Many manufacturers know it would be good to integrate their process automation and power control systems, and some can even explain why—but only a few were able to pull it off, at least, that is, until recently. To help users begin to realize the benefits of tying together more of their controls and power equipment, Stefan Bollmeyer presented “Electrical Integration: A Strategy for Achieving Unified Operations and Extended Asset Management” this week at the ABB Automation and Power World 2009 in Orlando. Bollmeyer is ABB’s fieldbus product manager for its System 800xA.
“Electrical integration is the next frontier in driving productivity, increasing safety and reducing costs.” ABB’s Stefan Bollmeyer discussed the bottom-line potential for an integrated approach to process and power controls.
Bollmeyer confirmed that much of the process electrification, process instrumentation, power distribution and power management devices in many plants have been there for years and still are not integrated. “For instance, a large pulp and paper mill may typically have 2,400 electrical actuators, 1,160 motor starters, 100 drives and 250 intelligent electrical devices (IEDs) for medium- and high-voltage switchgear, while its process plant may have 1,321 motor starters, 240 drives and 111 IEDs for medium-voltage switchgear,” he explained. “These are all high-cost assets, so there are many good reasons to integrate them.”
However, through their motivation for electrical integration might be the same, Bollmeyer added that different industries have different performance objectives. For instance, oil and gas applications generally want to maximize production, keep their processes running, conduct load-shedding during power interruptions and optimize use of generating capacity. Meanwhile, pulp and paper, aluminum and steelmakers and power generation facilities strive to manage electricity as a raw material cost, perform peak shaving, address high energy consumption and provide a reliable supply. And chemical and life sciences users want to optimize energy consumption and also make sure their utilities are operating reliably.
“Electrical integration is the next frontier in delivering a unified environment to drive improvements in productivity, increased safety and reduced costs,” said Bollmeyer. “Electrical integration enables users to achieve total plant visualization so they can make decisions based on dollars and cents, and not just on temperatures and voltages. This also means they maximize production by reducing the impact of an unreliable power supply, as well as reduce energy costs by conducting peak shaving.
“Electrical integration also allows users to reduce operational costs by unifying their operations environment, performing condition-driven maintenance, reducing spares and training, and establishing cross-discipline cooperation. They further can reduce investment costs by minimizing cabling and engineering, by implementing an optimized network design and by establishing asset management for their electrical subsystems.”
Despite these potential gains, Bollmeyer added that several persistent barriers continue to block electrical integration. “In the past, electrical integration was hampered by a lack of communication standards and architectural design, high project execution and commissioning costs, and high life-cycle costs,” he said. “Organizational barriers among departments within plants and suppliers have also hindered integration, and these mindset-based barriers often are harder to deal with than the technical challenges to integration. Many users have their own department and kingdoms, and they want them to stay just as they are.”
To help process control and power staffs cooperate on achieving better electrical integration, Bollmeyer reported that ABB recommends that they adopt a unified integration method based on a single system environment, use a fieldbus network to handle electrification control and management, and also employ the IEC 61850 standard to tie their process instrumentation, process electrification and power distribution networks more closely together. For instance, process electrification using ABB’s System 800xA includes comprehensive libraries with pre-defined software elements, defined aspects available in Plant Explorer software and extensive integration to make both engineering and maintenance tasks more efficient. For a low-voltage breaker, for example, device object types are available in ABB Device Library, and these can be used to integrate the supply side for that LV equipment into 800xA. This enables commands such as:
- Open/close, trip reset, acquire waveforms and harmonics;
- Read measured values such as voltages, frequencies, power factor and harmonics;
- Establish read/write parameters;
- Conduct asset monitoring of communications devices, electrical components, trip unit, and load and supply side; and
- Perform documentation for future reference
“The benefits of integrated process electrification include efficient integration via fieldbus that allows the communication interface at the controller and bus trunk to be redundant; increased visibility of device health information at the control room; and a unified asset management approach with process instrumentation,” explained Bollmeyer.
For example, he reported that using IEC 61850 to integrate MV motor controls gives users several benefits, including fewer cables, easier installation, higher performance, alarm and events from devices, and improved diagnostics.
“Especially at the lower end, electrical integration can save a lot in material and labor costs,” added Bollmeyer. “We still have separate work spaces for power people and process people, but everyone does more of their work the same way, using the same paradigm. This means more and better optimization, lower total costs and more minimization of risk.”
Latest from Safety Instrumented Systems
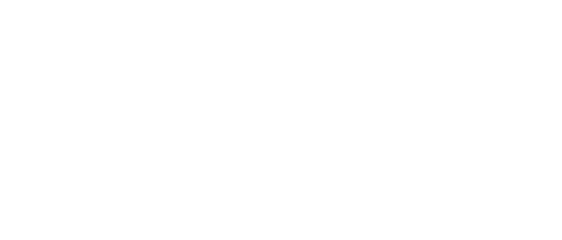
Leaders relevant to this article: