Plantman Go: The future of asset lifecycle modeling
Bob Sperber is a frequent contributor to Control.
However, are owner-operators ready for them? While some might be deemed bleeding edge, it may be time for process industry people to upgrade to a fuller realization of today’s lifecycle solutions.
Waking up from history
Because process facilities have been burdened for many decades with persistent problems reducing efficiency, safety and profitability across their lifecycles, it's often assumed that these difficulties are the unavoidable price of doing business. Project timelines and budgets are still routinely blown due to the inability of partners on capital projects to handle late-stage changes between design and engineering teams, training methods that can’t keep up with generational shift as older, experienced professionals leave the workforce, a lack of IT integration, and other sources of waste and inefficiency.
However, despite the process industries’ fabled resistance to technological change, such issues are reaching a tipping point because ever-larger projects can't be executed without more and better collaboration between partners, including in-house staff, outside engineering, procurement and construction (EPC) contractors and automation providers. Jim Nyquist, president, systems and solutions, for Emerson Process Management, reported at last fall's Emerson Global Users Exchange that, “Today, 65% of projects worth more than $1 billion and 35% of projects under $500 million fail, where failure is defined as at least 25% over budget and/or late by 50%.”
Another major issue is that 61% of owner-operators “lack complete confidence in their ability to find information needed to support response to an emergency,” and more than half spend 20-80% of their time just finding and validating plant information, including conducting walk-downs, according to a survey of 185 process industry professionals performed by TechValidate for Intergraph.
[sidebar id =1]The shame of these findings is that even with slightly older, 2012 technology, data can still be made much more accessible. Royal Dutch Shell and Qatar Petroleum, for example, have standardized handover of instrumentation data using Intergraph’s SmartPlant Instrumentation software for their $18-19-billion Pearl Gas to Liquids (GTL) facility in Ras Laffan, Qatar (Figure 1). At full capacity, it converts 1.6 billion cubic feet per day of natural gas into 140,000 barrels per day of GTL products such as gasoil, kerosene, base oils, naphtha and normal paraffins, as well as 120,000 barrels per day of natural gas liquids and ethane.
Pearl GTL's engineering instrumentation database holds 150,000 loops, 350,000 instruments and 90,000 data sheets from roughly 25 contractors. During design and construction, about 200 users collaborated via this software environment's secure, online Citrix channel and the Internet to access its database 24/7.
This is a step in the right direction, especially when it comes to the critical handover of data custody from the EPC, working in the capital expenditure phase of a project, to the process plant's owner-operator who must use that data for the operating expenditure (OpEx) phase—meaning the life of the plant from startup to eventual decommissioning. The next steps toward a solution include greater integration between automation and design/engineering/CAD platforms.
Automation’s upfront role
To help users adopt more comprehensive asset lifecycle models and methods, many automation suppliers have become more vertically integrated as they add consulting services to, in effect, become EPCs at the automation level. For instance, Honeywell Process Solutions offers its Lean Execution of Automation Projects (LEAP) service and technology. It encompasses software-configured universal I/O and cloud-based access to virtualized control system engineering data—and a mix of management methodologies—to produce estimated savings up to 30% in capital expenditures (CapEx) with a 25% savings in time and scheduling. Honeywell reports an upstream oil and gas platform’s “typical benefits” with LEAP can be $30-60 million through reduced production losses and unplanned downtime, and increased safety and regulatory compliance.
“We do all our projects in the cloud now. We call it a virtual engineering environment," says Jack Gregg, director of product marketing for Honeywell's Experion automation platform. "And it's no longer just for projects, but for operations as well, where a large part of your control system is running in the cloud.” Engineers use it just as they would if it were mounted on a hard drive, giving the vendor the ability to be the long-term administrator for updates and patches.
[javascriptSnippet]
Similarly, Emerson’s Project Certainty, which in part resulted from Emerson’s 2014 acquisition of Management Resources Group, led to a merger of consulting and technology that targets project inefficiencies with a mix of services, methods and technologies. These capabilities include unified project documentation and information (including tag databases and instrument indices) from multiple sources. Project Certainty also uses Emerson’s Characterization Modules (CHARMS) and Smart Commissioning technologies for electronic marshaling with smart junction boxes, which reduces commissioning time for HART and Foundation fieldbus devices by up to 80%. It also employs reusable, virtualized configuration templates and built-in validation reports through reusable, virtualized configuration templates and built-in validation reports.
“The big end users are saying to us, ‘Guys, you’ve got to work with our EPCs and figure out how to bring costs down and make our projects more efficient,’” says Jason Sarnataro, an Emerson operations manager with Project Certainty. He adds its innovations are “more efficient, more streamlined and cheaper” than traditional methods. End users are asking Emerson and the EPCs to eliminate "long, labor-intensive steps that lead to projects being behind schedule and over budget. Now, we’re able to decouple our final end devices from software configuration, so we can give EPCs the information they need to complete their 3D models, and the system will automatically sense the end devices in a more parallel activity rather than in a linear series of activities like in the old days.”
Michael Kane, vice president of technical services at Sasol North America, adds that, “Project Certainty will enable Sasol to reduce rework, improve spare parts inventory and working capital, and reduce training costs.” The company’s $8.9-billion ethane cracker and multi-plant complex in Louisiana, slated for completion in 2018, will more than triple its U.S. chemical production capacity.
The EPC for Sasol's project consists of a joint venture by Fluor Corp. and Technip S.A., which are designing it using Intergraph's Smart Plant software. To incorporate flow, valve and other inline instrumentation into the EPC's 3D models, Sarnataro says his team is providing dimensional data and building templates to feed SmartPlant Interface (SPI) data from Emerson's DeltaV DCS, Fisher Rosemount valves and other instrumentation. All parties can then “use those templates to get data out of the SPI, and also to get data back. And the EPCs will use that information to build their model of what the plant will look like.” The same routines will interface with Sasol's safety instrumented system, plant asset management and added instrumentation.
“When you talk about 3D models, there’s not really a DCS piece in the interface, but the data works directly with the SmartPlant instrumentation, which goes directly into the [EPC’s] 3D model,” which has various modules for electrical, P&ID, instrumentation, Delta V and more, says Ron Mitchel, instrumentation and electrical technical consultant at Emerson and I&E core lead for the Sasol project. The resulting configuration data, shared via an XML file, is exported directly to the SPI, “which keeps us from having to manually export all that data. We can export our database directly to an XML file, with some added Excel add-ons, and import that directly into the SmartPlant software."
{pb}
Design-engineering interfaces
Automation suppliers routinely develop interfaces to meet specifications from CAD/engineering software developers. From that initial coding, and added dimensional data from the automation vendor, “we automatically create the 3D model that can be placed in the 3D design for the right ISO extraction, interference and so on,” explains Frank Joop, executive director for business development at Intergraph.
Another path to more open integration could come from standardized communications. OPC UA provides some “glue,” as does general Open Data Protocol at the application level, but more specific efforts are underway. One targeted effort is by ISO 15926, "Industrial automation systems and integration—integration of lifecycle data for process plants including oil and gas production facilities." Industry-wide adoption would allow dynamic information-sharing of automation and process data with plant design software environments, supplier databases and other applications—without the need to communicate through proprietary interfaces.
In fact, Siemens used ISO 15926 for the “OpenPlant Engineering Adapter” interface it introduced in May between its Comos lifecycle engineering software and Bentley Systems’ Open Plant software. However, Joop warns that ISO 15926 is incomplete, so there’s no true interoperability or openness, or widespread industry adoption yet. The same goes for a collection of related standards and organizations, which include Standard for the Exchange of Product (STEP) Model Data (ISO 10303), Fiatech, ISO, iRing Tools User Group, Mimosa and the Germany-based Data Exchange in the Process Industry, which is similar to ISO 15926.
[sidebar id =2]Even if interfaces remain proprietary between automation and engineering design systems, user and industry demand can still create a groundswell for better integration of P&ID data, instrument design, electrical design and dimensional data to foster more and better 3D modeling. A lack of standards is no excuse to hold off on technology.
For instance, Australia-based gas producer Santos Ltd., in partnership with Malaysia's Petronas, France's Total and South Korea's Kogas, has adopted Intergraph software to manage specifications and corporate standards for its Gladstone LNG plant in Queensland, which started production this spring, and has “continued to reduce costs for new designs and management of change on existing facilities,” according to Shaun Barclay, GLNG upstream information manager at Santos. The system allows replication of standard, as-built designs to speed access to procurement, construction, commissioning and other data needed for facility maintenance for the next 25 years (Figure 2).
Handover history
While the process industries have been moving from raw data to 3D design, CAD vendors have spent close to 50 years perfecting 3D CAD software, and are now backfilling their portfolios with capabilities ranging from lifecycle engineering platforms to point-cloud integration with project, process and automation data.[sidebar id =6]Likewise, since the 1970s, building information modeling (BIM) software has been enriched by continually improving graphic models with lifecycle information for complex civil, commercial, residential and industrial projects. These efforts have led to Open BIM standards for enhanced collaboration and increased interoperability. And while BIM focused on “plant information management and the notion of a digital plant, its emphasis has also shifted toward product lifecycle management (PLM) and asset lifecycle information management (ALIM),” says Anne-Marie Walters, process industry marketing director with Bentley Systems.
As a result, easier integration has made it simpler for plant owner-operators to take over more EPC tasks, which also may have contributed to shifts in the CAD/engineering software market. In the past 10 years, upwards of 80% of engineering and design system sales were to EPCs, while "it’s about 50/50 today,” reports Dick Slansky, senior analyst with ARC Advisory Group, which developed the ALIM acronym. He adds that EPCs need to deepen their expertise to better combat cost overruns and blown project milestones—in part by integrating complete project datasets that alleviate handover of project data custody from the CapEx phase of a project to the open phase. Slansky adds that new ALIM-type systems allow this, and that the value of such integration work goes far beyond the engineering phase of a capital project. “It’s when you move over into the procurement, materials management and construction phases; that’s where the [big] money is and where plants need the information from design,” says Slansky.
Walters adds that, “I've seen a shift. EPCs bring a lot more to the table than just design, procurement and construction.” She reports that EPC MWH Global won a contract to design, build and operate a water treatment system in Taiwan, and promised "We'll run your water system for 35 years. We'll guarantee that the water will cost 'this much,’ and then we'll hand it over to you.” In such cases, it benefits EPCs to add value and manage handover efficiently, so they don't lose profitability, especially as western EPCs have to compete more with lower-cost EPCs from other countries such as India.”
Research funded by Intergraph found that plants store facility information across a disjointed patchwork of engineering information systems (54%); enterprise content management systems (42%); shared drives (39%) and ERP or CMMS databases (27%). To a lesser degree, Intergraph found that data are still accessed via hard copies, isolated central or department or archives, and requests sent to company document managers or librarians.
Worse, Slansky reports meeting an operations guy from Shell, and asking him how data handover was typically handled from upstream design personnel to operations. The Shell employee told him, "Imagine an 18-wheeler pulling up to a large loading dock, and dumping pallets and pallets of 2D drawings. It isn’t even organized. It’s like a great big pile of stuff. We gotta get away from this!”
Unified remedies
Fortunately, integrated asset lifecycle systems such as Intergraph's SmartPlant for Owner Operators target a “single source of the truth.” This is similar to what a DCS promises, but these systems function at a more expansive level, encompassing a model of the physical world from the site’s grounds to the plant, process and, ultimately, automation system. Done right, the result is cloud-enabled, anytime, anywhere data access across enterprise, operational and partner systems.
Types of data covered by these new asset solutions include facility design; automation systems managing P&ID, electrical and instrumentation; historians; health, safety and environmental (HSE); enterprise content management; and asset/maintenance systems. This allows users to navigate between 3D models created at a workstation, graphics based on photos and photorealistic laser scans, and all underlying data, including hot-spotted schematic drawings linked to related vendor documents.
For example, Atlanta-based electric utility Southern Company sought to overcome handover problems by using Bentley's AssetWise ALIM software to access its Maximo computerized maintenance management system. This utility ended up with “true asset lifecycle information, enabling seamless handover of project information to operations,” according to Ted Weitzman, project manager at Southern Company. The seamless aspect includes unified design procedures, standards and guidelines across all engineering disciplines and outsourcing partners, which has saved hundreds of millions of dollars during one plant’s operational lifecycle due to reduced time spent seeking asset information required to execute its reliability maintenance program, plus added savings in man-hours and safety performance. The system is presently being integrated with Southern Company's internal materials management system to ensure physical asset alignment with design functional tags. Overall, Bentley reports its asset data handover solution that began at one pilot plant in 2013 currently supports $5 billion in project work for seven plants.
{pb}
Go further with 3D
While process automation firms have increasingly invested in 3D modeling for design and training, it's rare for users to completely bridge the gap between project work and a complete, soup-to-nuts virtual environment. However, even though large process industry projects can take up to five years to design, remote 3D training “is starting to pick up,” says ARC's Slansky, especially because it’s not feasible to wait for a facility to be completed, and it’s difficult to shuttle trainees to remote locations. He adds major process firms including ExxonMobil, Shell and Total S.A. realize this, and the latter “has gone 100% 3D with its training simulation. This includes graphics that are accurate and amazing, thanks in part to advances in gaming software graphics and physics, including their use of virtual reality (VR) goggles and game controllers.”
[sidebar id =3]On the automation engineering side, Siemens’ acquisition in 2012 of Belgium-based VRcontext International S.A., including its flagship WalkInside software, is one example of 3D technology supplementing an automation vendor’s lifecycle engineering offerings—in this case, Siemens’ COMOS platform with immersive 3D visualization and virtual reality capabilities. It can be used in training well ahead of startup, thanks to virtualization of control strategies. And, with the current state of platforms, a full cloud-based global implementation of this technology allows real-time collaboration across all disciplines and through all phases of plant lifecycles for owner-operators, EPCs and automation partners (Figure 3).
The business justification for 3D assists to asset lifecycle management appears sound based on research. Siemens reports 3D-based training produces a 78% trainee retention rate, far greater than more traditional methods. Personnel can learn standard operating procedures and HSE requirements to prevent abnormal situations and incidents well before facilities come online. This business case is further supported by eliminating manual engineering chores, reducing risk of errors, and speeding deployment of control and maintenance strategies from initial designs and troubleshooting to lifecycle upgrades.
On the plant design level, Bentley recently acquired Acute3D, which produces a photogrammetry or photo-meshing system that surveys and maps to measure distances between objects. When brought into an engineering design, this technology automatically converts any amount or depth of digital photos into scaled, 3D meshes of facilities from aerial views to detailed views of specific plant assets. It claims to have more granular capabilities than a static point cloud or a one-time laser scan of assets of a facility. The closer users are to an object photographed, the greater the resolution of the mesh becomes, whether it's field device or an overhead plant view (Figure 4).
[sidebar id =4]In addition, other automation suppliers provide immersive 3D training simulators across the lifecycle, “modeling the plant before it’s been built, so you can test your control strategy to makes sure the physical design of the plant matches the control strategy that you built into the software,” says Honeywell’s Gregg. The company’s 3D simulation capabilities include its UniSim operations training simulator, which is the result of a partnership with FieldOp3D immersive training simulator for field operations from SNC-Lavalin Global Training and Simulation.
As far as "how 3D” asset lifecycle solutions need to be, they don’t have to go all the way to offer benefits. Bentley's Walters says plant personnel don’t have to don goggles, but can be maintain plants using iPad applications with augmented reality functions that combine geolocation with added data. "This can be a total game changer for maintenance, serviceability, for everything," she says. "Once the maintenance technicians can put on their [3D] glasses and walk the plant with an iPad, they’ll have instant access to all the engineering information they need. They’ll no longer have to go out to some office and try to find the right set of engineering drawings, maintenance manuals and service bulletins, and then try to figure out how things relate to the asset they’re trying to service. They can have their smart goggles or even their tablet, and have all the information they need, instantly.”
Emerson’s Mitchel adds it’s possible “to build a 3D virtual plant environment that gives operators a real-time view of the physical environment, but it depends on how far you want to model that environment, and how much money a customer wants to spend." EPC’s 3D designs include process simulations, and interfaces to control companies most often "touch each other at the control device level, which needs to be in the 3D model for the EPCs to complete their model.” At present, however, full instrumentation data are not typically included in the 3D models, which largely depend on the desire of process plant customers to justify the cost of a full, working 3D model of the entire plant.
[sidebar id =7]
Intergraph’s Joop notes the cost of virtual reality or fully integrated, immersive, 3D models may be too expensive for many companies to justify, but using laser scanning to create 3D models at plants has become “really cost-effective,” as has the cost of maintaining 3D models. “Plus the combination of the 3D model and the asset information, with the augmented reality and the integration between 3D, P&ID, control systems data and maintenance, make the value proposition much more attractive,” explains Joop, who adds the benefits of 3D are also becoming more evident as owner-operators seek to reduce costs and safety risks.
As a result, there are some areas where 3D technology is becoming more commonplace. Instrumentation vendors already maximize field technical productivity by loading ruggedized mobile devices loaded with DCS and asset management software to allow technicians to accomplish instrument configuration without calling back to the control room to do chores such as stroke valves during tests. Another innovation isn’t necessarily 3D, but includes photos with hot links that allow workers to use wireless laptops and tablets to work with limited 3D capabilities for faster, more efficient field work—from testing and commissioning through operations across the life of the plant.
Latest from Asset Management
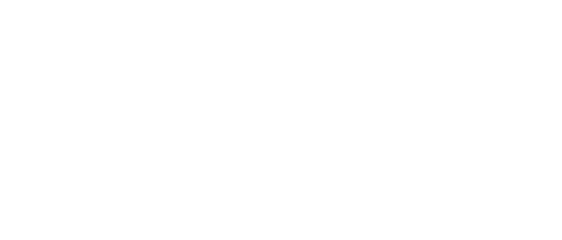
Leaders relevant to this article: