āAsk the Experts,ā on ControlGlobal.com, is moderated by noted process control authority BĆ©la LiptĆ”k. In this column, he and other experienced process control engineers welcome questions concerning process measurement, control and optimization. If you would like to be on our team of āexperts,ā send your resume to [email protected].
Q: We have a liquid level measurement application where weāre replacing existing displacer type transmitters with remote seal d/p type transmitters due to severe service requirements. The existing bridle process flange connections are oriented as side/bottom, and weāre looking for your advice regarding installing the new DP remote seal flanges with the same orientation; i.e., the bottom (HP) side remote seal flange would be in a vertical position. Are there any concerns or limitations with this type of installation in terms of the effectiveness or the accuracy of the measurement, or is it empirical that we carry out a piping modification to provide for side/side orientation for installation of the remote seal flanges?
Ahmed Khalaf, SIE
AC&EE Dept., Engineering Division, ADGAS
A:Using the bottom connection on the tank, and locating the d/p cell below the āzero levelā is OK.
I assume that āsevereā service means that dirty, viscous, slurry or sludge-type process fluid is stored in the tank, and I also assume that the specific gravity of the fluid is known and constant. In that case, you have to watch out for two issues:
a) Plugging of the tank nozzle
b) Range elevation.
You can provide protection against plugging by using an extended diaphragm d/p cell (Figure 1) if your nozzle is large enough (3-in. or 4-in.) for that type of insert. The extension will fill the nozzle and be flush with the inside, so it will keep out the material that could plug the nozzle. If your nozzle is larger or somewhat smaller, you can use an extended chemical seal and a filled d/p. If your nozzle is very small, you can purge.
Since the d/p cell will be below the tank, you want to elevate the span (suppress the zero) as illustrated in Figure 2. Itās preferable that you buy the d/p with the elevation already set by the supplier. This you can get by giving them the ālower range valueā (the level that you consider to be zero level) and the elevation when the d/p cell experiences a zero differential. On the specification, you should also give the specific gravity of the fluid. Then the supplier will accurately set the elevation before shipping the unit. Be careful that the sum of the span and the elevation cannot exceed the full range of the d/p cell.
BƩla LiptƔk
A:The question statement isnāt clear to me; Iām very conservative. If the nozzle to be used for the pressure measurement is at the bottom of the tank, then I would suggest that the user should consider that the measured pressure is not a measure of level, but of mass. A displacer has a similar dependence on density, but because the displacer is usually much shorter than the tank height, the effect is small.
If, however, the diaphragm seal is installed at the lower displacer nozzle, the errors probably donāt matter. Level from pressure is inferred from knowledge or control of the fluid density.
If tank overflow is a safety or environmental concern, the user should range the transmitter, so the actual level at the lowest possible liquid density is below the overflow level when the level signal is 100% full. The prudent engineer also allows for transmitter and installation errors and will be conservative.
Cullen Langford
President, Cullen G. Langford Assoc.
Ian H. Gibson, CPChem, RPEQ, FSEng
Process, Control and Safety Engineering Consultant
Q: Iām looking for a reference or some guidance as to reasons for not providing fuses at marshalling terminals for isolation and circuit protection purposes.
Our DCS vendor informs us that isolation fuses for the analog and digital inputs will not be provided, as the same is not to be put in IS circuits and also arenāt compliant with standards. As an alternative, they will provide knife-edge terminals in the IS circuits for isolation purposes.
Weāre not sure about this recommendation, and could not find a reference about it in the standards. In the past, weāve seen different DCS vendors provide isolation fuses for the inputs and outputs in these situations. Have the requirements changed?
I would be grateful if you could kindly give us your opinion about this.
Chandra Sekar
A:I depend on the DCS; i.e. FoxI/A has zener diodes at each input and optical isolation, so fuses are not necessary. Blown fuses can be a nuisance. The older Honeywell TDCIII does need fuses.
I am not up to date on the latest systems. I think the system should be fuseless or do not buy it!
Stephan Gaertner, PE
Chevron, Richmond, California
A:Ā Replaceable fuses are not called for in intrinsically safe (IS) circuits, since they canāt be relied on as being of the proper rating. They may also have been replaced with fuses of the wrong rating or bypassed altogether.
Current and voltage to the hazardous (classified) area are limited at the boundary by approved safety barriers, the design, mounting, and physical protection of which are specified in the IS standard or code applicable to and within the local jurisdiction.
Fuses may be used in the circuits of the unprotected (unclassified) area, including circuits connected to the safe (unclassified) side of barriers, though this must be recognized as lowering reliability by introducing additional pressure/friction connections.
Otto Muller-Girard, PE, FISA
A:There is no reason not to fit fuses in IS circuits.By their very nature they are intrinsically safe, and so you can work on them live.
Maybe the question to be asked is why you would want to use a fuse in the first place. By definition an IS circuit is current-limited, and the likelihood of your finding a fuse that would operate between the working current and the short circuit current is small.
So I guess we should initially ask what problem are you trying to solve with the fuse?
Jon Malins
MTL Instruments Chief Technology Officer
Latest from Home
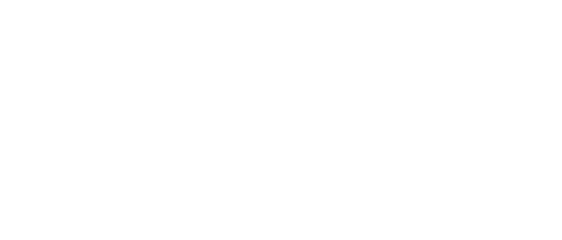
Leaders relevant to this article: