Over the past 20 years, 163 incidents involving reactive hazards have occurred in the U.S., according to the Chemical Safety & Hazard Investigation Board (CSB). These accidents included chemical reactions, toxic gas releases and violent chemical decompositions.
While the U.S. chemical processing industry historically ranks among the safest industrial work environments, and instrumentation and automation have contributed to this standing, great care always has been taken to ensure that measurement and control signals do not constitute an unintended additional hazard.
Safety protection methods used with instrumentation signals have included total encapsulation, explosion-proof/flameproof enclosures, purging with an inert gas, use of fiberoptic signaling, non-incendive/increased safety measures, as well as intrinsically safe (IS) designs. IS requires that both the electrical equipment and the wiring in the hazardous environment be incapable of releasing sufficient electrical or thermal energy, under normal or abnormal conditions, to cause ignition of a specific hazardous atmospheric mixture in its most easily ignited concentration.
Intrinsic safety has been an extensive practice in European chemical plant instrumentation. In North America, industrial safety practices have relied to a much greater extent on explosion-proof enclosures and encapsulation methods. As plant control systems manage increasingly large databases, hazardous area measurement and control points are expanding dramatically. So is the incentive to employ intrinsically safe devices. Maintenance efficiency, primarily the ability to maintain instruments in place, is an important advantage of IS gear.
Hazardous area classification in Europe is by zone based on the number of hours per year that the hazardous condition exists:
Zone 0 : More than 1,000 hours
Zone 1: 10â⬓1,000 hours
Zone 2: Less than 10 hours
These classifications may also be used in North America which has traditionally used a class/division system:
Class I, Div. 1: Hazardous gases; high probability during normal operation
Class I, Div. 2: Hazardous gases; low probability during normal operation
Worldwide operations are tending to standardize on the zone classification scheme. This is especially true within the North American operations of European firms. Div. 1 corresponds to Zones 0 and 1 while Div. 2 corresponds to Zone 2.
In Sept 2002, Venture Development (www.vdc-corp.com) issued market reports on intrinsically safe instrumentation products for North America and Europe. In the context of these reports, VDC conducted in-depth telephone and electronic interviews with responsible personnel at consulting engineering/construction firms, process manufacturers, OEMs and Systems Integrators. Some key findings included:
÷ The majority chose the protection method regarded as "standard" in the local market.
÷ IS is perceived as a lower-cost option by a majority of the respondents.
÷ A large share would consider switching to IS if the cost savings are significant.
÷ Current IS use in Europe is highest in Zone 1 applications and lowest in Zone 0 applications.
÷ Current IS use in North America is greatest in Class I, Div. 2 applications.
With regard to the third point, VDC believes switching is likely only in new construction and major modernization projects. A white paper by James Taylor, group manager for industrial automation and principal author of the IS reports, discussing these findings can be found at www.vdc-corp.com/industrial/reports/index.html .
According to VDC, North American demand for IS products in 2001 was less than half of the comparable European demand. Projected North American demand growth, however, is twice that of Europe through 2006. Among the IS products covered (distributed remote I/O, IS barriers, I/P converters, operator interface devices, NAMUR proximity switches, solenoid valves and transmitters), IS distributed remote I/O showed the fastest growth at over 10% per year.
FISCO (Fieldbus Intrinsically Safe COncept) is an emerging technology that allows multiple field devices to be connected to a single source. In a FISCO-based fieldbus network, power supplies and power repeaters can supply up to 100 mA to field instruments in a Class I, Div. 1 hazardous area, a 25% increase versus the conventional approach.
Mind you, I'm only a chemical engineer and more than a little nervous discussing the inductive/capacitive/impedance-matching gyrations involved in designing, specifying, and certifying an intrinsically safe circuit. It does seem, however, that the Europeans may be right for once. The U.S. Navy commissioned its last battleship (USS Wisconsin BB-64) almost 60 years ago in February 1944. It may finally be time to get the battleships out of process plants.
Terrence K. McMahon
McMahon Technology Associates
135 Fort Lee Road
Leonia, NJ 07605
Tel: 201-585-2050
Fax: 201-585-1968
Latest from Home
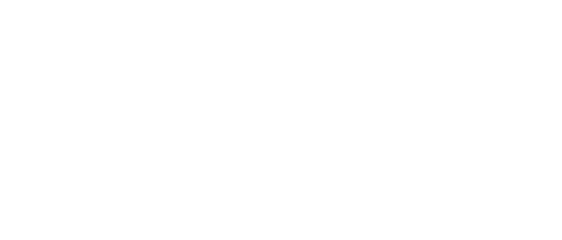
Leaders relevant to this article: