WATER AND wastewater flowmeters have much in common. They are typically large with many applications that operate over a wide range of flows. These flowmeters are used in plants categorized as potable water, wastewater and industrial facilities, so they must cover a variety of applications for both clean and dirty water.
Water for potable water systems is typically drawn from a lake, river or wells and treated to remove impurities that make it suitable for drinking. Flowmeters are often used to measure the plant influent flow and are sometimes to calculate payments and taxes. Permitted influent flow limits are often enforced using these measurements. The water treatment plant may include additional procedures, such as chlorination and fluoridation. These and other treatment operations typically require flowmeters to measure water and/or chemical flows to ensure smooth operation and efficacy.
In addition, flowmeters are used throughout the water distribution system to measure the output of the treatment plant and the water flows to various parts of the system. These flowmeters are usually located in large pipes that can operate at relatively low flow rates for significant periods of time. The measurements are typically used to account for water in the system, but they may also be used to calculate payment from local water purveyors. Flowmeter performance is extremely important, especially when the flowmeter is used to calculate payments.
Wastewater flow measurements include measurements throughout the collection system that may be used for monitoring and/or billing purposes. The plant influent flow usually is measured to enforce permit limits and sometimes to calculate payments and taxes. Wastewater treatment plants usually are designed such that their hydraulics reduce the number of instruments required, however there are still a number of flowmeters used within the plants to measure intermediate flow rates and chemical additives. Additionally, flowmeters that can be made portable are often used for infiltration and inflow, sewer sizing and stormwater monitoring studies.
Industrial plant influent flow is usually measured and is often used to enforce permit limits. Flowmeters are installed throughout the plant water distribution system for monitoring and control in addition to calculating water balances. Plant effluent flowmeters generally are used to measure the water leaving the plant and are often used to enforce permit limits and calculate payments when the effluent is treated by another entity.
Common to the water, wastewater and industrial water industries is the need to measure water in large pipes over relatively wide flow ranges. In general, the water is relatively clean in industrial plant influent streams and potable water systems; whereas wastewater treatment plants generally contain dirty water streams. Industrial water streams may be clean and/or dirty, depending upon the plant.
Venturi flowmeters commonly are used to measure potable water flow in large pipes.
Water treatment and distribution systems are relatively large, so flowmeter accuracy is a prime concern because the flowmeters often are used to generate invoices for the various water purveyors, and even a 1% error can have a significant impact on the bill. In addition, operation of the water system requires flow measurements that can be used to account for the water entering the system. Failure to do so on an ongoing basis can result in water losses and can reduce the effective capacity of the water system. Typically, accounting for the distribution of the incoming water is accomplished using a series of water balances around various portions of the system. Increasing unaccounted for water losses can prompt work to improve the quality of flow measurement for balance and billing purposes.
Figures 3 and 4 below show predicted and actual flows downstream of a single-bend piping configuration. Note that the higher fluid velocity near the pipe wall will result in measurement of an improper differential pressure and cause flow measurement error.
Furness also notes, The condition of the flowmeter element can have a significant effect on the measured flow rate.
He found that surface buildup can affect the Venturi flowmeters installed in some water systems by as much as 0.2% to 0.3% per year. In one such installation in the U.K., a Venturi that was in service almost 100 years was documented to be measuring 17% higher than the actual flow.
Furness is also quick to point out that the details of the pressure tap can introduce unacceptable errors. In one application in the U.S., pressure tap changes resulted in a flow measurement shift of approximately 3%. This may seem small, but it is approximately 6 times more than some suppliers claimed accuracy of the Venturi. In a fiscal metering system, such an error would be unacceptable and likely grounds for lawsuits.
FIGURE 3:Other flow devices need calibration, too, and may be better fits for plant requirements. Venturi flowmeters are passive mechanical devices where inlet and throat diameter measurements are used as the basis for calculating flow rate. This gives these flowmeters an inherent reliability and repeatability with few sources of measurement error and limits on their magnitudes. Furthermore, redundant taps can be used for custody transfer applications where it is desirable to independently check transmitter measurements, says Dave Wyatt, president of Wyatt Engineering, Lincoln, R.I., who designs and manufactures Venturi flowmeters for the water and wastewater industries.
The ratio of throat diameter to inlet diameter (beta ratio) provides significant design flexibility by reducing upstream straight run requirements, adds Wyatt, because Venturi flowmeters are less sensitive to upstream piping as the beta decreases. Tailoring your flowmeter to your installation, rather than the other way around, is a significant bonus for engineers and plant managers of older water treatment facilities where sufficient straight run may not be available.
Wyatt warns users that square root extraction should be taken either in the transmitter or in the control room, but not in both places. In addition, Turndown can be increased by stacking transmitters (i.e., low range and high range) and being sure to size the Venturi to maintain sufficient Reynolds number, he says.
This is the actual flow shown in Fig.3 so you can really see the disturbance.
Pennington adds, Chemical composition and concentrations are subject to change in industrial wastewater streams due to process and production changes. Magnetic flowmeters are prevalent in these applications because they are available with compatible materials of construction and are not affected by changes in sound speed. On a lesser note, there is a trend to use flowmeters in place of pump strokes as a measure of flow so as to reduce chemical consumption.
One of the biggest problem areas in water and wastewater flow measurement is the measurement of flow in open conduits and partially filled pipes. Generally found in wastewater collection systems (sewers), stormwater systems and industrial outfalls, these flows have been problematic since Robert Mannings formula was created in the 19th century. Generally, open channel flows are measured when possible through the use of a primary device (a weir or a flume) but in many cases, a primary device cannot be installed because of application conditions. In those cases, several types of devices to produce rude approximations of flow rate have been designed, including dippers, area/velocity flowmeters, varieties of compound meters and a magnetic flowmeter variant that actually measures flow when the pipe is not full. Most of these devices, unfortunately, have been found to have potential error in excess of 40% of rate. Included in this number are nearly all of the portable solutions to the problem, so many users bite the bullet and dig up the street and do it over properly.
Water and wastewater flowmeters sometimes have much in common, but often are considerably different. Flowmeter accuracy is often more important than the application would initially indicate. Many existing flowmeters have not been installed according to manufacturer recommendations, so they are apt to exhibit significant flow measurement errors. Further, recent research has shown that upstream flow profile effects in large pipes are larger than previously anticipated. In general, the user is cautioned to pay attention to flowmeter detailsespecially when measurements are used to generate invoices valued at millions of dollars per year.
About the Author |
Latest from Home
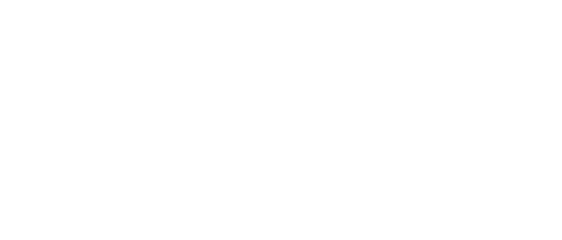
Leaders relevant to this article: