[sidebar id =1]
The University of North Carolina (UNC) at Chapel Hill was spending too much time and money supporting an existing control system. That’s unacceptable for UNC Chapel Hill, which has nearly $1 billion in annual research expenditures, and ranks eighth in research activity among public and private universities in the United States.
Much of this research is done in about 1,000 cold, warm and freezer chambers located around campus. Some chambers store millions of dollars worth of products, while others perform critical research in life science. In many cases, chamber temperatures must be controlled accurately to within 0.5 °C due to the controlled experiments inside.
Many research chambers at UNC were installed more than 20 years ago, and it was becoming difficult to find parts for the controllers used to control temperature and other variables (Figure 1). During maintenance of one particular chamber, UNC staff couldn’t find a supplier to repair a malfunctioning temperature controller. This maintainability concern was recognized as a possible campus-wide issue since many of the chambers were put into service at about the same time.
In addition, needs were expanding, with researchers requesting tighter, more accurate temperature and humidity control, and the ability to view temperatures in real time. None of these requests were possible with the old control and monitoring systems. Investigation showed it would be too expensive to upgrade the existing proprietary systems, so the university sought a more affordable and flexible solution.
After speaking with many system integrators wanting to employ proprietary programming technology, UNC Chapel Hill decided to work with Affinity Energy after hearing about the company’s open-system PLC integration for critical systems.
Universal open system
Several types of hardware were used to control the chambers. Each performed essentially the same functions, but there were changes in newer iterations of cooling technologies. Affinity Energy designed a customizable, universal panel prototype to regulate temperature in all of UNC’s chambers, regardless of the existing controller or cooling technology.
There are three types of heating or cooling systems in the chambers, distinguished primarily by solenoid valves controlling liquid or hot gas, or by proportional valves controlling liquid, hot gas or reheat. Solenoid valves operate differently from proportional valves, so different control methods are used, as well as different program logic. This is typically addressed by using a controller specific to the type of valves, so a controller for solenoid valves couldn't be used on a chamber with proportional valves.
A primary goal of the project was to find a programmable logic controller (PLC) that could be used in any of the chambers, regardless of the devices being controlled. This first controller was considered a prototype since it would have to be used in many different chambers.
After extensive hardware and controller research, UNC Chapel Hill and Affinity Energy specified AutomationDirect PLCs. Because AutomationDirect’s PLC programming software is open, the university wouldn’t be held hostage to proprietary software or a single system integrator’s services if they wanted to adjust or completely overhaul the system in the future.
Control plus visibility
[sidebar id =2]
Previously, researchers had only rudimentary indication of a room’s temperature, and in case of failure, there was no indication until opening a cold room door and feeling a blast of warm air. The old controller also had significant fluctuation between setpoint thresholds. Affinity Energy designed a temperature control system using AutomationDirect’s Do-more PLC (Figure 2).
The new controller provides smoother and more accurate control than the legacy control systems. The controller enclosure is built with the PLC and other control devices (drivers, relays, etc.) as a unit. Field devices are wired to terminal blocks included for connections, and the panel is mounted on a wall outside the environmental chamber.
The Do-more PLC is fast, has plenty of memory, and includes multiple communication options such as serial, USB and embedded Ethernet. It can be configured for several separate Ethernet communications ports, each running multiple protocols. Do-more PLCs are programmed with Do-more Designer software, which is available free online.
Affinity Energy also installed an AutomationDirect C-more human machine interface (HMI). This color touchscreen monitor displays data points such as temperature, humidity, defrost cycle activity, and liquid line and hot gas valve status. The HMI is installed in the door of the custom-built enclosure, and is located outside and beside the chamber entrance door.
The main HMI screen displays the temperature in the room and alarm indicator (Figure 3). It also includes status indicators for the various field devices such as liquid and hot gas valves and evaporator fans, and shows whether a defrost cycle is active or not. An operator adjusts the room temperature using the HMI by entering a password-protected screen.
[sidebar id =3]
"Not only is the HMI designed for us by Affinity Energy a lot easier to navigate, having the capability to plug into the controller to conduct maintenance and troubleshooting is a real home run for our techs,” says Mark Obenshain, assistant director, HVAC operations at UNC Chapel Hill.
To alert researchers and maintenance personnel of out-of-tolerance temperature values, Affinity Energy included alarming functionality. In addition to an alarm message displayed on the HMI, an audible alarm mounted on the control enclosure sounds as soon as a temperature rises or falls outside a specific set of parameters.
Not only does the HMI make it much easier to operate the environmental chamber, it also provides data logging to a built-in SD memory card. It can also send an e-mail, access an FTP server, act as a web server, and provide remote Internet access. All of these functions are easy to add at a researcher’s request.
Due to the nature of research conducted in the chambers, a chart recorder was still required. Affinity Energy replaced the outdated chart recorder with a new circular chart recorder by Future Design Controls, saving money without compromising accuracy.
T within half a degree
The refrigeration process includes the typical compressor, evaporator and condenser devices. A refrigeration cycle begins at the compressor, which pressurizes the gas returning from the evaporator coil in the chamber. This high-pressure refrigerant gas condenses into its liquid state, but can only do so if it can release heat.
As the gas travels through a condenser coil located outside of the chamber, it gives off heat, becoming a high-pressure liquid. This liquid refrigerant travels through an orifice and becomes a low-pressure liquid, which wants to evaporate to a gas, but must absorb heat to fuel the transformation. The gas travels through the evaporator coil located inside the chamber, where it can absorb heat, cooling the room and becoming a low-pressure gas, which is returned to the compressor to begin the cycle again.
In this application, temperature is controlled and maintained by managing the liquid line and hot gas valves. The liquid line valve is open all the time except during a defrost cycle. As a result, the temperature in the room would continue to become colder and colder, reaching temperatures below freezing, were it not for the hot gas valve injecting a portion of the gas leaving the evaporator coil inside the chamber back into the inlet of the evaporator coil.
Adding some of the hot gas into the liquid entering the evaporator coil slows the cooling process, bringing the temperature toward a desired point. Since the liquid line valve is always open, the hot gas valve is modulated at the duty cycle required to reach and maintain a specific temperature.
Humidity is controlled by heat injection to manage how much moisture in the chamber condenses on the evaporator coil.
A custom PID control method was needed to manage both the positive and the negative side of the operation curve. “Keeping temperatures within a half a degree Celsius, with researchers going in and out all day long, is not an easy thing, but Affinity Energy’s integrated solution has been running flawlessly,” notes Steve Hargett, supervisor, facilities maintenance at UNC Chapel Hill.
Although it is an advanced control function, it was relatively simple for Affinity Energy to develop the custom-control algorithm in the AutomationDirect PLC. The algorithm is essentially a PI loop, but coded explicitly, rather than using the off-the-shelf PID programming module in the controller.
Even with constant researcher traffic throughout the day, the prototype control solution holds the temperature steady within the required 0.5 °C. With their new control system, and with PLC programming supplied by Affinity Energy, UNC Chapel Hill has the freedom to introduce future enhancements using its own personnel.
The plan is to replace controllers on other chambers across the UNC campus, using this open design based on AutomationDirect PLCs and HMIs. Program changes will be incorporated into this universal control solution for the different types of chambers to maintain consistency. As the university integrates this new control solution into the rest of its environmental chambers, all they need to do is copy it, and provide a few minor calibration tweaks based on each room’s characteristics.
UNC Chapel Hill’s future plans include full access to room temperature and alarm history using remote access. This will provide quick access to critical historical data required by various regulatory agencies.
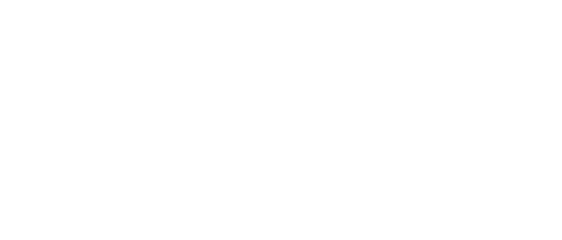
Leaders relevant to this article: