Many changes are occurring in the worldwide flowmeter market. While growth of new-technology flowmeter applications continues to outpace those of more traditional meters, long-term favorites such as turbine and positive displacement are holding their own in many applications.
For now at least, change is evolutionary rather than revolutionary. This article looks at significant developments occurring in each of 10 flow technologies.
New-Technology Flowmeters
These types of meters, introduced since 1950, include Coriolis, magnetic, ultrasonic, vortex, and multivariable differential pressure (DP). They are the main focus of product development by the major suppliers, and typically have accuracy levels of 1% or better. Sales of all of these types are growing at a compound annual growth rate (CAGR) faster than the flowmeter market as a whole (greater than 2.1%).
* The Mystery Meter: The first Coriolis meters featured bent tubes. However, since straight-tube meters were introduced in the mid-1990s, much of the product development has been focused on them. Straight-tube Coriolis meters are especially suited for sanitary applications, since they are easier to clean than bent-tube meters. Particles are less likely to get lodged in straight-tube than in bent-tube meters.
Line size continues to be an issue for Coriolis meters. More than 90% of Coriolis meters sold are 2 in. or less in size. Coriolis meters become expensive and unwieldy in larger line sizes, especially 4 in. and above. No one has as of yet been able to invent a Coriolis meter for the larger line sizes that is modest in both price and size.
One of the most interesting new Coriolis products is Foxboro's digital Coriolis meter, the CFT50. This meter is designed to deal with measurement applications involving two-phase flow, such as liquid and gas, or entrained air. The meter was developed as the result of a customer needs analysis in conjunction with the engineering department at the University of Oxford. It can handle difficult-to-measure applications including slurries and non-homogeneous fluids, as well as pharmaceutical batch applications, railcar and tank truck unloading, pulp & paper coating applications, and dairy processes in cheese manufacturing.
End users have a unique loyalty to Coriolis meters. This may stem from admiration for their high accuracy together with the inability to see the inner workings of the meter. This gives Coriolis meters a sense of mystery that no other meter has. Despite this, in interviews end users have requested a sight glass to visually check flow on Coriolis flowmeters.
* A Magnetic Attraction: Magnetic flowmeters are the workhorses of the flowmeter market. They are wildly popular in Europe, where there is great need to measure water flow, and the leading suppliers are based in Europe. In fact, magnetic flowmeters were first introduced in Holland in 1952.
Because magnetic flowmeters are so widely used for sanitary applications, much of the new product development either centers around linings or around meters designed for particular applications. Application-specific meters typically meet certain industry standards and are designed with materials suited for a particular industry. An example is Emerson Rosemount's Model 8721 sanitary magnetic flowmeter.
More money is spent on magnetic flowmeters annually than on any other type. This is projected to remain true through 2007. In terms of units, there are far more magnetic flowmeters sold than any other type of new-technology meter. More than twice as many magnetic flowmeters are sold in Europe than in the U.S. It appears, then, there is a certain magnetic attraction between end users and these flowmeters.
* The Ultra-Fast-Growing Meter: Ultrasonic flowmeters are the fastest growing meter category. However, most of this growth comes from explosive growth in the market for custody transfer of natural gas. This growth began in Europe in 1995 with the publication of Technical Monograph 8 by Groupe Europeen de Recherches GaziSres (GERG). This monograph laid out criteria for using ultrasonic flowmeters for custody transfer of natural gas. In June 1998, the American Gas Assn. (AGA) followed suit with a similar document, AGA-9, which resulted in explosive growth of ultrasonic meters for that application in North America.
While natural gas measurement has captured many of the headlines, some important developments have been occurring on the liquid side. The American Petroleum Institute (API) has published a draft standard about using transit-time ultrasonic flowmeters to measure liquid hydrocarbons. Krohne recently introduced the UFM 3030, a three-beam transit-time ultrasonic flowmeter designed to measure liquids, including hydrocarbons. That unit is a follow-up to the company's AltoSonic V, the first multiple-beam ultrasonic flowmeter for custody transfer of liquids.
* A Plethora of Vortices: Vortex flowmeters have so far failed to capture the imagination of the end user community. While they have many attractive features, they do not have one overriding strength that makes them a must-have for a particular application. They are highly accurate, but not as accurate as Coriolis meters. And while they are minimally intrusive, they are more intrusive than magnetic and ultrasonic meters.
Vortex meters are at their best in steam applications because they can handle the high pressures and temperatures associated with measuring steam flow. However, steam only accounts for about 10% of total flow applications. Perhaps this is why vortex meters are currently the slowest growing new-technology segment.
Traditional Technology Flowmeters
These flowmeter technologies were introduced prior to 1950. There is less product development among these meters than among new-technology meters. And traditional meters typically perform at a lower level than new-technology meters in categories such as accuracy and repeatability. Traditional meters include differential pressure (DP), positive displacement (PD), turbine, open channel, thermal, and variable area.
* A Difference in Pressure: Differential pressure transmitters have been used for more than a century to measure flow. In conjunction with a primary element, such as an orifice plate or a Venturi tube, they measure the pressure drop across an obstruction in the pipe. This is a well-understood technology and is especially popular in the U.S.
One of the most important developments in DP flowmeters in the past five years has been the packaging of DP transmitters together with primary elements to create a true DP flowmeter. Instead of having to buy and install an orifice plate or averaging pitot tube separately, this new style of DP flowmeter comes with the primary element already integrated with the transmitter. Some models also come with pressure and temperature sensors, and the ability to measure mass flow. The ProBar and the Mass ProBar from Emerson Rosemount are examples.
Important advances have been made in multivariable flowmeters, which are a type of new-technology meter. These flowmeters compute flow by measuring two or more process variables. They typically use a DP transmitter and the values from a pressure and temperature sensor to compute mass flow. Foxboro and ABB are among the companies that recently introduced multivariable transmitters.
* Positive Disposition: The history of positive displacement meters goes back to 1815, with the invention of a PD meter for measuring gas flow. Nutating disc meters, used to measure water flow, were invented in 1830. The popular oval gear flowmeter, used today for industrial applications, was patented in Germany by Bopp & Reuther in 1932. Bopp & Reuther is still selling this meter today, and it is also manufactured in Brazil by Metroval.
Positive displacement meters operate by capturing the fluid in a small volume whose dimensions are precisely known. They then count how many times this operation occurs. This need for counting is what gives rise to the registers that adorn the top of many positive displacement meters. The counting registers give the meters a personality with their face-like appearance.
PD meter suppliers have been using advanced manufacturing techniques and chronometry to more accurately measure the dimensions of PD meters and produce more precise flowmeters. Due to their precision, PD meters are still widely used for custody transfer measurement of hydrocarbons and water. They are also used for custody transfer of gas.
* A Spinning Thing: Reinhard Woltman invented the first turbine meter in 1790. Since that time, at least six different types of turbine meters have been invented. However, the modern use of turbine meters to measure fuel flow is more recent. It stems from attempts made during World War II to develop a reliable flowmeter for measuring fuel consumption on military airplanes.
There are at least 140 suppliers of turbine flowmeters worldwide, more than for any other type of flowmeter. There are also more turbine flowmeters sold annually than any other type of meter in terms of units. In fact, more turbine meters were sold in 2002 than the sum total of all new-technology flowmeters worldwide. The same equation does not hold true for dollars, however, since the average selling price of turbine meters is considerably less than the average selling price of new-technology meters.
Turbine suppliers are improving their meters by using more durable materials to increase their reliability. For example, Hoffer Flow Controls uses hybrid ceramic ball bearings to increase longevity. Hoffer also has introduced clamp-on insertion turbine meters to compete with plastic paddlewheel meters.
* Open to Many Channels:Open channel flowmeters are used to measure flows of rivers and streams and also to measure water flow in partially filled large pipes. There are a variety of methods used, including weirs and flumes, area velocity, and dilution methods. When weirs or flumes are used, a variety of methods are used to measure level.
Some advances in open channel flow measurement revolve around electronic enhancements and improvements in communication. There is also room for improvements in sensor technologies. Some improvements of this type have already occurred with Doppler technology.
* Taking the Temperature of the Flow: Thermal flowmeters were developed in the 1960s and 1970s by several independent companies in California. The technology evolved out of hot-wire anemometry, the origins of which go back to the early 1900s. Hot-wire anemometers were used in velocity profile and turbulence research. Because they are fragile and are susceptible to error caused by dirt, they are not suited to industrial environments.
Fluid Components Intl. (FCI) first developed thermal flow switches to give a flow or no-flow reading for oil being pumped out of wells in California. The process of creating these flow switches begin in 1964; it wasn't until 1981 that FCI began producing thermal flowmeters. These meters were designed to measure gas flow. Sierra Instruments independently developed thermal flowmeters during the same period.
While it is clear that hot-wire anemometry is a traditional flow technology, thermal flowmeters fit some of the criteria for new-technology flowmeters. And recent technological advances are resulting in thermal meters that perform at a significantly higher level. If these technological developments continue, it may be necessary to reclassify them as new-technology meters.
* Variable Flows: Most variable area flowmeters are read manually. They have a float that rises in proportion to the force of the flow. A calibrated glass, metal, or plastic tube has markings that indicate flowrate.
Variable area flowmeters are mainly used where high accuracy is not required. They are valuable for a flow/no-flow reading and where a visual reading is all that is necessary. More recently, however, some suppliers have developed variable area meters with an output signal, making them more usable in a process environment.
Beyond the Top 10
In addition to these 10 technologies, there are several others including target meters. More exciting is the development of what appear to be genuinely new flow technologies. One is the Sonartrac flowmeter from CiDRA Corp., which uses sonar techniques to measure volumetric flow. The meter senses pressures on a pipe caused by naturally occurring vortex-like disturbances in turbulent flows. It is intended for industrial applications.
Photon Control of British Columbia takes a different approach. This company is developing a series of optical flowmeters for the oil & gas industry. Like most new-technology flowmeters, these optical meters have no moving parts and are non-invasive. The company has licensed technology from TransCanada Pipelines to develop optical flowmeters for the energy sector.
It is very unusual for a new flowmeter technology to come along. All of a sudden, we seem to be blessed with several new technologies at once. This is partly a result of the fact that, for the past several years, companies have been able to focus on something other than fieldbus. It is also because technology continues to evolve and grow, and inventive minds are continuing to focus on new ways to measure flow.
Jesse Yoder, Ph.D., is president of Flow Research, Wakefield, Mass. He has 16 years of experience as an analyst and writer in process control. Yoder specializes in flowmeters and other field devices, including level, pressure, and temperature products. He has written 60 market research studies in industrial automation and process control, has published numerous journal articles, and is the author of the Worldflow Handbook, which includes a detailed guide to flowmeter selection. He also is the author of The World Market for Flowmeters (published in February 2003), a market study that includes all 10 flow technologies. He may be reached at 781/245-3200 or [email protected].
Latest from Flow
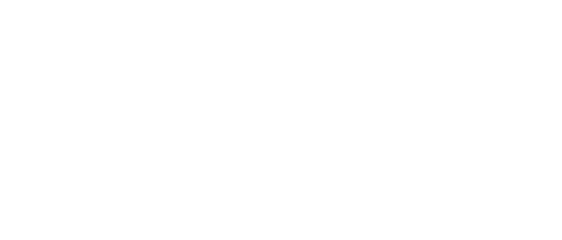
Leaders relevant to this article: