We're worried about our jobs, but as regular CONTROL contributor Dick Morley pointed out during our panel discussion at ISA 2004, we aren’t really losing them to China. Ironically, China itself is losing the same kinds of jobs to automation as we are. It is all about productivity. One-hundred years ago, it took over half the population of the U.S. to feed us. Now less than 5% of the population is involved in farming. Farmers were concerned about many things we take for granted. We’re in the enviable situation of having the first society where even the poor have television and cars, and where access to high-speed data transmission is a cutting-edge civil right. The average life expectancy has increased more than 30 years in the past century and now we can afford to be worried about lots of things like affordable health care, and specialized education for all. This is the effect of the increased productivity that we, who work in process automation, have created. As a society, we’ve moved on. And, as process automation professionals, we have to move on too. What people in our profession need to care moor about today is the process itself, and not just the controls.
About the Author
Walt Boyes has more than 30 years of experience in sales, sales management, marketing, and product development in the automation industry both for sensors, devices and control systems for industrial and environmental controls, including Executive Committee and Board experience in several companies. Walt currently is serving as Editor-in-Chief of CONTROL and www.controlglobal.com.First came reliable sensors and final control elements. Then came control loops, followed by distributed control systems and SCADA—all to give us a real-time picture of the state of the controls. From this picture, the operator and the process engineers were supposed to be able to infer that their process was running right, because the loops were all “right and tight.” As we all know, this wasn’t necessarily so. The gap between the data from the control system and the data from the lab and quality control was huge, and sometimes seemed an uncrossable divide.Loop tuning, and advanced process control software, predictive maintenance and asset management are the productivity tools of the future, not controls. Field instruments and final control elements have been made such that reliability and uptime are assumed, not issues. Where previously, we measured the flow in a control loop, now we want to see not just the flow, but also the pump speed, the motor temperature, the vibration level and the torque necessary to open and close the control valve, and many more parameters. Recently, Siemens sent Paul Studebaker, Editor in Chief of Plant Services magazine, and the former occupant of this space, a list of the over 4,000 data tags that you can get out of a “simple” drive unit. All of these can be analyzed by predictive maintenance software, and translated into work tags that can keep a plant from unplanned shutdowns and maximize availability. And now we care much more about how to control the process than how to make the controls work.This is an order of magnitude change. Taken individually, each loop may be working as well as it can, yet the process as a whole may be operating at far less than optimum throughput and efficiency. Today’s tools have shifted our viewpoint.So what does this mean? The business of making instruments function is now a technician’s job. Automation engineers are much more useful connecting plant-floor systems to the enterprise asset management and supply chain systems than troubleshooting an obnoxious level measurement. Process engineers can now have more direct control over how the process as a whole works, because the instrumentation layer is more transparent, and increasingly interoperable. By our own incredible productivity, we’ve changed our jobs.
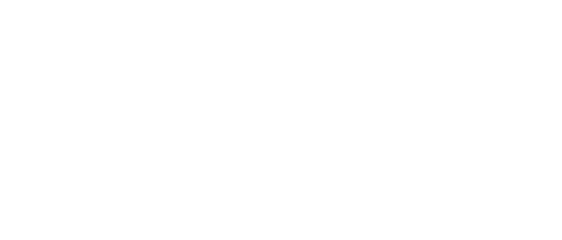
Leaders relevant to this article: