By Paul Miller, contributing editor
While silicon wafer fabrication is largely a discrete manufacturing operation, theres still a lot of process control going on in the utilities supporting a fab. The critical clean room heating, ventilation, and air conditioning (HVAC) systems present some especially interesting closed-loop control challenges.
Death by Dust
Semiconductor product yields depend on environmental conditions inside the fabs clean rooms. Not only must ambient temperature and humidity levels be maintained within very tight tolerances, airborne particulates must also be carefully controlled because they can render semiconductor components worthless.
For these reasons, clean rooms use extensive HVAC systems with high-performance filters to tightly control temperature and humidity, while filtering airborne particles. Typically, powerful recirculation air handlers (RAHs) provide a high velocity of air at a uniform temperature. This creates a unidirectional or laminar flow of air through the clean room. The straight parallel streams of air at high velocity carry away airborne particles and prevent wafer contamination. The temperature in the clean room is controlled within ±1.5 °F. To maintain this accuracy, each recirculation air handler relies on a cooling coil, a set of isolation dampers, and a fan.
Teaching an Older Fab New Tricks
At one large wafer fabrication facility, more than 160 truck-sized recirculation air handlers (RAHs) are aligned in a grid high above the 125,000 square foot clean room (Figure 1). When the fab was originally built, nearly 100 air handlers were installed. Unfortunately, only a few were actually commissioned before the project was put on hold in the late 1990s when overcapacity hit the previously red-hot semiconductor manufacturing industry.
Fan Deck
Figure 1: Recirculation air handlers (RAHs) are aligned in a grid to provide the fabs cleanroom with tightly controlled and filtered air.
When the decision was made to reopen the fab, the wafer manufacturer also decided to update and coordinate the controls for its critical recirculation air handlers. For this accelerated project, it tapped Industrial Design Corp. (IDC), a global engineering firm for engineering procurement contractor, CH2M Hill.
For our customers, time to market equals time to profit, says Gary Mays, IDCs instrumentation and controls manager. Our first priority is to get our customer up and running as quickly as possible.
To save time, IDC initially considered using the existing motor starters. However, it quickly became apparent that this was neither the best control approach nor the most cost-effective solution for the air handlers.
Instead, IDC worked with Rockwell Automation to develop and implement an innovative intelligent motor control solution for the recirculation air handlers. The solution included Allen-Bradley PowerFlex intelligent, variable speed drives (Figure 2), a ControlLogix programmable automation controller, ControlNet networking, and FactoryTalk View human machine interface (HMI).
Smart Speed
Figure 2: Intelligent drives control fan speeds to keep the cleanroom pressurized and save energy.
No More Home-Run Cabling
Using its existing motor starters, the fab previously would have needed to hardwire each starter back to the controller cabinet. By networking the smart drives, they could instead install one communications cable between the drive and controller cabinets. The temperature transmitter, control valve, damper position switches and damper solenoids in each RAH unit were all wired directly to the drive mounted on the RAH unit, eliminating the need to home run these instruments to a central control panel (Figure 3).
Besides reducing wiring and installation costs, this approach created a centralized point for all drive programming and file storage, providing the flexibility and integrated capabilities that would carry the fab into the future.
Drives Pay Own Way
When we evaluated our equipment options, Rockwell didnt have the lowest initial purchase price, says Mays. But when we assessed the total cost to design, develop, and deliver the solution, Rockwells variable frequency drives easily paid for themselves.
Because space is at a premium inside a wafer fab, design firms look for innovative ways to reduce equipment footprints. IDC engineers designed the RAH control system to allow field I/O to be wired directly to the drives I/O board, essentially using the drive as a distributed I/O drop. Networking the drives I/O back to the controller eliminated the space required for new panels and conduit runs, saving valuable real estate.
Drive operating status and speed are communicated to the programmable automation controller via the network. When the RAH is in auto mode, the unit is stopped and started from the controller via the network.
The controller closes the temperature PID loop based on the actual temperature in the clean room and the desired setpoint. The controller automatically adjusts the motor speed as needed to keep the clean room pressurized.
Architectural Overview
Figure 3: The drives I/O provides a distributed I/O drop thats networked back to the controller. The drive is mounted on the RAH, providing easy termination of the I/O devices at the unit.
Access to information is the foundation of intelligent motor control. One of the benefits of using the intelligent drives is that they provide about five times more information than a non-networked drive, adds Mays. That gave our customers the competitive advantage to review trending information and schedule preventative maintenance, a critical step considering these plants often run all day, every day.
Based on previous experience, IDC understands how critical network certification is to eliminating and preventing communications issues. Once the ControlNet network was in place, IDC called on Rockwells network engineering specialists to help verify and validate the network.
These specialists tested the network to make sure that the signal loss across the network was acceptable, network lengths were not exceeded, and that all connections were made properly. Network verification reduces the risk of discovering last-minute problems, when theyre often more difficult to identify or can have a worse impact on the overall project schedule.
More than $500,000 Saved
The intelligent motor control solution helped save the semiconductor fab owner more than $500,000 in installation costs, according to IDCs estimates. Reduced wiring, centralized configuration and maintenance generated real savings during the start-up and commissioning of the project. The fab owner will continue to reap savings through better control, enhanced diagnostics, and easier troubleshooting. For example, if one of the drives needs to be replaced or a unit moved to a new location, configuring it will take just a few minutes, compared to more than an hour in the past.
Programming the drives and ns conrollers and a couple of hundred motors used to take a couple of months, but now we can create software profiles and templates, and just and paste them into each device with fewer mistakes and more consistency, adds Goh. This can save lots of time and money because downtime costs so much. User can now save at the design, engineering and commissioning, maintenance, and other stages of the lifecycleespecially as they gain more of the benefits of predictive maintenance.
Latest from Home
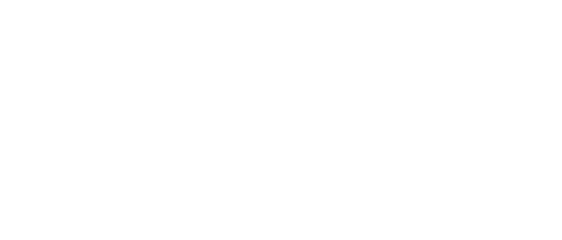
Leaders relevant to this article: