Boost Safety and Compliance While Testing New Limits
Even as companies strive for optimal performance of their operating assets, safety and regulatory compliance necessarily come first. But many plants simply weren't designed or built to meet today's stringent requirements, and finding ways to keep legacy equipment up to code presents a constant challenge.
The costs of compliance are not trivial. Many industries face increasing regulation that puts 30 to 50 percent of their profits at stake, according to a recent McKinsey report. Furthermore, the U.S. Dept. of the Interior estimated that new safety regulations introduced in 2010 added $1.4 million in annual operating costs to each of the oil and gas industry's deep water drills with floating rigs.
Compounding these operational demands, people every day still must travel to remote areas or go into harm's way to take manual process measurements deemed too expensive or impractical to automate even a few years ago. They need instrumentation that runs reliably and accurately at high and low temperatures and under other extreme conditions. Further, added measurement points in increasingly remote or hard-to-reach areas dictate minimal maintenance or calibration requirements that repeatedly endanger plant personnel. Managers, engineers and operators also need better predictive diagnostics and improved visibility into their plant's true capabilities if they're to safely squeeze more productivity and efficiency out of their processes. And they're turning to a new generation of high-performance instrumentation technologies to make that possible.
Minimize Risky Worker Procedures
Perhaps nowhere else is the instrumentation payoff greater than where it can prevent the need for a worker to risk injury in pursuit of a process measurement. Instrumentation that is both easy and cost-effective to install—and then performs reliably and accurately in even the harshest conditions—will help ensure that workers seldom have to visit these oftentimes hazardous or, hard-to-reach areas again. Overall safety increases as do process control and predictability, owing to the improved vigilance and consistency of a dedicated, high-performance instrument as compared to manual measurement.
At the AOC resin manufacturing facility in Perris, Calif., Rosemount wireless temperature sensors eliminated clipboard rounds that were an inefficient use of operator time, subjected personnel to a safety risk, and lengthened time to market. The new Smart Wireless network ensures proper mixing of AOC's intermediate resin products with micro-additives at target temperatures to achieve customer-specific formulations and quality—all from the safety of the control room.
"By replacing manual sampling with on-line measurements, we were able to decrease cycle time up to 10 percent," said Tou Moua, AOC product engineer. "We also improved operator safety, and freed up their time to focus on other key areas of the plant."
And at chemical intermediates manufacturer Croda, Inc. in Mill Hall, Pa., Rosemount wireless temperature sensors tackled an application that previously had been both unsafe and impractical for traditional wired approaches: the early detection of exothermic reactions in railcars. With continuous temperature monitoring that goes wherever the railcars do, if the temperature starts to rise, operators are alerted and can take preventive action well before a hazardous situation escalates.
"The Emerson Smart Wireless solution not only saves us time and money, since plant personnel no longer have to monitor those railcars daily, it has also greatly enhanced the overall safety of the plant and our personnel," says Danny Fetters, Croda I&E designer. "No matter where a railcar is positioned on-site, the quality of the transmissions is unaffected, and the signals integrate seamlessly into our control system."
Wireless instruments typically can be installed for a small fraction of the price and effort of a wired instrument. But perhaps the ultimate in installation ease—and safety—is the new Rosemount 0085 Pipe Clamp Sensor which together with a Rosemount 648 Wireless Transmitter provides a simple, fast solution for adding temperature measurements, exactly where you need them, without interrupting the process. The sensor's spring-loaded silver or nickel tip is designed to ensure contact against the pipe surface and provide measurement accuracy and fast response time.
The ease with which reliable new measurement points can be added is only one factor in the wireless safety equation. By installing Emerson Smart Wireless THUM Adaptors on existing instruments—especially those critical, hard-to-reach devices—plants can easily access and finally begin to leverage the advanced diagnostics and multivariable capabilities of the many HART-capable devices that currently communicate only their 4-20mA process variable signal. Liberating stranded diagnostics and secondary process variables provides added insight into the status of these instruments themselves, as well as feeding critical asset health information to operations, maintenance and reliability systems—contributing to safer, more reliable and more efficient operations.
Instrument Your Safety Infrastructure
A key non-traditional arena where wireless instrumentation is proving its worth is in the monitoring of safety infrastructure, including safety showers and pressure relief valves.
At Lion Oil's El Dorado, Ark., facility, for instance, remote safety showers are equipped with Rosemount 702 Wireless Discrete Transmitters and TopWorx GO Switches and Brackets to alert operators when a safety shower has been activated. This provides an immediate alert to emergency personnel and a digital record that the event occurred. "The discrete switches on the showers would easily have cost $10,000 each to wire," said Wilson Borosvskis, Lion Oil instrumentation and control engineer.
At a paper mill in Idaho, eyewash stations are wirelessly instrumented, in part because drivers unloading chemicals don't have a direct communication channel with operators. Although they use lots of radios at the plant, none of the contractors and only some of the employees have them. By installing a wireless network instead of a traditional wired network, they were able to save about 60 percent in installation costs, and know immediately when and where there is a safety issue.
In another non-traditional instrumentation application, the Rosemount 708 Wireless Acoustic Transmitter can be configured to detect the discharge of a pressure relief valve (PRV) and automatically alert operations. And while a PRV is technically a piece of safety equipment itself, acting to prevent a high pressure excursion from escalating to catastrophic failure, a PRV release often implies an environmental emission (and potential fine) as well as an accompanying root-cause condition that merits further investigation.
Automate Monitoring, Ensure Compliance
In its broadest sense, plant safety includes not just plant personnel but people and the environment outside the plant's perimeter as well. Also critically important is compliance with current safety and environmental regulations, along with the ability to prove being in compliance to regulatory authorities.
Demonstrating compliance often hinges on accurate record-keeping, a constant challenge in even the most organized plants. But Rosemount instrumentation is designed to help with these tasks, too. Date stamps and audit trails built into each product show when measurements have been taken and other compliance-related tasks performed. Further, this information is collected and stored in an online database for easy access if an audit is requested. Experienced Emerson personnel can even help evaluate whether older instrumentation is running safely and in compliance: they'll do a top-to-bottom installation audit, identify high risk areas, make sure instruments are installed correctly, and make any adjustments needed to ensure devices are performing to specification.
For an existing plant challenged to keep up with an ever-changing regulatory landscape, wireless instrumentation is proving itself an especially cost-effective solution. This includes safety measures as well as the monitoring and prevention of environmental impacts.
Tank farms are a common beneficiary, as wireless savings rapidly compound in these often sprawling environments. At FH Tank Storage in Kalmar, Sweden, Rosemount 3051S Wireless Differential Pressure Sensors automate level measurement in 14 of the petrochemical terminal's smaller solvent and chemical tanks, while 15 Rosemount 5402 non-contacting radar devices with Smart Wireless THUM Adapters are on the larger tanks, many with floating roofs. "Not only has the new system improved the monitoring of tank levels, it has provided a fully approved overspill protection solution," says Lars Ferm, site manager. "The Smart Wireless network was relatively simple to install and both the network and the transmitters have been extremely reliable," Ferm says. And at another refinery site in the U.S., wireless level switches are on trial to provide an added independent protection layer (IPL) to the tank farm's primary instrumentation.
Safety Only the Start
These are only a few examples of companies that started down the wireless path with a specific regulatory compliance need in mind. Indeed, for many a process industry facility around the world, improved safety or compliance with an environmental regulation helped clear the initial justification hurdle for implementing its first wireless instrument network.
But once that first network is in place, they're discovering that new measurement points are easy and relatively inexpensive to add. This is opening their eyes to incremental applications that can advance other plant performance metrics such as production throughput, energy efficiency and asset utilization rates. Confident that their operations are now safe and compliant, they're pushing facilities to operate closer to their full potential.
Latest from Safety Instrumented Systems
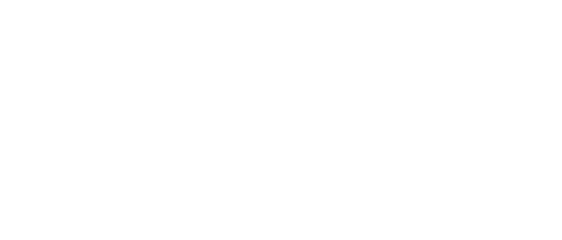
Leaders relevant to this article: