PlantPAx was introduced in 2009 as a distributed control system (DCS) offering from Rockwell Automation.
"Last year, we differentiated it by showing how it goes above and beyond the traditional DCS," said Kris Dornan, PlantPAx characterization and integration manager, Rockwell Automation. "Now, with release 4.0 coming out in March, 2016, we have made many improvements."
Speaking to attendees of his keynote address, "Process Solutions Roadmap for the Future," at the Rockwell Automation Process Solution Users Group (PSUG) meeting at the Automation Fair event in Chicago, Dornan and Jason Wright, PlantPAx business manager, Rockwell Automation, described developments driven by three goals of the modern DCS:
- To improve automation productivity (decreasing time to market and reducing lifecycle costs by automating engineering tasks)
- To enable other technologies (such as virtualization, mobility and security)
- To enhance control (to meet productivity, quality and utilization goals).
Together, Dornan said, "It's a modern approach, using common technologies and control equipment you already have."
Updated engineering environment
Engineering productivity stands to gain from an updated design environment based on Studio 5000 v24. The Studio 5000 environment combines design and engineering elements into one standard framework, one place for engineers to develop all elements of their control system for operation and maintenance.
"A splash screen allows you to get your objects into the system quickly, in a single window—a single place where you can see controllers, HMIs and servers, and set them all up." Kris Dornan described the working environment of the next release of PlantPAx, due out in March, 2016.
It extends beyond one controller to be a system-wide development and design tool. The intuitive design and configuration software package is intended to simplify development of complex control solutions, provide greater access to real-time information and support localized applications in a single control platform.
Studio 5000 Architect is an integrated engineering environment that streamlines the building of Logix and FactoryTalk View automation systems, supports reuse of content and provides seamless exchange of data between with engineering tools.
Studio 5000 Logix Designer, the progression of RSLogix 5000 software, delivers standardized frameworks for discrete, process, batch, motion, safety and drive-based systems, helping save programming time.
Studio 5000 View Designer is the design environment for the PanelView 5000 graphic terminals. As part of the Studio 5000 environment, View Designer offers enhanced integration with Logix to improve operator performance. Studio 5000 Application Code Manager is a design tool that allows users to leverage re-usable content, helping increase deployment efficiency, accuracy and overall cost savings.
"A splash screen allows you to get your objects into the system quickly, in a single window—a single place where you can see controllers, HMIs and servers, and set them all up," Dornan said. "You can drag and drop, cut and paste without having to repeat anything. You can drop logic into the controllers, screens into the HMI—it's a single place where you can build a system."
New PlantPAx features target specific process control needs.
"An Alarm Groups editor allows you to create folders for groups based on operator role, and drag and drop alarms into them," said Wright.
A backup and restore tool is integrated in FactoryTalk AssetCentre for automated backup. RSLogix Emulate 5000 is expanded to integrate to operator training, and an extension allows the integration of time snapshots and manipulation of time to expose operators to scenarios.
A new PlantPAx system estimator helps to define and size systems more flexibly. "Two new user manuals, for infrastructure and code, detail every activity with step-by-step, click-by-click procedures, and a checklist feature helps you assure your system was built according to requirements," Wright added.
"With Application Code Manager, you define the rules, and it asks you questions to define the control based on those rules," Wright said. It includes objects from Rockwell Automation process libraries to use as a starting point. Code Manager asks questions and interactively builds the code for a particular application.
"We asked, ‘What are the common strategies people use, and how can we take time out of configuring them?' And that's what we did," said Dornan. Using a typical application, Dornan demonstrated how the Studio 5000 design environment reduced the time required to program a strategy from 10 minutes to 58 seconds.
New and enabling technology
"It's all about taking advantage of new and enabling technology, like mobility, virtualization and networks," said Wright. Integration with FactoryTalk Viewpoint 8.1 eliminates the need for plug-ins for mobile. "It displays on an iPhone or iPad as well as a desktop, so operators and engineers can get what they need when they're not at a desk or in a control room."
New Stratix 5400 DIN-rail- and 5410 rack-mount network distribution switches allow complete configuration under a single architecture, "an all-Stratix architecture that bridges the IT and OT worlds," Wright said. Virtual systems are being built out with new templates including batch, I/O and more, "so you can just copy them over and deploy them," he added.
Integration with FactoryTalk Viewpoint allows system designers to publish displays with a wizard, view them on the Web, then select the ones to enable by device or dashboard. "The next generation will not be sitting at a desk working from their PCs, they'll be using their phones and tablets on the plant floor," said Dornan.
The 4.0 release puts model predictive control (MPC) in a new module, with up to a 10x10 linear model in the control layer. "This simplifies and opens up opportunities for MPC," Wright said. Other hardware releases include Dynamix 1444 integrated condition monitoring for rotating equipment; 12-channel RTD and 16-channel thermocouple cards; and two new I/O families for intrinsic safety: 1718 for Zone 1 and 1719 for Zone 2, Div. 2.
Software releases include new language libraries with Chinese, Spanish, Portuguese and French out of the box, and new objects for deadband, lead/lag and I/O module status. The Endress+Hauser Liquiline transmitter is now integrated, HART integration is enhanced, and many other improvements have been made in areas from batch and alarm to thin-client management. "We continue to tie automation to IT to get the next level of productivity out of the manufacturing plant," said Wright.
Modern DCS of the future
Beyond 4.0, Rockwell Automation is working on an HTML 5 interface for FactoryTalk Batch and AssetCentre mobile, and "Project Stanton" aims to leverage Microsoft's Project Tally technology to use mobile phones as relay points to get information to the right person in the right place at the right time.
A FactoryTalk Batch expansion intends to modernize operator displays, and Sequence Manager will execute higher-level recipes inside the controller. A new 5580 controller will be "very much faster than previous machines, adding alarm, batch, high availability and high on-board computing power," Dornan said.
"We look to our users to get feedback, to get input on what we need to be as a DCS," Dornan concluded. "The 4.0 release is specifically tied to user voting. What we do next is up to you. Install the app, take the customer surveys and let us know what you want in the way of batch, core, library and advanced control.
"For me, now is an exciting to time to be part of Rockwell Automation, to be part of the modern DCS—PlantPAx—and to make use of the technology to be more productive," Dornan said. "Consider us when you chose your next DCS."
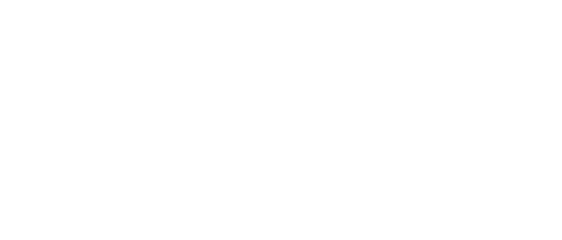
Leaders relevant to this article: