Oil & Gas Forum: Primed to exploit enterprise connectivity
Like the extreme conditions under which it discovers and extracts much of today's raw hydrocarbon feedstocks, the oil and gas industry is subject to the extremes of today's industrial challenges: unplanned downtime, regulatory requirements, employee productivity and security, as well as operational and maintenance efficiency.
"Ours is one of the most highly regulated industries in the world," said Luis Gamboa, global oil and gas market development manager, Rockwell Automation. And with oil prices now down around $40 per barrel, "We need the next level of productivity to optimize and minimize the cost of production."
Oil and gas facilities are prime candidates to benefit from the competitive advantages of connecting the enterprise. "We have smart assets in the field, smart assets plant-wide. They're more intelligent than ever, generating amounts of data we've never seen before," Gamboa told attendees of the Oil & Gas Industry Forum this week at the Automation Fair event in Chicago.
Among other things, a Connected Enterprise uses data from the field, plant floor and supply chain to drive "smart production" that is sustainable, optimized and demand-driven, Gamboa said. "Not driving around in the field, seeing whether pump jacks are operating or not, taking days or weeks to respond to a failure."
A Connected Enterprise also responds to changing market conditions, using predictive analytics to manage the supply chain, reduce risk and optimize asset performance. "It recognizes the indications, the patterns that lead to failure," Gamboa said. "It fine-tunes processes to optimize them, squeezing the most out of limited cap-ex dollars."
"Historians can be spun up offsite, configured, tested and saved as an appliance, then taken onsite and brought online in 10 minutes." Ahmad Dean, senior instruments and automation engineer for oil and gas giant BHP Billiton described how virtualization streamlines deployment, boosts reliability and eases maintenance.
It starts by connecting information technology (IT) and operations technology (OT) systems in a common, secure network infrastructure, Gamboa explained. Transactional management systems meet real-time control data: manual reports and spreadsheets are replaced with direct communications over standard, unmodified Ethernet. This makes it possible to use big data and analytics to recognize the patterns and opportunities described above.
It enables cloud computing and virtualization, which allow users to overcome obsolete hardware and limited IT infrastructure by using IT as a service, perform disaster recovery and streamline deployments and maintenance. And it supports mobility, which gives the right people all the information they need to make decisions.
But it's not easy. "Execution is a journey—and you can't do it all at once, you have to take on one thing at a time," said Gamboa. "Assess, secure and upgrade your communications. Then work the data capital: run analytics and big data tools on data you already have. Then apply the results, optimize and collaborate."
Virtualization unlocks reliability
One key enabling technology of The Connected Enterprise is virtualization. A virtual machine (VM) is a software implementation of a computer operating system (OS)—a snapshot of the computer. In many cases, multiple VMs can be run on a single server because the powerful machines are typically underused.
"VMs can help you meet industry challenges by providing increased uptime for productivity and safety systems," said Ahmad Dean, senior instruments and automation engineer, BHP Billiton. His is "the biggest company you never heard of," Dean said, a global leader in oil and gas exploration, production, development and marketing with major operations in the Gulf of Mexico, Australia, Tobago and Texas.
"The benefits of virtualization for oil and gas facilities are significant, but also apply to most operations where 24/7 uptime is king," Dean said.
Along with system reliability, VMs support disaster recovery, ease maintenance and reduce the time required to develop and deploy applications. Virtualization also eliminates problems due to obsolete hardware.
"It breaks the link between the operating system and the operating hardware—it doesn't matter what OS you have, you can run it on the same hardware," Dean said.
In a typical application, three servers run all the VMs, and all three are monitored for failures. On a failure, that machine's VMs migrate to another host. "The virtual machines come back magically in about five minutes," Dean said. "It's seamless—you don't see any bumps. Operators don't see any effects."
For disaster recovery, a virtual machine essentially becomes two files: one on the machine, one on a thumb drive or other storage device. "If a machine is lost, you can find another machine with enough power and load it back on," Dean said. "That comes in handy once in a while. We simulated a disaster on our virtualized system, and it took me about two hours to bring the system back online."
Virtualization in the field
Virtualization also simplifies deployment of configured solutions. For example, a historian can be added with no new machine to install, no concern about space, power, cooling, etc.
"A historian can be spun up offsite, configured, tested and saved as an appliance, then taken onsite and brought online in 10 minutes," Dean said. The firmware, operating system and patches can be tested before deployment.
"I typically test them for a few days before rollout so we can see any problems and fix them," he added. "When we see firmware problems—and we do—we can take a snapshot, apply patches and test the results."
Implementations will test the storage area network (SAN) and network configuration, and will uncover problems if the network was not set up properly. "In one application, we tried to use zero clients but the network was not robust enough," Dean said. "We couldn't take it down to fix it, so we went back to PCs for the clients."
The health status of all the VMs is easy to monitor, Dean said. "VMware offers one place to see the health of the system—switches, host, power supplies, networks—in one view, through a web browser."
Maintenance technicians can move a running machine from one server to another. "With vMotion software, they can put the server in maintenance mode, push a button and the VMs move to another machine," Dean said. "After they perform service and put the machine back online, the VMs migrate back. They can maintain or replace hard drives without taking the system down, with no slowdown in performance, no hiccups."
Building the data center
Virtualization calls for an industrial-strength data center. "We had to decide whether or not to roll our own," Dean said. He chose Rockwell Automation, which manages his VMware needs as well Cisco networking hardware and EMC hard drives.
"It's one place for all our needs. For a Cisco part or an EMC part, we can just call Rockwell and they handle the interaction. I don't see it, I just get a hard drive, all through one technical support number. That helps a lot."
The upfront investment is significant, but the advantages far outweigh the cost, Dean concluded. "Some will say you can buy 25 servers for the cost of virtualization, but it's the scalability and uptime advantages that make the difference."
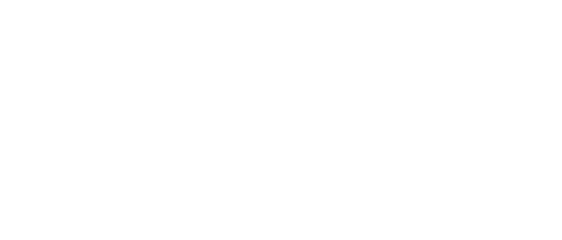
Leaders relevant to this article: