Leak detection helps wells meet OSHA PSM requirements
Peters described how he uses two technologies—dual-channel gas monitoring and ultrasonic leak detection—to help Seneca meet the OSHA PSM mandate. "Combining both technologies is a cure-all for detecting any gas emissions," he said.
The presentation started with ultrasonic leak detection. Emerson Process Management's GDU-Incus is "like a microphone—it listens for leaks, for ultrasonic sounds in the 25-100 kHz range that we can't hear," Peters said. "It's well suited for outdoor applications because it's not affected by wind or weather. The gas doesn't have to reach the detector."
The Incus has four detectors and is rated to detect leaks at a range of 40 meters (130 ft.). "I get about four times that range because of the kind of leaks I'm looking for," Peters said. It can be set to alarm at 50-160 dB, takes little power (250 mA at 24 VDC), and provides a 4-20 mA signal with three relays and an RS485 interface. "It never requires calibration," Peters said, "and it works anywhere you have pressurized emission of any gas."
HAZOPS call for leak detectors
Seneca HAZOP and HAZID studies as long as five years ago indicated very high risk, including 200 necessary action items. "Forty of them would require a device like Incus as a safeguard," Peters said. "Over the past five years, we've installed more than 90 ultrasonic leak detectors of various kinds. Now we only use Incus."
"Combining ultrasonic leak detection and dual-channel gas detection handles anything out there." Seneca Resources' Josh Peters on his company's use of Emerson sensing technologies to detect leaks and comply with OSHA PSM requirements.
As Seneca increases the number of well pads per location, the installations are covering larger areas. "We place the Incus 15-18 feet high so it can cover the full area, which can be as much as 350 ft. distant, to detect high-pressure leaks," Pierce said. In the case of a leak, technicians respond within 20-30 minutes but the Incus is also wired with visible and audible alarms so visitors can see from the gate that they shouldn't enter."The 4-20 mA signal lets us trend values, see what's going on, and raise or lower setpoints locally or remotely," Peters said. "We can disable the detector when necessary, such as when instrument techs are there blowing down flowmeters for calibration." The SCADA system notices the disabled instrument and notifies if it stays off for more than 60 minutes.
"The logic requires the noise to reach a specific dB level for a specified time," Peters said. The delay is typically one or two seconds, so truck air brakes don't set it off. The setpoints are checked by blowing nitrogen in the vicinity.
Gas monitors complete protection
To complete its leak detection instrumentation, Seneca uses dual-channel gas monitors. "These are Emerson M22 transmitters (Millennium II
Series), fixed-gas detectors that allows you to mix and match two sensors on a single transmitter," said Peters. "They're compatible with all sensor types—IR, catalytic bead, electrochemical and NE-MOS—to detect virtually any type of gas." The two sensors on a transmitter can be separated by up to 2,000 ft.
The instrumentation on the gas production units uses natural gas. "We use M22s in the enclosures, with one detector set high to detect natural gas leaks and one set low for condensibles," Peters said. He uses them outdoors on vapor recovery units, and on tanks both near the hatches to detect gas and near the ground to detect condensibles.
"You can use the M22 anywhere you need more than one gas detector, which is pretty much anywhere," Peters said. "Every location I have is a multi-detector installation. We've installed over 400 point detectors over the past five years."
Peters described an increasing need for simultaneous operations (SIMOPS), where wells continue to produce while adjacent wells are refitted or new wells are drilled. SIMOPS can mean an additional 3-50 MMCF/day of natural gas. When this is done, "You need to be thinking about PSM," he said. "We add more instruments to be sure of safe operation. I use my own wireless system to temporarily add more detectors wherever EHS thinks we need them."
A winning combination
"We use the Incus for outdoor, high-pressure leaks and the M22 inside for low pressure leaks," said Peters. "Combining ultrasonic leak detection and dual-channel gas detection handles anything out there."
The combination ensures safe operation and shut-in of potential catastrophic failures, meets many of the elements required for OSHA PSM mandates, and lets Seneca keep wells flowing while simultaneously performing other operations.
"Multi-detector installs save money by using dual transmitters as opposed to multiple single transmitters—they save more than 60% vs single transmitters," Peters said. "It's not why I chose them—I went to them because they're reliable, capable and rugged. And by the way, you can use two detectors and save money."
Latest from Safety Instrumented Systems
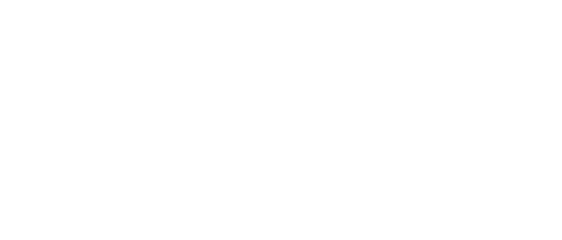
Leaders relevant to this article: