibility of machines that quickly become far more intelligent than we are. This could go badly if we have given them control of our manufacturing and utility processes, not to mention weapons. See Our Final Invention by James Barrat.
Machines Need People
Machines require maintenance performed by people carrying tool boxes and spare parts. Automating the maintenance function will require dexterous mobile machines with true intelligence. The computers that replace operators can be as large as necessary, but maintenance robots need something like Asimov's fictional positronic brain. The nearest thing we have to that is quantum computing, where things are still going slowly. I/O functions are proving to be particularly difficult.
It appears that we can't design factories that don't need humans for the foreseeable future. We need to design automation to work with people for the time being. Discrete process machines, PID controllers and the like work quite well with people. The main problem is the programming of procedures.
Normal operation is straightforward to write as a procedure. Process procedures may have 10 times as many lines of code to deal with the possible exceptions than are needed for normal operation. Accidents happen when there was no plan for what to do when the first incident occurs in a chain that becomes a disaster.
The Future: Human Language Programming
One way to allow an operator to know what the automation is doing is to write procedures that an operator can read. Combined with some indication of the part of the procedure that is being executed now, an operator can tell if the program is actually happening and what might happen next.
This will require an interpreter in the computer that can turn the written procedure into commands to equipment. This is not difficult—BASIC is an interpreter. However, BASIC is very computer-centric and mathematical compared to what is needed to express a readable procedure. The users need to be able to define the vocabulary that the interpreter will use. See my book Automating Manufacturing Operations for a complete discussion of this subject.
Success depends on a structure described in ISA 88 where product procedures command equipment modules. The modules are designed to provide process functions that are independent of the product being made. Examples are CNC milling machines, pick-and-place robots, reactor jacket temperature control and distillation columns.
The work to create the interpreter will be simpler if a group of vendors and users can agree on a user requirements specification. ISA standards committees have done this kind of work in the past, but sometimes industry organizations are faster. Perhaps the work could be completed before opaque automation causes a serious accident, as management continues to reduce the number of operators for a process.
Continue Reading
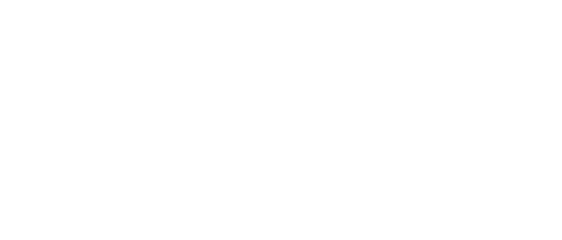
Leaders relevant to this article: