The typical manufacturing plant has two control systems: One, the basic process control system (and safety instrumented system piggybacking on it) and the other, the electric power control system. They are separate. They are usually operated by entirely different teams not cross-trained with each other. And they operate on different digital communications protocols. The process side of the plant uses HART, Foundation Fieldbus and Profibus, while the electrical controls communicate via Profibus and IEC 61850. So not only are they separate; they cant talk to each other.
We see tighter integration as having the potential to increase both efficiency and productivity. Peter Terwiesch, ABB chief technology officer, is bullish on the promise of a unified approach to process control and electrical systems.
According to Mats Pettersson, ABBs product manager for electrical integration, this is a situation that needs changing.
Electrical integration, he said in his presentation at ABB Automation World this week in Houston, is simply connecting the electrical devices to a control system. Integration doesnt replace power distribution SCADA systems, but complements them on the plant site. It provides a common platform for unified operations and allows extended asset management and additional applications like power management to be included in the plant control system.
Electrical integration saves electrical and installation cost, reduces the possibility of blackouts and minimizes operational costs by non-duplication of systems and staff, Pettersson asserted. It can reduce investment cost by as much as 20% over the non-integrated, two-control system approach, he said.
He gave as an example an ABB project for NorskHydrothe Grane offshore oil platform―an entirely integrated system, with controls and electrical systems all working from a common ABB 800xA control system.
Today, theres fieldbus and better networks on the controls side, but on the electrical side, everything is still hard-wired and either analog or analog-discrete. We have the capability to move customers to an all-digital, single-system approach. For asset management, DTM permits use of ABBs Asset Master software on the electrical controls, motors, switchgear and drives, as well as the process instrumentation and control valves in the plant.
Because power and automation have different communications standards, much missionary work will be required, but the result is going to be well worth the effort, Pettersson said. With the introduction of IEC 61850, which is sometimes called station bus, you now have fieldbus on one side and station bus on the other, bridging two worlds. He described a network with integrated Foundation Fieldbus HSE, Profinet and IEC 61850 providing all the plant control communications needs.
Pettersson said a recent Voice of the Customer study revealed that customers like the idea of one protocol: One system for automation and electrics and the visibility that one user interface provides to the end user. The study noted the preference for value-added applications such as asset management, centralized data recording, connections to systems for ERP and alarm management.
Latest from Safety Instrumented Systems
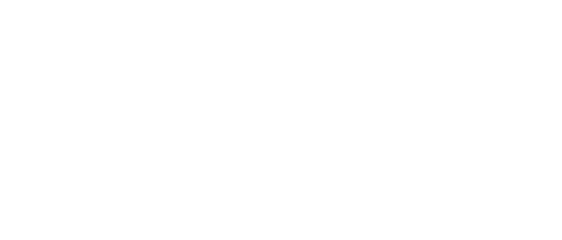
Leaders relevant to this article: