BATCHING, dosing, and weighing seem like simple, straightforward production operations. Set a target value, open a valve, measure the material, and close the valve when the measured value matches the target value. Of course, we all know nothing is ever as simple as it seems.
We asked users who spend their days working in the consumer products, food, pharmaceuticals, and wine production industries to share their batching, dosing, and weighing challenges. A few asked that we not use their names, while some others asked that we not include their company names, but rest assured that these are companies whose products you know well.
Next, armed with our newly created and somewhat unexpected list of challenges, we talked with hardware and software manufacturers to learn what products and technologies they have or are developing that can help users overcome some of these challenges. These challenges and the solutions are eye opening.
Heavy Challenges
Anyone who has dumped a bag of dry solids, say flour, into a container has experienced inconsistent product flow, product hang up, and dust-control issues associated with that transfer. Now introduce bulk storage tanks with vibrators, piping, scales, valves, mixing vessels, dust collectors, and environmental influences, like humidity, and you can begin to appreciate the challenges of making accurate, repeatable, dry solids additions at places like Washington Quality Foods, a producer of Dolly Madison and Tasty-Kake products.
Tony Murray, Washington’s director of information technologies, explained that it uses a lot of sugar, salt, dextrose, six grades of flour, and more than 300 other ingredients to produce cake, muffin, waffle, and other dry-food mixes.
“When we decided to build a new plant,” Murray says, “we faced the typical challenges of moving, measuring, and dispensing dry products, but we also wanted to resolve two additional challenges: determine which ingredient additions could be fully automated and which were best served by a software supported manual process, and improve our kosher-validation processes.” All of Washington’s products are kosher validated. This means food is prepared in accordance with Jewish dietary laws, and a rabbi verifies that appropriate ingredients, as well as strict handling and cleaning procedures are being enforced.
A field operator makes a manual addition to a vessel at Washington Quality Foods.
“Cosmetic, custom food, and pharmaceutical producers share a lot of the same challenges. These include using lots of different ingredients, making gram-sized dosages, ensuring ingredient confidentiality, maintaining personnel and material safety, minimizing waste of high-value products, and ensuring production facilities perform as efficiently as is possible,” says Yves DuFort, with Invensys/Wonderware. He adds that ingredient confidentiality and gram-sized dosages concern several industries, so it’s common to repackage ingredients into generic containers, and then develop barcodes that indicate ingredient, source, and lot. These ingredients are stored in secure, central weighing and dispensing facilities, similar to a pharmacy.
“When a specific product (recipe) is to be produced,” DuFort says, “employees in the dispensing facility pre-weigh and package the individual ingredients and produce a new or second barcode that augments the content of the original barcode with such things as the scales used, actual weight, date, dispensing personnel, etc. These are all the things that need to be part of the batch history to meet kosher and/or regulatory requirements.”
Once production begins, software prompts the operator when it’s time to make an addition, helps enforce any required personal protective measures, and uses the barcode information to validate that the correct ingredient is being added at the appropriate time. For automated ingredient additions, software helps ensure accuracy, efficiency, and repeatability by binding specific pieces of equipment such as scales to all iterations of a particular recipe, and informs operators as soon as a transfer path becomes available for cleaning.
Jim Wiesler, who works for a major pharmaceutical firm, says he has talked with his peers at other companies, and they agree that the challenges associated with both dry solids and liquid-ingredient additions are very similar to the challenges expressed by Murray and DuFort.
However, Wiesler adds, “Another really big challenge is getting the product experts, the scientists, to establish ingredient target values with a proven, acceptable over and under-target range. For example, when we begin taking a product from the laboratory to production, the scientist may tell us we need to add ‘exactly’ 1,000 liters of high-purity water—not 999 liters and not 1,001 liters. Sometimes we’re able to talk through the reasons, and eventually establish an acceptable target range. For these additions, we’re able to apply automation. For ingredient additions that the scientist insists must have a zero or near-zero target range, we apply manual methods of measuring and dispensing, and accept the allied costs and production impacts that manual intervention creates.”
David Chappell, who works for Proctor & Gamble (P&G), responded to our question with questions of his own. “Is it better to implement all the batch addition control functions in the process automation system (PAS) software,” he asks, “even if you have to compromise the control algorithm? Or, is it better to integrate best-in-class, standalone instruments and devices with the PAS?”
Chappell explains that, several years ago, P&G engineers developed a predictive adaptive control (PAC) algorithm that dramatically improved P&G’s ability to make accurate, efficient, repeatable material additions. However, each PAC algorithm deployment required some specialized knowledge and support that P&G engineers weren’t able to consistently provide across P&G’s global operations.
“We knew we had created a better mousetrap,” says Chappell, “but we were only able to support about 20% of the P&G deployment opportunities, so we begin seeking outside assistance. In 2001, we (P&G) licensed our PAC algorithm to Mettler Toledo, which has successfully commercialized its Q.impact material transfer controller. By using Mettler Toledo’s products and services, P&G engineers are now available to assist with additional PAC deployments.” (See “The Better Mousetrap Dilemma: Buy Versus Make” sidebar below.)
However, not all challenges associated with batching, dosing, and weighing can be solved with new hardware or software—or can they?
Dose of Regulations
Regulatory oversight is another batching, dosing, and weighing challenge that food, cosmetic, pharmaceutical and wine producers share. Whether that oversight comes from the U.S. Food and Drug Administration (FDA), the Alcohol and Tobacco Tax and Trade Bureau (TTB), or the rabbi, their goals are essentially the same—to ensure that established quality standards are maintained.
A statement in the FDA’s “Guide to Inspections of Dosage Form Drug Manufacturer’s” emphasizes the importance it places on weighing and dosing systems. It reads, “Critical manufacturing steps include the selection, weighing, measuring, and identifying of components and addition of components during processing. It includes the recording of deviations from the batch record, mixing time, and testing of in-process material, and the determination of actual yield and percent of theoretical yield. These manufacturing steps are documented when done, and not before or after the fact.”
Such emphasis illustrates why Wyeth materials manager Javier Suarez says, “We needed to become FDA-compliant to achieve our goal of becoming the worldwide supplier of Refacto. AspenTech’s weighing and dispensing software solution is a critical component for attaining this compliance, and we’re very pleased that our weighing and dispensing solution didn’t receive any observations from the FDA during the approval process.” Refacto is an intravenously administered product that helps correct deficiencies in the blood of people with hemophilia.
Now Add PAT
The stated goal of the FDA’s Process Analytical Technology (PAT) framework is to encourage regulated industries to design and develop processes that build quality into a product, rather than trying and testing it in after the fact. One of the more innovative technology investigations being advanced under the PAT framework is a collaboration between a global pharmaceutical manufacture, BOC Edwards Pharmaceutical Systems, and Bruker BioSpin to use time-domain nuclear magnetic resonance (TD-NMR) technology to provide online check-weighing.
“The FDA’s PAT initiative has highlighted that traditional sample checking, such as using precision scales, is no longer sufficient. This non-contact, check-weighing (NCCW) system represents a significant innovation and advance in check weighing,” says Paul Stewart, BOC’s technology director.
What makes BOC Edwards’s NCCW system so innovative is that it provides 100% in-line weight measurement at speeds up to 400 vials per minute, and it supports closing the loop to BOC’s filling equipment.
When we first began developing this article, we anticipated that user challenges would include measurement, such as load cells and tank gauging systems, and final control devices, such as analog verses on/off valves. We also thought there might be some industry-specific challenges identified. We were wrong on both counts. What we learned, and what you should keep in mind is, that when you’re facing batching, dosing, and weighing challenges, look beyond your own industry for solutions because it’s highly likely that the solution already exists somewhere.
The Better Mouse Trap Dilemma:
Buy Versus Make
DESPITE THE existence of many instrumentation and automation devices designed to perform very specific measurement or control functions, there continues to be integrators and engineers who argue that they can “build a better mouse trap.” The justifications are many, even though some may be suspect. Nevertheless, the biggest justification usually is verbalized as: “We bought this really great automation system, why don’t we use it?”
Certainly that argument has merit, and the tradeoffs of integrating a third party device as opposed to developing the equivalent functionality in the automaton systems software must be evaluated, but occasionally a device comes along that provides patented or proprietary functionality that’s impossible to replicate. One such device is Mettler Toledo’s Q.impact (Q.i) material transfer controller. What makes this particular device unique is its use of a patented predictive adaptive control (PAC) algorithm originally developed by Proctor & Gamble (P&G). The PAC algorithm accounts for such things as material-in-suspension, lags in input signal updates, and material kinetic forces to predict the precise moment the measured material addition will equal the target value.
P&G has carefully documented its installations where the Q.i controller replaced other material transfer methods, including those implemented in automation system software. Without exception, the Q.i controller has allowed P&G to “control the so-called uncontrollable,” and thus produce operational improvements ranging from 34 to 84%.
P&G’s Dave Chappell says, “Some of our Q.i controller deployments have been challenging, but when we were diligent about applying the four “E”s—education, environment, embracement, and economics—the challenges were minimal and easier to overcome.”
- Education—Before a special purpose device or technology can be deemed suitable for a particular process or application, process and automation engineers need to possess an in-depth understanding of the underlying technology and its capabilities. Only by acquiring first-hand knowledge of what a technology is capable of doing can users confirm if the myths, rumors, and legends that are circulating about the device or technology are valid.
- Environment—Despite arguments about “sister plants,” every application, process, and plant has its own idiosyncrasies. These may be in piping and vessel design and layout; different operational and/or maintenance philosophies; different power, grounding, and network designs; and/or different staff and local support capabilities. What’s necessary for success is to understand and accommodate all the environments where the new device or technology is being installed.
- Embracement—The ability to successfully integrate the new device or technology requires that all affected parties including process engineers, operational leads, unit managers, local integrators, project managers, and control system suppliers embrace and are committed to the new device or technology. Sometimes people in these last three groups may offer the greatest resistance. The local integrator may not understand the new device or technology, may view it as adding risk, and may work behind the scene to get it eliminated from the project’s scope. The project manager may not appreciate its lifecycle-cost savings, and thus views the new device as unnecessarily adding costs and complexity. Control system suppliers may view the new device or technology as “taking money out of their pockets.”
- Economics—Supporters of the new device or technology must develop and sell a meaningful value proposition. This can’t be just a bunch of ballpark numbers or broad-brush claims; it must establish meaningful, quantifiable measurements that identify improvements in the areas of engineering, operations and maintenance. For example, reducing the number of manual interactions (touches) that operators make during a shift is a meaningful, quantifiable measurement that will likely result in better product quality and improved throughput.
Chappell adds, “Even in those installations that we could have done a better job of applying the four “E”s, we achieved significant improvements, and not one of our Q.i implementations has been removed.” This is certainly a solid testament to buying versus making that better mouse trap.
About the Author |
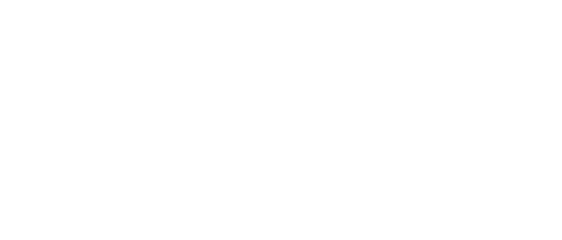
Leaders relevant to this article: