Training simulators smooth operations
One of the earliest applications for simulator-based training was to train airplane pilots. Today, simulators are used to train people across many professions, including as health care (e.g., for surgeons), aviation, military, aerospace, shipping, nuclear, oil & gas, chemical and many other industries in which workers have high levels of responsibility with the possibility that mistakes could result in harm to people, equipment and/or the environment.
Although a well-rounded program that includes classroom, online and on-the-job training is important, ongoing research indicates that for operations and other personnel in many types of industrial plants and facilities, operator training simulators (OTS) can be particularly beneficial. This is because simulators enable operators to practice operations in a situational context. Unlike training on live control systems, operator training simulators can be used to practice real-life scenarios (both normal and abnormal) without the risk of adverse consequences. In addition to gaining an understanding how the plant functions, simulators can enable workers to learn how to solve problems and make better and faster decisions.
Research has shown that companies that have utilized simulation in training have workers that learn faster, retain information longer, and perform much better than workers who have only been trained through more traditional training such as on the job, on-line, or classroom training.
ARC Advisory Group recently conducted a research survey in conjunction with Control to develop a better understanding of how industrial organizations today utilize operator training simulators (OTS) and the specific benefits they accrue. The survey examined various types of OTS simulation solutions used today, current implementation practices, reasons for implementing, training methods, and specific benefits.
This Insight highlights selected findings from the survey, focusing on the responses received from end users with actual OTS experience. The majority of participants were from the oil, gas, chemical, and petrochemical industries. The energy and nuclear industries were also represented. ARC clients will also receive a more detailed report on the survey findings in the near future.
Top benefits from implementing OTS
The survey examined the top benefits received from implementing OTS. Survey participants were allowed to choose up to five answers (top choices are shown in graph and all choices are listed in the table).
The top benefits from implementing OTS identified by respondents include:
- Smoother startups, shutdowns and transitions
- Fewer abnormal situations, trips, incidence avoidance and troubleshooting skills
- Improved process knowledge capture and transfer
- Improve process safety, & reduce risk & liability
- Test operational modifications & process control before
The number one reason given for implementing OTS was to obtain smoother startups, shutdowns, and transitions. Operations teams today do not always get the hands-on training needed for starting up and shutting down a plant and although technology has made it easier to capture procedures, critical plant information is not always easy to obtain when it counts the most. For plants that startup and shutdown frequently, just the cost savings from avoiding equipment damage can help justify the OTS purchase. One person ARC interviewed estimated that the savings could be as high as $10,000 to $50,000 per day in a coal-fired power plant. Another estimate given was that plants can save as much as $300,000 to $400,000 per startup.
Respondents also indicated that improving process safety and reducing risk and liability was another major OTS benefit realized. Lower risk can mean lower liability and even lower insurance costs in some cases. Another benefit was to test operational modifications and process control before implementation. Companies benefit from using an OTS system for factory acceptance testing and checkout and optimizing the process control system prior to and following startup. One end user told ARC that by using the OTS for testing they were able to obtain a ROI before startup.
How OTS are used
According to respondents, the number one reason for OTS usage is to train operators before startup. This aligns with the top benefits given. The number two reason is to respond to abnormal situations. The third most popular reason give is for troubleshooting. In fact, some companies have received ROI by identifying potential issues before startup.
Many industrial accidents occur because of insufficient training on automation equipment, instrumentation, or in safety procedures for operations and maintenance. Operators must be trained for emergencies so that they know how to respond to process malfunctions or other abnormal events. Operator training simulators offer one of the best methods to provide this training.
A well-publicized explosion at a refinery in Texas in 2005 that occurred while starting up an isomerization (isom) unit killed 15 workers and injured more than 170 others. The company had to pay more than a billion dollars in fines to compensate victims, suffered millions of dollars in equipment damage and lost production, and took a major hit to its reputation. ARC research indicates that “training for startups” is the number one benefit from OTS training.
The accident at this particular plant involved the startup of the isom unit where instrumentation issues and inadequate safeguards, combined with inadequate supervision, procedural and human factors issues, miscommunication, and inappropriate operator actions, resulted in the fatal explosion. The investigation, documented in a Chemical Safety Board video showed that operator training was insufficient and that the company had not invested in simulators. Ironically, the CSB accident investigation team made extensive use of simulators to understand how the accident occurred. Lack of adequate training was also cited in a number of other CSB accident investigations.
Training with high-fidelity simulations that incorporate the control system user interface and control strategies in a virtual environment would have been particularly effective for preventing this type of accident. In addition to training the operator, such simulations would challenge the written startup procedures as well as the suitability of the field instrumentation and the control, alarming, and shutdown strategies. OTS system users report that training activities also often also serve to test DCS displays, controls, alarming, and shutdown strategies and often leads to improvements in both safety and ease of use.
Multi-faceted training programs most effective
Interactive operator training simulators that simulate the real-world environment can help improve training and ensure that workers retain and gain confidence from what they have learned. Process and control engineers should be closely involved in the development and use of the OTS. The OTS platform can also be used to effectively test controls, alarms, displays, and shutdown strategies.
However, ARC believes that companies should continue using a multi-faceted strategy that includes traditional classroom training, computer-based training, and simulator-based training. Emerging training approaches that incorporate gaming and 3D visualization technologies should also be evaluated.
ARC has published numerous reports operator training simulators, operations training, training technologies, and training strategies and will continue to research and report on these important topics for our Advisory Service clients. ARC is planning a dedicated session on operator training simulators at the upcoming ARC Industry Forum in Orlando, FL, Feb. 8-11, 2016.
Janice Abel is a principal analyst for ARC Advisory Group. She performs research and provides consulting services for clients in process and discrete industries. Mrs. Abel focuses on enterprise manufacturing intelligence, manufacturing execution systems, supply chain integrity, simulation training and other areas. Mrs. Abel has published numerous articles on these topics. She has over 25 years of experience in industrial automation, regulatory requirements, enterprise control, performance improvements and operational excellence. Mrs. Abel has a Master’s Degree in Chemical Engineering and an MBA.
Rick Rys is a Senior Consultant in the analyst group at ARC. He performs research and provides consulting services related to the process industries and other emerging technologies. Mr. Rys focuses on Process Technology, Energy Production (including renewables), Process Control, Optimization, Process Modeling, Simulation, Sensors, and data analysis applications. He has published numerous articles on these topics. He has over 35 years of experience in the roles of control system engineering, software application development, and field commissioning. He has a BS in Chemical Engineering and is a registered professional engineer in Massachusetts.
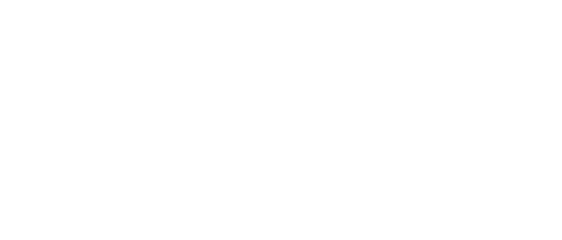
Leaders relevant to this article: