Major flare gas recovery project delivered on time, on budget
With shrinking budgets and higher expectations to do more with less, large capital projects are more at risk than ever of failing to deliver on time and on budget. As projects become larger and more complicated, relying on a project management team to manage suppliers, each with their own work methods, standards, communication tools and reporting processes, is becoming a thing of the past.
Projects now require one integrated team to provide a complete instrumentation, control and safety system that can seamlessly interface with vendor-supplied packages and electrical systems. In the oil and gas industries, this is the only way large organizations can efficiently manage project development costs, and provide safe and controllable systems that will integrate with their clients’ systems.
Ending routine flaring
At Qatargas, the world’s largest liquefied natural gas (LNG) producer, we have experience with using an integrated team to deliver large-scale projects. Officially inaugurated in April 2015, our Jetty Boil-Off Gas (JBOG) Recovery Project is the biggest project of its kind and one of the largest environmental investments in the world.
[javascriptSnippet]
That same month, the major oil companies partnered with government and other officials from oil-producing countries to work toward ending routine gas flaring at oil production sites by 2030. This partnership, Zero Routine Flaring by 2030, will end the unsustainable process of routine oil gas flaring as soon as possible and no later than 2030.
[sidebar id =1]As part of its participation in the Zero Routine Flaring program, the State of Qatar needed to minimize flaring nationwide. This initiative was translated by its Ministry of Environment (MoE) into conditions inserted in the Consent to Construct for LNG trains at Ras Laffan Industrial City (RLIC) (Figure 1). RasGas obtained a waiver from MoE to allow RasGas and Qatargas to operate trains if the JBOG recovery project was implemented. With Qatargas producing 42 million tons of LNG per year, it was essential for us to reduce flaring from our LNG trains to align with the national focus on flare minimization, and reducing emissions and carbon footprint. Because gas flaring impacts the environment by emitting CO2, black carbon and other pollutants, miniming the impact of LNG production was a top priority.
Moreover, flaring is simply wasteful because it discards a valuable fuel source that can be used in applications worldwide. Savings from the JBOG project can power the equivalent of more than 300,000 homes each year.
Boil-off recovery basics
The JBOG recovery system minimizes flaring at all six LNG berths at Ras Laffan with a vapor recovery system that compresses gas for fuel to the fullest practicable extent. A study in 2006 showed that boil-off gas recovered from three simultaneous berth loadings achieved a recovery rate of up to 97.7% of projected berth flaring, which is based on 78.3 million metric tons per annum of total LNG production. Updated studies during front-end engineering and design (FEED) stages indicated the JBOG recovery rate will be around 90% of the boil-off gas generated.
[sidebar id =2]The JBOG Recovery Project is owned by all of RLIC’s LNG-producing ventures and facilities. During construction, ConocoPhillips provided staff to execute the project, together with others from Royal Dutch Shell. Also, Fluor provided engineering, procurement planning and management services. Commercial discussions during the FEED stages led to ownership proportions based on estimated amounts of JBOG that each owner will produce. On behalf of RLIC’s owners, Qatargas was entrusted by Qatar Petroleum to oversee development and eventual operation of the JBOG project.
The largest component of the project is the 2 x 50% BOG compressor system, located in the central compressor area (CCA) near Lot H (Figure 2). In all, there are three sets of compressors, including two low-pressure (LP) BOG compressors, two middle-pressure (MP) BOG compressors, and two high-pressure (HP) BOG compressors to handle all gas recovered from the six berths.
Completion of the $1-billion JBOG project is the first stage of flare reduction at RLIC. Its objective is minimizing flaring at the LNG terminal by recovering the gas flared during LNG loading at the six berths at Ras Laffan City Terminal. The project is designed to recover all JBOG generated during three simultaneous bulk loadings of ships in port, and its JBOG system can recover up to 163 tons of gas per hour. With all producers generating about 77 million tons of LNG in 2011, flaring at the terminal averages 0.7 million tons of gas per year or about 100 million cubic feet per day (mmscfd). The JBOG project will result in a 90% reduction in flaring at the six berths. Also, flare management and reduction strategies implemented by the JBOG project will position Qatargas for future opportunities to monetize carbon emissions in a global carbon trading market.
{pb}
Coordinating controls and suppliers
Because of its critical priorities, the project team at Qatargas knew successful implementation of the JBOG project hinged on delivering it on time and on budget. The main obstacle to successful implementation was integrating three existing control systems and several vendor packages, and coordinating suppliers, programmers and engineers. The JBOG team needed to reduce conflicts from dealing with multiple EPCs.
To simplify this multivendor process and develop one point of contact for our project team, we contracted with a main instrumentation and controls contractor (MICC) at the start of the project to organize implementation, ensure proper configuration, and avoid costly miscommunications or miscalculations between vendors. Because of our excellent, longstanding relationship, Qatargas contracted with Emerson Process Management for all MICC services from FEED through implementation, commissioning and training. The JBOG project’s FEED began with Emerson in Houston during fourth quarter 2010 and was completed in first quarter 2011. The three control systems integrated by the JBOG team included:
- DeltaV DCS covering berths 4, 5 and 6, and storage tanks in Lot N;
- Foxboro control system covering berths 2 and 3 and Lot H flaring; and
- Separate Foxboro controls covering Berth 1, a Qatargas tank farm, and a legacy fire and gas system.
All field devices, either HART or Foundation fieldbus, were connected by PlantWeb using Emerson Asset Management Suite (AMS). A new DeltaV DCS controlling the new plant area and Qatargas berth interfaces was integrated with existing DCSs controlling the RasGas berth interfaces. These systems were integrated with the separate, existing safety system to meet Qatargas safety standards.
[pullquote]The MICC oversaw programming of the new DCS and safety systems, and subcontracted programmers to integrate controls from different vendors. It also handled interface programming with vendor packages and connections to the electrical system to start/stop equipment motors, and managed plant controls and interfaces to berths and gas plants.
Contractor aids project team
Design of the JBOG project control system began in December 2011. Because of planning completed at the FEED stage, detailed designs were produced smoothly. Much of the FEED work already included relevant design philosophies, concepts and system architectures. Final acceptance testing (FAT) was delivered in October 2012, and the JBOG system started up in October 2014. Just a year later, it had already recovered gas from 1,000 ships.
For our project team, the main benefit of the MICC was that, despite three control systems and many vendor packages, we only had to deal with one contractor for all control and instrumentation issues. This let the team focus on overall project design and construction, while the MICC ensured different interfaces were programmed consistently and similar to existing systems. Because the project team worked closely with the MICC from the beginning, we overcame many issues of tying into existing systems. In many cases, special assistance facilitated integration and the MICC coordinated it. At one point, the MICC deployed 36 people from its organization and other DCS, safety, and fire and gas system suppliers.
The MICC’s value was also shown when challenges arose. One was fast-tracking cabinet and console assembly to meet a short delivery schedule. The MICC met target first delivery in June 2012, arranging for marshalling cabinets to be onsite early for installation and field wiring. The remaining cabinets were left in the staging area to enable system integrated factor acceptance testing (SIFAT), which allowed overall control system testing by simulating compressor control system startup, operation and shutdown.
[sidebar id =4]
Finally, the MICC gave our project team access to other resources we couldn’t access alone. It could fly in small parts for tie-ins to DCS equipment in older control rooms. We also needed seal gas rings for valve repairs, but they weren’t immediately available, and waiting would have put the JBOG project behind schedule, so the MICC sourced more from the U.S. and U.K. It also sped up production in India to cut the wait time from months to a couple of weeks. Having a partner that could coordinate between multiple suppliers and our team to provide fast resolution for repairing these valves was critical to keeping us on schedule.
As a result, our MICC not only saved Qatargas money, but also helped us deliver a streamlined, efficient facility at the forefront of environmental performance. Recovering 90% of the boil-off gas formerly flared at the six berths will let them function as part of a common facility, streamlining operations and simplifying management. This will result in a reduction of 1.6 million tons of CO2 per year.
Qatargas takes its corporate responsibility seriously. Having seen the results of our JBOG project, we’ll continue to encourage other LNG facilities to follow the model of this milestone project. Many of the pitfalls and delays that plague massive projects were a great concern when we began this project, but our MICC gave us the support and resources to anticipate and avoid traps that lead to missed deadlines and cost overruns. We estimate our MICC startup program saved as much as 30% of the time over a traditional startup without an MICC.
[sidebar id =3]
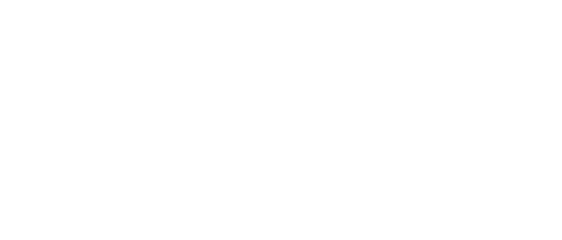
Leaders relevant to this article: